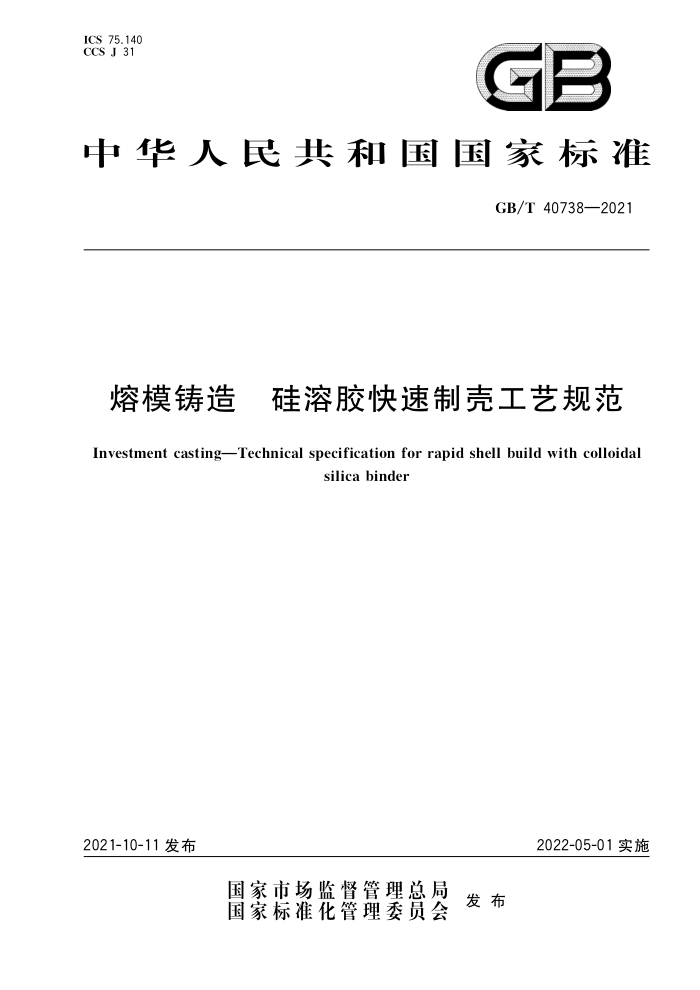
ICS 75.140 CCS J 31
GB
中华人民共和国国家标准
GB/T40738—2021
熔模铸造 硅溶胶快速制壳工艺规范
Investment castingTechnical specification for rapid shell build with colloidal
silica binder
2022-05-01实施
2021-10-11发布
国家市场监督管理总局
国家标准化管理委员会 发布
GB/T 40738—2021
前言
本文件按照GB/T1.1一2020《标准化工作导则 厂第1部分:标准化文件的结构和起草规则》的规定起草。
本文件由全国铸造标准化技术委员会(SAC/TC54)提出并归口。 本文件起草单位:东风精密铸造有限公司、东营嘉扬精密金属有限公司、胜利新大实业集团有限公
司、上海交通大学、苏州泰尔航空材料有限公司、浙江米皇新材股份有限公司、中国航发南方工业有限公司、贵州安吉航空精密铸造有限责任公司、青岛新诺科新材料科技发展有限公司、沈阳铸造研究所有限公司、东莞德威铸造制品有限公司、山东泰义金属科技有限公司。
本文件主要起草人:马波、蔡华洲、汪东红、魏智育、段继东、郝新、李毅、朱家辉、蓝勇、张寅、李锐、 迟连功、陶佳栋、宋珊珊、武超、邵斌、吴光鹏、王正、钟泉、张立军、黄华。
1
GB/T40738—2021
熔模铸造 硅溶胶快速制壳工艺规范
1范围
本文件规定了熔模铸造硅溶胶快速制壳所用原辅材料,快速制壳工艺技术要求,检验与检测方法。 本文件适用于熔模铸造硅溶胶快速制壳原辅材料的选择、工艺制定与过程控制。
规范性引用文件
2
下列文件中的内容通过文中的规范性引用而构成本文件必不可少的条款。其中,注日期的引用文件,仅该日期对应的版本适用于本文件;不注日期的引用文件,其最新版本(包括所有的修改单)适用于本文件。
GB/T 5611 铸造术语 GB/T 11007 电导率仪试验方法 GB/T 11165 实验室pH计 GB/T 12214 熔模铸造用硅砂、粉 GB/T 12215 熔模铸造用铝矾土砂、粉 GB/T14235.1 熔模铸造低温模料第1部分:物理性能试验方法 GB/T 32251 熔模铸造工艺污染物的控制 HB 5346 熔模铸造用硅溶胶 HB 5347 熔模铸造用电熔白刚玉粉 HG/T2521 工业硅溶胶 JB/T9223 铸造用锆砂、粉 JB/T11733 熔模铸造用熳烧高岭土砂粉
3 术语和定义
GB/T5611界定的以及下列术语和定义适用于本文件
3.1
硅溶胶 silica sol(colloidal silica) 熔模铸造用黏结剂,与耐火粉料构成熔模铸造用涂料。 注:一般为碱性,以Na+为稳定剂,分子式:mSiO2·nH2O。
3.2
快干硅溶胶 rapidly dried sol silicate 通过对硅溶胶胶团微结构改造、表面离子改性、添加水溶性高聚物材料或者几种措施复合作用,缩
短制壳干燥时间的特殊硅溶胶品种。 3.3
