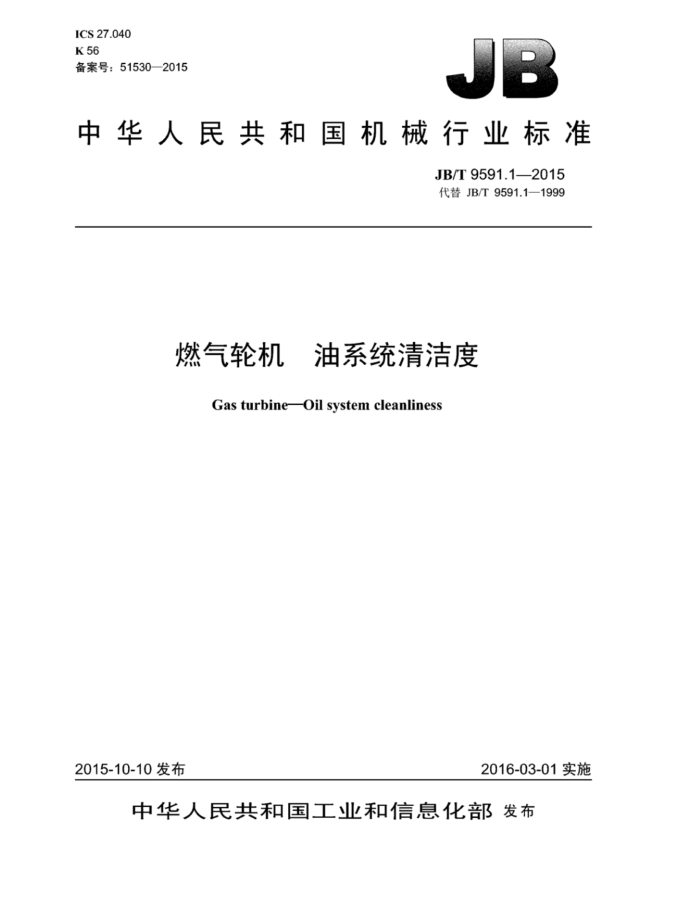
ICS27.040 K56 备案号:51530—2015
中华人民共和国机械行业标准
JB/T9591.12015 代替JB/T9591.1—1999
燃气轮机 油系统清洁度
Gas turbine-Oil system cleanliness
2015-10-10发布
2016-03-01实施
中华人民共和国工业和信息化部发布
JB/T9591.1—2015
目 次
前言 1 范围 2 规范性引用文件. 3 术语和定义 4制造期间的清洁度要求
一
4.1零部件的清洁度 4.2冲洗要求. 5运输和贮存期间的清洁度要求 5.1燃气轮机运输及正常贮存周期中保持清洁度的措施 5.2燃气轮机超过正常贮存期时保持清洁度的措施 6安装期间的清洁度要求, 6.1燃气轮机在安装期间的清理和冲洗 6.2清洁度要求.. 7维护性修理后和大修后的清洁度要求 7.1维护性修理后的清洁度要求. 7.2现场大修后油系统的冲洗附录A(规范性附录) NAS标准固体颗粒污染度分级附录B(资料性附录) ISO标准污染度分级 B.1ISO标准污染度等级代号 B.2ISO标准污染度等级组合代号. 附录C(资料性附录) MOOG标准污染度分级附录D(资料性附录)) ISO标准、NAS标准、MOOG标准污染度等级对照
6
6
10 11
表A.1 NAS标准固体颗粒污染度分级(按100mL油样计)表B.1 ISO标准污染度等级代号表B.2 ISO标准污染度等级组合代号表C.1 MOOG标准污染度分级. 表D.1 ISO标准、NAS标准、MOOG标准污染度等级对照.
