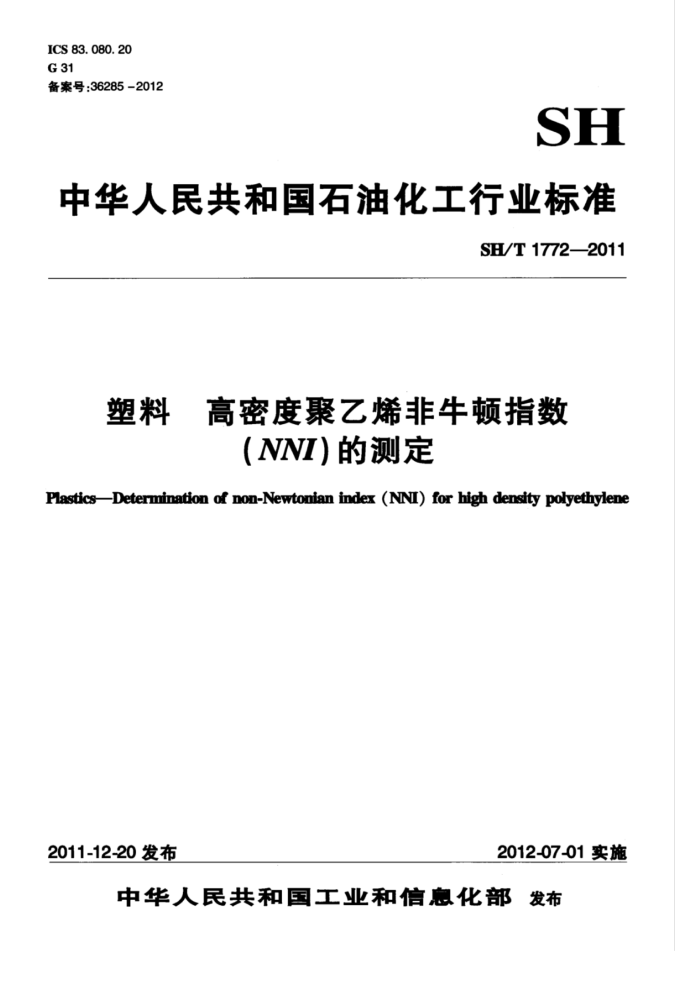
ICS 83. 080.20 G 31 备案号:36285-2012
SH
中华人民共和国石油化工行业标准
SH/T 1772—2011
塑料 高密度聚乙烯非牛顿指数
(NNI)的测定
PlasticsDetermination of non-Newtonian index (NNI) for high density polyethylene
2012-07-01实施
2011-12-20 发布
中华人民共和国工业和信息化部 发布
SH/T1772—2011
前 言
本标准按照GB/T1.1—2009给出的规则起草。 本标准由中国石油化工集团公司提出。 本标准由全国塑料标准化技术委员会石化塑料树脂产品分技术委员会(SAC/TC15/SC1)归口。 本标准负责起草单位:中国石油化工股份有限公司北京燕山分公司树脂应用研究所。 本标准参加起草单位:中国石化扬子石油化工有限公司、中国石油化工股份有限公司北京燕山分
公司质量监督检验中心。
本标准主要起草人:郑慧琴、曾伟丽、吴世斌、杨黎黎、田江南。
-
SH/T1772-2011
塑料高密度聚乙烯非牛顿指数(NNI)的测定
1范围
1.1本标准规定了测定高密度聚乙烯非牛顿指数(NNI)的方法。 1.2本标准适用于颗粒状高密度聚乙烯。
注:熔体质量流动速率大于1.0g/10min(190℃,2.16kg)的粉状高密度聚乙烯可参照本标准。
2规范性引用文件
下列文件对于本文件的应用是必不可少的。凡是注日期的引用文件,仅所注日期的版本适用于本文件。凡是不注日期的引用文件,其最新版本(包括所有的修改单)适用于本文件。
GB/T3505一2009产品几何技术规范(CPS)表面结构轮廊法术语、定义及结构参数 GB/T4340.1--2009金属维氏硬度试验第1部分:试验方法 GB/T25278—2010塑料用毛细管和狭缝口模流变仪测定塑料的流动性
3术语和定义
GB/T25278一2010界定的以及下列术语和定义适用于本文件。
3. 1
非牛顿指数non-Newtonianindex NNI,在高密度聚乙烯的表观剪切应力(T)与表观剪切速率(。)之间关系的流动曲线上,规
定的两个表观剪切应力与所对应的表观剪切速率之比。通常情况下,Tl为4×10*Pa,T为24× 10*Pao
4原理
用挤出式毛细管流变仪在规定温度下测得表示剪切应力和剪切速率之间关系的样品流动曲线,从
该曲线中得到两个规定的表观剪切应力T和T对应的表观剪切速率和服,该剪切速率之比(m/)即为样品的非牛顿指数(NNI)。
5仪器
5.1试验仪器 5.1.1概述
试验仪器应由加热料筒组成,其内膛底部用可互换的毛细管口模封住。试验压力应通过柱塞、螺杆或使用气压施加到料筒内的熔体上。图1为典型示例,允许有其他尺寸。
1
SH/T 17722011
$ 12:0.01
00