快干剂 Jquick-drying agent 一种加人硅溶胶涂料后能缩短型壳干燥时间的辅助制壳材料,一般为水溶性高聚物材料。
1
GB/T40738—2021
3.4
砂料、粉料 +sandandflour 熔模铸造用耐火材料颗粒物。 注:型壳用砂粉按粒径或粗细度的不同分粉料和砂料,粉料粒径为0.075mm(粗细度200目)以下的颗粒物;砂料粒
径一般在0.075mm~3.350mm(粗细度200目~6目)之间。常用粉料和砂料包括锆英石、刚玉、高岭土、铝矾土、石英、熔融石英等。
3.5
粉液比 powder-to-liquidratio 涂料中粉料与黏结剂、去离子水等液体溶剂的质量比。
3.6
快速制壳 fast drying of ceramic shell 通过使用快干硅溶胶、快干剂等对制壳涂料改性,及通过制壳环境参数改变,使其制壳干燥时间比
传统工艺缩短1/2以上的一种制壳工艺,
快速制壳用原辅材料
是
4
4.1 模料
熔模铸造常用模料包括填充型模料、非填充型模料及快速原型等。模料的软化点、线收缩率、灰分等指标应满足工艺要求。 4.2 黏结剂 4.2.1 黏结剂的选择
可选择快干硅溶胶成品或普通硅溶胶。普通硅溶胶宜与快干剂配合使用。硅溶胶的SiO2含量、平均粒径应满足工艺要求。 4.2.2熔模铸造用普通硅溶胶
熔模铸造常用的碱性硅溶胶产品,均适用于本文件。 4.2.3快干硅溶胶
快干硅溶胶的种类、品牌、快干机理各不相同,其用于制壳的干燥时间应能满足表1要求。
表1 快干硅溶胶各层型壳的干燥时间
层间干燥时间
层次面层过渡层加固层封浆
绝对干燥时间/h
与普通硅溶胶干燥时间比
≤50% 50% ≤40% ≤40%
3~5 4~6 2~6 1~6
4.3 耐火材料
4.3.1 快速制壳所用砂料可以选择高岭土熟料、电熔白刚玉、锆英、铝矾土、石英等,其平均粒度、SiO
2
GB/T40738—2021
含量、A12O:含量应满足工艺要求。 4.3.2为避免粉料中碱性氧化物、水溶带电离子破坏涂料性能,宜监测粉液pH值、电解质电导率。熳烧高岭土粉液按照附录A方法制备。缎烧高岭土粉液pH值与电导率见表2。
表2高岭土粉液pH值与电解质电导率
检测项目 pH值
参考范围 6.0~9.5 ≤200
电解质电导率/(μS/cm)
4.3.3粉料、撒砂料按面层、过渡层、加固层(也称“背层”)区分。砂粉料粒度按制壳层次均衡增加;不同制壳层次采用同一种粉料的,粉料粒径可以相同。具体耐火材料粒度见表3。
表3不同制壳层次的耐火材料粒度
耐火材料制壳粉料 面层、过渡层、加固层
层次
备注视粉料品种选择
常用粒度(单位:目数或mm)
按目数:200;270;325;400 按粒径(mm):0.075;0.053;0.045;0.038 按目数:40~70;40~100;80~120 按粒径(mm):0.212~0.425;0.150~0.425;0.125~0.180 按目数:30~60;60~80 按粒径(mm):0.250~0.600;0.250~0.180 按目数:16~30;8~16 按粒径(mm):0.600~1.18;1.18~2.36
