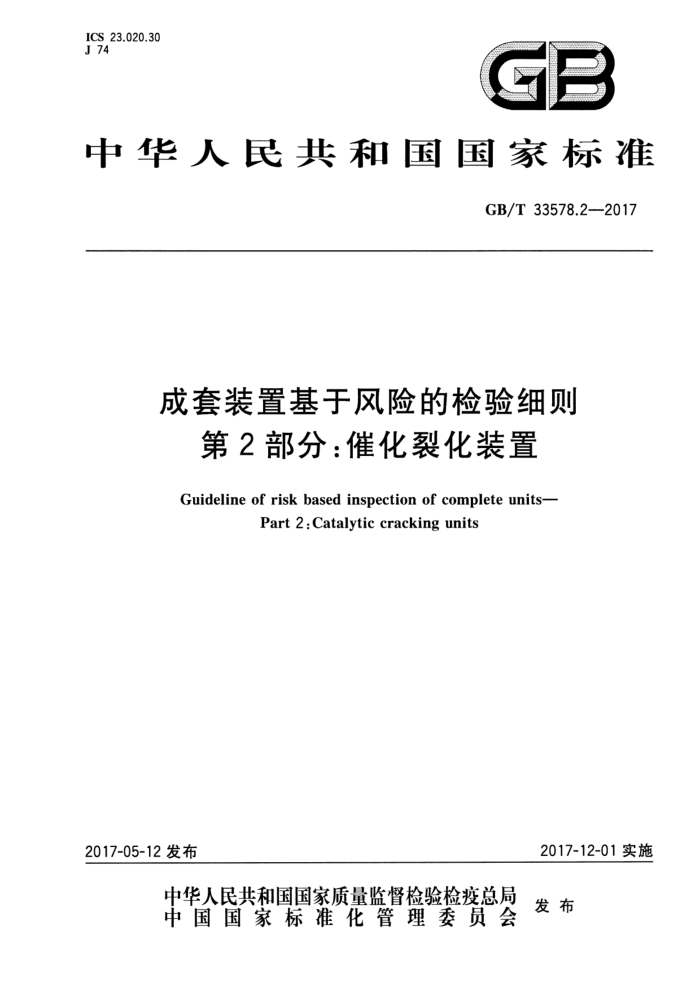
ICS 23.020.30 J 74
C 三
中华人民共和国国家标准
GB/T33578.2—2017
成套装置基于风险的检验细则
第2部分:催化裂化装置
Guideline of risk based inspection of complete units-
Part 2:Catalytic cracking units
2017-12-01实施
2017-05-12发布
中华人民共和国国家质量监督检验检疫总局中国国家标准化管理委员会
发布
GB/T 33578.2—2017
目 次
前言
范围 2 规范性引用文件 3 术语和定义 4 总则 5 通用流程
1
装置损伤模式分布基于风险的检验细则
6
2
附录A(资料性附录)催化裂化装置工艺简介附录B(资料性附录) 催化裂化装置损伤模式流程分布
19
22
....
GB/T33578.2—2017
前言
GB/T33578《成套装置基于风险的检验细则》分为两个部分:
第1部分:乙烯装置;第2部分:催化裂化装置。
-
本部分为GB/T33578的第2部分。 本部分按照GB/T1.1一2009给出的规则起草。 本部分由全国锅炉压力容器标准化技术委员会(SAC/TC262)提出并归口。 本部分起草单位:中国特种设备检测研究院、国家质量监督检验检疫总局特种设备安全监察局、合
肥通用机械研究院、中国石油化工股份有限公司、中国石油天然气股份有限公司、中国石油关然气股份有限公司克拉玛依石化分公司、中国石油天然气股份有限公司独山子石化分公司、中国石油化工股份有限公司北京燕山分公司、中国石油化工股份有限公司上海高桥分公司、中国石油化工股份有限公司天津石油分公司、中国石油化工股份有限公司洛阳分公司、中国石化工程建设有限公司、中国石油天然气股份有限公司哈尔滨石化分公司、中国石油化工股份有限公司齐鲁分公司。
本部分主要起草人:谢国山、李军、吕运容、李伟、王笑梅、王建军、宋晓江、邵珊珊、陈炜、穆澎淘、 王庆荣、胡明东、李志峰、高肇、顾雪东、魏冬、叶国庆、于力、钱晓龙、王远慧、杜博华。
-
GB/T 33578.2—2017
成套装置基于风险的检验细则
第2部分:催化裂化装置
1范围
GB/T33578的本部分给出了催化裂化装置基于风险的检验(RBI)实施细则。 本部分适用于流化催化裂化装置实施了RBI项目的承压设备,其他类型的催化裂化装置(如固定
床、移动床催化裂化装置)可参考使用。
本部分不适用于安全阀,安全阀校验策略见GB/T26610.2。
2规范性引用文件
下列文件对于本文件的应用是必不可少的。凡是注日期的引用文件,仅注日期的版本适用于本文件。凡是不注日期的引用文件,其最新版本(包括所有的修改单)适用于本文件。
GB/T26610.1 承压设备系统基于风险的检验实施导则第1部分:基本要求和实施程序 GB/T26610.2 承压设备系统基于风险的检验实施导则第2部分:基于风险的检验策略 GB/T26610.3 承压设备系统基于风险的检验实施导则 第3部分:风险的定性分析方法 GB/T26610.4 承压设备系统基于风险的检验实施导则第4部分:失效可能性定量分析方法 GB/T26610.5承压设备系统基于风险的检验实施导则第5部分:失效后果定量分析方法 GB/T30579 9承压设备损伤模式识别 SH/T3096 高硫原油加工装置设备和管道设计选材导则
