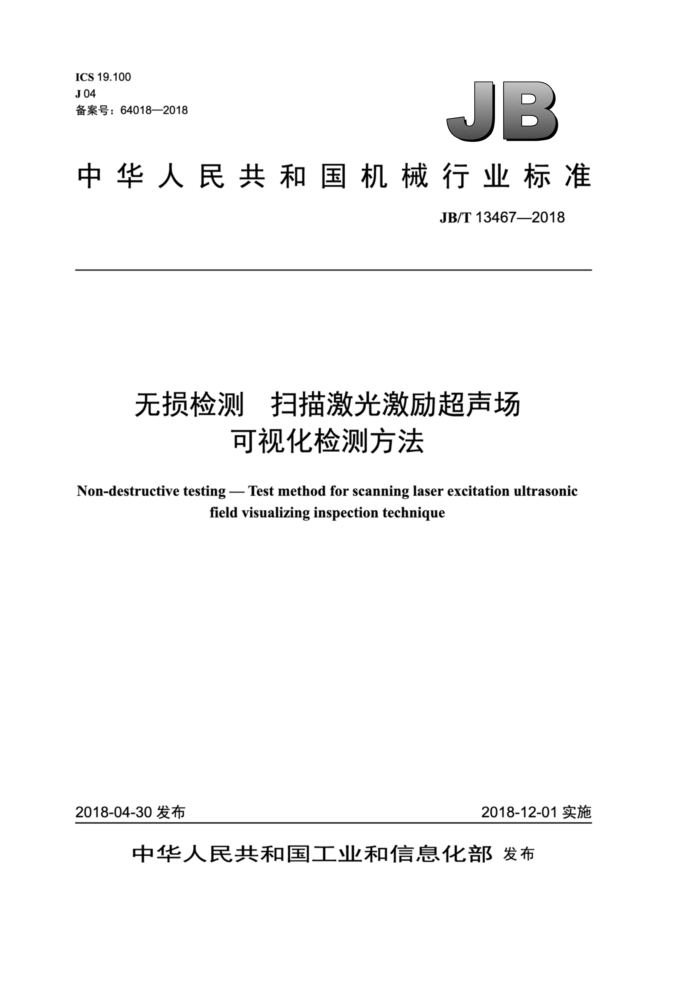
ICS 19.100 J04 备案号:64018—2018
JB
中华人民共和国机械行业标准
JB/T13467—2018
无损检测 扫描激光激励超声场
可视化检测方法
Non-destructivetesting-Testmethodforscanninglaserexcitationultrasonic
field visualizing inspection technique
2018-12-01实施
2018-04-30发布
中华人民共和国工业和信息化部发布
JB/T13467—2018
目 次
前言... 范围
I
1
2规范性引用文件 3术语和定义 4方法概要. 5人员要求. 6 检测系统. 7 参考试块 8 检测...
检测结果的分析与评价 10检测记录与报告附录A(资料性附录) 典型损伤和缺陷参考文献
9
11
图1 检测工件 碳纤维复合材料,图2 最大振幅图图3 超声波声场快照图4 差分滤波处理得到的超声波声场图像图A.1 工件(L型CFRP)图A.2 最大振幅图(L型CFRP)图A.3 T=34.79μs时刻的超声波声场快照(L型CFRP)图A.4 工件(T形角焊缝)图A.5 最大振幅图(T形角焊缝)图A.6 T=18.59μs时刻的超声波声场快照(T形角焊缝)图A.7 工件(钢管端部)图A.8 最大振幅图(钢管端部)图A.9 T=11.67μs时刻的超声波声场快照(钢管端部)
6 6 6
S
d
C
0
.10 .10 .10
1
JB/T13467—2018
前 言
本标准按照GB/T1.1一2009给出的规则起草。 本标准由中国机械工业联合会提出。 本标准由全国无损检测标准化技术委员会(SAC/TC56)归口。 本标准起草单位:西安金波检测仪器有限责任公司、爱德森(厦门)电子有限公司、中国科学院金
属研究所、中国科学院声学研究所、北京航空材料研究院、南昌航空大学。
本标准主要起草人:王波、蔡桂喜、沈建中、史亦韦、林俊明、卢超、赵晋成,本标准为首次发布。
II
JB/T13467—2018
无损检测扫描激光激励超声场
可视化检测方法
1范围
本标准规定了扫描激光激励超声场可视化检测方法。 本标准适用于对壁厚不大于50mm的固体材料或工件的表面、近表面和内部的缺陷(如裂纹、气
孔、腐蚀等)进行扫描激光激励超声波传播可视化的无损检测。
本标准不适用于超声波传播衰减较大(接收信号的信噪比小于6dB)及曲率较大(入射激光与工件界面法线夹角大于60°)的复杂形面固体材料或工件。
2规范性引用文件
下列文件对于本文件的应用是必不可少的。凡是注日期的引用文件,仅注日期的版本适用于本文件。凡是不注日期的引用文件,其最新版本(包括所有的修改单)适用于本文件
GB 7247.1 激光产品的安全第1部分:设备分类、要求 GB/T9445无损检测 人员资格鉴定与认证 GB/T12604.1无损检测术语超声检测 GB/T15313 激光术语
3术语和定义
GB/T12604.1和GB/T15313界定的以及下列术语和定义适用于本文件。
3.1
最大振幅图 maximum amplitude image 该图像中每一点显示的是扫查区域中对应该点的超声波信号在指定时间段内和/或频率段内的最大
振幅值。 3.2
超声波传播图像 象ultrasonicwavepropagationimage 显示随时间变化的工件扫查区域内超声波传播过程中波幅分布的一顿顿图像。
3.3
超声波声场快照 snapshotvisualization ofultrasonicwave 超声波传播过程中某一个确定时刻超声波声场的空间分布所构成的图像。 注:表现超声波声场的物理量可以是位移,也可以是应力分量。
