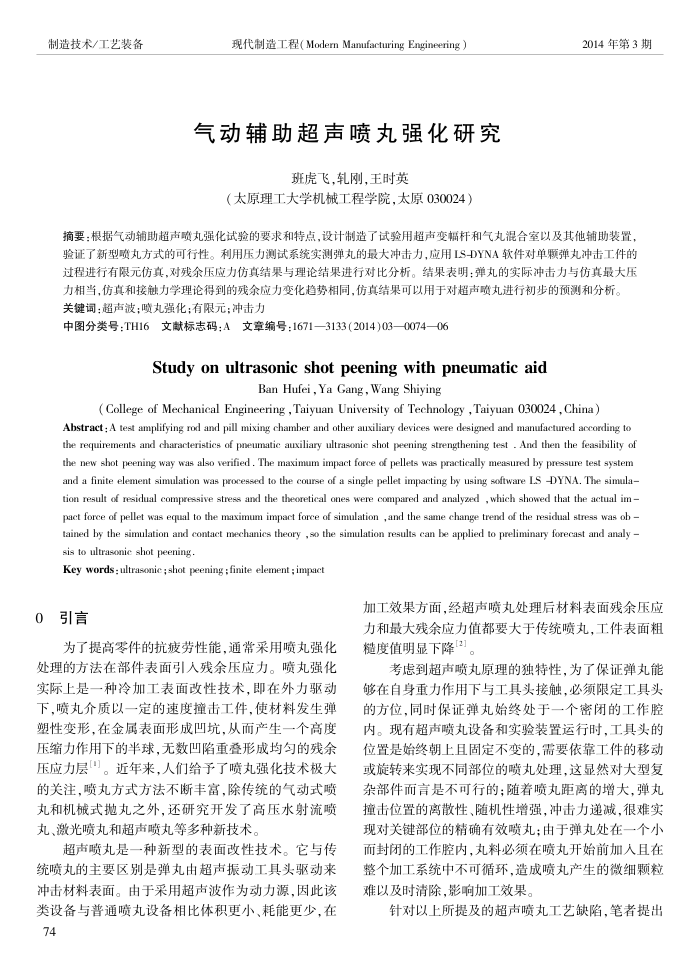
制造技术/工艺装备
现代制造工程(Modem Manufacturing Engineering)
气动辅助超声喷丸强化研究
班虎飞,轧刚,王时英
(太原理工大学机械工程学院,太原030024)
2014年第3期
摘要:根据气动辅助超声喷丸强化试验的要求和特点,设计制造了试验用超声变幅杆和气丸混合室以及其他辅助装置验证了新型丸方式的可行性。利用压力测试系统实测弹丸的最大冲击力,应用LS-DYNA软件对单赖弹丸冲击工件的过程进行有限元仿真,对残余压应力仿真结果与理论结果进行对比分析。结果表明:弹丸的实际冲击力与仿真最大压
力相当,仿真和接触力学理论得到的残余应力变化趋势相同,仿真结果可以用于对超声喷丸进行初步的预测和分析。关键词·超声波:喷丸强化:有限元:冲走力
中图分类号:TH16文麟标志码:A文章编号:1671—3133(2014)03—0074—06
Studyonultrasonic shotpeeningwithpneumatic aid
Ban Hufei, Ya Gang, Wang Shiying
( College of Mechanical Engineering , Taiyuan University of Technology ,Taiyuan 030024, China)
Abstract : A test amplifying rod and pill mixing chamber and other auxiliary devices were designed and manufactured according to the requirements and characteristics of pneumatic auxiliary ultrasonic shot peening strengthening test . And then the feasibility ol the new shot peening way was also verified . The maximum impact force of pellets was practically measured by pressure test system and a finite element simulation was processed to the course of a single pellet impacting by using software LS -DYNA. The simula tion result of residual compressive stress and the theoretical ones were compared and analyzed , which showed that the actual im-pact force of pellet was equal to the maximum impact force of simulation ,and the same change trend of the residual stress was ob -tained by the simulation and contact mechanics theory , so the simulation results can be applied to preliminary forecast and analy -sis to ultrasonie shot peening.
Key words : ultrasonic ;shot peening ;finite element ; impact
0引言
为了提高零件的抗疲劳性能,通常采用喷丸强化处理的方法在部件表面引人残余压应力。喷丸强化实际上是一种冷加工表面改性技术,即在外力驱动下,喷丸介质以一定的速度撞击工件,使材料发生弹塑性变形,在金属表面形成凹坑,从而产生一个高度压缩力作用下的半球,无数凹陷重叠形成均勾的残余压应力层"。近年来,人们给予了喷丸强化技术极大的关注,喷丸方式方法不断丰富,除传统的气动式喷丸和机械式抛丸之外,还研究开发了高压水射流喷丸、激光喷丸和超声喷丸等多种新技术
超声喷丸是一种新型的表面改性技术。它与传统喷丸的主要区别是弹丸由超声振动工具头驱动来冲击材料表面。由于采用超声波作为动力源,因此该类设备与普通喷丸设备相比体积更小、耗能更少,在 74
加工效果方面,经超声喷丸处理后材料表面残余压应力和最大残余应力值都要大于传统喷丸,工件表面粗糙度值明显下降[2]。
考虑到超声喷丸原理的独特性,为了保证弹丸能够在自身重力作用下与工具头接触,必须限定工具头的方位,同时保证弹丸始终处于一个密闭的工作腔内。现有超声喷丸设备和实验装置运行时,工具头的位置是始终朝上且固定不变的,需要依靠工件的移动或旋转来实现不同部位的喷丸处理,这显然对大型复杂部件而言是不可行的;随着喷丸距离的增大,弹丸撞击位置的离散性、随机性增强,冲击力递减,很难实现对关键部位的精确有效喷丸;由于弹丸处在一个小而封闭的工作腔内,丸料必须在喷丸开始前加人且在整个加工系统中不可循环,造成喷丸产生的微细颗粒难以及时清除,影响加工效果
针对以上所提及的超声喷丸工艺缺陷,笔者提出