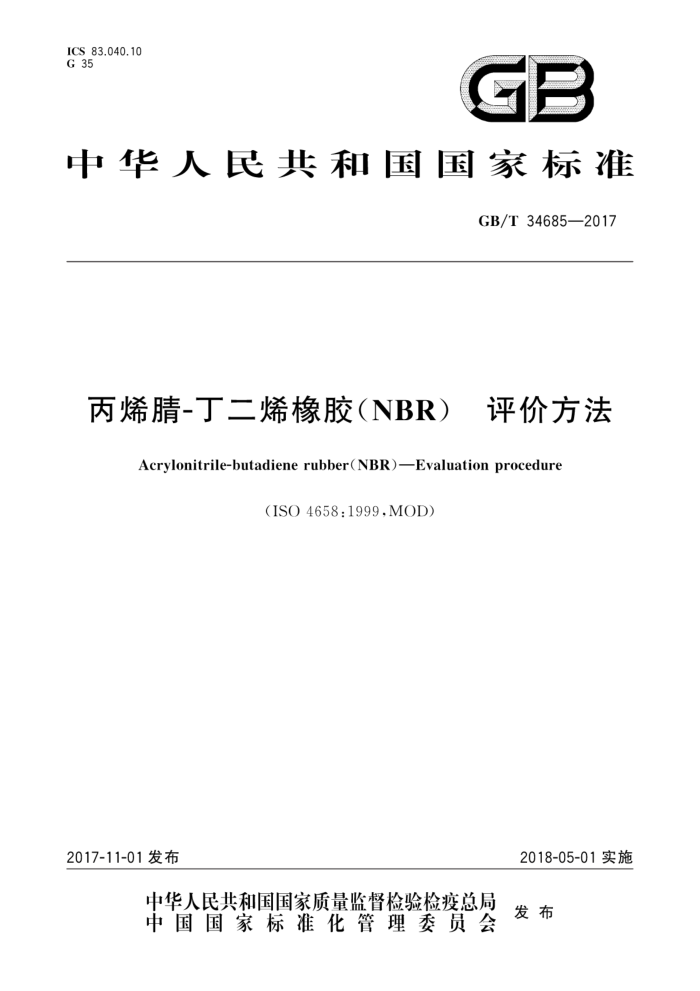
ICS 83.040.10 G 35
GB
中华人民共和国国家标准
GB/T346852017
丙烯腈-丁二烯橡胶(NBR) 评价方法
Acrylonitrile-butadiene rubber(NBR)—Evaluation procedure
(ISO4658:1999,MOD)
2018-05-01实施
2017-11-01发布
中华人民共和国国家质量监督检验检疫总局
中国国家标准化管理委员会 发布
GB/T34685—2017
目 次
前言
范围 2 规范性引用文件 3 取样和制样
生胶的物理和化学试验 4.1 门尼黏度 4.2 挥发分 4.3 灰分
5评价用混炼胶试样的制备 5.1 标准试验配方
5.2 程序 5.2.1 通则 5.2.2 开炼机混炼程序
5.2.2.1 概述· 5.2.2.2 程序1 5.2.2.3 程序2 5.2.3 小型密炼机混炼程序 5.2.4 密炼机初混炼开炼机终混炼程序 5.2.4.1 概述 5.2.4.2 密炼机初混炼程序 5.2.4.3 胶料的调节 5.2.4.4 开炼机终混炼程序 5.2.4.5 胶料的调节
6 硫化特性评价 6.1用圆盘振荡硫化仪 6.2用无转子硫化仪
硫化胶拉伸应力-应变性能评价
7
精密度
8
9试验报告附录A(资料性附录) 规范性引用文件调整情况附录B(资料性附录) 精密度参考文献
11
GB/T 34685—2017
前言
本标准按照GB/T1.1一2009给出的规则起草。 本标准使用重新起草法修改采用ISO4658:1999《丙烯腈-丁二烯橡胶(NBR) 评价方法》。 本标准与ISO4658:1999相比,主要技术性差异如下:
关于规范性引用文件,本标准做了具有技术性差异的调整,以适应我国的技术条件,调整的情况集中反映在第2章“规范性引用文件”中,具体调整情况参见附录A;修改了试验配方中配合剂的技术要求(见5.1);修改了开炼机混炼程序1(见5.2.2.2);增加了累积时间(见5.2.2.2,5.2.2.3.2,5.2.2.3.3,5.2.3.3,5.2.4.2,5.2.4.4);增加小型密炼机混炼后硫化胶片的温度和时间(见5.2.3.4);
一
修改"精密度”(ISO4658:1999的第8章)为资料性附录B。 本标准做了下列编辑性修改:
纳入了ISO4658:1999/Amd.1:2004技术内容(见5.2.4);删除了ISO4658:1999/Amd.1:2004概述中重复的内容(见ISO4658:1999/Amd.1:2004中 5.2.4.1,本版的5.2.4.1);增加了资料性附录A,给出规范性引用文件调整情况。
本标准由中国石油化工集团公司提出本标准由全国橡胶与橡胶制品标准化技术委员会合成橡胶分技术委员会(SAC/TC35/SC6)
归口。
本标准起草单位:中国石油天然气股份有限公司石油化工研究院、宁波顺泽橡胶有限公司、中国石油天然气股份有限公司兰州石化分公司。
本标准主要起草人:翟月勤、吴毅、赵慧晖、陈跟平、张兆庆、欧俊军、杨玉琼、黄世英、何连成、李波
I
GB/T34685—2017
丙烯睛-丁二烯橡胶(NBR)评价方法
警示一一使用本标准的人员应有正规实验室工作的实践经验。本标准并未指出所有可能的安全问
题。 使用者有责任采取适当的安全和健康措施,并保证符合国家有关法规规定的条件
1范围
本标准规定了丙烯腈-丁二烯橡胶(NBR):
生胶的物理和化学试验方法;一评价内烯睛-丁二烯橡胶(NBR)硫化特性所用的标准材料、标准试验配方、设备、操作程序以及
评价硫化橡胶拉伸应力-应变性能的方法。 本标准适用于丙烯睛-丁二烯橡胶(NBR)。
2规范性引用文件
下列文件对于本文件的应用是必不可少的。凡是注日期的引用文件,仅注日期的版本适用于本文件。凡是不注日期的引用文件,其最新版本(包括所有的修改单)适用于本文件
