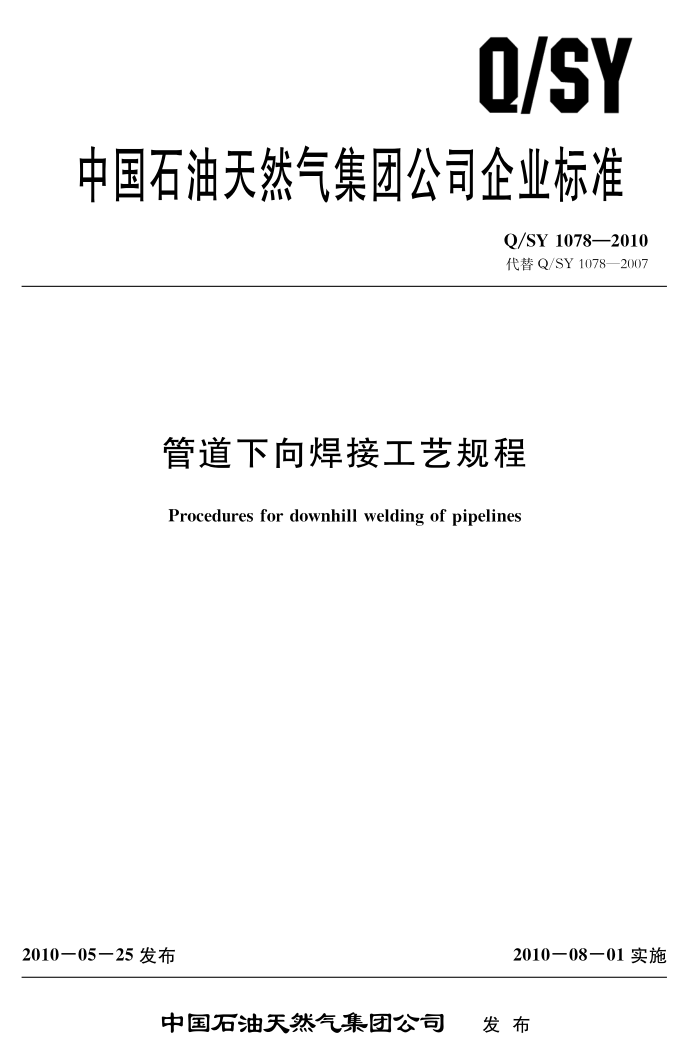
Q/SY
中国石油天然气集团公司企业标准
Q/SY 1078—2010 代替Q/SY1078—2007
管道下向焊接工艺规程
Procedures for downhill welding of pipelines
2010—05—25发布
2010—08—01实施
中国石油天然气集团公司 发布
Q/SY 1078—2010
目 次
前言 1 范围 2 规范性引用文件
术语和定义管材焊接材料焊接设备焊接工艺评定
3
4 5 6 7
.
