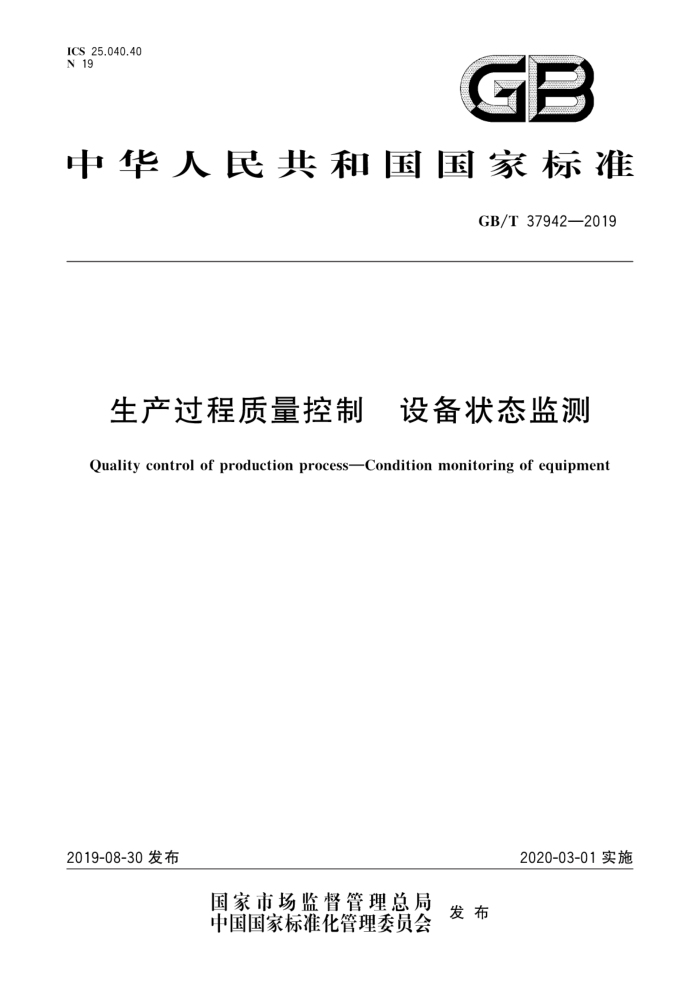
ICS 25.040.40 N 19
GB
中华人民共和国国家标准
GB/T37942—2019
生产过程质量控制 设备状态监测
Quality control of production processCondition monitoring of equipment
2019-08-30发布
2020-03-01实施
国家市场监督管理总局中国国家标准化管理委员会
发布
GB/T37942—2019
目 次
前言引言范围
1
2 规范性引用文件 3 术语和定义缩略语
4
总体要求 5.1状态监测系统结构 5.2 状态监测基本要求 6状态监测数据采集 6.1 数据选择原则 6.2 数据分类 6.3 数据采集方法状态监测数据处理
5
7
7.1 数据预处理 7.2 状态判别方法 7.3 决策支持 8信息输出与显示 8.1 输出内容 8.2 信息显示附录A(资料性附录) 设备状态监测数据举例附录B(资料性附录) 设备状态监测功能块模型附录C(资料性附录) 生产线状态监测层级案例
GB/T 37942—2019
前言
本标准按照GB/T1.1一2009给出的规则起草。 本标准由中国机械工业联合会提出。 本标准由全国工业过程测量控制和自动化标准化技术委员会(SAC/TC124)归口。 本标准起草单位:无锡职业技术学院、机械工业仪器仪表综合技术经济研究所、珠海格力电器股份
有限公司、安徽苏瑞智能科技有限公司、江苏新合益机械有限公司、东风设计研究院有限公司、中国石油大学、浙大中控技术股份有限公司、电力规划总院有限公司、中国科学院沈阳自动化研究所、辽宁大学、 中信戴卡股份有限公司、绵阳市维博电子有限责任公司、大连誉洋工业智能有限公司。
本标准主要起草人:吴慧媛、王成城、唐立平、游和平、赵华、张晋宾、王骏、郭琼、俞张勇、王金江、 宋岩、黄亮、彭正红、俞文光、王春喜、黄文君、李栋、陈进、杭文伟、饶启琛、李文军、刘阳、肖鹏、曹国兴、 朱小飞、姜作诚、苗盈。
一
GB/T 37942—2019
引言
设备状态监测是生产过程质量控制的重要内容之一,其任务是采集和记录生产过程中设备状态,目的是为实现设备状态预测和故障诊断提供信息和数据支持,为离散型制造领域生产过程提供参考信息。
通过设备状态监测,可以实现设备动态与量化管理,执行预测性维护并且向上一级信息系统提供有
效的设备数据。建立设备状态监测系统是实现数字化车间的基础条件之一。
本标准描述了设备状态监测的总体要求、数据采集、数据处理、信息输出与显示,主要可用于离散型制造领域企业。
Ⅱ
GB/T37942—2019
生产过程质量控制 设备状态监测
1范围
本标准规定了离散型制造领域数字化车间的生产现场设备状态监测的总体要求、数据采集、数据处
理、信息输出与显示
本标准适用于离散型制造领域数化车间生产过程质量控制中的设备状态监测系统,
2规范性引用文件
2
下列文件对于本文件的应用是必不可少的。凡是注日期的引用文件,仅注日期的版本适用于本文件。凡是不注日期的引用文件,其最新版本(包括所有的修改单)适用于本文件
GB/T37393—2019 数字化车间通用技术要求
3 :术语和定义
GB/T37393一2019界定的以及下列术语和定义适用于本文件。
3.1
聚合 aggregation 对复杂设备或系统状态和趋势监测数据进行选取、加权、分析、判别,从而获得设备或系统状态数据
的转化过程。 3.2
基线数据 baseline data 在各种过程中正常状态下,设备特征值允许比较计算或测量的基准值。
3.3