面层
视工艺要求选择
制壳砂料
过渡层
视工艺要求可微调
加固层
4.4快干剂 4.4.1快干剂包括液态快干剂和固态快干剂。常见的液态快干剂包括聚丙烯酰胺、聚丙烯酸钾、聚丙烯酸钠等;固态快干剂一般是水溶性高聚物,如聚乙烯醇等。 4.4.2在普通硅溶胶中添加快干剂后,制壳干燥时间应达到表1规定的绝对干燥时间。 4.4.3不同类型的快干剂,添加方式、添加量与预处理方式均不相同,应单独建立操作规程予以控制。 4.5其他辅助材料 4.5.1面层涂料中添加表面活性剂。表面活性剂宜选用非离子型产品,避免活性剂与硅溶胶之间的相互影响。 4.5.2面层涂料中添加消泡剂。消泡剂宜选用非离子型有机硅类产品。 4.5.3根据产品结构,快速制壳所用的硅溶胶或涂料中还应添加防止型壳干燥过快而开裂的辅助强化材料,辅助强化材料添加后应确保型壳强度、铸件表面质量符合工艺要求。
5快速制壳工艺技术要求
5.15 蜡模组树检查
制壳前应确认蜡模质量符合工艺质量要求,检查蜡模组树表面是否清洗干净,无蜡滴与蜡屑、无披
缝与焊缝。
3
GB/T40738—2021
5.2 快速制壳工艺流程 5.2.1 快速制壳工艺流程见图1。
(面层)
配制涂料
上涂料
撤砂
干燥
A (过渡层) A (加固层) A (封浆)
上涂料
配制涂料
撤砂
配制涂料
撒砂
上涂料
干燥
配制涂料
干燥
上涂料
图1 硅溶胶快速制壳工艺示意图
5.2.2根据零件结构可分别设置多层面层、过渡层、加固层。 5.3配制涂料 5.3.1 快速制壳用涂料采用快干硅溶胶直接与粉料按一定粉液比配制;或采用普通硅溶胶与一定量的快剂混溶后,再与粉料按一定粉液比配制, 5.3.2配制涂料在连续转动的涂料搅拌桶中完成,加料次序及搅拌要求如下
a) 快干硅溶胶可一次性加入搅拌桶;普通硅溶胶一次性加人后,搅拌桶边旋转边缓慢加人快干
剂,快干剂全部加入后,搅拌时间不低于3min,确保胶水中无絮状物 b) 耐火粉料可分两至三次加入搅拌桶,每次加入后搅拌时间不低于5min,确保涂料桶内无未分
散的粉团;其他固态添加剂混合在粉料中一起添加,视制壳质量需要,加人表面活性剂、消泡剂、悬浮剂等液态添加剂。 涂料组分全部添加进涂料搅拌桶后,开始计量涂料搅拌时间。
c) d)
5.3.3应设定面层、过渡层、加固层等各层涂料最低搅拌时间,保证涂料均匀,且涂料黏度、涂片重量、 涂料密度等主要参数达到工艺要求方能使用。典型耐火材料配制的快干硅溶胶涂料搅拌时间见表4。
表4典型耐火材料涂料配制搅拌时间
单位为小时
锆英粉涂料新配涂料 补充配料 新配涂料 补充配料 新配涂料 补充配料
莫来粉涂料
石英粉涂料
重点监控指标
层次
M5 涂料黏度、涂片厚度、
≥12 ≥8 ≥6
≥20 ≥10 ≥10
≥24 ≥16
≥10 M5 M5
面层过渡层加固层 ≥12
≥10 5 M5
涂料密度涂料黏度、涂料密度
≥3 ≥3
采用附录B中的标准流杯,分3次测量涂料黏度,每次间隔1min,测量涂料搅拌桶中3个点的涂料黏度;黏度值误差±2S,即可判定搅拌均匀
GB/T40738—2021