4方法概要
采用脉冲激光束照射固体材料表面时,材料表面发生热弹性效应产生超声波,通过接收装置采集这种超声波信号,并通过放大、滤波及软件处理,得到材料表面超声波传播过程的可视化结果,从而对材料内外部缺陷进行可视化无损检测。
-
JB/T13467—2018
5人员要求
5.1从事扫描激光激励超声场可视化检测的检测人员,应掌握一定的激光超声可视化检测知识,并掌握一定的被检工件材料与加工工艺知识,了解可能存在的缺陷及检验目的和需求。 5.2按照本标准实施检测的人员,应按GB/T9445或合同各方同意的体系进行资格鉴定与认证,并由雇主或其代理对其进行岗位培训和操作授权。
6检测系统
6.1系统组成
扫描激光激励超声场可视化检测系统应包括脉冲激光器、激光扫描装置、信号接收装置、前置放大器、数据采集及成像系统等。 6.2脉冲激光器
脉冲激光器需满足以下条件:
脉冲激光器的输出能量1应可调节,入射激光与工件界面法线夹角应小于60°,其输出的激光能量应足以在被检工件中激励出一定强度的超声波,以与超声接收探头的接收灵敏度相适应,其单次输出能量I的稳定度△I/I应优于5%;脉冲激光器的激光脉冲宽度应能使脉冲激光束所激励的超声波具有适当的频率带宽,一般使用的脉冲激光器脉冲宽度约为1ns~50ns,激励超声波的频率带宽约在20MHz~1000MHz之间; 一为获得清晰的超声波传播图像,脉冲激光器应能产生足够小的激光光斑,激光出射口的光斑直径宜不大于1mm;
一为减小激光激励距离变化对光斑尺寸的影响,脉冲激光器的发散角应足够小;一脉冲激光器的激光激励重复频率应能调节,检测中选用适当的重复频率,以保证超声波声场图
像的图像质量和检测效率:一脉冲激光器的激光激励与超声波信号接收应有较好的同步功能。
6.3激光扫描装置
激光扫描装置用于使激光束在工件上扫描并激励出点源超声波,形成激光束与工件之间的相对扫描
运动。激光扫描装置应满足以下要求:
一对于被检部位,应具有对长度方向(X轴)以及宽度方向(Y轴)分别进行扫描的独立控制功能;一扫描步长宜小于超声接收探头频率带宽所对应的最小超声波波长的一半:一扫描、激光激励、数据采集三者应同步。
6.4信号接收装置
信号接收装置为压电超声(横波、纵波及表面波)探头。根据工件大小及形状复杂度可使用一个或多个压电超声探头。根据检测深度可适当选用垂直压电超声探头或斜角压电超声探头,
接收探头的频率范围推荐在30kHz~10MHz之间,当选用高频探头(大于1MHz)时,应考虑高频超声波在工件中传播时的传播衰减和扩散衰减对检测灵敏度降低的影响,应确保接收探头在高频带范围内有足够的接收灵敏度。
压电超声探头应采用适当的耦合剂涂在工件上,检测过程中应保持耦合的稳定性。
2
JB/T13467—2018
6.5前置放大器
前置放大器的频率响应应与接收探头的频率响应相匹配,其增益推荐采用40dB、60dB。 6.6数据采集及成像系统
基于扫描装置的同步信号使A/D转换器对激光激励的超声波信号进行同步采集,将采集到的超声波信号存入计算机。成像系统对该时间序列数字信号按工件检测面上的扫描点对应的空间投影坐标进行排列,并对存储的超声波信号在各个时刻的振幅值进行灰度调制生成超声波声场图像(静止图像,即超声波声场快照),再对所述声场图像按时间序列连续显示,生成动态的超声波声场视频(即超声波传播的动态图像)。
数据采集及成像系统应满足以下要求:
A/D转换器应具有适当的采样速度、分辨率和采样点数,A/D转换器缓存和计算机内存应足够大;数据采集速度应与激光扫描速度相匹配;
