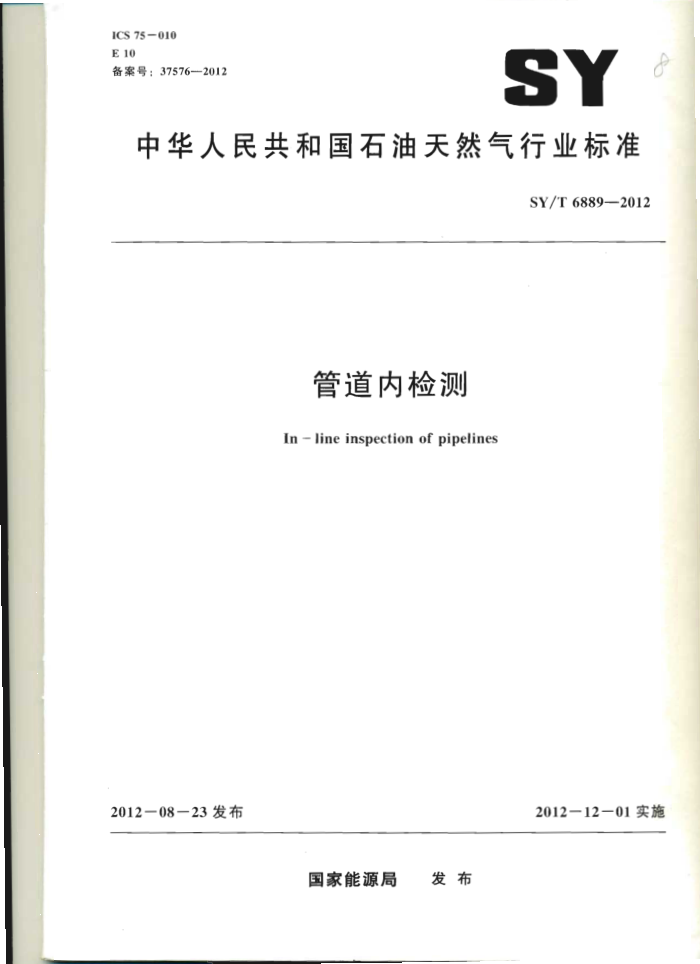
ICS 75010 E 10 备案号:375762012
SY
中华人民共和国石油天然气行业标准
SY/T6889—2012
管道内检测
In-lineinspectionofpipelines
2012一08一23发布
2012一12一01实施
国家能源局 发布
SY/T6889—2012
目 次
前言
0
范围规范性引用文件术语和定义检测器的选择 4. 1 检测器的适宜性 4.2 操作要点 5管道内检测匹配性评估 5. 1 检测器确认 5. 2 管道调查表 5. 3 检测器环境 5. 4 管道及设施的匹配性 5. 5 介质、介质流速、速度要求与介质压力 5. 6 信息收集 5. 7 管道清管 5. 8 管道检测
1
2
3
4
实施计划指导 6. 1 签订合同首要考虑的问题 6. 2 运行报告 6.3 数据规范 6. 4 报告时间表 6. 5 验证要求检测计划 7. 1 制定检测计划时应考虑的因素 7. 2 资源(人员和设备) 7. 3 确定基准与跟踪 7. 4 应急计划 8 数据分析要求, 8. 1 数据分析方法 8. 2 管道特征列表和报告 8. 3 几何检测器—特定的分析与分级方法 8. 4 金属损失(腐蚀)
6
.