数据采集 data acquisition 通过传感器或系统检测与收集反映设备状态信息的过程。
3.4
数据处理 data processing 对采集的电信号或非电信号进行处理,以便抽取出反映设备状态特征的过程注:对信号进行提取、变换、分析、综合等处理过程的统称
3.5
维修 多repair 设备技术状态劣化或发生故障后,为恢复其功能而进行的技术活动。 注:包括各类计划维修和计划外的故障维修及事故处理。 [GB/T37393—2019.定义3.17
3.6
阔值 threshold 设备特征值的参考临界值。
1
GB/T37942—2019
缩略语
4
下列缩略语适用于本文件。 ERP:企业资源计划(EnterpriseResourcePlanning) MES:制造执行系统(ManufacturingExecutionSystem) MTBF:平均故障间隔时间(MeanTimeBetweenFailure) MTTR:平均修复时间(MeanTimeBetweenRepairs) OEE:设备综合利用率(OverallEquipmentEffectiveness) RFID:射频识别(RadioFrequencyIdentification)
5总体要求
5.1 状态监测系统结构
设备状态监测系统结构主要包括状态监测数据采集、状态监测数据处理和信息输出与显示三部分
设备状态监测系统结构如图1所示。
信息输出与显示
现场标牌、指示灯状态、显示屏、广播/蜂鸣器、操作终端、MES、ERP...
状态监测数据处理
决策支持
阅值判别
聚合判别
数据预处理
状态监测数据采集
数据采集器(条码扫描器、RFID
传感器(电压、电流、温度、 液位、位移、速度、加速度
数据采集器.
设备及系统(加工设备、组装设备、物流设备、检测设备、辅助设备、MES、ERP.)
图1 设备状态监测系统结构
2
GB/T37942—2019
状态监测数据采集,主要由设备及系统、传感器和数据采集器完成。设备及系统主要提供设备或系
统的基础、统计、管理等信息;传感器主要用来采集设备及相关联环境的状态与过程信息,传感器可为设备内部传感器,也可为依据用户需求加装的外部传感器;数据采集器主要提供生产现场设备过程信息,如条码扫描器、RFID数据采集器等。
状态监测数据处理包含数据预处理、阀值/聚合判别与决策支持。数据预处理是对数据采集获得的信息进行预处理、特征分析,从而获得表征设备状态特征的数据。值/聚合判别与决策支持是对设备状态表征数据进行处理,从而获得设备状态判别结果的方法
信息输出与显示,是将设备状态判别结果,输出至设备显示模块或相关管理系统,主要为MES与 ERP系统。其中MES或ERP系统中与设备状态监测相关的模块主要是制造数据管理、质量管理、设备管理、工具工装管理、成本管理、生产过程控制等。 5.2状态监测基本要求
状态监测应满足下列要求:
在线监测:在被测设备处于运行或待机状态条件下,对设备状况进行自动监测,对无条件或不宜在线监测的设备状态数据对此不作要求;数字化:设备状态监测信息应能够转成数字信息;
一数据一致性:设备状态监测系统由若干设备状态监测单元组成,其数据相互传输与格式均应遵
循相同通信协议与规约;可靠性:设备状态监测系统应具备在规定的条件下和规定的时间内完成规定功能的能力。常用可靠度、MTBF、MTTR、可用度、有效寿命等指标衡量。
6状态监测数据采集
6.1 数据选择原则
生产质量控制相关的设备状态是依据若干反映设备状态特征的数据进行预测与判断,设备状态监测数据的选择原则为
关联性:其能全面表征监测设备的能力;灵敏性:监测参数随着设备状态的变化应比其他参数的变化更明显;
-