5.3.4快速制壳涂料的寿命较普通硅溶胶涂料会有所缩短,涂料配制后应尽快用完。未用尽涂料在涂料桶中维持搅拌若超过3天,再次使用前应重新测定涂料黏度、涂片厚度、涂料密度等指标是否符合工艺要求,指标超出工艺要求范围的,应补充黏结剂、耐火材料、快干剂等新料,充分搅拌,重新测定合格后才能使用。未用尽涂料超过7天的,还应增加胶凝性指标检测,胶凝性超标20%的,不应继续使用。
5.4快速制壳工艺 5.4.1熔模铸造制壳工艺包括上涂料、撒砂、干燥等3个工序。 5.4.2上涂料包括常压或真空流涂、浸涂与喷涂等。快速制壳上涂料一般采用常压浸涂或流涂。 5.4.3撒砂采用浮砂或淋砂方式。 5.4.4型壳干燥主要控制温度、湿度、风速三个参数。不同铸件结构、不同模料、不同耐火材料、不同涂料黏度,干燥的温度、湿度、风速设置均不相同。表5列出了适宜于快速制壳干燥通用性环境参数。
表5适宜于快速制壳干燥通用性环境参数
层次面层过渡层加固层封浆
风速/(m/s) 层间干燥时间/h
温度/℃ 25±3 25±3 27±5 27±5
湿度/% 50 ~ 75 45 ~65 ≤60 60
干燥判断
3~5 4~6 2~6 1~6
1.6~3.3 3.4~ 5.4 5.5~7.9 5.5~7.9
测量孔、槽等深腔部位型壳温度与外表面温差,面层、过渡层温差≤1℃,加固层≤1.5℃
具体湿度要求可根据区域环境、季节变化,由供方自行调整环境温度视产品尺寸精度、模料种类,由供方自定。 制壳环境湿度越大,温度越低,风速相应宜调大。
5.4.5脱蜡及焙烧后的型壳应满足抗弯强度要求值,并能保障产品外观、尺寸精度等符合图纸规定。 抗弯强度评价频次由供方自行确定。 5.4.6制壳过程涉及的材料、工艺污染物应符合GB/T32251规定。 5.5 制壳工艺参数控制 5.5.1 硅溶胶快速制壳工艺参数应被记录并跟随产品工序交接,工艺参数记录包括但不限于下列内容:
a) 模料种类及规格,模组数量; b) 制壳各层次黏结剂、砂粉材料、快干剂和其他辅助材料的种类、规格及批次: c) 制壳各层次的环境温度、湿度、风速等; d) 各层次涂料黏度、涂片厚度、型壳表面温度、深孔温度、干燥时间等。
5.5.2 制壳工艺参数按产品批次进行记录管理。
6检验方法
6.1 模料的软化点、线收缩率、灰分检验按GB/T14235.1的规定执行 6.2 硅溶胶的SiO2含量、平均粒径检验按HG/T2521、HB5346的规定执行。 6.3高岭土熟料的平均粒度、SiO2含量、A12O:含量检验按GB/T12214的规定执行。 6.4 电熔白刚玉的平均粒度、A12O:含量检验按GB/T12215的规定执行。 6.5 锆英砂粉的平均粒度、ZrO含量检验按HB5347的规定执行。
5
GB/T40738—2021
6.6 铝矾土砂、粉的粒度、SiO2与Al2O:含量检验按JB/T9223的规定执行 6.7 石英砂、粉的平均粒度、SiO2含量检验按JB/T11733的规定执行 6.8 高岭石粉pH值、离子浓度测定按附录A执行。 6.9 涂料黏度、涂料密度、涂片厚度测定按附录B执行。 6.10 型壳的抗弯强度测定按附录C执行 6.11 涂料胶凝性测定按附录D执行