GB/T528硫化橡胶或热塑性橡胶拉伸应力应变性能的测定(GB/T528一2009,ISO37:2005, IDT)
GB/T1232.1未硫化橡胶 用圆盘剪切黏度计进行测定第1部分:门尼黏度的测定 (GB/T1232.1—2016,ISO289-1:2014,IDT)
GB/T2449.1一2014工业硫磺第1部分:固体产品 GB/T2941 橡胶物理试验方法试样制备和调节通用程序(GB/T2941一2006,ISO23529:2004,
IDT)
GB/T3185—2016氧化锌(间接法) GB/T 4498.1 橡胶灰分的测定第1部分:马弗炉法(GB/T4498.1一2013,ISO247:2006,
MOD)
GB/T6038—2006 橡胶试验胶料 配料、混炼和硫化设备及操作程序(ISO2393:1994,MOD) GB/T9103—2013 工业硬脂酸 GB/T 9869 橡胶胶料 硫化特性的测定圆盘振荡硫化仪法(GB/T9869一2014,ISO3417:
2008,IDT)
GB/T 15340 天然、合成生胶取样及其制样方法(GB/T15340一2008,ISO1795:2000,IDT) GB/T 16584 橡胶用无转子硫化仪测定硫化特性(GB/T16584一1996,ISO6502:1991,MOD) GB/T 19187 合成生橡胶抽样检查程序 GB/T 21184 橡胶配合剂次磺酰胺促进剂 试验方法(GB/T21184—2007,ISO11235:1999,
NEQ)
ISO248-1:2011生橡胶挥发分含量的测定第1部分:热辊法和烘箱法(Rubber,raw一De termination of volatilematter content—Part1:Hot-mill method and ovenmethod)
3取样和制样
3.1# 按GB/T19187取样约1.5kg。
1
GB/T34685—2017
3.2 按GB/T15340制备试样。
4 生胶的物理和化学试验
4.1 门尼黏度
按GB/T1232.1测定门尼黏度,制备试样见3.2。测定结果以ML(1十4)100℃表示。 4.2 挥发分
建议按ISO248-1:2011热辊法测定挥发分含量。如果按热辊法测定橡胶粘辊,可以使用烘箱法在温度105℃±5℃测定。 4.3 灰分
按GB/T4498.1测定灰分含量。
5 评价用混炼胶试样的制备
5.1 标准试验配方
标准试验配方见表1。 应使用符合国家或国际标准的标准样品。如果没有标准样品,应使用有关团体认可的材料。
表1 标准试验配方
材料
质量份 100.00 3.00 1.50 1.00 40.00 0.70 146.20
丙烯腈-丁二烯橡胶(NBR)氧化锌" 硫磺硬脂酸“ 炭黑 TBBS 合计
·GB/T3185—2016中I型。 bGB/T2449.1—2014中优等品,其中水分含量应小于0.5%。 GB/T9103—2013中1840型,—等品应使用当前我国的或国际的炭黑标准样品。 炭黑应在125℃土3℃下干燥1h,并于密闭容器中贮存, N-叔丁基-2-苯并噻唑次磺酰胺,粉末形态。按GB/T21184测定,其最初甲醇不溶物含量应小于0.3%。该材料应在室温下贮存于密闭容器中,每6个月检查一次不溶物含量,若超过0.75%,则废弃或重结晶
5.2程序 5.2.1 通则
试验胶料的配料、混炼和硫化设备及操作程序按GB/T6038一2006进行,可以用开炼机、小型密炼机或密炼机初混炼开炼机终混炼程序制备混炼胶,但结果可能稍有不同。
2
GB/T34685—2017
5.2.2开炼机混炼程序 5.2.2.1概述
标准实验室开炼机每批胶量应为配方量的四倍,以g计混炼时,在两辊筒间隙的上方应保持适量的堆积胶,否则应对辊距稍作调整。 下述两种开炼机混炼程序可任选一种。
5.2.2.2程序1
