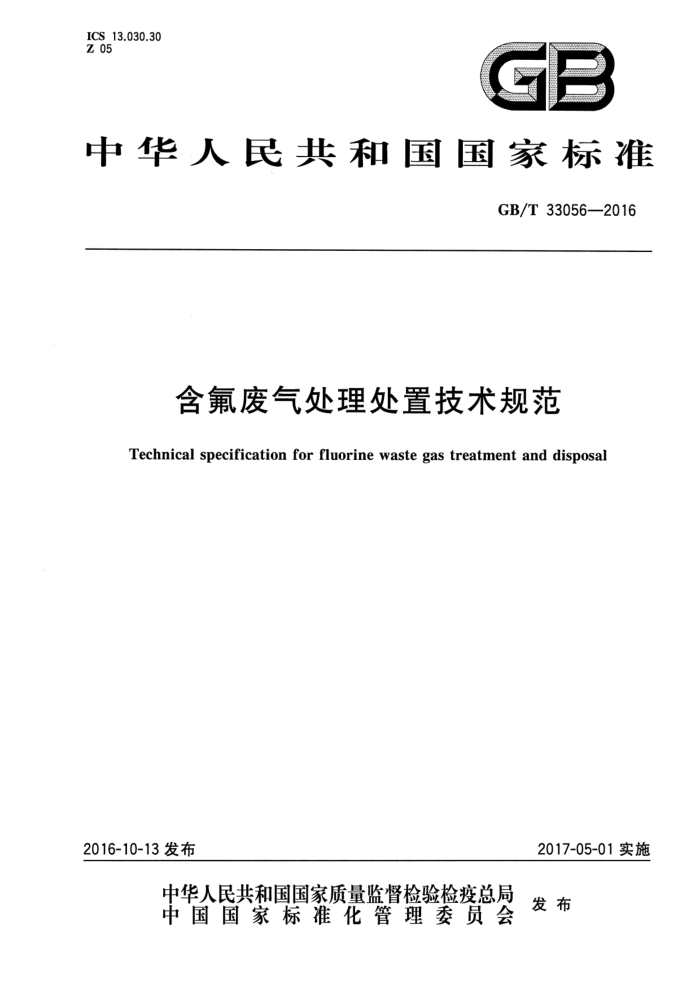
ICS_13.030.30
Z 05
P
中华人民共和国国家标准
GB/T 33056—2016
含氟废气处理处置技术规范
Technical specificationforfluorinewastegastreatment anddisposal
2017-05-01实施
2016-10-13发布
中华人民共和国国家质量监督检验检疫总局中国国家标准化管理委员会
发布
GB/T 33056—2016
前言
本标准按照GB/T1.1—2009给出的规则起草。 本标准由中国石油和化学工业联合会提出。 本标准由全国废弃化学品处置标准化技术委员会(SAC/TC294)归口。 本标准起草单位:云南氟业环保科技股份有限公司、潍坊大耀新材料有限公司、厦门高普尔自动化
设备有限公司、中化重庆滘陵化工有限公司、泉州市云尚三维科技有限公司、贵州瓮福蓝天氟化工股份有限公司、浙江省化工研究院有限公司、贵州省产品质量监督检验院、中海油天津化工研究设计院。
本标准主要起草人:林明卉、王强、冯建平、李兵、许华港、孟文祥、方路、陈建敏、钟宏波、龚宁、 史婉君、赵美敬。
-
GB/T33056—2016
含氟废气处理处置技术规范
1范围
本标准规定了含氟废气的主要成分、处理处置方法和环境保护要求。 本标准适用于湿法磷酸及磷肥生产过程中产生的含氟废气。
2规范性引用文件
下列文件对于本文件的应用是必不可少的。凡是注日期的引用文件,仅注日期的版本适用于本文件。凡是不注目期的引用文件,其最新版本(包括所有的修改单)适用于本文件。
GB7744工业氢氟酸 GB7746工业无水氟化氢 GB14554恶臭污染物排放标准 GB16297大气污染物综合排放标准 HG/T4692工业氟硅酸铵
3含氟废气的主要成分
含氟废气的主要成分为四氟化硅(SiF4)气体和氟化氢(HF)气体。
4 处理处置方法
4.1生产氟硅酸铵 4.1.1原理
用氟化铵溶液吸收含氟废气,得到氟硅酸铵溶液,经冷却结晶,离心分离、干燥后即得成品。其反应方程式如下:
SiF+2NH,F→(NH)SiF
分离后的稀氟硅酸铵与氨反应,得到浓度较低的氟化铵溶液,氟化铵溶液可用于吸收含氟废气,其
反应方程式如下:
(NH4)SiF+4NH+2HzO→6NH,F+SiO
也可用氟化铵溶液吸收含氟废气,得到氟硅酸铵溶液,不进行冷却结晶而直接通入氨气,可获得浓
度较高的氟化铵溶液,氟化铵溶液可用于制取如氟化铵、氟化氢铵、氟化铝等多种无机氟盐。同时可加水稀释一部分浓度较高的氟化铵溶液,稀释后用于吸收含氟废气。
4.1.2工艺流程
一塔和二塔用浓度15%~25%的氟化铵溶液作为吸收介质,三塔用水作为吸收介质,含氟废气经一塔和二塔吸收生成氟硅酸铵,此时含氟废气基本吸收完全,而用三塔吸收一塔和二塔未吸收完全的少量含氟废气,同时把一塔和二塔氟化铵溶液挥发出的氟化铵、氟硅酸铵及游离氨进行洗涤吸收。一塔吸
1
GB/T33056—2016
收后的氟硅酸铵经冷却结晶即可分离出氟硅酸铵产品,分离氟硅酸铵产品后的稀氟硅酸铵溶液用液氨氨化,获得浓度15%25%的氟化铵溶液,返回一塔和二塔作为吸收介质,三塔的吸收液达到相应指标后加人到分离后的稀氟硅酸铵溶液内进行氨化或直接与氨气反应制取多种无机氟盐。