8
O
10 *8:11
JB/T9591.1—2015
前言
JB/T9591《燃气轮机油系统清洁度》分为三个部分:
第1部分:燃气轮机油系统清洁度:一第2部分:燃气轮机油系统清洁度测试取样:
第3部分:燃气轮机油系统清洁度测试用显微镜计数法测定油液中固体颗粒污染度。 本部分为JB/T9591的第1部分。 本部分按照GBT1.1一2009给出的规则起草本部分代替JB/T9591.1—1999《燃气轮机油系统清洁度》,与JB/T9591.1—1999相比主要技术变
化如下:
更新了引用标准,修改了燃气轮机油系统的定义:补充了制造期间对管道及其附件的清洁及防护要求:一补充了系统及部件冲洗要求:一增加了燃油系统清洁度要求;一修订了运输贮存期间的防护要求:一增加了安装期间的清洁度要求:
附录中增加了MOOG标准污染度等级代号。 本部分由中国机械工业联合会提出。 本部分由全国燃气轮机标准化技术委员会归口本部分起草单位:南京燃气轮机研究所、南京汽轮电机(集团)有限责任公司、上海电气上海汽轮
机广,东方汽轮机有限公司神华浙江国华余姚燃气发电有限责任公司,杭州华电下沙热电有限公司哈尔滨汽轮机厂有限责任公司。
本部分主要起草人:张亚平、徐文文、崔耀欣、赵世全、韩建清、朱达、张宏涛。 本部分所代替标准的历次版本发布情况为:
ZBK56003—1989: JB/T9591.1—1999。
II
JB/T9591.1—2015
燃气轮机油系统清洁度
1范围
JB/T9591的本部分规定了在制造、安装、运输、贮存、维修和大修期间对燃气轮机油系统的清洁度要求,以及相应的清理和冲洗要求,冲洗用油的污染度要求。
本部分适用于燃气轮机动力装置。 本部分不适用于航空发动机自由活塞燃气轮机等装置
2规范性引用文件
下列文件对于本文件的应用是必不可少的。凡是注日期的引用文件,仅注日期的版本适用于本文件。 凡是不注日期的引用文件,其最新版本(包括所有的修改单)适用于本文件。
GB/T15135燃气轮机词汇 JB/T9591.2燃气轮机油系统清洁度测试取样 JB/T9591.3 燃气轮机油系统清洁度测试用显微镜计数法测定油液中固体颗粒污染度
3术语和定义
GB/T15135确定的以及下列术语和定义适用于本文件。
3.1
燃气轮机油系统 oil system of gas turbine 燃气轮机液压油系统、润滑油系统和燃料油系统的统称冲洗flushing 在油系统中,通过高速油循环减少系统中的污染物,以达到要求的系统清洁度的一种方法。
3.2
3.3
排油冲洗oilremovalflushing 在油系统中,通过油循环去除防锈油(剂)之类液体污染物的一种方法
3.4
绝对过滤精度absolutefiltrationprecision 在规定的试验条件下,能通过过滤装置的最大球形固体颗粒的直径。这是反映过滤元件过滤等级的
指标。
4制造期间的清洁度要求
4.1零部件的清洁度 4.1.1铸件 4.1.1.1油系统中所有铸件(包括轴承座及其他壳体)在机加工前,其非加工面应彻底清砂铸件的内腔室,通道,铸入管道等处应采用各种工艺方法彻底清理干净,清除掉氧化皮,附者物,粘砂夹砂
1
JB/T9591.1—2015
及其他一切污染物,并采取适当的防锈措施 4.1.1.2铸件的加工面在机加工后,应彻底清理干净。要特别注意内腔室、通道、铸入管道、沟槽、 小孔等处,清除掉铁屑、毛刺、锈斑、油污、灰尘及其他一切污染物,并涂覆适当的防锈油(剂)。然后采取措施将所有油通道的开口处密封,防止污染物进入。
4.1.2冷作焊接件 4.1.2.1冷作焊接件中使用的板材和型材,在制作和焊接之前应清理干净,清除掉氧化皮、锈斑及其他一切污染物,并采取适当的防锈措施。 4.1.2.2冷作件在制作和焊接后,应采取方法彻底清理干净,清除掉氧化皮,焊渣、飞溅,锈斑、油污、灰尘及其他一切污染物,并涂覆适当的防锈油(剂)。 4.1.2.3油箱内表面应采取防锈措施,如涂覆耐油、耐水和耐高温的永久型涂料、镀层或涂防锈油等。