-
一成像系统内存及处理速度应能满足超声波成像和超声波传播图像视频显示的要求。
7参考试块
参考试块主要用于检测系统的校验和检测灵敏度的设定。 参考试块应具有与被检工件相同或相近的材质,相同的形状、公称尺寸和相似的表面状况、热处理
条件及声学特性(如声速、衰减系数)。
根据供需双方的协议确定人工参考试块上人工缺陷的类型、位置、方向和尺寸。用钻入工件表面下
一定深度的沉孔或球形凹坑模拟腐蚀缺陷;用刻槽模拟工件表面裂纹;用与工件表面倾斜一定角度的刻槽模拟折叠;用平底孔模拟工件内部的夹杂和分层,为使平底孔的圆柱面不产生超声波的反射,平底孔需进行塞封,只保留其孔底。
参考试块上人工缺陷的位置、尺寸应采用复型、光学等测量方法加以确认。
8检测
8.1检测要求 8.1.1扫描激光激励超声场可视化检测时需要按GB7247.1的要求采取适当的防护措施。 8.1.2激光输出功率较大时,激光会在被检工件表面造成一定的烧蚀,检测时需要适当控制脉冲激光器的输出功率。 8.1.3在检测之前应适当对工件表面浮尘或油污进行清理。 8.1.4建议应针对不同工件或产品可能存在的缺陷类型和缺陷可能产生的位置,制作人工缺陷参考试块。人工缺陷的类型、位置、方向和尺寸等应尽可能接近实际情况。 8.1.5扫描装置与工件之间不应有任何阻隔激光光束的障碍物存在。 8.1.6应通过检测工艺试验确定扫查区域大小,以保证区域内各处均能达到所需的检测灵敏度, 8.1.7在设定脉冲激光的输出功率时,应考虑激光激励的能量强度对内部缺陷检测能力的影响,优化检测工艺参数。 8.1.8工件的光洁表面会反射激光,不利于吸收激光能量激励超声波,因此,可以考虑在工件表面涂覆一层能吸收光能的薄涂层,以提高工件中激光激励超声的强度,并在检测工艺参数中明确对涂层的要求。 8.1.9异型结构或复杂结构工件在扫描激光激励超声场可视化检测时,需要考虑工件结构可能引起的超声波模态转换对检测的影响。
3
JB/T13467—2018
8.1.10扫描过程中扫描装置与工件应尽可能保持相对静止,可以根据检测精度要求对扫描速度及扫描间距在扫描前进行调整,以提高检测效率。 8.1.11检测环境应避免强电磁和振动干扰 8.1.12推荐采用压电换能器接收激光激励的超声波,在不能采用压电换能器的情况(比如高温或非接触等)下,也可采用电磁超声换能器或激光干涉仪等方式接收超声波,但需通过检测工艺试验确认其接收灵敏度和对缺陷的检测能力是否达到要求 8.1.13检测结果需经专业培训的技术人员解读,否则可能结果误判。 8.1.14在保证接收信号有足够信噪比(大于6dB)的条件下,激光输出功率应尽量低,以免激光烧蚀工件表面。激光入射角(与工件界面法线夹角)应不大于60°(参见参考文献[1])。 8.2 检测工艺试验与设备校验
检测工艺试验是用人工参考试块来调整和确定检测设备的检测参数、检测灵敏度并确定接收探头,只有检测工艺试验可以检测出参考试块中的所有人工缺陷,并在超声波传播图像或最大振幅图中清晰地反映人工缺陷回波或形状时,才满足检测要求。检测工艺试验满足检测要求即视为校验完毕。
检测设备调整和校验过程中,脉冲激光器距人工参考试块的距离以及接收探头所处位置等设置,应与实际生产检验时一致。
检验过程中每隔一段固定时间(建议每4h)校验一次,并且在操作人员换班或在检验的开始和结束时各校验一次。
更换检验对象时,需用与之相应的人工参考试块重新进行检测工艺试验和设备校验。 8.3信号接收装置的选择及调整
选择适当工作频率和接收方向(倾斜角度)的接收探头,在适当(与普通超声检测相同)的位置放置接收探头,调整接收探头与放大器,使检测信号信噪比大于6dB。在扫描过程中接收状态应保持不变。