x 12
A D
10
9-光学传感器; 10一控温室; 11—温度计; 12一人角,
1--施加力或恒速; 2一绝热层; 3一柱塞; 4一料筒:
5一加热圈; 6一压力传感器; 7—毛细管门模: 8-口模锁紧螺母;
图1毛细管口模挤出流变仪的典型示例
5.1.2料筒
料筒应由能够在加热系统的最高温度下抗磨损和抗腐蚀的材料制成,料筒内靠近口模人处可有侧孔,以插入熔体压力传感器。料筒整个长度上平均内膛直径的允许偏差应少于±0.007mm:所用材料的维氏硬度至少为800HV30(见GB/T4340.1-2009和注1)、并IⅡ表面粗糙度R,小于0.25μm(算术平均偏差,见GB/T3505—2009)。
注1:氮化钢材料适于高达400℃的温度。硬度值虽然低于规定值、但足以抗腐蚀和磨损的材料,同样可用于制作
料筒和[I模组件。
注2:料筒内膛直径的增大,增加了单个料筒试验能够测量的次数以及增大仪器的剪切速率范围。但较大内腔直
径的料简需用的样品量大,且样品达到温度平衡所需的时间长,商业化流变仪的料简内腔直径范围为 6.35mm ~25mm。
2
SH/T1772—2011
5.1.3毛细管口模
毛细管口模壁的整个长度上直径(D)的机加T精度应为±0.007mm,长度(L)的机加工精度应为±0.025mm(见图1)。
毛细管口模应使用维氏硬度至少为800HV30的材料进行加T(见GB/T4340.1一2009和5.1.2中的注1),并且表面粗糙度R,小于0.25μm(算术平均偏差,见CB/T3505一2009)。
毛细管孔不应有明显的机械加工痕迹和偏心。 注:最常用的口模材料为硬化钢、碳化钨、钨铬钴合金和硬化不锈钢。 用毛细管口模测定表观剪切速率和表观剪切应力T,其长径比L/D至少应为16,人口角为
180°,除非相关标准另有规定。使用入口角(±1°)、长度(±0.025mm)和直径(±0.007mm)均相同的毛细管获得的数据才有可比性。人口角的定义见图1。 5.1.4柱塞
如果使用柱塞,其直径应比料简内膛直径小0.040mm±0.005mm。为减少熔体在柱塞上的回流,可安装断开的或完整的密封圈。柱塞的硬度应比料筒的低,但不应低于375HV30。 5.2试验温度的控制
对于任何设定的料筒温度,在整个试验过程中,从毛细管口模到可允许加料高度整个范围内的温度都应得到有效控制,在筒壁所测温度的差异和变化不得超过表1规定的范围。
表1 随距离和时间变化的最大允许温差
随时间的温差"
试验温度6
随距离的温
℃ ≤200
° ± 1. 0 ± 1. 5 ± 2. 0
℃ ± 0. 5 ± 1. 0 ± 1.5
200≤300
>300
"在整个试验过程中,从毛细管口模到可允许加料高度整个范围内的所有位置。 试验仪器应设计能以1℃或更小的间隔设置试验温度。
5.3试验温度的测量和校准 5.3.1试验温度的测量