8 焊接
+
焊缝检验及缺陷返修附录A(资料性附录) 常用钢管的化学成分和力学性能附录B(资料性附录) 下向焊焊材的选用
y
8
1
Q/SY 1078—2010
前言
本标准代替Q/SY1078一2007《管道下向焊接工艺规程》。 本标准与Q/SY1078一2007相比,主要增加了管道半自动下向焊技术等内容,本标准的附录A和附录B为资料性附录本标准由中国石油天然气集团公司石油石化工程建设专业标准化技术委员会提出并归口。 本标准起草单位:中国石油管道焊接培训中心。 本标准主要起草人:高泽涛、李建军、续理、刘光云、吕向阳、孙冬梅、王炜、韩德辉、胡庆
春、王义。
本标准所代替标准的历次版本发布情况为:
Q/CNPC78—2002,Q/SY1078—2007。
II
Q/SY1078—2010
管道下向焊接工艺规程
1范围
本标准规定了管道下向焊接工艺的基本内容,包括焊接材料的选择及焊接参数的范围。 本标准适用于管道环焊缝对接;焊接方法为电弧焊,自动化程度为手工和半自动;材质为碳钢、
低合金钢,输送介质为石油、天然气的管道对接焊缝的全位置下向焊接。其他介质输送管道下向焊接可参照本标准执行。
2规范性引用文件
下列文件中的条款通过本标准的引用而成为本标准的条款。凡是注日期的引用文件,其随后所有的修改单(不包括勘误的内容)或修订版均不适用于本标准,然而,鼓励根据本标准达成协议的各方研究是否可使用这些文件的最新版本。凡是不注日期的引用文件,其最新版本适用于本标准。
GB/T5117碳钢焊条 GB/T 5118个 低合金钢焊条 GB/T8110气体保护电弧焊用碳钢、低合金钢焊丝 GB/T8163 输送流体用无缝钢管 GB/T9711.1石油天然气工业输送钢管交货技术条件第1部分:A级钢管 GB/T9711.2石油天然气工业输送钢管交货技术条件第2部分:B级钢管 GB/T174931 低合金钢药芯焊丝 SY/T0452 :石油天然气金属管道焊接工艺评定 SY/T4103 钢质管道焊接及验收 SY/T4109 石油大然气钢质管道无损检测 JB/T3223 焊接材料质量管理规程 APIStd1104管道和相关设施的焊接 APISpec5L管线钢管规范 ASME锅炉及压力容器规范第Ⅱ卷材料A篇铁基材料标准 ASME锅炉及压力容器规范第X卷焊接和钎焊评定标准 AWSA5.1碳钢手工电弧焊焊条 AWSA5.5低合金钢药皮焊条 AWSA5.18碳钢气保护电弧焊填充金属 AWSA5.28低合金钢气体保护电弧焊填充金属 AWSA5.291 低合金钢药芯焊丝
3术语和定义
下列术语和定义适用于本标准。
3. 1
STT surface tension transfer 基于表面张力过渡技术的单面焊双面成形的焊接方法。
1
Q/SY1078—2010
3. 2
RMD regulated metal deposition 基于熔滴过渡控制技术的单面焊双面成形的焊接方法。
3.3
药芯焊丝flux-coredwire 将薄钢带制成圆形或异型钢管,同时在其中填满药粉,经拉制而成的一种细直径焊丝。外皮材料
可选用低碳钢等具有一定延展性的材料,药芯材料可根据产品用途选择各类金属、非金属粉末、矿物粉、化工产品,以及纳米材料等。药粉具有造气、造渣、脱氧和合金过渡等作用。根据焊接时是否需要保护气体分为自保护药芯焊丝和气保护药芯焊丝。 3.4
金属粉芯焊丝metalcorewire 将薄钢带制成圆形或异型钢管,同时在其中填满金属粉,经拉制而成的一种细直径焊丝。外皮材
料可选用低碳钢等具有延展性的材料,粉芯材料主要为铁粉和合金元素,具有提高熔敷效率和增加合金元素过渡的作用。焊接时需要保护气体。
4管材 4.1管道用钢管应符合下列标准要求:
—GB/T 9711. 1。 GB/T 9711. 2。 GB/T 8163。 API Spec 5L。
ASME锅炉及压力容器规范第Ⅱ卷材料A篇铁基材料标准。
