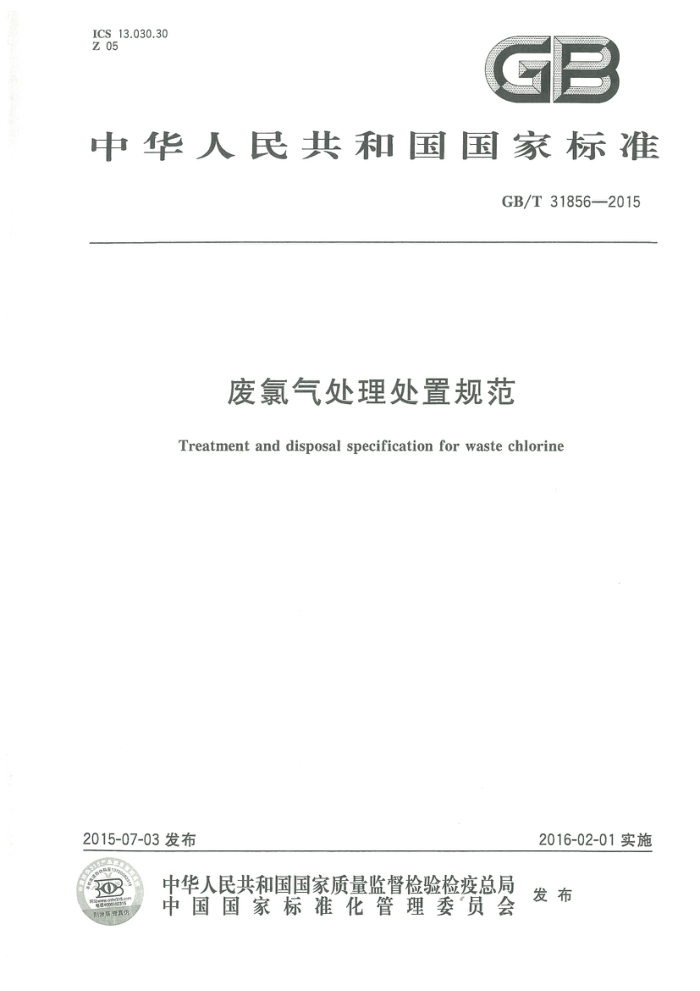
ICS13.030.30 Z 05
CE
中华人民共和国国家标准
GB/T31856—2015
废氯气处理处置规范
Treatment and disposal specification for waste chlorine
2016-02-01实施
2015-07-03发布
中华人民共和国国家质量监督检验检疫总局
KO
中国国家标准化管理委员会 发布
GB/T 31856—2015
前言
本标准按照GB/T1.1一2009给出的规则起草。 本标准由中国石油和化学工业联合会提出。 本标准由全国废弃化学品处置标准化技术委员会(SAC/TC294)归口。 本标准起草单位:江苏奥喜埃化工有限公司、山东新龙集团有限公司、中海油天津化工研究设计院、
河南佰利联化学股份有限公司。
本标准主要起草人:徐正群、李通、杨裴、周金龙、孙雪胜、陈建立、王晓玲、廉晓燕。
I
GB/T31856—2015
废氯气处理处置规范
1范围
本标准规定了废氯气处理处置的术语和定义、处理处置方法和安全要求。 本标准适用于废氯气的处理处置。
2 规范性引用文件
下列文件对于本文件的应用是必不可少的。凡是注日期的引用文件,仅注日期的版本适用于本文件。凡是不注日期的引用文件,其最新版本(包括所有的修改单)适用于本文件。
GB320工业用合成盐酸 GB16297大气污染物综合排放标准 GB19106 次氯酸钠 GBZ2.1工作场所有害因素职业接触限值 第1部分:化学有害因素 HG/T4684 液氯泄漏的处理处置方法 HJ 547 固定污染源废气氯气的测定 碘量法
3术语和定义
下列术语和定义适用于本文件。
3.1
废氯气wastechlorine 在生产、使用系统产生的泄压氯气,钢瓶或液氯储槽内的残余氯气以及开停车过程产生的废氯气及
来自生产系统、使用系统、贮存系统的设备及管道出现不正常现象时产生的氯气等。
4 4处理处置方法
4.1碱液吸收工艺 4.1.1原理
废氯气与稀碱液发生化学反应,生成次氯酸钠。其化学反应方程式如下:
2NaOH+Cl2→NaCIO+NaCl+H,O
此反应为放热反应,当反应热蓄积,温度上升,会发生以下副反应:
3Cl. +6NaOH→ NaC1+ 5NaCIO:+ 3H,0
4.1.2原料 4.1.2.1氢氧化钠溶液:质量分数不小于30%。 4.1.2.2水。
1
GB/T31856—2015
4.1.3工艺流程
来自液体氢氧化钠储槽的氢氧化钠溶液与水通过流量计控制按一定比例进人混合器,配制成一定浓度的稀碱液,贮存在碱液储槽中。