通常,常规超声检测中放置发射探头的最佳位置,即为本检测方法中放置接收探头的位置。 8.4重复频率的设定
重复频率不应过高,以保证前一个激光脉冲产生的超声波对后一个激光脉冲产生的超声波的影响可以忽略,调整其激励周期,使前一次激光发射产生的超声波充分衰减后再进行后续激光脉冲激励。 8.5扫描参数的设定
扫描参数应包括:
-扫描区域的基准点:通常选扫描区域的中心点为扫描区域的基准点;一扫描距离:激光出射口(扫描镜面)到基准点的距离为扫描距离,通常在设备放置好后通过人
工测量或自动测距装置测量;扫描步长:取决于要求的空间分辨率和检测缺陷的灵敏度(一般步长与空间分辨率相当);一扫描频率:与所设定的重复频率一致(与材料衰减特性有关,一般为100Hz~10kHz);一扫描范围:X轴和Y轴方向各自的扫描长度,取决于要求的检测区域。
8.6激光输出的设定
激光激励频率范围宜选为0~10kHz,在保证接收信号有足够的信噪比(大于6dB)的条件下激光输出能量应尽量低,以免激光烧蚀工件表面。如果激光出射口到被检部位的距离远,应调整脉冲激光器的聚焦装置,使激光照射在工件上的光斑直径足够小。
4
JB/T13467—2018
8.7A/D转换器的参数设定
A/D转换器的参数应包括:
-采样频率f:推荐大于接收探头中心频率f的10倍,即f>10f:采样长度N:取决于接收探头至检测区域最远点的距离d、材料声速v及采样频率f,N>f,d/v; -采样延时时间t:取决于接收探头至检测区域最近点的距离d及材料声速v,t
采样精度(A/D转换分辨率)和采样内置缓存大小通常由设备决定,不作为检测调整参数:前置放
大器的增益设置应使接收探头的超声波信号相对于A/D的量程不至于太大,也不至于太小。 8.8扫描
由计算机控制脉冲激光器扫描激励超声波,工件上各扫描点的空间位置和超声波传播图像的像素位置应相互对应,并以文件形式存储空间位置各点的超声波信号波形数据。 8.9超声波传播图像处理 8.9.1概述
超声波传播图像处理是对以文件形式存储的空间位置各点的超声波信号波形数据进行处理。成像系统对模数转换处理后的数字化的激光激励超声波信号按工件检测面上的扫描点对应的空间投影坐标进行排列,并对激光激励超声波信号的各个时刻的振幅值进行灰度调制生成声场图像,再对声场图像按时间序列连续显示,生成动态的声场视频(即超声波传播的动态图像)。成像系统可以产生超声波传播的静止、动态、最大振幅等三种类型的图像。 8.9.2超声波传播的静止图像
将扫描区域(通常以X-Y坐标系表示)各点的超声波信号在某一时刻的幅度以色阶或灰度表示成为一幅(一顿)静止图像,该图像也称为这个时刻的超声波声场快照。各点的超声波信号在成像前通常需进行适当的滤波等处理。 8.9.3超声波传播的动态图像
将8.9.2一顿一顿的超声波传播静止图像按采样时间序列通过软件制成动态视频,通过视频播放就可观察从接收探头“发出”的超声波传播到扫描检测区域的传播过程。通过观察这种超声波传播过程,可以分析传播中的超声波与检测区域工件结构或缺陷的作用过程。如果缺陷比较小,视频中的缺陷对超声波传播的影响不够明显,需要通过特定的分析软件进行进一步的处理。 8.9.4超声波传播的最大振幅图像
在X轴(横轴)取X轴方向扫描点的位置,在Y轴(纵轴)取Y轴方向扫描点的位置,以各扫描点的激光照射时刻为基准,将各扫描激励点对应的接收波形在指定的时间段或频率段内的最大振幅值转换为相应的图像灰度值,由此得到最大振幅图像。
9检测结果的分析与评价
9.1检测结果的分析
检测结果的分析方法有多种:
通过观察工件扫描检测区域的超声波传播过程的视频,可直观地观察到有无缺陷,可对缺陷位置进行定位,但一般不能对缺陷进行定量测量;