4.2 常用钢管的化学成分和力学性能参见附录A。 5焊接材料 5.1 管道下向焊焊接材料应包括焊条、自保护药芯焊丝、实心焊丝和金属粉芯焊丝。 5.2焊条应符合GB/T5117,GB/T5118,AWSA5.1和AWSA5.5的规定。 5.3自保护药芯焊丝应符合GB/T17493和AWSA5.29的规定 5.4实心焊丝和金属粉芯焊丝应符合GB/T8110,AWSA5.18和AWSA5.28的规定。 5.5焊接材料的焊接工艺性能应满足全位置下向焊接工艺要求。 5.6焊接材料应参照附录B的要求选用;输气管道填充盖面应选用低氢型焊接材料。 5.7保护气体的纯度和配比应符合焊接工艺规程的要求。 5.8焊接材料应有产品合格证和质量证明书。 5.9焊接材料应避免受潮气、雨水、雪霜及油类等有害物质的侵蚀,焊接材料的保管应符合JB/T 3223的规定 5.10焊接材料应按说明书规定进行烘干;说明书规定不明确时,应按下列要求烘干:
a)低氢型下向焊条烘干温度为350℃~400℃,恒温时间为1h~2h。 b)纤维素型焊条不宜进行烘干,受潮后,纤维素型焊条烘干温度应为80℃~100℃,烘干时间
为0.5h~1h。纤维素型焊条不得二次烘干。 c)自保护药芯焊丝、金属粉芯焊丝和实心焊丝不应进行烘干。
5.11 经烘干的低氢下向焊条,应存放在温度为100℃~150℃的恒温箱内,随用随取, 5.12现场使用的低氢下向焊条,应存放在保温筒内。 5.13施工现场当天未用完的焊条应回收存放,低氢焊条重新烘干后应优先使用。重新烘干的次数不 2
Q/SY 1078—2010
得超过两次。 5.14药皮出现裂纹、脱落等影响焊接质量的下向焊条不得用于管道焊接。 5.15焊接材料的烘干、发放、回收应设专人负责,并做好详细的记录。
6焊接设备 6.1 管道下向焊应使用满足焊接工艺要求的焊接设备。 6.2焊接设备的性能应稳定,功率等参数应满足工程焊接要求。 6.3半自动根焊宜选用具有表面张力过渡、熔滴控制过渡等特殊功能的管道专用数字型焊接电源。 7焊接工艺评定 7.1焊接工艺评定应按设计文件规定执行。 7.2如设计文件对焊接工艺评定没有明确要求时,应按照SY/T4103,SY/T0452,APIStd1104 和ASME第IX卷等执行。 8焊接 8.1焊前准备 8.1.1管道下向焊接施工前,应根据焊接工艺评定制定下向焊接及缺陷返修工艺规程。 8.1.2参加管道施工的电焊工应持有有效的焊工资格证。必要时应在施工前进行试焊,合格后方可从事焊接工作。 8.1.3管道施工前应将坡口两侧油污、浮锈、水分、泥沙、气割后的熔渣、氧化皮等杂物以及坡口内侧机加工毛刺等打磨清理干净,内外坡口边缘不小于10mm范围内应露出金属光泽。 8.1.4管口组对尺寸应符合焊接工艺规程要求。 8.1.5沟上焊接时,管口处的作业空间高度不宜小于500mm;沟下焊接时,工作坑尺寸应能保证焊工操作和施工安全,每侧宜大于500mm。 8.2焊接施工 8.2.1在下列任何一种环境下进行焊接,应采取有效的防护措施,否则不得进行施焊。
a)雨天或雪天。 b)气体保护焊时风速超过2m/s,低氢型焊条焊接时风速超过5m/s,其他方法焊接时风速超过
8m/s. c)大气相对湿度超过90%。 d)环境温度低于焊接工艺规程中规定的温度。
8.2.2管口组对宜选用内对口器,在撤离内对口器前应完成100%根焊;若采用外对口器时,撤离外对口器前根焊应完成50%以上,且焊完的焊道应沿管周长均匀分布,但对口支撑或吊具则应在完成全部根焊道后撤除。 8.2.3施焊时,管子应保持稳定,不应移动,不应受到震动和冲击。 8.2.4焊接地线与钢管应有良好的接触,避免产生电弧灼伤母材。 8.2.5施焊时不得在坡口以外钢管表面引弧。 8.2.6根焊道焊完后,应尽快进行热焊道焊接,根焊道与热焊道间隔时间不宜超过10min。 8.2.7每层焊道宜连续焊完,中间不应中断,更换焊条应迅速,应在熔池未冷却前换完焊条继续焊接。必要时应使用角向磨光机打磨弧坑,再进行引弧。 8.2.8每道焊口宜连续焊完。若当日不能完成的焊口,应至少完成50%以上壁厚,且不少于3层。 重新焊接时,应预热至焊接工艺规程规定的温度。每个作业机组当日未完成焊口不应超过10道。 8.2.9全位置下向焊接应遵循薄层多遍焊道的原则,层间应仔细清除熔渣和飞溅物,对根焊及各填