废氯气从氯吸收塔的下部进入吸收塔,在填料层与塔顶循环喷淋下来的稀碱液逆流接触,进行吸收反应。产生的热量会使吸收碱液的温度升高,较热的吸收液进人吸收塔循环槽,通过加压进人吸收塔冷却器,与循环冷却水或冷冻水进行热交换,应保证吸收液温度不大于45℃。从吸收塔冷却器出来的温度较低的吸收液重新进人氯吸收塔,继续吸收不断产生的废氯气。从氯吸收塔顶出来的尾气再进人尾气塔底部,在填料层继续与塔顶循环喷淋下来的稀碱液反应逆流接触,进行吸收反应。达到环保排放标准的尾气经塔顶导出,通过风机排人大气。同样,尾气吸收塔中的吸收液吸收氯气后温度升高,从塔底流出至尾气塔循环槽,通过加压进人屋气塔冷却器,与循环冷却水或冷冻水进行热交换,应保证吸收液温度不大于45℃。从尾气塔冷邮器出来的温度较低的吸收液重新进人尾气吸收塔,继续吸收。
随时监控游离碱和有效氯的浓度,确保吸收效果,在放出次氯酸钠溶液或打碱过程中,不应出现两个循环槽同时进行操作的情况。
碱液吸收工艺处理废氯气工艺流程图见图1
尾气
尾气
废氟牛
磷冷却器
尾气塔循环槽
吸收塔循环槽
液体氢氧化钠
储槽
一成品
混合器
稀碱瘦储
次氯酸钠成品槽
水
图1碱液吸收工艺处理废氯气工艺流程图
4.1.4工艺过程控制 4.1.4.1工艺参数
碱液吸收处理废氯气的工艺参数推荐如下:
反应温度不大于45℃;稀碱液的浓度为15%~20%。
-
2
GB/T31856—2015
4.1.4.2 过程控制
4.1.4.2.1 严格控制操作温度,通过冷却系统及时将反应热移走。 4.1.4.2.2 严格控制游离碱含量,确保吸收效果。 4.1.4.2.3 密切注意废氯气系统压力的变化,控制好风机的抽气量,确保废氯气系统压力控制在负压状态,严禁氯气外泄污染环境。 4.1.4.2.4定时分析、监测循环碱液的浓度。 4.1.4.2.5 碱液吸收工艺的应用实例参见附录A。 4.1.5成品控制
利用废氟气所生产的次氯酸钠溶液产品应符合GB19106的技术要求。 4.1.6 6排放控制
尾气排放应符合GB16297的相关要求。 4.1.7 主要设备
碱液吸收工艺处理废氯气的主要设备见表1。
表1碱液吸收工艺主要设备
设备名称
材质聚氯乙烯/玻璃钢聚氯乙烯/玻璃钢聚氯乙烯/玻璃钢聚氯乙烯/玻璃钢
氯吸收塔尾气吸收塔吸收塔循环槽尾气塔循环槽液碱储槽碱液储槽吸收塔冷却器尾气塔冷却器引风机
304不锈钢 304不锈钢
钛钛玻璃钢
4.1.8 装置配置要求 4.1.8.1氯生产、使用企业应设置事故氯吸收塔)装置,在有可能出现氯气泄漏的装置区域,安装与吸收装置连接设施。吸人端采用非金属塑料弹性软管,并可移动,非金属塑料弹性软管的长度、直径大小与数量应根据可能泄漏的氯气量和泄漏点位置确定,保证泄漏的氯气及时被导人吸收装置。移动风管配置具体可参见附录B,也可以根据氯气生产贮存或用氯规模,在生产系统或液氯储存场所附近设置单独的与事故应急相应的泄漏氯气吸收装置。 4.1.8.2设备应具备自动切换备用电源和24h连续运行的能力,并与系统主要设备动力电紧急停车系统连锁控制。 4.1.8.3应满足紧急情况下的系统事故氯吸收处理能力,吸收液循环槽具备切换、备用和配液的条件,保证设备有效运行。 4.1.8.4液碱储槽配备保温措施,应具备自控调节阀,与碱循环槽进行液位连锁控制,保证有足够的碱