3术语和定义
GB/T26610.1~26610.5和GB/T30579界定的术语和定义适用于本文件。
4总则
4.1本部分是在GB/T26610.1~26610.5和GB/T30579的基础上,针对炼油工业典型装置——催化裂化装置的工艺、设备特点制定的检验细则。本部分并不替代风险评估工作,而是GB/T26610.2针对具体装置的应用。 4.2本部分在按催化裂化装置工艺流程确定承压设备潜在损伤模式的基础上,给出了典型设备及其他特殊部位针对性的检验方法,其余设备基于损伤模式的检验方法按GB/T26610.2确定。 4.3本部分所述催化裂化装置损伤模式,根据其常用材料、典型工艺条件确定,是可能发生的潜在损伤。实际催化裂化装置的具体损伤模式应根据实际情况进行调整。为了让使用者能够区分主次,本部分基于损伤模式分析和实际使用经验,按损伤模式发生的严重程度和频次,将损伤模式定性划分为主要损伤模式和次要损伤模式, 4.4本部分设备常用材料依据国内催化裂化装置设备材料实际使用经验和SH/T3096确定。 4.5本部分中承压设备潜在的损伤模式是在正常工况下给出的,非正常工况或其他特殊工况下(如超负荷、低负荷、原料成分变化、超设计)的损伤模式及基于风险的检验细则按实际情况确定。
1
GB/T33578.2—2017
4.6检验过程中发现的损伤模式,检验人员应根据范围和损伤程度决定是否需要扩检。检验过程中发现的缺陷,按相关标准规范进行处理。 4.7大气腐蚀(包括无隔热层和有隔热层)为碳钢与低合金钢材料设备普遍存在的损伤模式,检验方法以外部目视检测为主,在本部分第6、7章中不再赞述 4.8使用本部分时,可以直接由第7章找出对应的设备,对于第7章没有提到的设备,可以根据设备所处流程位置,在第6章中找出其损伤模式及部位,然后按照GB/T26610.2或GB/T30579选择基于损伤模式的检验方法。 4.9检验细则并不等同于检验方案,实际检验方案要根据具体情况制定。基于损伤模式的检验内容按本部分确定,以本部分规定的主要损伤模式为主,兼顾次要损伤模式。对于本部分没有覆盖的检验内容,如基础、支撑结构、接地、接管及补强、涂层和隔热层、表面状况、法兰接头、阀门等,参照《压力容器定期检验规则》和《在用工业管道定期检验规程》确定。
5通用流程
5.1损伤模式确定
按本部分及GB/T30579确定损伤模式。 5.2风险分析计算
根据5.1确定的损伤模式,按GB/T26610.4和GB/T26610.5对催化裂化装置承压设备进行定量分析计算,确定其失效可能性和失效后果等级。按GB/T26610.1确定承压设备的风险。风险的定性分析可用于定量分析前设备的筛选分析,按GB/T26610.3进行。 5.3制定检验细则
根据5.2风险分析计算结果按GB/T26610.2确定催化裂化装置设备的检验时间(或基于检验时间确定的检验范围)、检验类型,结合GB/T26610.2和本部分的要求制定催化裂化装置设备的检验方法和检验部位。
6装置损伤模式分布
6.1反应-再生工段 6.1.1原料油进料单元:
a)原料油混合器、原料油缓冲罐、原料油轻柴油热交换器(原料油侧)及相连管道:冲蚀、湿硫化氢
破坏; b)原料油一中段油热交换器(原料油侧)、原料油循环油浆热交换器(原料油侧)、原料油回炼油混
合器及相连管道至提升管入口:高温硫化物腐蚀(无氢气环境)、环烷酸腐蚀、冲蚀; c) 回炼油进料管道、回炼油罐及出口管道:高温硫化物腐蚀(无氢气环境)、环烷酸腐蚀、冲蚀; d) 回炼油泵出口管道:高温硫化物腐蚀(无氢气环境)、环烷酸腐蚀、冲蚀; e) 蒸汽管道、凝结水罐及相连管道、蒸汽扩容器及相连管道:冲蚀、锅炉冷凝水腐蚀。
6.1.2反应沉降单元:
蒸汽管道至提升管反应器入口:冲蚀、锅炉冷凝水腐蚀;
a)
b) 提升管反应器(催化剂700℃~750℃):耐火材料退化、高温硫化物腐蚀(无氢气环境)、石墨
化、冲蚀、蠕变;
2
GB/T33578.2—2017
c)沉降器沉降段、汽提段:耐火材料退化、高温氧化腐蚀、高温硫化物腐蚀(无氢气环境)、冲蚀、过
热、石墨化、渗碳、再热裂纹;
d) 沉降器顶部油气管道:耐火材料退化、冲蚀、高温硫化物腐蚀(无氢气环境)、热疲劳、蠕变、回火
脆化、石墨化;
e) 油气管道膨胀节:连多硫酸应力腐蚀开裂、氯化物应力腐蚀开裂、螨变、冲刷、热疲劳。 6.1.3催化剂再生单元:
a)再生器稀相段、密相段:耐火材料退化、冲蚀、过热、高温氧化腐蚀、烟气露点腐蚀、硝酸盐应力
腐蚀开裂、渗碳、石墨化:
b) 再生烟气管道至三级旋风分离器:耐火材料退化、冲蚀、过热、高温氧化腐蚀、烟气露点腐蚀、硝
酸盐应力腐蚀开裂、螨变、石墨化;
c) 待生斜管、再生斜管、循环斜管:耐火材料退化、冲蚀、热疲劳、硝酸盐应力腐蚀开裂; d)再生滑阀:连多硫酸应力腐蚀开裂、耐火材料退化、冲蚀。
6.1.4外取热单元:
a)外取热器出人口烟气管道:耐火材料退化、冲蚀、硝酸盐应力腐蚀开裂; b)外取热器(烟气侧):蠕变、高温氧化腐蚀、耐火材料退化、冲蚀、烟气露点腐蚀、硝酸盐应力腐蚀
开裂; c)外取热器(水侧):锅炉冷凝水腐蚀、汽蚀。
6.2分馏工段
6.2.1分馏单元:
a)分馏塔塔顶:湿硫化氢破坏、氯化铵腐蚀、酸性水腐蚀(碱式酸性水)、碳酸盐应力腐蚀开裂 b)分馏塔塔釜:高温硫化物腐蚀(无氢气环境)、蠕变、石墨化、冲蚀、475℃脆化。
6.2.2油浆单元:
a)分馏塔底出口油浆管道、原料油循环油浆热交换器(油浆侧)、循环油浆蒸汽发生器(油浆侧)、
产品油浆-热水热交换器(油浆侧)及相连管道:高温硫化物腐蚀(无氢气环境)、冲蚀;
b)油浆冷却器及相连管道:湿硫化氢破坏、冲蚀;
循环油浆蒸汽发生器(蒸汽侧):锅炉冷凝水腐蚀、汽蚀、管束振动、碱应力腐蚀开裂;
d)汽包:锅炉冷凝水腐蚀、汽蚀; e)产品油浆-热水热交换器(水侧)、油浆冷却器(水侧)及相连管道:冷却水腐蚀。
6.2.3中段油单元:
a)分馏塔侧线出口中段油管道、原料油一中段油热交换器(中段油侧)、分馏一中段油热水热交
换器(中段油侧)及相连管道:高温硫化物腐蚀(无氢气环境)、氯化铵腐蚀、冲蚀; b)一中段油热水热交换器(水侧):冷却水腐蚀; c)一中段油热水热交换器(水侧)相连循环水管道:冷却水腐蚀、冲蚀;
分馏塔侧线出口二中段油管道、分馏二中段油蒸汽发生器(中段油侧)及二中段油返回分馏塔
d)
