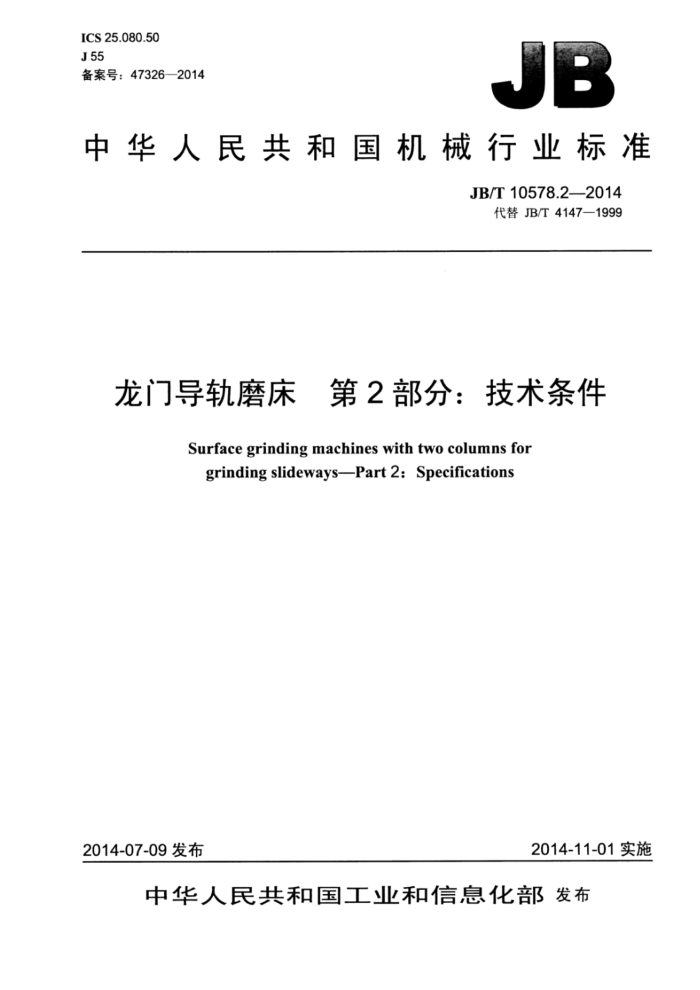
ICS 25.080.50 J55 备案号:47326—2014
、
中华人民共和国机械行业标准
JB/T10578.2—2014
代替JB/T4147—1999
龙门导轨磨床 第2部分:技术条件
Surface grinding machines with two columns for
grinding slideways-Part 2: Specifications
2014-11-01实施
2014-07-09发布
中华人民共和国工业和信息化部发布
JB/T10578.2—2014
目 次
前言.. 范围
1
1
2规范性引用文件.
一般要求.. 4 附件和工具.
3
安全卫生。 加工和装配质量机床空运转试验. 7.1 静压导轨浮起量试验. 7.2 温度和温升试验. 7.3 磨头的垂直与横向进给精度检验 7.4 工作台运行平稳性试验。 7.5 横梁升降的试验. 7.6 磨头空运转试验. 7.7 砂轮修整器空运转试验 8机床的负荷试验(抽查)
5 6 7
机床的精度检验
9
10直线坐标最小设定单位试验 10.试验方法 10.2 误差的计算方法 10.3 公差.
10.4检验工具
JB/T10578.2—2014
前言
JB/T10578《龙门导轨磨床》分为两个部分:
第1部分:型式与参数:第2部分:技术条件。
本部分为JB/T10578《龙门导轨磨床》的第2部分。 本部分按照GB/T1.1一2009给出的规则起草。 本部分代替JB/T4147—1999《龙门导轨磨床技术条件》,与JB/T4147—1999相比主要技术变化如
下:
一修改了前言:一修改了规范性引用文件(见第2章,1999年版的第2章);
修改了一般要求(见第3章,1999年版的第3章);修改了手柄、手轮操纵力表(见5.6,1999年版的5.5);修改了机床零件的名称(见6.3,1999年版的6.3);修改了机床清洁度的检验(见6.10,1999年版的6.10);修改了温度与温升试验(见7.1,1999年版的7.2);修改了磨头的垂直与横进给精度检验(见7.3,1999年版的7.3);修改了检验万能磨头回转精度的角度(见9.3,1999年版的9.3);增加了对砂轮防护罩的要求(见5.5);增加了热检项目(见9.4);将机床的负荷试验中的悬自段改为章节(见8.1,1999年版的第8章)。
本部分由中国机械工业联合会提出。 本部分由全国金属切削机床标准化技术委员会(SAC/TC22)归口。 本部分起草单位:上海重型机床厂有限公司。 本部分主要起草人:蔡新、沈利、徐银荣、陈明连。 本部分所代替标准的历次版本发布情况为:
JBn4147-1985JB/T4147--1999.