专用检测器分析和分级方法
8. 5 裂纹检测技术 专用检测器分析方法 8. 6 惯性工具/测绘技术 专用检测器分析和分级方法 8.7 内检测报告结果与开挖验证的关系
-
SY/T6889—2012
9 数据管理 9. 1 检测数据· 9. 2 检测信息 9.3 腐蚀增长速率的使用 10 新建管道适应性要求 10. 1 设计与建设 10. 2 材料 10. 3 建设信息收集 10), 4 维修记录附录A(资料性附录) 本标准与NACESP(0102:2010相比结构变化情况附录B(资料性附录) 本标准与NACESP010)2:2010)的技术性差异及其原因附录C(规范性附录) 内检测器的类型与检测用途附录D(资料性附录) 管道检测调查表实例参考文献
16
C
16
-
19
20
21
D
SY/T6889—2012
管道内检测
1范围
本标准规定了管道内检测项目的计划、组织、实施等相关活动的过程,以及内检测数据管理和数据分析有关的方法及要求。
本标准适用于输送天然气、危险液体(包括含无水氨的液体)、二氧化碳、水(包括盐水)、液化石油气的钢质管道系统,以及对内检测器功能与稳定性无害的其他系统。
本标准适用于介质驱动式内检测器,不适用于有缆或遥控检测装置。
2规范性引用文件
下列文件对于本文件的应用是必不可少的。凡是注日期的引用文件,仅注日期的版本适用于本文件。凡是不注日期的引用文件,其最新版本(包括所有的修改单)适用于本文件。
SY/T6151钢质管道管体腐蚀损伤评价方法
3术语和定义
下列术语和定义适用于本文件。
3. 1
标识器 above-ground marker (AGM) 置于管道上方的便携或永久性设备,能够探测并记录内检测器的通过信号,或内检测器能够探测
并记录其发射的信号。 3. 2
异常 anomaly 管材、涂层或焊缝的未经验证的偏差。
3. 3
屈曲buckle 管道受到较大塑性变形,造成管壁或管道截面永久性起皱或变形。
3. 4
腐蚀 corrosion 由于与所处环境发生化学或电化学反应,造成某种材料(通常是金属)的劣化
3. 5
裂纹crack,cracking 一种断裂型不连续,其主要特征为锋利的尖端和张开位移处长宽比大
3. 6
变形deformation 形状的永久性改变,如弯曲、屈曲、凹陷、椭圆度、波纹、褶皱或影响管道截面圆度或平度的
其他变化。
-
SY/T6889—2012
3. 7
凹陷dent 因外力,如机械撞击或岩石碰撞,造成管道表面的局部变形。
3. 8
电阻焊 electricresistanceweld(ERW) 通过电阻加热管子的两边,使其熔合的焊缝成形方法。
3. 9
特征 feature 内检测系统检测到的所有物理对象。特征可能是异常、部件、邻近金属物、焊缝、附属物等。
3. 10
地理信息系统 geographical information system(GIS) 能够整合、存储、处理和显示地理参考信息的计算机系统。
3. 11
几何检测器 geometrytool 记录管道或管壁几何情况的一种测量内检测器。
3. 12
全球定位系统 global positioning system(GPS) 利用卫星技术向用户提供地球表面确切位置的导航系统。
3. 13
划痕 gouge 金属机械切削造成的细长凹槽或凹腔。
3. 14
水压试验 hydrostatictest 管道压力试验,在试验管道中完全充满水并加压以确保管道满足设计条件。
3. 15
交互作用准则 interaction rules 将相邻异常按单个较大的异常处理时,制定的异常之间的间隔准则。
3. 16
分层 lamination 由于内部金属分离形成的通常平行于表面的离层。
3. 17
漏磁 magnetic flux leakage (MFL) 使用磁铁两极在管壁上产生磁场的内检测技术。管壁材料的异常影响管壁内磁通量的分布。漏磁
用于检测和表征管壁异常。 3. 18