5
ICS 19.100 J04 备案号:64018—2018
JB
中华人民共和国机械行业标准
JB/T13467—2018
无损检测 扫描激光激励超声场
可视化检测方法
Non-destructivetesting-Testmethodforscanninglaserexcitationultrasonic
field visualizing inspection technique
2018-12-01实施
2018-04-30发布
中华人民共和国工业和信息化部发布
JB/T13467—2018
目 次
前言... 范围
I
1
2规范性引用文件 3术语和定义 4方法概要. 5人员要求. 6 检测系统. 7 参考试块 8 检测...
检测结果的分析与评价 10检测记录与报告附录A(资料性附录) 典型损伤和缺陷参考文献
9
11
图1 检测工件 碳纤维复合材料,图2 最大振幅图图3 超声波声场快照图4 差分滤波处理得到的超声波声场图像图A.1 工件(L型CFRP)图A.2 最大振幅图(L型CFRP)图A.3 T=34.79μs时刻的超声波声场快照(L型CFRP)图A.4 工件(T形角焊缝)图A.5 最大振幅图(T形角焊缝)图A.6 T=18.59μs时刻的超声波声场快照(T形角焊缝)图A.7 工件(钢管端部)图A.8 最大振幅图(钢管端部)图A.9 T=11.67μs时刻的超声波声场快照(钢管端部)
6 6 6
S
d
C
0
.10 .10 .10
1
JB/T13467—2018
前 言
本标准按照GB/T1.1一2009给出的规则起草。 本标准由中国机械工业联合会提出。 本标准由全国无损检测标准化技术委员会(SAC/TC56)归口。 本标准起草单位:西安金波检测仪器有限责任公司、爱德森(厦门)电子有限公司、中国科学院金
属研究所、中国科学院声学研究所、北京航空材料研究院、南昌航空大学。
本标准主要起草人:王波、蔡桂喜、沈建中、史亦韦、林俊明、卢超、赵晋成,本标准为首次发布。
II
JB/T13467—2018
无损检测扫描激光激励超声场
可视化检测方法
1范围
本标准规定了扫描激光激励超声场可视化检测方法。 本标准适用于对壁厚不大于50mm的固体材料或工件的表面、近表面和内部的缺陷(如裂纹、气
孔、腐蚀等)进行扫描激光激励超声波传播可视化的无损检测。
本标准不适用于超声波传播衰减较大(接收信号的信噪比小于6dB)及曲率较大(入射激光与工件界面法线夹角大于60°)的复杂形面固体材料或工件。
2规范性引用文件
下列文件对于本文件的应用是必不可少的。凡是注日期的引用文件,仅注日期的版本适用于本文件。凡是不注日期的引用文件,其最新版本(包括所有的修改单)适用于本文件
GB 7247.1 激光产品的安全第1部分:设备分类、要求 GB/T9445无损检测 人员资格鉴定与认证 GB/T12604.1无损检测术语超声检测 GB/T15313 激光术语
3术语和定义
GB/T12604.1和GB/T15313界定的以及下列术语和定义适用于本文件。
3.1
最大振幅图 maximum amplitude image 该图像中每一点显示的是扫查区域中对应该点的超声波信号在指定时间段内和/或频率段内的最大
振幅值。 3.2
超声波传播图像 象ultrasonicwavepropagationimage 显示随时间变化的工件扫查区域内超声波传播过程中波幅分布的一顿顿图像。
3.3
超声波声场快照 snapshotvisualization ofultrasonicwave 超声波传播过程中某一个确定时刻超声波声场的空间分布所构成的图像。 注:表现超声波声场的物理量可以是位移,也可以是应力分量。