3
Q/SY1078—2010
充焊道产生的凸起部分和接头高点也需进行必要的打磨,打磨不得伤及母材,焊工自检合格后方可焊下一层焊道, 8.2.10每相邻焊道接头应错开20mm以上。 8.2.11 施焊时焊条发红,该根焊条应予废弃 8.2.12 2管道下向焊施工宜采用流水作业。根焊的焊工数量和施焊顺序宜根据图1所示进行。
焊工甲
焊工乙
D≤406.4mm
a)
焊工甲
焊工乙
焊工甲
焊工乙
②
O
②
406.4mm
②
D≥1016mm
②
①
①
②
焊工丙 c)
b)
图 1 根焊的焊工数量和施焊顺序
8.2.13不同管壁厚度所需焊道层数,宜符合表1的规定。
表1 不同管壁厚度要求的焊层数
壁厚 mm 层数注1:焊道宽度不宜超过15mm。 注2:盖面焊接前,立焊位置填充量不足时宜进行立填焊。
12~15 5~7
17~21 7~10
6~8 3~4
8~10 4~5
10~12 5~6
15~17 6~9
21~26 8~12
4
Q/SY1078—2010
8.2.14 纤维素型焊条下向焊接工艺参数,宜符合表2规定的范围,
表2纤维素型焊条下向焊接工艺参数
电流 A 55~100 70~130 80~100 90~140 90~140
电压 V 20~36 20~36 25~37 25~37 20~35
焊条直径 mm 3. 2 4. 0 3. 2 4. 0 4. 0
焊接速度 cm/min 6~20 8~22 10~30 15~35 10~25
项 目
电流极性
直流正接或直流反接
根焊
热焊
直流反接
填充及盖面
直流反接
8.2.15 纤维素型焊条+低氢型焊条下向焊接工艺参数,宜符合表3规定的范围。
表3纤维素型焊条十低氢型焊条下向焊接工艺参数
焊条直径 mm 3. 2 4. 0 3. 2 4. 0 4. 0
电流 A 55~100 70~130 80~100 90~140 170~220
电压 V 20~36 20~36 25~37 25~37 19~28
焊接速度 cm/min 6~20 8~22 10~30 15~35 15~25
项 目
电流极性
直流正接或直流反接
根焊 (纤维素型焊条)
热焊(纤维素型焊条)
直流反接
填充焊及盖面(低氢型焊条)
直流反接
8.2.16 纤维素型焊条+自保护药芯焊丝下向焊焊接工艺参数, 宜符合表4规定的范围。
表4纟 纤维素型焊条十自保护药芯焊丝下向焊焊接工艺参数
送丝速度 m/min (in/min)
电流 A 55~100 20~36
电压 V
焊条/焊丝直径
焊接速度 cm/min 6~20
项 目
电流极性
mm
3. 2 4. 0 2. 0
根焊(纤维素型焊条)填充焊及盖面(自保护药芯焊丝)
直流正接或直流反接 70~130 20~36 8~22
1.78~3.30 (70~130)
180~260 16~21
直流正接
10~35
8.2.17 STT根焊+自保护药芯焊丝下向焊焊接工艺参数, 宜符合表5规定的范围。
表5STT根焊十自保护药芯焊丝下向焊焊接工艺参数
送丝速度 m/min (in/min)
焊丝直径 mm
电流 A 峰值电流
电流极性
电压 焊接速度 V
气体流量 L/min
项 目
cm/min
根焊 (STT)
反接 基值电流 14~18 20~25 3.30~4.06 正接 180~260 16~21 10~35 (70~130)
直流 350~450
1. 2
20~35
(130~160)
50~65
直流
填充焊及盖面(自保护药芯焊丝)注:保护气体为100%CO2,纯度≥99.5%, 含水量≤0.005%
1.78~3.30
2. 0
5