提伪
6
ICS 75.140 CCS J 31
GB
中华人民共和国国家标准
GB/T40738—2021
熔模铸造 硅溶胶快速制壳工艺规范
Investment castingTechnical specification for rapid shell build with colloidal
silica binder
2022-05-01实施
2021-10-11发布
国家市场监督管理总局
国家标准化管理委员会 发布
GB/T 40738—2021
前言
本文件按照GB/T1.1一2020《标准化工作导则 厂第1部分:标准化文件的结构和起草规则》的规定起草。
本文件由全国铸造标准化技术委员会(SAC/TC54)提出并归口。 本文件起草单位:东风精密铸造有限公司、东营嘉扬精密金属有限公司、胜利新大实业集团有限公
司、上海交通大学、苏州泰尔航空材料有限公司、浙江米皇新材股份有限公司、中国航发南方工业有限公司、贵州安吉航空精密铸造有限责任公司、青岛新诺科新材料科技发展有限公司、沈阳铸造研究所有限公司、东莞德威铸造制品有限公司、山东泰义金属科技有限公司。
本文件主要起草人:马波、蔡华洲、汪东红、魏智育、段继东、郝新、李毅、朱家辉、蓝勇、张寅、李锐、 迟连功、陶佳栋、宋珊珊、武超、邵斌、吴光鹏、王正、钟泉、张立军、黄华。
1
GB/T40738—2021
熔模铸造 硅溶胶快速制壳工艺规范
1范围
本文件规定了熔模铸造硅溶胶快速制壳所用原辅材料,快速制壳工艺技术要求,检验与检测方法。 本文件适用于熔模铸造硅溶胶快速制壳原辅材料的选择、工艺制定与过程控制。
规范性引用文件
2
下列文件中的内容通过文中的规范性引用而构成本文件必不可少的条款。其中,注日期的引用文件,仅该日期对应的版本适用于本文件;不注日期的引用文件,其最新版本(包括所有的修改单)适用于本文件。
GB/T 5611 铸造术语 GB/T 11007 电导率仪试验方法 GB/T 11165 实验室pH计 GB/T 12214 熔模铸造用硅砂、粉 GB/T 12215 熔模铸造用铝矾土砂、粉 GB/T14235.1 熔模铸造低温模料第1部分:物理性能试验方法 GB/T 32251 熔模铸造工艺污染物的控制 HB 5346 熔模铸造用硅溶胶 HB 5347 熔模铸造用电熔白刚玉粉 HG/T2521 工业硅溶胶 JB/T9223 铸造用锆砂、粉 JB/T11733 熔模铸造用熳烧高岭土砂粉
3 术语和定义
GB/T5611界定的以及下列术语和定义适用于本文件
3.1
硅溶胶 silica sol(colloidal silica) 熔模铸造用黏结剂,与耐火粉料构成熔模铸造用涂料。 注:一般为碱性,以Na+为稳定剂,分子式:mSiO2·nH2O。
3.2
快干硅溶胶 rapidly dried sol silicate 通过对硅溶胶胶团微结构改造、表面离子改性、添加水溶性高聚物材料或者几种措施复合作用,缩
短制壳干燥时间的特殊硅溶胶品种。 3.3
快干剂 Jquick-drying agent 一种加人硅溶胶涂料后能缩短型壳干燥时间的辅助制壳材料,一般为水溶性高聚物材料。