采用涂覆永久型涂料措施时,所用涂料应与油箱内部油液相容,并适应环境,不允许涂料脱落造成污染。采用镀层、涂防锈油措施时,不得污染油箱内部油液。 4.1.2.4油箱可采用碳钢板或不锈钢板制作。推荐采用不锈钢板,以防止油箱锈蚀造成的污染 4.1.3管子、管道及附件 4.1.3.1油系统的所有管子和管道组装前都应按照要求存放和防护,以防止生锈和污染,并按照材料种类分开存放。除碳钢管外,其他材料的管子和管道都应按要求进行标记。任何管子或管道,若25% 的内表面的锈痕超过0.25mm深,将不可用于油管路。 4.1.3.2油系统中所有的管子(包括管组),在定位焊后、做第一道焊接之前,应从管子(包括管道附件)上去除所有油漆。在焊接时应采取工艺措施防止焊接造成的污染。宜采用氩弧焊,避免焊渣等污染 4.1.3.3在组装之前,所有管子(包括管道附件)应采用各种工艺方法彻底清理干净,清除掉管子内外表面的铁屑、毛刺、焊渣、飞溅、氧化皮、锈斑、油污、水分及其他一切污染物。 4.1.3.4在组装之后,所有管组应进行清洗,清除掉管子内外表面的铁屑、毛刺、焊渣、飞溅、氧化皮、锈斑、油污、水分及其他一切污染物。然后在专用的压力油冲洗机上,用清洁的热滑油冲洗管组。 管组冲洗干净后,碳钢管内表面应立即涂覆清洁的与工作油相容的防锈油,外表面涂覆适当底漆:其他材料的管子内外表面应采用适当的方法进行保护。 4.1.3.5管子(管组)内表面油封之后,其端部应进行密封,如采用金属盖、塑料盖或塞子等。在生产过程中,直到管子(管组)最终装配前,应确保这些临时性的盖子或塞子不脱落和损坏。管子(管组若不立即装在装置上,则应存放在特定的地方,以防止与其他没处理过的管子(管组)相混。 4.1.3.6所有管子(管组)总装前应清洗干净。
a)如果碳钢管子的存期已超过防锈油的有效期,建议在总装之前重新酸洗或采用其他适当的清
洗剂进行清洗,并涂覆防锈油: b)总装前,油系统中所有管子、管组及管道附件(包括外购件等)应用干燥清洁的压缩空气吹干
净
4.1.3.7总装时,管子(管组)的最终装配和焊接工作量应是最低限度的,管道焊接应尽量在冲洗前完成。在管道焊接和安装过程中产生的焊渣、飞溅、毛刺、铁屑及其他一切污染物,应彻底清除干净,碳钢管道应在管道外表面涂漆。 4.1.4机械加工零部件 4.1.4.1油系统中所有机械加工零部件在机加工后应彻底清理干净。要特别注意小孔、沟槽、内表面等处,清除掉铁屑、毛刺、锈斑、油污、灰尘及其他一切污染物,并涂覆适当的防锈油(剂)。然后采取措施将开口密封,防止污染物进入。
2
JB/T9591.1—2015
4.1.4.2机械加工零部件在装配前应清理干净。 4.2冲洗要求 4.2.1系统及部件的冲洗 4.2.1.1范围
油系统管道安装完成后,用专用的热油冲洗机对油箱、油系统管道、负荷齿轮箱、轴承座等油系统管道及主要部件分别进行热油冲洗。若油箱、管道等设备已经在设备制造厂或需在电厂采用其他方法处理干净,则该设备可以不进行热油冲洗。在整个系统安装完成后,采取分阶段的整体循环方式进行油循环冲洗。
在冲洗前,对于油系统中要求高清洁度的液压元件应采取旁路措施或卸下,以防止冲洗过程中污染物进入。但这些元件应单独清洗,或确认已是清洁的。 4.2.1.2对冲洗用热油的要求
对冲洗用热油的要求如下: a)冲洗用热油由专用的热油冲洗机供给,可循环使用。冲洗用油最好使用工作用油,也可使用与
其相容的其他油类。 b)冲洗用油在注入热油冲洗机之前,应经过滤机或滤油车严格过滤。然后按JB/T9591.2的规定取
油样,按本部分4.2.3.2的规定测定油样的污染度,其数值应达到本部分附录A中的5级~6级具体的污染度等级可根据机组的不同要求,由制造厂从中选定。污染度高于规定等级的冲洗用油,不得注入热油冲洗机。
c)在整个冲洗过程中,热油的温度应保持为70℃~80℃。各截面上的冲洗油流速至少为该截面上
额定流速的两倍。
4.2.1.3对冲洗装置过滤精度的要求