生产氟硅酸铵工艺流程图见图1。
含氟废气吸收系统
一塔上 塔 三塔 一达标排放
含氟废气
氨化系统
氯硅酸铵溶液
............
氟化铵溶液
+..........
一级冷却结晶槽
氨陈化 过滤机 二氧化硅渣
氨化器
*4
二级冷却结晶槽
稀氟硅酸铵溶液
..........
三级冷却结晶槽
浓密机 缓冲槽 离心机 电炉 氟硅酸铵成品
固液混合物
氟硅酸铵冷却结晶系统
氨硅酸铵产品分离系统
图1生产氟硅酸铵工艺流程图
4.1.3工艺控制条件
一塔和二塔用浓度为15%25%的氟化铵溶液作为吸收介质,吸收时一般控制pH为2.5~3.0即达到相应指标,达到指标后氟化铵溶液全部吸收含氟废气后反应为氟硅酸铵。一般吸收时氟化铵溶液从二塔加入,然后溢流至一塔,达到指标后排尽一塔内吸收介质,然后从二塔补人新鲜的氟化铵溶液用作吸收介质,二塔内原来的氟化铵溶液溢流至一塔。控制一塔吸收液的pH为2.0士0.5,吸收液达到该 pH即排出一塔内的吸收液,排出吸收液后从二塔补人新的氟化铵作为吸收介质。而三塔吸收一塔和二塔未吸收完全的少量含氟废气,同时把一塔和二塔氟化铵溶液挥发出的氟化铵、氟硅酸铵及游离氨进行洗涤吸收。三塔通过控制波美度以控制三塔内吸收液浓度,波美度控制不超过20,测量吸收液温度,然后用量程为0~35的波美比重计测量波美度,波美度达到20即把吸收液排出并加水用于三塔吸收,三塔的吸收液中含氟硅酸、氟化铵、氟硅酸铵,可加人到分离后的稀氟硅酸铵溶液内进行氨化或直接与氨气反应制取多种无机氟盐。 4.1.4主要设备
高压离心风机、喷淋式吸收塔、耐腐砂浆泵、烟窗、冷却结晶槽、浓密机、缓冲槽、离心机、电炉、稀氟硅酸铵储槽、振动流化床、旋风除尘器、液氨储罐、氨化器、氨陈化槽、过滤机、上悬式离心机、稀氟化铵储槽、稀氟化铵输送泵等。
2
GB/T33056—2016
4.1.5产品质量
氟硅酸铵产品质量应符合HG/T4692的规定。 4.2生产无水氟化氢 4.2.1原理
含氟废气通过吸收制得稀氟硅酸,提浓后与浓硫酸反应的方法。在反应器中浓硫酸将浓氟硅酸分
解,生成氟化氢和四氟化硅。通过蒸馏得到粗氟化氢气体,再经预净化、冷凝和精馏制成无水氟化氢产品,四氟化硅气体进人氟硅酸浓缩器对稀氟硅酸进行提浓。 4.2.2工艺流程 4.2.2.1含氟废气吸收系统
含氟废气通过两级逆流吸收得到稀氟硅酸(一级吸收塔采用工艺水作为补充液)。 4.2.2.2脱砷系统
稀氟硅酸经脱砷系统脱砷后,进人尾气洗涤系统(原料中砷含量低于相关要求的不需经过该系统)。 4.2.2.3尾气洗涤系统
稀氟硅酸送人尾气洗涤系统吸收装置产生的含氟气体。尾气经多级洗涤达标排放,吸收液送入氟硅酸浓缩器。 4.2.2.4反应系统
浓硫酸经硫酸吸收塔吸收蒸馏塔出来气体中残留的氟化氢后进入反应器。在反应器中,浓硫酸将浓氟硅酸分解,生成氟化氢和四氟化硅。其反应方程式如下
HzSiF+HzSO→SiF,+2HF+HSO4
4.2.2.5 5氟硅酸浓缩系统
反应器出来的四氟化硅进入浓缩吸收器,对尾气系统输送来的稀氟硅酸进行提浓。其反应方程式如下:
3SiF,+2H,0→2HzSiF+SiO
4.2.2.6过滤系统
氟硅酸浓缩过程中产生二氧化硅沉淀通过过滤机分离,二氧化硅渣用于生产其他产品,浓氟硅酸进入反应器。 4.2.2.7蒸馏系统
反应器来的含氟硫酸进人蒸馏系统进行蒸馏得到粗氟化氢气体和稀硫酸。 4.2.2.8汽提系统
来自蒸馏系统的硫酸,进人汽提塔,脱除少量的氟化氢,稀硫酸送到其他装置使用。 4.2.2.9预净化系统
粗氟化氢气体进入预净化系统脱除大部分杂质。
3
GB/T33056—2016
4.2.2.10 冷凝系统
来自预净化系统的粗氟化氢气体经过冷凝得到粗氟化氢液体。 4.2.2.11精馏系统
液相的粗氟化氢进入精馏塔进行精馏提纯,再经冷凝为液相后得到无水氟化氢。 4.2.2.12 :包装储存系统
来自精馏系统的氟化氢进入贮槽储存,按要求进行包装。 生产无水氟化氢工艺流程图见图2。
反应系统 预净化系统 冷凝系统 精馏系统
氟硅酸浓缩系统
过滤系统
浓氟硅酸
氧化硅渣 过滤机
浓缩吸收器
反应器
预净化器
冷凝器
精馏塔
!放空
硫酸吸收塔
一级吸收塔
工艺水
罐区、灌装
尾气处理
稀硫酸槽
蒸馏塔
汽提塔
含氟废气
二级吸收塔
稀氟硅酸 浓硫酸
无水氟化氢
脱砷沉淀槽
稀硫酸
包装储存系统
脱砷系统
含氟废气吸收系统
蒸馏系统
尾气洗涤系统
汽提系统
图2生产无水氟化氢工艺流程图
4.2.3 工艺控制条件 4.2.3.1 稀氟硅酸浓度:≥18%。 4.2.3.2 浓硫酸浓度:≥98%。 4.2.3.3 稀硫酸浓度:60%~75%。 4.2.3.4 蒸汽压力:中压蒸汽。 4.2.3.5 粗氟化氢槽液位:≤80%。 4.2.3.6 精馏塔塔压:≤0.3MPa。 4.2.3.7 精馏塔塔顶温度:≤60℃。 4.2.3.8 精馏塔塔釜温度:≤65℃。 4.2.3.9 产品储槽液位:≤80%。 4.2.3.10 尾气风机真空度:≤7kPa。 4.2.4主要设备
含氟废气一级吸收塔、含氟废气二级吸收塔、尾气吸收器、硫酸吸收塔、反应器、蒸馏塔、预净化器、 冷凝器、精馏塔、产品贮槽、汽提塔、稀硫酸槽、浓缩吸收器、过滤机、脱砷沉淀槽等。
4
GB/T33056—2016
4.2.5产品质量
无水氟化氢产品质量应符合GB7746的规定。 4.3生产氢氟酸 4.3.1原理
将含氟废气按4.2制成无水氟化氢后,用脱盐水或纯水配置而得。制取氢氟酸原理同4.2.1。 4.3.2工艺流程
将无水氟化氢送人氟化氢吸收器,用脱盐水或纯水吸收得到氢氟酸,氢氟酸送人贮槽储存。不凝气体用真空泵送人无水氟化氢装置尾气洗涤器。生产氢氟酸工艺流程图见图3。
氟化氢吸收器
氢氟酸贮槽氢氟酸系统 AHF装置尾气
无水氟化氢包装存储系统
放空
真空泵
洗涤器
图3 生产氢氟酸工艺流程图
4.3.3工艺控制条件 4.3.3.1真空度:≤10kPa。 4.3.3.2 2氢氟酸贮槽液位:≤80%。 4.3.4主要设备
氟化氢吸收器、氢氟酸贮槽、真空泵、装置尾气洗涤器等。 4.3.5 5产品质量
氢氟酸产品质量应符合GB7744的规定。
5环境保护要求
5.1 处理后的恶臭物质应符合GB14554的排放要求。 5.2处理后的废气、粉尘应符合GB16297的排放要求。
n