3
GB/T318562015
液供应;循环泵应配备用泵;大型吸收塔无害化气体放空管高度不应小于25m,并应高于现场建筑物或设备高度2m以上,不应无序排放。 4.1.8.5所有氯气生产和使用场所应配备相应的氮气捕消器,用于处理小规模的氟气泄漏。 4.2合成盐酸工艺 4.2.1原理
生产过程中产生的废氯气经过干燥、净化处理后,与氢气发生反应,用于合成氯化氢气体,氯化氢气体溶于水或用水喷淋形成盐酸。其化学反应方程式如下:
HCh-2HCl
4.2.2原料 4.2.2.1氢气
氢气中氢(H含量不小于98%(体积分数)。 4.2.2.2 氯气
氯气中氟(C1)含量不小手95%(体积分数 氧食量不大于4%(体积分数且水分不大于
6%体积分数)氢H)食量有大于3%(体
0.06%(质量分数);或者氯积分数)。 4.2.3 工艺流程
氢气经炉前氢气阻灵器 墨合成 氯气按 比例在烧的作用下生成氯化氢气体。从
气体经 冷却后进人石婴知塔冷却至50C以下,进人HCl
合成炉出来的600℃左右吸收塔,用HCI尾气吸收塔 精酸 生成药1%成品酸,必塔底经酸进 人成品槽。
在HO吸收塔内未被 收的策化先续吸收,不性气体被水摩 射泵捕
吸收塔顶部被由吸收水泵送来的吸收水继
.
S
合成盐酸工艺处理废氯
纯水水箱
石盈冷却塔 HCI吸收塔
水喷射泵
石墨合成炉
冷却水
盐酸成品
氯气氢气
冷却水
图2合成盐酸工艺处理废氯气的工艺流程图
4
GB/T31856—2015
4.2.4工艺控制参数
合成盐酸工艺处理废氯气的工艺控制参数如下:
氯气压力为0.06MPa~0.20MPa;氢气压力不小于6.67kPa;夹套水温不大于60℃;进塔温度不大于60℃;
—进炉氟气:氢气=1.05~1.1 ——吸收水温不大于45℃;进炉阻力不大于5.33kPa;
成品酸温度不大于60℃。
4.2.5成品控制
利用废氯气所生产的盐酸产品应符合GB320的要求。 4.2.6 6主要设备
合成盐酸工艺进行废氯气处理处置主要设备有石墨合成炉、石墨冷却塔、HCI吸收塔、HC1尾气吸收塔、水喷射泵。 4.2.7其他要求 4.2.7.1随时注意氯氢的压力,防止回火及氯气过量。 4.2.7.2开车时,点火人员不可正对氢气进炉夹布胶管,以免火焰喷出灼伤,点火时如炉内发生爆鸣致使火焰熄灭时,看火人员应迅速切断气源,关闭氢气阀门,水喷射泵抽气15min后,拔出氢气进炉夹布胶管,继续置换合格后方可重新点炉。 4.2.7.3正常停车时,应逐渐调小进炉气量,先关氢气调节阀,再关氢气球阀,并同时迅速关闭氯气调节阀,停炉后,系统抽10min~15min后方可关闭水喷射泵。 4.3氧化还原工艺 4.3.1原理