1
GB/T40738—2021
3.4
砂料、粉料 +sandandflour 熔模铸造用耐火材料颗粒物。 注:型壳用砂粉按粒径或粗细度的不同分粉料和砂料,粉料粒径为0.075mm(粗细度200目)以下的颗粒物;砂料粒
径一般在0.075mm~3.350mm(粗细度200目~6目)之间。常用粉料和砂料包括锆英石、刚玉、高岭土、铝矾土、石英、熔融石英等。
3.5
粉液比 powder-to-liquidratio 涂料中粉料与黏结剂、去离子水等液体溶剂的质量比。
3.6
快速制壳 fast drying of ceramic shell 通过使用快干硅溶胶、快干剂等对制壳涂料改性,及通过制壳环境参数改变,使其制壳干燥时间比
传统工艺缩短1/2以上的一种制壳工艺,
快速制壳用原辅材料
是
4
4.1 模料
熔模铸造常用模料包括填充型模料、非填充型模料及快速原型等。模料的软化点、线收缩率、灰分等指标应满足工艺要求。 4.2 黏结剂 4.2.1 黏结剂的选择
可选择快干硅溶胶成品或普通硅溶胶。普通硅溶胶宜与快干剂配合使用。硅溶胶的SiO2含量、平均粒径应满足工艺要求。 4.2.2熔模铸造用普通硅溶胶
熔模铸造常用的碱性硅溶胶产品,均适用于本文件。 4.2.3快干硅溶胶
快干硅溶胶的种类、品牌、快干机理各不相同,其用于制壳的干燥时间应能满足表1要求。
表1 快干硅溶胶各层型壳的干燥时间
层间干燥时间
层次面层过渡层加固层封浆
绝对干燥时间/h
与普通硅溶胶干燥时间比
≤50% 50% ≤40% ≤40%
3~5 4~6 2~6 1~6
4.3 耐火材料
4.3.1 快速制壳所用砂料可以选择高岭土熟料、电熔白刚玉、锆英、铝矾土、石英等,其平均粒度、SiO
2
GB/T40738—2021
含量、A12O:含量应满足工艺要求。 4.3.2为避免粉料中碱性氧化物、水溶带电离子破坏涂料性能,宜监测粉液pH值、电解质电导率。熳烧高岭土粉液按照附录A方法制备。缎烧高岭土粉液pH值与电导率见表2。
表2高岭土粉液pH值与电解质电导率
检测项目 pH值
参考范围 6.0~9.5 ≤200
电解质电导率/(μS/cm)
4.3.3粉料、撒砂料按面层、过渡层、加固层(也称“背层”)区分。砂粉料粒度按制壳层次均衡增加;不同制壳层次采用同一种粉料的,粉料粒径可以相同。具体耐火材料粒度见表3。
表3不同制壳层次的耐火材料粒度
耐火材料制壳粉料 面层、过渡层、加固层
层次
备注视粉料品种选择
常用粒度(单位:目数或mm)
按目数:200;270;325;400 按粒径(mm):0.075;0.053;0.045;0.038 按目数:40~70;40~100;80~120 按粒径(mm):0.212~0.425;0.150~0.425;0.125~0.180 按目数:30~60;60~80 按粒径(mm):0.250~0.600;0.250~0.180 按目数:16~30;8~16 按粒径(mm):0.600~1.18;1.18~2.36
面层
视工艺要求选择
制壳砂料
过渡层