II
JB/T10578.2——2014
龙门导轨磨床 第2部分:技术条件
1范围
JB/T10578的本部分规定了一般用途的龙门导轨磨床制造和验收的要求。 本部分适用于最大磨削宽度为800mm~3150mm最大磨削长度为2000mm~16000mm的龙门
导轨磨床。
2规范性引用文件
下列文件对于本文件的应用是必不可少的。凡是注日期的用文件,仅注日期的版本适用于本文
件。凡是不注日期的引用文件,其最新版本(包括所有的修改单)适用于本文件。
GB5226.12008 机械电气安全机械电气设备第1部分:通用技术条件 GB/T5288—2007 龙门导轨磨床精度检验 GB/T9061—2006 金属切削机床通用技术条件 GB15760-2004 金属切削机床安全防护通用技术条件 GB/T16769--2008 金属切削机床噪声声压级测量方法 GB/T17421.1—1998 机床检验通则第1部分:在无负荷或精加工条件下机床的几何精度 GB/T23572—2009 金属切削机床 液压系统通用技术条件 GB/T25372—2010 金属切削机床 精度分级 GB/T25373—2010 金属切削机床 装配通用技术条件 GB/T25374—2010 金属切削机床 清洁度的测量方法 GB/T25376—2010 金属切削机床 机械加工件通用技术条件 JB4029-2000磨床砂轮防护罩 安全防护技术要求
3一般要求
3.1按本部分验收机床时,应同时对GB/T9061—2006、GB/T25373-2010、GB/T25376—2010中未经本部分具体化的其余验收项目进行检验。 3.2机床按GB/T25372一2010的规定为II级精度的机床。
4附件和工具
4.1机床应随机供应表1所列的附件和工具。
表1 数量 1套 3套
备注
附件及工具名称冷却液箱
用途冷却工件装夹砂轮
砂轮卡盘
碗形砂轮卡盘根据使用情况可适当减少
1
JB/T10578.2-2014
表1 (续)
附件及工具名称
用途平衡砂轮起吊砂轮
备注周边和万能磨头各1套
数量 2套 1套
平衡轴砂轮吊杆床身检具砂轮修整器
测量床身安装水平 1套
双V形床身导轨可用圆检验棒周边和万能磨头修整器各1套
2套
修整砂轮磨头主轴调整角度 1件
万能磨头回转扳手
有机动机构可省略
卸砂轮扳手卸砂轮螺塞高压油枪管接头高压油枪进给用摇手
2 件 2件
拆卸砂轮卡盘拆卸砂轮卡盘拆卸锥形滚动轴承 1件拆卸锥形滚动轴承 1件调整磨头水平位置 1套调整安装水平
卸周边和万能磨头砂轮卡盘扳手各1件卸周边和万能磨头砂轮卡盘螺塞各1件磨头不采用滚动轴承结构的不提供磨头不采用滚动轴承结构的不提供
无手动机构的不提供数量按机床的规格提供数量按机床的规格提供
垫铁
1套 1套 1套 2套 1套
地脚螺栓及其垫圈螺母
压紧床身底脚
标准扳手不提供
扳手传动带平衡架
辅助传动用平衡砂轮
备件1套
4.2 机床可按协议供应特殊附件。
5 安全卫生
5.1 1工作台往复运动、横梁升降、磨头垂直和水平移动应有限位或防止碰撞的保险装置。 5.2磨头横向快速移动与砂轮旋转运动、横梁升降与工作台纵向运动及砂轮旋转运动等应有安全联锁装置。 5.3床身、立柱、横梁导轨面应有防护装置。 5.4机床运转时不应有非正常的尖叫声和冲击声。在空运转条件下,机床的噪声声级应不超过 83dB(A)。机床噪声的测量方法按GB/T16769—2008的规定。 5.5磨削砂轮的防护罩应符合JB4029—2000的规定。 5.6手轮、手柄操纵力不应大于表2的规定值,磨头水平和垂直移动手柄或手轮以及砂轮修整器操作手轮操纵力按“经常用的”手轮进行考核,其他手柄或手轮操纵力按“不经常用的”手轮进行考核。