管道:高温硫化物腐蚀(无氢气环境)、冲蚀; e) 分馅二中段油蒸汽发生器(蒸汽侧)及汽包:锅炉冷凝水腐蚀、汽蚀; f)重污油管道:高温硫化物腐蚀(无氢气环境)、冲蚀。
6.2.4轻柴油单元:
a)分馏塔出口轻柴油管道至轻柴油汽提塔人口:高温硫化物腐蚀(无氢气环境)、冲蚀; b)轻柴油汽提塔塔顶:氯化铵腐蚀; c)轻柴油汽提塔塔釜:高温硫化物腐蚀(无氢气环境); d)轻柴油汽提塔塔釜出口管道、轻柴油-富吸收油热交换器(轻柴油侧)及相连管道、原料油-轻柴
3
GB/T 33578.2—2017
油热交换器(轻柴油侧)及相连管道:高温硫化物腐蚀(无氢气环境)、冲蚀; e) 轻柴油-热水热交换器(柴油侧)、贫吸收油冷却器(柴油侧)及相连管道、轻柴油冷却器(柴油
侧)及相连管道:湿硫化氢破坏、冲蚀;
f) 轻柴油-热水热交换器(水侧)、贫吸收油冷却器(水侧)、轻柴油冷却器(水侧):冷却水腐蚀; g) 循环水管道:冷却水腐蚀、冲蚀。
6.2.5分馏塔顶循环单元:
a) 分馏塔顶循环油抽出管道、顶循环油热水热交换器(油侧)及出口返分馏塔回流管道:酸性水腐
蚀(碱式酸性水)、氯化铵腐蚀、冲蚀、湿硫化氢破坏、碳酸盐应力腐蚀开裂; b)顶循环油热水热交换器(水侧):冷却水腐蚀 c)顶循环油热水热交换器(水侧)相连循环水管道:冷却水腐蚀、冲蚀。
6.2.6分馏塔顶油气单元:
分馏塔顶出口油气管道至分馏塔顶油气分离罐入口:酸性水腐蚀(碱式酸性水)、氯化铵腐蚀、
a)
二氧化碳腐蚀、冲蚀、湿硫化氢破坏、碳酸盐应力腐蚀开裂; b) 分馏塔顶油气冷却器(油气侧)、分馏塔顶油气空冷器管箱及管束、分馏塔顶油气分离罐:酸性
水腐蚀(碱式酸性水)、氯化铵腐蚀、二氧化碳腐蚀、湿硫化氢破坏、碳酸盐应力腐蚀开裂;分馏塔顶油气分离罐底出口酸性水管道、酸性水缓冲罐底出口酸性水管道:酸性水腐蚀(碱式
c)
酸性水)、氯化铵腐蚀、冲蚀、湿硫化氢破坏、碳酸盐应力腐蚀开裂;
d) 酸性水缓冲罐:湿硫化氢破坏、酸性水腐蚀(碱式酸性水)、氯化铵腐蚀、二氧化碳腐蚀、碳酸盐
应力腐蚀开裂;
e) 酸性水缓冲罐顶出口酸性气管道:二氧化碳腐蚀、湿硫化氢破坏、冲蚀; f) 粗汽油抽出管道、回流管道:湿硫化氢破坏、冲蚀; g) 分馏塔顶油气冷却器(水侧):冷却水腐蚀。
6.2.7富气压缩单元:
a 富气管道至气压机人口油气分离罐、干气管道至干气分液罐:湿硫化氢破坏、酸性水腐蚀(碱式
酸性水)、冲蚀、二氧化碳腐蚀、碳酸盐应力腐蚀开裂; b)气压机人口油气分离罐、干气分液罐、中间冷却器、气液分离罐、压缩富气空冷器管箱和管束、
气压机出口油气分离罐:湿硫化氢破坏、酸性水腐蚀(碱式酸性水)、二氧化碳腐蚀、碳酸盐应力腐蚀开裂;
c) 气压机入口油气分离罐顶部出口富气管道、干气分液罐顶部出口干气管道、压缩机一级和二级
出口管道、中间冷却器出口管道至气液分离罐、气液分离罐顶出口管道至压缩机、压缩富气空冷器进出口管道至气压机出口油气分离罐:湿硫化氢破坏、酸性水腐蚀(碱式酸性水)、二氧化碳腐蚀、冲蚀、碳酸盐应力腐蚀开裂;
d)气压机人口油气分离罐底出口凝液管道、干气分液罐底出口凝液管道、气液分离罐底出口凝液
管道、气压机出口油气分离器罐底酸性水管道:湿硫化氢破坏、酸性水腐蚀(碱式酸性水)、冲蚀、碳酸盐应力腐蚀开裂;