热油冲洗机应装有可切换的高精度双路过滤装置。建议采用二级过滤,绝对过滤精度分别为10um 和3um,以保证在热油循环使用过程中进入被冲洗系统或部件的油总是清洁的。 4.2.1.4冲洗方法
冲洗方法如下: a)轴承装配前,每个轴承座和连接的油通道应采用热压力油(表压力为1.4×10°Pa左右)灌洗,
去除其内部一切污染物。清洗后用白绢布或内窥镜伸入轴承油通道内检查。油通道内不允许有铁屑、砂粒或其他一切污染物。轴承座热油清洗结束后,要采取措施防止重新污染,并应尽快装配轴承。装配前轴承部分的表面应完全保护,并检查证明所有表面是干净的。
b)根据4.2.1.1的范围,将需要冲洗的油箱、部件和油系统管道分别与热油冲洗机接通,用符合
4.2.1.2要求的热油进行循环冲洗。在冲洗轴承时,进油管处应安装过滤精度为100um的滤网,以防止大颗粒污染物进入轴承。冲洗一段时间后,应检查滤网是否干净,若不干净,应更换新的滤网,并增加冲洗时间。
c)油箱、部件和油系统管道冲洗时间,应由设计或工艺人员视具体情况确定。但每一分系统或部
件至少应冲洗15h,且从油温达到70℃时开始计算冲洗时间。热油冲洗应连续进行。 d)在热油冲洗过程中,若热油冲洗机中过滤装置前后的压差达到了制造厂的规定值,则应切换过
滤装置,并更换滤芯。 e)在热油冲洗过程中,应在规定的位置(如弯头、法兰、管接头等处),采用机械或手动方法振动
3
JB/T9591.1—2015
管道,以加速管道内污染物的脱落和流动。管道振动的振幅应大于其额定运行时的预期值,但不得超过其机械极限。推荐采用固定式或手提式气动振动器。
4.2.1.5清洁度检测
当油箱、部件和油系统管道的冲洗达到规定时间后,均应按JB/T9591.2的规定取样,并按本部分 4.2.3.2测定油样的污染度,其数值应达到本部分附录A中的5级~7级。具体的污染度等级可根据机组的不同要求,由制造厂从中选定。若测定结果不合格,应继续进行热油冲洗,直至油样污染度符合要求。 4.2.2整机自身循环冲洗 4.2.2.1对冲洗用热油的要求:
a)冲洗用热油由油箱供给,可循环使用。在回油管路上装回油滤网,防止回油中的污染物进入油
箱循环。冲洗过程中,应经常检查滤网,以防止堵塞、溢流。冲洗用油最好用工作用油,也可用与其相容的其他油类。
b)冲洗用油在注入已冲洗合格的油箱之前,应经滤油机或滤油车严格过滤,然后按JB/T9591.2
的规定取样,按本部分4.2.3.2的规定测定油样的污染度。对于不设置独立液压油箱的机组,注入润滑油箱的油液污染度数值应达到本部分附录A中的5级~6级。对于设置独立液压油箱的机组,注入液压油箱的油液污染度数值应达到本部分附录A中的5级~6级:注入润滑油箱的油液污染度数值应达到本部分附录A中的7级~8级。燃油系统7~8级。具体的污染度等级可根据机组的不同要求,由制造厂从中选定,但冲洗用油的污染度等级不应高于系统工作用油的污染度等级。
c)在整个冲洗过程中,热油的温度应保持为60℃~70℃。若机组本身油系统的加热能力不足以获
得必需的温度,则应采用其他辅助的加热措施。
4.2.2.2对油系统中过滤装置的要求:
机组每个油系统均采用双路多级过滤。根据系统中部件及元件对清洁度的不同要求,确定各油系统中过滤装置的精度。建议各系统中最高一级过滤装置的绝对过滤精度分别为:润滑油系统,10um;液压油系统,3um:燃料油系统,10μm
为了进一步提高油系统的清洁度,建议对油箱采用高精度的旁通净化装置,其流量应占总流量的 10%~20%,绝对过滤精度为3um10um。在机组自身循环冲洗及正常运行过程中,旁通净化装置应投入工作,以使油箱中油的污染度保持在一定水平。 4.2.2.3冲洗方法:
整套油系统设备及管道安装完成后,应分阶段地油循环冲洗管道,保证管道的清洁度。 在部件及油系统管道热油冲洗合格后,对于不设置独立液压油箱的机组,将各部件及油系统管道与
润滑油系统接通,进行整机自身循环冲洗:燃料油系统管道与燃料油箱接通