表2
机床质量
操纵力N
不经常用的
经常用的
t ≤10 >10
80 120
120 160
5.7 按本部分验收机床时,应同时对GB15760—2004、GB5226.12008、GB/T23572-—2009中未经本部分具体化的其余有关验收项目进行检验。
6 加工和装配质量
6.1下列铸件为重要铸件,应在粗加工后进行时效处理: 2
JB/T10578.2—2014
a)床身; b)工作台; c)立柱; d)横梁; e)磨头溜板; f)垂直拖板。
6.2床身,工作台,立柱,横梁等为易磨损主要零件,应采用与寿命相适应的耐磨措施。 6.3床身与工作台导轨副、横梁与立柱导轨副、横梁与磨头溜板导轨副、磨头溜板与垂直拖板导轨副为主要导轨副,应采用耐磨铸铁、镶钢、淬火、贴塑与静压导轨等耐磨措施。 6.4下列结合面应按GB/T25373一2010中“重要固定结合面”的要求进行考核:
a)上顶梁、连接梁与立柱结合面; b)修整器底座与基体的结合面: c)磨头上传动箱体与基体的结合面: d)横梁升降丝杆螺母座与基体的结合面。
6.5下列结合面应按GB/T25373一2010中“特别重要固定结合面的要求进行考核
a)拼接床身、拼接工作台的结合面; b)立柱与床身的结合面: c)万能磨头回转体与磨头拖板的结合面(采用多齿盘结构时,应考核多齿盘与磨头壳体和拖板的
结合面); d)各种导轨的镶条、压板与基体固定的结合面: e)滚珠丝杠副支承与基体的结合面及螺母座与基体的结合面: f)镶钢导轨与基体的结合面。
6.6床身与工作台导轨副、横梁与磨头溜板导轨副、磨头溜板与垂直拖板导轨副应按GB/T25373一2010 中静压,滑(滚)动导轨”的要求进行考核 6.7横梁与立柱导轨副应按GB/T25373-2010中“移置导轨”的要求进行考核。 6.8带刻度装置的手轮、手柄反向空程量应不超过 1
10r.
6.9磨头电动机和装在磨头体上的油泵电动机应连同带轮或联轴器进行动平衡校正,其剩余不平衡量引起振动的双振幅值应不超过表3的规定。
表3
单位为微米
振动的双振幅值
电动机用途磨头电动机油泵电动机
4 8
6.10 按GB/T25374一2010的规定检验清洁度,其中周边磨头主轴油箱、主油泵油箱内部清洁度按重量法进行抽样检验。周边磨头主轴油箱内部杂质和污物的含量不应超过100mg/L,主油泵油箱内部杂质和污物的含量不应超过200mg/L。其他部位的清洁度按目测法或手感法进行检验,不应有明显的杂质和污物。
7 机床空运转试验
7.1静压导轨浮起量试验
采用静压导轨的机床,空运转前应将工作台置于床身中部并调整好浮起量,各油腔出油点的浮起量应均匀,其不均匀值应不超过表4的规定值。
3
JB/T10578.2—2014
表4
单位为毫米
工作台长度 ≤4000 >4 000
工作台浮起量的不均匀值
0.02 0.03
7.2温度和温升试验 7.2.1砂轮主轴应在无负荷状态下进行空运转试验(空运转时间不少于4h),当主轴轴承达到稳定温度后,在靠近磨头主轴轴承处(或油箱)的温度及温升应不超过表5的规定值。
表5 温度 55 65
单位为摄氏度
轴承形式滑动轴承滚动轴承
温升 25 35