磁粉检测 Jmagneticparticleinspection(MPI) 使用细磁粉和磁场,定位钢铁材料表面裂纹的无损检测技术。
3. 19
金属损失 metalloss 任何发生金属减损的管道异常。金属损失通常是由于腐蚀所致,但划伤、制造缺陷或机械损伤也
能导致金属损失。 3. 20
椭圆度 ovality
2
SY/T68892012
偏离圆形,如蛋形或类椭圆形。 3. 21
过球指示器 pigsignal 通常指安装在管道上的传感器,能够感知清管器的通过。
3. 22
短节 pupjoint 一种短管件,一般长度为3m或更短。
3.23
量化精度 sizing accuracy 报告的异常尺寸或特性的精度。通常精度用公差和可靠性表示。如金属损失深度的量化精度通常
表示为可靠性为80%时,公差为壁厚的±10%。 3. 24
非满流 slackline 流动的介质不能完全填充管道。
3. 25
褶皱 wrinkle 管子外壁可见的光滑的局部凸起。褶皱有时限定为高度大于壁厚的凸起部分。
3. 26
标准分辨率检测器 standard resolution tool 通常使用线圈传感器,传感器尺寸与间距较大,能够对缺陷的深度进行分级,如轻度(10%~
30%壁厚)、中度(30%~50%壁厚)、严重(50%壁厚以上),一般不能区分是内部缺陷还是外部缺陷。 3. 27
高分辨率检测器 highresolutiontool 与标准分辨率检测器原理基本相同,通常使用霍尔传感器,但使用的传感器尺寸较小、数量较
多、传感器间距较小(通常10mm~17mm),能够较精确地量化缺陷的长度与深度等参数,能够区分是内部缺陷还是外部缺陷。 3. 28
超高分辨率检测器 extra-high resolution tool 与高分辨率检测器相比,使用的传感器尺寸更小、数量更多、传感器间距更小、(通常4mm~
8mm),通常采集两个(轴向与径向)或三个(轴向、径向与环向)方向的数据,能够非常精确地量化缺陷的长度与深度等参数。不但能够区分是内部缺陷还是外部缺陷,还能够探测出凹陷等其他缺陷。 3. 29
通用横轴墨卡托投影 universal transverseMercator (UTM) 一种等角横轴割圆柱投影,为一在圆柱面与地球椭球体面横割于与中央子午线对称的两个小
圆,按经差6°进行的分带投影。
4检测器的选择
4. 1 检测器的适宜性
管道运营方和检测服务方的代表宜共同分析检测的目的和目标,并使内检测器的能力和性能与管道检测的需求相适应。内检测器的类型与检测用途见表C.1,选择时应考虑以下方面:
3
SY/T6889—2012
a) 检测精度和检测能力:检测概率、分类和尺寸判定与预期相符 b) 检测灵敏度:最小可探测异常尺寸小于期望探测的缺陷尺寸。 c) 类型识别能力:能够区分出目标缺陷类型。 d) 量化精度:足够用于评估或确定剩余强度。 e) 定位精度:能够定位异常。 f) 评价要求:内检测结果满足缺陷评价要求。
4. 2 操作要点
管道运营方应向检测服务方提供一套完整的管道调查表,列出待检管段的所有相关参数和特征,管道检测调查表实例参见附录D。应考虑以下操作要点:
a) 管道的物理特性,包括
1) 识别内检测器需要通过管道的特性(如钢材等级、焊缝类型、长度、内径、高程等),
以及所有约束、弯头、已知椭圆度、阀门和无挡条三通; 2) 内检测器在结构、几何形状和可操作性方面差异较大,应考察发球简与收球筒的适
用性; 3) 管道的清洁度会影响检测器的磨损情况、数据采集的完整性和成功运行的其他因素,故
应检查管道的清洁度;
4) 内涂层可能妨碍检测,某些检测器也可能破坏内涂层,实施内检测前应考虑该因素。
b) 输送流体的特性,包括:
1) 流体类型可能影响检测技术的选择; 2) 流体介质的腐蚀性可能限制检测器有效运行的能力; 3) 流速、压力和温度的范围应满足检测服务方的要求; 4) 介质流速影响内检测器的检测速度、性能和检测所需总时间; 5) 检测高流速管道时,宜考虑降低介质的流速,或考虑内检测器的降速能力,或两者同