4方法概要
采用脉冲激光束照射固体材料表面时,材料表面发生热弹性效应产生超声波,通过接收装置采集这种超声波信号,并通过放大、滤波及软件处理,得到材料表面超声波传播过程的可视化结果,从而对材料内外部缺陷进行可视化无损检测。
-
JB/T13467—2018
5人员要求
5.1从事扫描激光激励超声场可视化检测的检测人员,应掌握一定的激光超声可视化检测知识,并掌握一定的被检工件材料与加工工艺知识,了解可能存在的缺陷及检验目的和需求。 5.2按照本标准实施检测的人员,应按GB/T9445或合同各方同意的体系进行资格鉴定与认证,并由雇主或其代理对其进行岗位培训和操作授权。
6检测系统
6.1系统组成
扫描激光激励超声场可视化检测系统应包括脉冲激光器、激光扫描装置、信号接收装置、前置放大器、数据采集及成像系统等。 6.2脉冲激光器
脉冲激光器需满足以下条件:
脉冲激光器的输出能量1应可调节,入射激光与工件界面法线夹角应小于60°,其输出的激光能量应足以在被检工件中激励出一定强度的超声波,以与超声接收探头的接收灵敏度相适应,其单次输出能量I的稳定度△I/I应优于5%;脉冲激光器的激光脉冲宽度应能使脉冲激光束所激励的超声波具有适当的频率带宽,一般使用的脉冲激光器脉冲宽度约为1ns~50ns,激励超声波的频率带宽约在20MHz~1000MHz之间; 一为获得清晰的超声波传播图像,脉冲激光器应能产生足够小的激光光斑,激光出射口的光斑直径宜不大于1mm;
一为减小激光激励距离变化对光斑尺寸的影响,脉冲激光器的发散角应足够小;一脉冲激光器的激光激励重复频率应能调节,检测中选用适当的重复频率,以保证超声波声场图
像的图像质量和检测效率:一脉冲激光器的激光激励与超声波信号接收应有较好的同步功能。
6.3激光扫描装置
激光扫描装置用于使激光束在工件上扫描并激励出点源超声波,形成激光束与工件之间的相对扫描
运动。激光扫描装置应满足以下要求:
一对于被检部位,应具有对长度方向(X轴)以及宽度方向(Y轴)分别进行扫描的独立控制功能;一扫描步长宜小于超声接收探头频率带宽所对应的最小超声波波长的一半:一扫描、激光激励、数据采集三者应同步。
6.4信号接收装置
信号接收装置为压电超声(横波、纵波及表面波)探头。根据工件大小及形状复杂度可使用一个或多个压电超声探头。根据检测深度可适当选用垂直压电超声探头或斜角压电超声探头,
接收探头的频率范围推荐在30kHz~10MHz之间,当选用高频探头(大于1MHz)时,应考虑高频超声波在工件中传播时的传播衰减和扩散衰减对检测灵敏度降低的影响,应确保接收探头在高频带范围内有足够的接收灵敏度。
压电超声探头应采用适当的耦合剂涂在工件上,检测过程中应保持耦合的稳定性。
2
JB/T13467—2018
6.5前置放大器
前置放大器的频率响应应与接收探头的频率响应相匹配,其增益推荐采用40dB、60dB。 6.6数据采集及成像系统
基于扫描装置的同步信号使A/D转换器对激光激励的超声波信号进行同步采集,将采集到的超声波信号存入计算机。成像系统对该时间序列数字信号按工件检测面上的扫描点对应的空间投影坐标进行排列,并对存储的超声波信号在各个时刻的振幅值进行灰度调制生成超声波声场图像(静止图像,即超声波声场快照),再对所述声场图像按时间序列连续显示,生成动态的超声波声场视频(即超声波传播的动态图像)。
数据采集及成像系统应满足以下要求:
A/D转换器应具有适当的采样速度、分辨率和采样点数,A/D转换器缓存和计算机内存应足够大;数据采集速度应与激光扫描速度相匹配;
-
