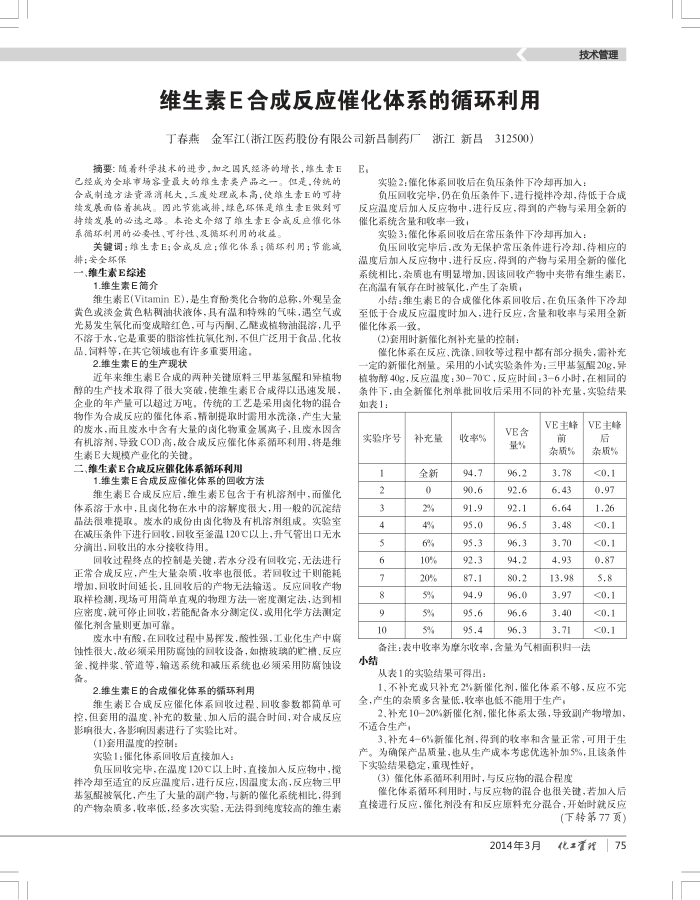
维生素E合成反应催化体系的循环利用
丁春燕金军江(浙江医药股份有限公司新吕制药厂
浙江新昌
摘要:随着科学技术的进步,加之国民经济的增长,炸生素E 已经成为全球市场容量最大的维生素类产品之一。但是,传统的含成制造方法资源消耗大,三成处理成本高,使维生素E的可持续发展面临着挑战。因此节能减排,绿色环保是维生素E做到可持续发展的必速之路。本论文介绍了维生素E合成反应催化体系循环利用的必要性、可行性、及循环利用的收益。
关键调:维生素E;含成反应;维化体系;循环利用;节能减排;安全环保
一、维生素E综述
1.维生素E简介
维生素E(Vitamin E),是生育酚类化合物的总称,外见呈金黄色或淡金黄色粘稠油状液体,具有温和特殊的气味,遇空气或光易发生氧化而变成暗红色,可与丙酮、乙醚或植物油混溶,几平不溶于水,它是重要的脂溶性抗氧化剂,不但广泛用于食品、化妆品、饲料等,在其它额域也有许多重要用途,
2.维生素E的生产现状
近年来维生素E合成的两种关键原料三甲基氢醒和异植物醇的生产技术取得了很大突磁,使维生素E合成得以迅速发展,企业的年产量可以超过万吨,传统的工艺是采用岗化物的混合物作为合成反应的催化体系,精制提取时需用水洗涤,产生大量的废水,而且废水中含有大量的卤化物重金属离子,且度水因含有机溶剂,导致COD高,故合成反应催化体系循环利用,将是维生素E大规模产业化的关键。
二、维生素E合成反应催化体系循环利用
1.维生素E合成反应催化体系的回收方法
维生素E合成反应后,维生素E包含于有机溶剂中,而催化体系溶于水中,且岗化物在水中的溶解度很大,用一般的沉淀结品法很难提取。废水的成份由卤化物及有机溶剂组成。实验室在减压条件下进行回收,回收至签温120C以上,升气管出口无水分滴出,回收出的水分接收待用
回收过程终点的控制是关键,若水分没有回收完,无法进行正常合成反应,产生大量杂质,收率也很低。若回收过干则能耗增加,回收时间延长,且回收后的产物无法输送。反应回收产物取样检测,现场可用简单直观的物理方法一密度测定法,达到相应密度,就可停止回收,若能配备水分测定仪,或用化学方法测定偿化剂含量则更加可靠。
度水中有酸,在回收过程中易挥发,酸性强,工业化生产中腐蚀性很大,散必须采用防腐蚀的回收设备,如携玻璃的忙槽、反应金、搅拌浆、管道等,输送系统和减压系统也必须采用防腐蚀设备。
2.维生素E的合成催化体系的循环利用
维生素E合成反应催化体系回收过程,回收参数都简单可控,但套用的温度,补充的数量,加入后的混合时间,对合成反应影响很大,各影响国素进行了实验比对。
(1)套用温度的控制:
实验1:催化体系回收后直接加人:
负压回收完毕,在温度120C以上时,直接加人反应物中,揽样冷却至适宜的反应温度后,进行反应,固温度太高,反应物三甲基氢醒被氧化,产生了大量的副产物,与新的偿化系统相比,得到的产物杂质多,收率低,经多次实验,无法得到纯度较高的维生素
E
312500
技术管理
实验2:催化体系回收后在负压条件下冷却再加入:
负压回收完毕,仍在负压条件下,进行揽搅拌冷却,待低于合成
反应温度后加人反应物中,进行反应,得到的产物与采用全新的催化系统含量和收率一致,
实验3:催化体系回收后在常压条件下冷却再加入:
负压回收完毕后,改为无保护常压条件进行冷却,待相应的温度后加人反应物中,进行反应,得到的产物与采用全新的催化系统相比,杂质也有明显增加,因该回收产物中夹带有维生素E,在高温有氧存在时被氧化,产生了杂质,
小结:维生素E的合成催化体系回收后,在负压条件下冷却至低于合成反应温度时加入,进行反应,含量和收率与果用全新催化体系一致。
(2)套用时新催化剂补充量的控制:
催化体系在反应、洗涤、回收等过程中都有部分损失,需补充-定的新催化剂量。采用的小试实验条件为:三甲基氢醒20g,异植物醇40g,反应温度:30-70,反应时间:3-6小时,在相同的条件下,由全新催化剂单批回收后采用不同的补充量,实验结果如表1:
VE主峰
实验序号
2 3 4
6 7 8 9 10
补充量全新 0 2% 4% 6% 10% 20% 5% 5% 5%
收率% 94.7 90.6 91.9 95.0 95.3 92.3 87.1 94.9 95.6 95.4
VE含量%
96.2 92.6 92.1 96.5 96.3 94.2 80.2 96.0 96.6 96.3
前杂质%
3.78 6.43 6.64 3.48 3.70 4.93 86 3.97 3.40 3.71
VE主峰后杂质%
<0.1 0.97 1.26 <0.1 <0.1 0.87 5.8 <0.1 <0.1 <0.1
备注:表中收率为摩尔收率,含量为气相面积归一法小结
从表1的实验结果可得出:
1.不补充或只补充2%新催化剂,催化体系不够,反应不完全,产生的杂质多含量低,收率也低不能用于生产,
2.补充10-20%新催化剂,催化体系太强,导致副产物增加,不适合生产。
3.补充4-6%新催化剂,得到的收率和含量正常,可用于生产。
为确保产品质量,也从生产成本考虑优选补加5%,且该条件下实验结果稳定,重现性好,
(3)催化体系循环利用时,与反应物的混合程度
催化体系循环利用时,与反应物的混合也很关键,若加入后直接进行反应,催化剂没有和反应原料充分混合,开始时就反应
(下转第77页)
2014年3月
化置理
75