视工艺要求可微调
加固层
4.4快干剂 4.4.1快干剂包括液态快干剂和固态快干剂。常见的液态快干剂包括聚丙烯酰胺、聚丙烯酸钾、聚丙烯酸钠等;固态快干剂一般是水溶性高聚物,如聚乙烯醇等。 4.4.2在普通硅溶胶中添加快干剂后,制壳干燥时间应达到表1规定的绝对干燥时间。 4.4.3不同类型的快干剂,添加方式、添加量与预处理方式均不相同,应单独建立操作规程予以控制。 4.5其他辅助材料 4.5.1面层涂料中添加表面活性剂。表面活性剂宜选用非离子型产品,避免活性剂与硅溶胶之间的相互影响。 4.5.2面层涂料中添加消泡剂。消泡剂宜选用非离子型有机硅类产品。 4.5.3根据产品结构,快速制壳所用的硅溶胶或涂料中还应添加防止型壳干燥过快而开裂的辅助强化材料,辅助强化材料添加后应确保型壳强度、铸件表面质量符合工艺要求。
5快速制壳工艺技术要求
5.15 蜡模组树检查
制壳前应确认蜡模质量符合工艺质量要求,检查蜡模组树表面是否清洗干净,无蜡滴与蜡屑、无披
缝与焊缝。
3
GB/T40738—2021
5.2 快速制壳工艺流程 5.2.1 快速制壳工艺流程见图1。
(面层)
配制涂料
上涂料
撤砂
干燥
A (过渡层) A (加固层) A (封浆)
上涂料
配制涂料
撤砂
配制涂料
撒砂
上涂料
干燥
配制涂料
干燥
上涂料
图1 硅溶胶快速制壳工艺示意图
5.2.2根据零件结构可分别设置多层面层、过渡层、加固层。 5.3配制涂料 5.3.1 快速制壳用涂料采用快干硅溶胶直接与粉料按一定粉液比配制;或采用普通硅溶胶与一定量的快剂混溶后,再与粉料按一定粉液比配制, 5.3.2配制涂料在连续转动的涂料搅拌桶中完成,加料次序及搅拌要求如下
a) 快干硅溶胶可一次性加入搅拌桶;普通硅溶胶一次性加人后,搅拌桶边旋转边缓慢加人快干
剂,快干剂全部加入后,搅拌时间不低于3min,确保胶水中无絮状物 b) 耐火粉料可分两至三次加入搅拌桶,每次加入后搅拌时间不低于5min,确保涂料桶内无未分
散的粉团;其他固态添加剂混合在粉料中一起添加,视制壳质量需要,加人表面活性剂、消泡剂、悬浮剂等液态添加剂。 涂料组分全部添加进涂料搅拌桶后,开始计量涂料搅拌时间。
c) d)
5.3.3应设定面层、过渡层、加固层等各层涂料最低搅拌时间,保证涂料均匀,且涂料黏度、涂片重量、 涂料密度等主要参数达到工艺要求方能使用。典型耐火材料配制的快干硅溶胶涂料搅拌时间见表4。
表4典型耐火材料涂料配制搅拌时间
单位为小时
锆英粉涂料新配涂料 补充配料 新配涂料 补充配料 新配涂料 补充配料
莫来粉涂料
石英粉涂料
重点监控指标
层次
M5 涂料黏度、涂片厚度、
≥12 ≥8 ≥6
≥20 ≥10 ≥10
≥24 ≥16
≥10 M5 M5
面层过渡层加固层 ≥12
≥10 5 M5
涂料密度涂料黏度、涂料密度
≥3 ≥3
采用附录B中的标准流杯,分3次测量涂料黏度,每次间隔1min,测量涂料搅拌桶中3个点的涂料黏度;黏度值误差±2S,即可判定搅拌均匀
GB/T40738—2021