一成像系统内存及处理速度应能满足超声波成像和超声波传播图像视频显示的要求。
7参考试块
参考试块主要用于检测系统的校验和检测灵敏度的设定。 参考试块应具有与被检工件相同或相近的材质,相同的形状、公称尺寸和相似的表面状况、热处理
条件及声学特性(如声速、衰减系数)。
根据供需双方的协议确定人工参考试块上人工缺陷的类型、位置、方向和尺寸。用钻入工件表面下
一定深度的沉孔或球形凹坑模拟腐蚀缺陷;用刻槽模拟工件表面裂纹;用与工件表面倾斜一定角度的刻槽模拟折叠;用平底孔模拟工件内部的夹杂和分层,为使平底孔的圆柱面不产生超声波的反射,平底孔需进行塞封,只保留其孔底。
参考试块上人工缺陷的位置、尺寸应采用复型、光学等测量方法加以确认。
8检测
8.1检测要求 8.1.1扫描激光激励超声场可视化检测时需要按GB7247.1的要求采取适当的防护措施。 8.1.2激光输出功率较大时,激光会在被检工件表面造成一定的烧蚀,检测时需要适当控制脉冲激光器的输出功率。 8.1.3在检测之前应适当对工件表面浮尘或油污进行清理。 8.1.4建议应针对不同工件或产品可能存在的缺陷类型和缺陷可能产生的位置,制作人工缺陷参考试块。人工缺陷的类型、位置、方向和尺寸等应尽可能接近实际情况。 8.1.5扫描装置与工件之间不应有任何阻隔激光光束的障碍物存在。 8.1.6应通过检测工艺试验确定扫查区域大小,以保证区域内各处均能达到所需的检测灵敏度, 8.1.7在设定脉冲激光的输出功率时,应考虑激光激励的能量强度对内部缺陷检测能力的影响,优化检测工艺参数。 8.1.8工件的光洁表面会反射激光,不利于吸收激光能量激励超声波,因此,可以考虑在工件表面涂覆一层能吸收光能的薄涂层,以提高工件中激光激励超声的强度,并在检测工艺参数中明确对涂层的要求。 8.1.9异型结构或复杂结构工件在扫描激光激励超声场可视化检测时,需要考虑工件结构可能引起的超声波模态转换对检测的影响。
3
JB/T13467—2018
8.1.10扫描过程中扫描装置与工件应尽可能保持相对静止,可以根据检测精度要求对扫描速度及扫描间距在扫描前进行调整,以提高检测效率。 8.1.11检测环境应避免强电磁和振动干扰 8.1.12推荐采用压电换能器接收激光激励的超声波,在不能采用压电换能器的情况(比如高温或非接触等)下,也可采用电磁超声换能器或激光干涉仪等方式接收超声波,但需通过检测工艺试验确认其接收灵敏度和对缺陷的检测能力是否达到要求 8.1.13检测结果需经专业培训的技术人员解读,否则可能结果误判。 8.1.14在保证接收信号有足够信噪比(大于6dB)的条件下,激光输出功率应尽量低,以免激光烧蚀工件表面。激光入射角(与工件界面法线夹角)应不大于60°(参见参考文献[1])。 8.2 检测工艺试验与设备校验
检测工艺试验是用人工参考试块来调整和确定检测设备的检测参数、检测灵敏度并确定接收探头,只有检测工艺试验可以检测出参考试块中的所有人工缺陷,并在超声波传播图像或最大振幅图中清晰地反映人工缺陷回波或形状时,才满足检测要求。检测工艺试验满足检测要求即视为校验完毕。
检测设备调整和校验过程中,脉冲激光器距人工参考试块的距离以及接收探头所处位置等设置,应与实际生产检验时一致。
检验过程中每隔一段固定时间(建议每4h)校验一次,并且在操作人员换班或在检验的开始和结束时各校验一次。
更换检验对象时,需用与之相应的人工参考试块重新进行检测工艺试验和设备校验。 8.3信号接收装置的选择及调整
选择适当工作频率和接收方向(倾斜角度)的接收探头,在适当(与普通超声检测相同)的位置放置接收探头,调整接收探头与放大器,使检测信号信噪比大于6dB。在扫描过程中接收状态应保持不变。