一稳定性:在相同测试条件下,所测得的监测参数值具有良好的重复性;一可解释性:监测参数具备一定物理意义,能用数字表示,可以量化。
6.2数据分类
按设备数据采集来源分类,需要对以下数据进行采集:
来源于设备或系统的数据:包含设备基本数据和经系统计算获取的统计数据及管理数据。设备基本数据包含设备名称、型号、规格、生产厂家、资产编号、采购及人库时间、运行程序等;统计数据包含开机率、主轴运转率、主轴负载率、设备运行率、故障率、OEE、设备生产率等;管理数据包含设备开关机、故障报警记录等
一来源于传感器的数据:按形式可分为模拟量、数学量;按性质可分为静态量、动态量;按被测物
理量可分为电压、电流、位置(行程)、温度、压力、液位、振动等来源于数据采集器的数据:包含人员、物料、设备、工装等的编码、位置、状态信息等。
设备状态监测数据的示例参见附录A。
6.3数据采集方法
数据的采集方法有人工输入、自动输入两种。人工输人采集数据量有限、速度慢,可对采集数据进行
3
GB/T37942—2019
人工筛选与处理;自动输入采集数据量大、速度高,可连续甚至实时监测,按指定方法自动筛选与处理。为提高设备状态监测系统在线检测水平,对设备状态数据应尽可能采取自动输人方式,对于无连续监测要求或自动采集困难的设备状态数据采取人工输人。按数据采集来源,设备状态数据采集方法具体如下:
一来源于设备或系统的数据:设备基本数据可采用通过手动输入,或扫描设备条码等方法进行采
集,或系统自动读取输入设备状态监测系统(如果设备支持);系统统计及管理数据可自动读取输入设备状态监测系统。
一来源于传感器的数据:自动输人至设备状态监测系统。 一来源于数据采集器的数据:可通过计算机终端、条码扫描仪、移动手持终端等方式人工或自动
输入设备状态监测系统。
7状态监测数据处理
7.1数据预处理
设备状态监测系统数据预处理流程与步骤如图2所示。
信号
信号
原始 预处理 中间 特征 状态
设备 采集
分析
表征
被测量
数据
数据
图2 数据预处理流程与步骤示意图
其中各部分具体含义如下:
设备被测量:能经传感器、数据采集器、被测设备或系统采集,并与设备状态特征值产生确定映射且可溯源的数据;
一原始测量值:设备状态及过程被测量经传感器信号采集未经处理的数据:一中间数据:通过传感器、设备或系统在运行中获取的动态或趋势数据,经调理或计算后,去除外
部干扰或无效信号的数据;状态表征数据:中间数据经特征提取后能表征设备状态特征的数据。
当设备被测量为静态量(比如温度、液位等)时,需依据信号与干扰情况,进行线性化或非线性化处理,以及滤波处理,常见的滤波处理有限幅滤波、限速滤波、中值滤波、平均算术滤波、加权平均算术滤波、防脉冲干扰平均值滤波、一阶滞后滤波等,信号预处理与特征分析不是必需的;当设备被测量为动态量(比如振动、应力、应变等)时,可依据需求进行幅值域分析、时域分析与频谱分析。 7.2状态判别方法 7.2.1阈值判别
基线数据可以设定为固定值,或者随着设备运行而改变的动态目标值,这取决于被监测的条件变量。 国值应采取绝对值或相对于基线数据(如果存在)的偏差形式。阈值绝对值为没有任何参考值情况
下有效的固定极限;阈值偏差值为与基线数据的绝对或相对偏差极限
國值的使用方式如图3所示。M为被监测设备特征值变化曲线,R为正常运行的基线数据,thA
为上限阈值,thB为下限阅值,为阈值thA、thB相对于基线数据R的偏差值,该值可为绝对值或百分比值。其中,图3a)的阈值thA、thB为没有基线数据的绝对值,是常数;图3b)的阈值thA、thB为相对于固定基线数据R的偏差值;图3c)的阈值thA、thB为相对于动态变化的基线数据R的偏差值
4