试验温度应是料简中毛细管入口附近熔体的温度,若不可能,则用毛细管人口附近料筒壁的温度最好在口模入口上方不大于10mm的位置进行测定(见5.3.2)。
温度测量装置的顶端应与熔体接触,若不可能,则与料筒的金属部分或距离熔体流道小于1.5mm 的毛细管壁接触。温度计中可使用热传导流体来更好地提高传导,温度计最好是热电偶或者铂电阻传感器,可按图1进行安装。 5.3.2试验温度的校准
试验中使用的温度测量装置应读至0.1℃内,并通过误差限度为±0.1℃的标准温度计进行校准。 校准时该温度计应遵照规定浸入一定的深度,为此,料筒可用低黏度熔体填满。
校准时应使用不污染口模、料筒或影响随后测量的流体做导热介质,如硅油。
3
SH/T1772—2011
5.4试验压力的测量及校准
5.4.1试验压力的测量
试验压力应是熔体上的压力降,试验中测量的是熔体进入毛细管口模前的压力和出口压力之差。 如有可能,试验压力应使用安放在毛细管口模人口附近的熔体压力传感器测量,在所有试验的情况下,压力传感器到口模入口面之间的距离应保持不变,且最好不大于20mm(见注)。否则,试验压力应通过施加在熔体上的力来测量,如通过柱塞,其力通过柱塞上方的力值传感器测得。
注:对于所有试验,口模人口面到压力传感器的距离保持恒定是很重要的,否则将影响压力降的测量。 力或压力测量装置应在其公称能力的1%~95%范围内使用。
5.4.2试验压力的校准
熔体压力传感器可用外部液压式试验仪进行校准,力值传感器应按照仪器厂家的使用说明书进行校准。压力传感器或负荷单元的读数最大允差均应小于或等于满量程的1%和小于或等于绝对值的5%,熔体压力传感器的校准最好在规定的试验温度下进行。 5.5体积流动速率的测定
体积流动速率应由柱塞的喂料速率确定,体积流动速率的测量误差应不超过1%。 为提供可比较数据,推荐在对数坐标上按平均分布设定表观剪切速率或流动速率,每个数量级上
应至少取三点。
注:只有满足了设想条件,其中之一就是柱塞和料简间泄漏量足够少的要求,才能符合由柱塞喂料速率确定体积流
动速率而规定的最大允许误差。经验表明,若料简与柱塞间的间隙不超过0.045mm,则能够达到目的(见 5. 1. 4)。
6取样
从试验材料中选择有代表性的样品作为试样。
7试验条件
推荐测定高密度聚乙烯非牛顿指数(NNI)的试验条件见表2。
表2测定高密度聚乙烯非牛顿指数(NNI)的试验条件
单筒毛细管流变仪毛细管口模尺寸
双筒毛细管流变仪毛细管口模尺寸
熔体质量流动速率 (190℃/2.16kg)
条件(字母代号)
试验温度
°℃
人口角 直径 (°)
人口角 (°) 180
直径 mm /
g/10min
长径比 30
长径比 30 16 0. 25 180 ≥16
mm 1 1 2
MFR>0.1 MFR>0.1 MFR≤0.1
190 190 250
A B c 注:对于配备英制尺寸毛细管口模的仪器,可使用与表中规定尺寸较接近的口模。
180
≥16 180
180
2
4