5.3.4快速制壳涂料的寿命较普通硅溶胶涂料会有所缩短,涂料配制后应尽快用完。未用尽涂料在涂料桶中维持搅拌若超过3天,再次使用前应重新测定涂料黏度、涂片厚度、涂料密度等指标是否符合工艺要求,指标超出工艺要求范围的,应补充黏结剂、耐火材料、快干剂等新料,充分搅拌,重新测定合格后才能使用。未用尽涂料超过7天的,还应增加胶凝性指标检测,胶凝性超标20%的,不应继续使用。
5.4快速制壳工艺 5.4.1熔模铸造制壳工艺包括上涂料、撒砂、干燥等3个工序。 5.4.2上涂料包括常压或真空流涂、浸涂与喷涂等。快速制壳上涂料一般采用常压浸涂或流涂。 5.4.3撒砂采用浮砂或淋砂方式。 5.4.4型壳干燥主要控制温度、湿度、风速三个参数。不同铸件结构、不同模料、不同耐火材料、不同涂料黏度,干燥的温度、湿度、风速设置均不相同。表5列出了适宜于快速制壳干燥通用性环境参数。
表5适宜于快速制壳干燥通用性环境参数
层次面层过渡层加固层封浆
风速/(m/s) 层间干燥时间/h
温度/℃ 25±3 25±3 27±5 27±5
湿度/% 50 ~ 75 45 ~65 ≤60 60
干燥判断
3~5 4~6 2~6 1~6
1.6~3.3 3.4~ 5.4 5.5~7.9 5.5~7.9
测量孔、槽等深腔部位型壳温度与外表面温差,面层、过渡层温差≤1℃,加固层≤1.5℃
具体湿度要求可根据区域环境、季节变化,由供方自行调整环境温度视产品尺寸精度、模料种类,由供方自定。 制壳环境湿度越大,温度越低,风速相应宜调大。
5.4.5脱蜡及焙烧后的型壳应满足抗弯强度要求值,并能保障产品外观、尺寸精度等符合图纸规定。 抗弯强度评价频次由供方自行确定。 5.4.6制壳过程涉及的材料、工艺污染物应符合GB/T32251规定。 5.5 制壳工艺参数控制 5.5.1 硅溶胶快速制壳工艺参数应被记录并跟随产品工序交接,工艺参数记录包括但不限于下列内容:
a) 模料种类及规格,模组数量; b) 制壳各层次黏结剂、砂粉材料、快干剂和其他辅助材料的种类、规格及批次: c) 制壳各层次的环境温度、湿度、风速等; d) 各层次涂料黏度、涂片厚度、型壳表面温度、深孔温度、干燥时间等。
5.5.2 制壳工艺参数按产品批次进行记录管理。
6检验方法
6.1 模料的软化点、线收缩率、灰分检验按GB/T14235.1的规定执行 6.2 硅溶胶的SiO2含量、平均粒径检验按HG/T2521、HB5346的规定执行。 6.3高岭土熟料的平均粒度、SiO2含量、A12O:含量检验按GB/T12214的规定执行。 6.4 电熔白刚玉的平均粒度、A12O:含量检验按GB/T12215的规定执行。 6.5 锆英砂粉的平均粒度、ZrO含量检验按HB5347的规定执行。
5
GB/T40738—2021
6.6 铝矾土砂、粉的粒度、SiO2与Al2O:含量检验按JB/T9223的规定执行 6.7 石英砂、粉的平均粒度、SiO2含量检验按JB/T11733的规定执行 6.8 高岭石粉pH值、离子浓度测定按附录A执行。 6.9 涂料黏度、涂料密度、涂片厚度测定按附录B执行。 6.10 型壳的抗弯强度测定按附录C执行 6.11 涂料胶凝性测定按附录D执行
提伪
6