对手设置独立液压油箱的机组,则液压油系统和润滑油系统应分别进行冲洗,防正液压油与润滑油
混合。
a)在冲洗前,对于油系统中要求高清洁度的液压元件及轴承应采取旁路措施或卸下,以防止冲洗
过程中污染物进入。同时还应将油系统中限制流量的元件卸下。 b)整机自身循环冲洗时间,应由设计或工艺人员视具体情况确定,但至少应为36h,冲洗应连续
进行。 c)在冲洗过程中,各油系统的过滤装置及油箱的旁通净化装置均应投入工作,若过滤装置前后的
压差达到了制造厂的规定值,则应切换过滤装置,并更换滤芯。 d)在冲洗过程中,应在规定位置,采用机械或手动方法振动管道,要求同4.2.1.4e)。
4
JB/T9591.1—2015
4.2.2.4清洁度检测:
当整机自身循环冲洗达到规定时间后:按JB/T9591.2的规定从油箱中取油样,并按本部分4.2.3.2
的规定测定油样的污染度。不设置独立液压油箱的机组,从润滑油箱所取油样的污染度数值应达到本部分附录A中的6级一8级。设置独立液压油箱的机组,从液压油箱所取油样的污染度数值应达到本部分附录A中的6级一8级:从润滑油箱所取油样的污染度数值应送到本部分附录A中的8级一10级。燃料油系统8级~10级。具体的污染度等级可根据机组的不同要求,由制造厂从中选定。若测定结果不合格,则应继续进行冲洗,直到油样污染符合要求。 4.2.2.5冲洗完成后,应将油箱及管道中冲洗用油排除,并将油箱彻底清理干净,不允许有任何肉眼可见的污染物存在。检查符合要求后,各油系统使用运行滤芯更换油冲洗滤芯,再重新注入清洁的工作用油,油的污染度要求同4.2.2.1b)。 4.2.2.6油箱注入清洁的工作用油后,将4.2.2.3中旁路或卸下的全部元件与系统管道接通,再次进行整机自身循环清洗,至少应连续12h。冲洗后,按4.2.2.4的规定,重复取样、测定、再冲洗等步骤,直至所取油样的污染度符合该条中的要求为止。 4.2.3油样污染度分级及测定 4.2.3.1污染度分级
本部分中所采用的油样污染度分级方法,是以每100mL油样内所含5个等级尺寸范围的最大极限固体颗粒数为评定指标的,具体分级见附录A。
也可采用附录B或附录C的污染度分级方法。 4.2.3.2污染度测定
油样污染度的测定应采用自动颗粒计数法或显微镜计数法。自动颗粒计数法应按照仪器制造厂说明书规定的标准方法执行:显微镜计数法应按照JB/T9591.3的规定。
5运输和贮存期间的清洁度要求
5.1燃气轮机运输及正常贮存周期中保持清洁度的措施 5.1.1碳钢材料制成的零部件表面应进行防锈保护。 5.1.2油系统所有容器、管道中的存水、存油等液体应全部放掉,并清洗干净,其内表面及其他零部件的浸油表面均应涂覆适当的防锈油:防锈油应易浴手工作用油并与其相容。 5.1.3所有不涂漆的外表面应用软的或硬的防锈薄膜(特殊成分的防锈油形成的透明薄膜)进行保护,选用的防锈薄膜应易于用手工方法或用溶剂去除,而且对工作用油的有害影响最小 5.1.4:油箱、轴承座等部件的内表面,应涂覆一种耐油、耐水和耐高温的永久型涂料。涂料应与内部油液相容,并适应环境。若不涂涂料,则应采取其他防锈措施。 5.1.5所有管道的开口处应进行密封,可采用金属盖、塑料盖或塞子等,盖子或塞子应涂防锈油:各部件应将各接口和接口法兰清洗干净,并用塑料或增强型防水布、气相防锈膜包扎,以防正污染物进入。 5.1.6如需在现场制作管道和施工,应按照4.1.3的要求,遵守在工厂装配期间同样的工艺。 5.1.7采用防锈包装运输的部件,若运输过程中包装未损坏,则在安装前不应将包装打开或拆除。 5.1.8对于贮存的机组,应采取防止气候影响的防护性措施。机组室内存时,室内温度应保持在 10℃~40℃,相对湿度保持在85%以下:机组室外贮存时,应对所有涂底漆的表面涂一层表面油漆。 5.1.9在贮存期间,应定期检查机组的防护性措施是否符合要求。如在贮存期间发现防锈包装损坏,应更换防锈包装。若机组贮存在高湿度和高盐分的环境中,应每三个月打开罩壳检查内部涂漆表面是否
5