通常,常规超声检测中放置发射探头的最佳位置,即为本检测方法中放置接收探头的位置。 8.4重复频率的设定
重复频率不应过高,以保证前一个激光脉冲产生的超声波对后一个激光脉冲产生的超声波的影响可以忽略,调整其激励周期,使前一次激光发射产生的超声波充分衰减后再进行后续激光脉冲激励。 8.5扫描参数的设定
扫描参数应包括:
-扫描区域的基准点:通常选扫描区域的中心点为扫描区域的基准点;一扫描距离:激光出射口(扫描镜面)到基准点的距离为扫描距离,通常在设备放置好后通过人
工测量或自动测距装置测量;扫描步长:取决于要求的空间分辨率和检测缺陷的灵敏度(一般步长与空间分辨率相当);一扫描频率:与所设定的重复频率一致(与材料衰减特性有关,一般为100Hz~10kHz);一扫描范围:X轴和Y轴方向各自的扫描长度,取决于要求的检测区域。
8.6激光输出的设定
激光激励频率范围宜选为0~10kHz,在保证接收信号有足够的信噪比(大于6dB)的条件下激光输出能量应尽量低,以免激光烧蚀工件表面。如果激光出射口到被检部位的距离远,应调整脉冲激光器的聚焦装置,使激光照射在工件上的光斑直径足够小。
4
JB/T13467—2018
8.7A/D转换器的参数设定
A/D转换器的参数应包括:
-采样频率f:推荐大于接收探头中心频率f的10倍,即f>10f:采样长度N:取决于接收探头至检测区域最远点的距离d、材料声速v及采样频率f,N>f,d/v; -采样延时时间t:取决于接收探头至检测区域最近点的距离d及材料声速v,t
采样精度(A/D转换分辨率)和采样内置缓存大小通常由设备决定,不作为检测调整参数:前置放
大器的增益设置应使接收探头的超声波信号相对于A/D的量程不至于太大,也不至于太小。 8.8扫描
由计算机控制脉冲激光器扫描激励超声波,工件上各扫描点的空间位置和超声波传播图像的像素位置应相互对应,并以文件形式存储空间位置各点的超声波信号波形数据。 8.9超声波传播图像处理 8.9.1概述
超声波传播图像处理是对以文件形式存储的空间位置各点的超声波信号波形数据进行处理。成像系统对模数转换处理后的数字化的激光激励超声波信号按工件检测面上的扫描点对应的空间投影坐标进行排列,并对激光激励超声波信号的各个时刻的振幅值进行灰度调制生成声场图像,再对声场图像按时间序列连续显示,生成动态的声场视频(即超声波传播的动态图像)。成像系统可以产生超声波传播的静止、动态、最大振幅等三种类型的图像。 8.9.2超声波传播的静止图像
将扫描区域(通常以X-Y坐标系表示)各点的超声波信号在某一时刻的幅度以色阶或灰度表示成为一幅(一顿)静止图像,该图像也称为这个时刻的超声波声场快照。各点的超声波信号在成像前通常需进行适当的滤波等处理。 8.9.3超声波传播的动态图像
将8.9.2一顿一顿的超声波传播静止图像按采样时间序列通过软件制成动态视频,通过视频播放就可观察从接收探头“发出”的超声波传播到扫描检测区域的传播过程。通过观察这种超声波传播过程,可以分析传播中的超声波与检测区域工件结构或缺陷的作用过程。如果缺陷比较小,视频中的缺陷对超声波传播的影响不够明显,需要通过特定的分析软件进行进一步的处理。 8.9.4超声波传播的最大振幅图像
在X轴(横轴)取X轴方向扫描点的位置,在Y轴(纵轴)取Y轴方向扫描点的位置,以各扫描点的激光照射时刻为基准,将各扫描激励点对应的接收波形在指定的时间段或频率段内的最大振幅值转换为相应的图像灰度值,由此得到最大振幅图像。
9检测结果的分析与评价
9.1检测结果的分析
检测结果的分析方法有多种:
通过观察工件扫描检测区域的超声波传播过程的视频,可直观地观察到有无缺陷,可对缺陷位置进行定位,但一般不能对缺陷进行定量测量;
5