7.2.2液压系统的温升试验,应符合GB/T23572一2009的规定。在额定工作压力下使系统运行至油液达到热平衡后,检验油液的温度和温升,其温度应不超过55℃,温升应不超过25℃。 7.3磨头的垂直与横向进给精度检验 7.3.1在检验前磨头应分别进行快速、慢速移动及连续、周期、微量进给运动试验,快速移动在全行程上往复应不少于1次,慢速移动时间应不少于1min,其动作应平稳可靠。 7.3.2磨头周期进给以最小和最大标称进给量分别检验,试验次数应不少于10次,其每次进给精度误差应不大于30% 7.3.3磨头进给以最小标称进给检验:每次进给相对误差应不大于100%,连续10次进给相对误差应不大于20%。 7.3.4磨头进给误差按公式(1)和公式(2)计算。
Jan - bl
8每次
×100%
(1)
b
式中:每次 每次进给相对误差;
an 每次实际进给量,单位为微米(um); b一最小标称进给量,单位为微米(um)。
10
Zam -10b S10次 10b
x100%
(2)
式中: S1o次 10次进给相对误差;
an 每次实际进给量,单位为微米(um);
一最小标称进给量,单位为微米(um)。
b
7.4工作台运行平稳性试验
工作台往复运动,应从低速短行程起依次达到高速全行程。若采用无级变速,则以5m/min速度递增。每级速度下的运行时间不得少于15min,在最高速度下的运行时间应至少1h,连续运行时间应不少于2h。运行过程中不应有冲击、爬行等现象。在规定的范围内,往返速差不得大于10%。 4
JB/T10578.2—2014
7.5横梁升降的试验
横梁升降试验时,磨头对称放置,使横梁负荷均匀,横梁在立柱全部行程上连续往复升降不得少于 1次,在运转中不应出现异常现象(如尖叫声)。 7.6磨头空运转试验
磨头主轴在运转时应平稳。如采用静压轴承,其动静刚度节流比、压力表值摆动按设计的要求进行考核。 7.7砂轮修整器空运转试验
砂轮修整器应作低速、中速、高速运行试验,每级速度下不得少于5次(全行程往复次数)。在运行过程中不应有冲击(两端碰缸位置除外)、爬行等现象。
8机床的负荷试验(抽查)
8.1磨头电动机达到额定(或设计规定)功率试验时,其试验规范如下:
a)磨削工件长度、截面形状和材料由设计规定: b)磨头主轴转速为中速、高速,即砂轮的线速度为20m/s~30m/s c)工作台速度为15m/min~20m/min; d)进给量均匀地增加到电动机达到额定或设计规定的功率;达到额定功率时,机床所有机构应工
作正常。
8.2做机床承载工件最大重量试验时,工作台应运行平稳,低速不得爬行。
9机床的精度检验
9.1机床精度检验按GB/T5288一2007的规定进行。 9.2砂轮修整器精度按表6的规定进行检验。
表6
单位为毫米
周边磨头修整器
万能磨头修整器
检验方法
检验项目
任意100长度上公差
按GB/T17421.1—1998中
修整器移动时的直线度修整器移动对磨头 垂直位置上为0.01(修整位 垂直位置上为0.015(修整位 按GB/T17421.1—1998中
0.004
0.008
5.4.1.2.5
主轴轴线的平行度 置):水平位置上为0.03 9.3万能磨头如采用多齿盘定位夹紧机构,应考核回转重复定位精度及回转平面在YZ平面内的平行度。检验时,可采用断续旋转定点法测量,要求测量点不少于5点,且每个点至少测3次(松开-回转夹紧按1次计)。其公差不超过下列规定:
置:水平位置上为0.03
5.2.3.2.1
a)回转重复定位精度:6*。 b)回转平面在Yz平面内的平行度(指示器距磨头回转轴线500mm处):
1)回转角度≤30:0.02mm 2)回转角度>30°:0.03mm。
注:测量点位置如用户无特殊要求,由制造商确定
9.4在GB/T5288一2007中几何精度检验G15项和工作精度检验M1M2项应在机床达到稳定温度后
5