e)气压机出口油气分离罐底富气管道至吸收塔:湿硫化氢破坏、二氧化碳腐蚀、冲蚀。 6.3吸收稳定工段 6.3.1 吸收单元:
a) 稳定汽油管道至吸收塔:湿硫化氢破坏、冲蚀; b) 吸收塔塔顶:湿硫化氢破坏、二氧化碳腐蚀; c) 吸收塔塔釜:湿硫化氢破坏、酸性水腐蚀(碱式酸性水)、碳酸盐应力腐蚀开裂; d) 吸收塔底出口富吸收油管道:湿硫化氢破坏、酸性水腐蚀(碱式酸性水)、碳酸盐应力腐蚀开裂、 4
GB/T33578.2—2017
冲蚀;吸收塔顶出口贫气管道:湿硫化氢破坏、二氧化碳腐蚀、冲蚀;
e) f) 吸收塔一中段油抽出及回流管道:湿硫化氢破坏、二氧化碳腐蚀、冲蚀;
g) 吸收塔一中段油冷却器(油侧):湿硫化氢破坏、二氧化碳腐蚀; h)二中段油抽出及回流管道:湿硫化氢破坏、酸性水腐蚀(碱式酸性水)、冲蚀、碳酸盐应力腐蚀
开裂; i) 吸收塔二中段油冷却器(油侧):湿硫化氢破坏、酸性水腐蚀(碱式酸性水)、碳酸盐应力腐蚀
开裂;吸收塔一中段油冷却器(水侧)及相连循环水管道、吸收塔二中段油冷却器(水侧)及相连循环水管道:冷却水腐蚀。
j)
6.3.2 再吸收单元:
a) 贫吸收油管道至再吸收塔:湿硫化氢破坏、冲蚀; b) 再吸收塔顶:湿硫化氢破坏、二氧化碳腐蚀; c) 再吸收塔签:湿硫化氢破坏; d) 再吸收塔底出口富吸收油管道:湿硫化氢破坏、冲蚀;
塔顶出口干气管道、干气分液罐顶出口干气管道:湿硫化氢破坏、二氧化碳腐蚀、冲蚀;
e) f)干气分液罐:湿硫化氢破坏、二氧化碳腐蚀;
g)干气分液罐底出口管道:湿硫化氢破坏、冲蚀。 6.3.3 解析单元:
a)凝缩油管道至解析塔口:湿硫化氢破坏、酸性水腐蚀(碱式酸性水)、冲蚀、碳酸盐应力腐蚀
开裂; b) 稳定汽油-凝缩油热交换器(凝缩油侧):湿硫化氢破坏、酸性水腐蚀(碱式酸性水)、碳酸盐应力
腐蚀开裂; c) 稳定汽油-凝缩油热交换器(稳定汽油侧):湿硫化氢破坏; d) 解析塔塔顶:湿硫化氢破坏、酸性水腐蚀(碱式酸性水)、二氧化碳腐蚀、碳酸盐应力腐蚀开裂; e) 解析塔塔釜:湿硫化氢破坏、酸性水腐蚀(碱式酸性水)、碳酸盐应力腐蚀开裂; f) 解析塔顶出口解析气管道:湿硫化氢破坏、二氧化碳腐蚀、冲蚀; g) 解析塔底出口脱乙烷汽油管道及回流管道:湿硫化氢破坏、酸性水腐蚀(碱式酸性水)、冲蚀、碳
酸盐应力腐蚀开裂;
h) 解析塔底重沸器(油侧):湿硫化氢破坏、酸性水腐蚀(碱式酸性水)、碳酸盐应力腐蚀开裂; i) 解析塔底重沸器(蒸汽侧):锅炉冷凝水腐蚀、汽蚀; i) 蒸汽管道:冲蚀、汽蚀、锅炉冷凝水腐蚀; k) 凝结水罐及蒸汽扩容器:锅炉冷凝水腐蚀、汽蚀。
6.3.4禾 稳定单元:
a)脱乙烷汽油管道至稳定塔人口:湿硫化氢破坏、酸性水腐蚀(碱式酸性水)、冲蚀、碳酸盐应力腐
蚀开裂;
b) 稳定塔进料热交换器(脱乙烷汽油侧):湿硫化氢破坏、酸性水腐蚀(碱式酸性水)、碳酸盐应力
腐蚀开裂; c) 稳定塔塔顶:湿硫化氢破坏、酸性水腐蚀(碱式酸性水)、二氧化碳腐蚀、碳酸盐应力腐蚀开裂; d) 稳定塔塔釜:湿硫化氢破坏; e) 稳定塔底重沸器(稳定汽油侧):湿硫化氢破坏、二氧化碳腐蚀; f) 稳定塔底重沸器(蒸汽侧):锅炉冷凝水腐蚀; g) 稳定塔顶出口液态烃管道、稳定塔顶油气空冷器出口液态烃管道:湿硫化氢破坏、酸性水腐蚀
5