时考虑;当流速过低时,应考虑增大输量;
6) 应考虑极端温度(极热和极冷)对检测器运行的影响。 c) 内检测器的可靠性。通过分析下述因素,评估内检测器的可靠性:
1) 内检测器的置信水平,如异常的检测概率、分类及量化精度; 2) 内检测器性能的开挖验证情况; 3) 运行成功率和运行失败调查; 4) 内检测器检测管道全长和横截面全周的能力; 5) 指示多种原因导致的异常的能力(异常与检测器最初设计检测的缺陷不同,如通过金属
损失检测器探测凹陷)。
5管道内检测匹配性评估
5.1 检测器确认
如果分析表明选择的内检测器不适合该管段,宜重新选择内检测器。
5. 2 管道调查表
附录D给出了一份典型的运行前管道调查表,该调查表便于运营方收集管道相关信息。内检测服务方通过分析管道运营方提交的管道调查表,可初步评估管道的可检测性。
SY/T6889-2012
5.3检测器环境
检测过程中检测器所处的介质与环境是决定使用何种检测器的重要因素。应考虑下述因素: a) 温度和压力:大多数检测器都有适用的运行温度和压力范围。 b) 流体成分因素:如果介质包含化学物质如硫化氢,宜考虑修改标准检测器的设计以解决腐
蚀性问题。其他化学物质也可能要求对检测器进行改造,宜提前处理。
5.4管道及设施的匹配性 5.4.1 发球和收球设备应适用于不同类型的检测器。发球筒和收球筒可在新建管道期间或现有设备改造期间安装,可以是永久性的也可以是临时性的。应考虑如下内容:
a)操作空间:应调查操作空间,以确保在装卸过程中有足够的空间用于调整内检测器和相关设
备,并确认其他辅助设备的空间要求。 b) 球筒长度:应保证在盲板与截断阀之间有足够的空间,以便能容纳检测器,球简长度要求
如下: 1) 对于发球筒,简体长度宜大于或等于检测器长度,直管段长度可减至最短。对简体长
度小于检测器长度的情况,应考虑其他装载方法,如拉入检测器:
2) 对于收球筒,直管段长度应大于或等于检测器的长度,以确保整个检测器通过截断阀。
简体长度应满足接收检测器时的制动距离。实际长度要求可能差别较大,取决于所使用的检测器,
5.4.2管道的某些物理特征易导致内检测器损伤或卡堵,包括但不限于:
a) 管道内径变化:如屈曲、凹陷、变径、缩径阀、止回阀等,即使检测器有通过这些约束的可
能性,也应逐一考虑每种情况。 植入管道的探头:可能损伤设备和检测器。
b)
c) 土体移动区域:宜考虑检查已知的土体移动区域。 d) 管道壁厚:某些检测器需标定壁厚,检测服务方应考虑壁厚因素;如果壁厚小于6.4mm或
大于13mm,宜提醒检测服务方;适用于厚壁小口径管道的检测器数量和类型较少; 1) 当使用漏磁技术检测气管道时,厚壁管可能导致速度偏移(如检测器通过厚壁管段时
比通过薄壁管段时需要更大的压差)。当检测器运行到薄壁管段时,大压差可能使检测器速度过快,导致数据降级;壁厚变化(如穿越公路与铁路使用的厚壁管)可能导致内检测器出现问题,这取决于
2)
厚壁管与薄壁管之间的过渡类型;阶梯过渡处如同刃口,可能导致内检测器损坏;宜避免阶梯过渡而使用锥形过渡。
e) 小半径弯头:多数检测器都能通过半径大于或等于3D(D为管道直径,下同)的弯头,能
否通过取决于使用的检测器与弯头壁厚,应逐一核查所有半径小于3D的弯头。 连续弯头:即弯头之间没有直管段过渡,可能阻碍检测器通过,造成卡堵。
f)
g) 阀:缩径阀可能导致检测器损坏,甚至检测器卡堵。应仔细评估检测器顺利通过止回阀的
能力;运行内检测器前,应将止回阀阀瓣锁定在全开位置,自动截断阀应取消自动关断功能。
h) 冷弯头和河流穿越:早期建设的管道可能存在小半径弯头、斜接和阶梯过渡,这些位置更
易受土体移动的影响,并可能存在直到实施内检测前还未发现的管道变形。
i) 分输和注入接口:当内检测器通过时,宜关闭分输和注人接口,影响因素包括接口尺寸与方
向、流量、单/双接口、管道污物量和检测器类型。 i)无挡条与连续三通:分接口(大于或等于30%管径)应有挡条,带压开孔的锐边也可能对检
15