以氯化亚铁溶液作为吸收剂,铁作为再生剂,利用氯化亚铁与氯气发生氧化反应,吸收泄漏的氯气反应后的溶液再跟铁发生还原反应,恢复其吸收作用,获得再生,循环利用。其化学反应方程式如下:
2FeCl2+Cl2→2FeCl3 2FeCls+Fe→3FeCl2
4.3.2原料 4.3.2.1 氯化亚铁溶液。 4.3.2.2铁屑。 4.3.3工艺流程
当氯气发生泄漏时,启动漏氯吸收保护装置,离心风机将气体抽送到反应吸收塔,气体由下向上作湍流运动,吸收液由上向下喷淋,通过填料层充分接触,让气液两相之间物质发生充分的物质传递,氯气被吸收液有效吸收并在吸收液中与氯化亚铁发生氧化还原反应生成三氯化铁,反应后的液体又流回储液再生槽,三氯化铁又被铁屑还原成氯化亚铁,继续吸收氯气,循环使用。直到氯气含量不超过要求,系统自动停止。
6
5
GB/T31856—2015
氧化还原工艺处理废氯气工艺流程图见图3。
尾气回流
吸收剂喷淋
铁屑 1
含氟空气加氧间
反应吸收塔
储液再生槽
风机
耐腐蚀系
吸收剂回流
图3氧化还原工艺处理废氯气工艺流程图
4.3.4工艺控制参数
氧化还原工艺处理废氯气的工艺控制参数如下:
氯化亚铁溶液浓度不小于20%;一过量的铁屑。
4.3.5 主要设备
氧化还原工艺处理废氯气的主要设备有储液再生槽、反应吸收塔、耐腐蚀泵、风机、风管等。 4.4总体要求 4.4.1氯吸收装置设计吸收能力应保证至少具备处理30min生产装置满负荷运行产出的氯气能力。 系统整体应设计合理,能充分提高氯气吸收效率。 4.4.2废氯气处理系统应配备自动控制系统,具备完善的模拟量控制、自控、连锁、报警、保护等功能,设集中和现场两种控制方式, 4.4.3关键工艺参数应能进行自动调节和控制,并能够集中监控。 4.4.4当存在微量泄漏时,预警系统应启动,发出声光报警,提醒有关人员。 4.4.5吸氯装置泄氯报警系统在泄漏的氯气含量达到报警限额时,应能正确、瞬时声光报警,并能迅速启动吸氯装置工作。 4.4.6编程控制器能控制设备全天候、全自动启动装置工作,使设备处于随时待命状态。
5安全要求
5.1氯的特性参见附录C,在氯环境中的作业人员应熟知并掌握。 5.2废氯气处理处置场所应配备防氯气的过滤式防毒面具(全面罩)、正压式空气呼吸器、气密型化学防化服,配备处理液态氯泄漏的防冻伤防护用品。 5.3废氯气处理处置场所应安装有毒气体检测仪,安装距离要求应符合相关规范。 5.4 废氯气处理处置场所应安装有氯气报警器,设定的报警浓度应符合GBZ2.1中的要求。 5.5废氯气处理处置场所进行氯气浓度检测时,应按照HJ547规定的方法操作。 5.6废氯气处理处置过程中可能接触到的化学物质在出现健康危害时的急救措施参见附录D。 5.7 在发生氯气泄漏时的处理处置方法按HG/T4684的要求进行操作。