本操作程序推荐使用2%MgCO;涂层硫磺,混炼过程中辊筒表面温度应保持在50℃土5℃。对于热法聚合NBR,按步骤a)塑炼4min,累积时间依次增加2min。
持续时间 累积时间 min
min 2.0 5.0 7.0 12.0 14.0 19.0 20.0 22.0 24.0 25.0
a) 调节开炼机辊距为1.4mm,使橡胶包在慢辊上 b) 将硬脂酸和氧化锌一起添加,然后再添加硫磺 c) 每边作3/4割刀3次 d) 在辊筒上方以恒定速度沿着橡胶均匀地加入一半炭黑 e) 调节辊距为1.65mm,每边作3/4割刀3次: f) 以恒定速度沿着辊筒上橡胶均匀地加入剩余的炭黑 g) 加入促进剂TBBS h) 当所有TBBS加人后,每边作3/4割刀3次 i) 调节辊距为0.8mm,将混炼胶打卷纵向薄通6次 ji) 调节辊距,将胶料对折过辊4次,制成约6mm厚的胶片 k) 下片,检查胶料的质量(见GB/T6038一2006),如果胶料质量与理论值之差超过十0.5%或
2.0 3.0 2.0 5.0 2.0 5.0 1.0 2.0 2.0 1.0
一1.5%,则弃去胶料,重新混炼。取足够的胶料供硫化仪试验用。 1) 按照GB/T528规定,将混炼胶制成约2.2mm厚的胶片用于制备试片,或制成适当厚度胶片
用于制备环形试片。 m) 混炼后和硫化前,将胶料调节2h~24h。如有可能,在GB/T2941规定的标准实验室温度和
湿度下调节。
5.2.2.3 程序2 5.2.2.3.1总则
本程序使用无涂层硫磺,为了获得好的分散性,硫磺与橡胶先进行预混炼。 5.2.2.3.2 硫磺预混胶的制备
本程序中,辊筒表面温度应保持在80℃土5℃。对于热法聚合NBR,按步骤a)塑炼4min,累积时间依次增加2min。
3
GB/T34685—2017
持续时间 累积时间 min
min 2.0 5.0 7.0
2.0 3.0 2.0
调节开炼机辊距为1.4mm,使橡胶包辑 b) 沿着橡胶缓慢、均匀地加入硫磺
a)
每边作3/4割刀3次,
C
(最多9.0)
d) 下片,如有可能,按GB/T2941规定的标准温度和湿度下调节0.5h~2.0h。 5.2.2.3.3 混炼程序
混炼过程中,辊筒表面温度应保持在50℃土5℃。
持续时间 累积时间
min 2.0 2.0
min 2.0 4.0
a) 调节开炼机辑距为1.4mm,使硫磺预混炼橡胶包辑 b) 加人氧化锌和硬脂酸
继续5.2.2.2的c)~m)程序。
5.2.3小型密炼机混炼程序 5.2.3.1混炼时,小型密炼机的密炼室温度应保持在63℃土3℃,转子转速为60r/min~63r/min。 5.2.3.2调节开炼机温度为50℃土5℃,制成约5mm厚的胶片,胶料过辊1次,将胶片切成宽约 25mm的胶条。 5.2.3.3 混炼周期:
持续时间 累积时间 min
min 0.0 1.0
a) 将胶条装入混炼室内,放下上顶栓开始计时 b) 塑炼橡胶 c) 升起上顶栓,谨慎加人预先混合好的氧化锌、硫磺、硬脂酸和
0.0 1.0
1.0 7.0
2.0 9.0
TBBS,避免任何损失。加人炭黑,清扫进料口并放下上顶栓 d) 混炼胶料,如果有必要,快速升起上顶栓扫入物料 e) 关掉电机,升起上顶栓,打开混炼室,卸下胶料。 f) 将混炼的胶料立即通过辊距为0.8mm,辊温为50℃土5℃的开炼机。 g) 将混炼胶打卷,纵向薄通六次。 h) 将混炼胶制成约6mm厚的胶片。检查胶料的质量(见GB/T6038一2006)。如果胶料质量与
理论值之差超过十0.5%或一1.5%,则弃去胶料,重新混炼。取足够的胶料供硫化试验用。 i) 按照GB/T528规定,将混炼胶制成约2.2mm厚的胶片,用于制备硫化试片,或制成适当厚
度,用于制备环形试片。 j) 混炼后和硫化前.将胶料调节2h~24h,如有可能,在GB/T2941规定的标准实验室温度或
湿度下调节。
5.2.3.4 如果测试硫化橡胶的拉伸应力-应变性能,推荐胶片在温度150℃硫化,硫化时间为40min。
4