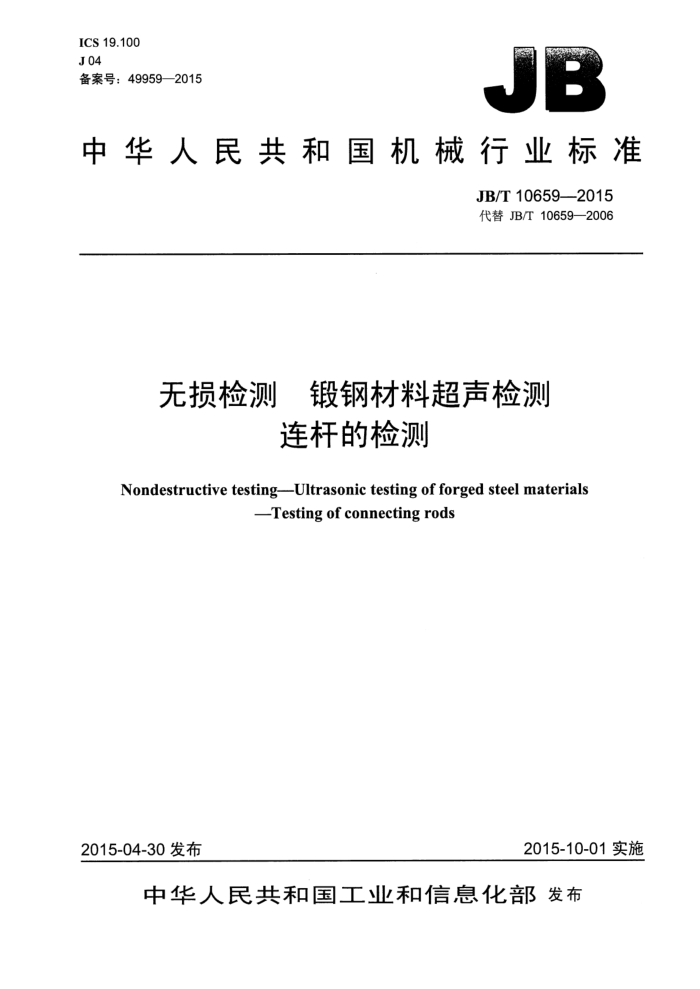
ICS 19.100 J04 备案号:49959—2015
中华人民共和国机械行业标准
JB/T10659—2015 代替JB/T10659—2006
无损检测 锻钢材料超声检测
连杆的检测
Nondestructive testing--Ultrasonic testing of forged steel materials
Testingofconnectingrods
2015-10-01实施
2015-04-30发布
中华人民共和国工业和信息化部发布
JB/T10659—2015
目 次
前言引言范围.
III IV
1 2规范性引用文件
3术语和定义 4连杆区域的划分 5 人员要求,
检测系统. 6.1 超声检测系统的性能 6.2 探头 6.3耦合剂. 7检测原则, 7.1 检测技术, 7.2 连杆原材料的检测 7.3 连杆的检测 8检测准备,
6
8.1 表面清理 8.2 检测环境. 8.3 表面粗糙度.. 9 超声检测灵敏度. 9.1 连杆原材料超声检测灵敏度 9.2 连杆超声检测灵敏度. 10检测. 10.1 检测时机, 10.2 连杆原材料(棒料)的超声检测 10.3 锻造连杆毛坏的超声检测 11质量分级, 11.1 缺陷的评定... 11.2连杆原材料质量分级. 11.3连杆原材料综合质量分级 11.4连杆质量分级... 11.5连杆综合质量分级 12检测报告附录A(规范性附录) 连杆原材料超声检测灵敏度试块 A.1 形状和尺寸 A.2 要求 A.3应用.. 附录B(资料性附录) 连杆原材料超声检测报告示例
E
10
JB/T10659—2015
附录C(资料性附录) 连杆超声检测报告示例
11
图1连杆区域划分示意图. 图2连杆I区杆身“工”字形部位的超声检测示意图图3连杆不同区域超声检测示意图图A.1LG-I型连杆原材料超声检测灵敏度试块,
J
S 9
表1超声检测连杆区域的划分表2连杆原材料质量分级表表3 3连杆质量分级表
6
II
JB/T10659—2015
前言
本标准按照GB/T1.1—2009给出的规则起草。 本标准代替JB/T10659—2006《无损检测 锻钢材料超声检测连杆的检测》,与JB/T10659一2006
相比主要技术变化如下:
修改了范围(见第1章,2006年版的第1章);修改了规范性引用文件(见第2章,2006年版的第2章);一修改了超声检测系统的性能(见7.3,2006年版的7.3);修改了莲杆超声检测灵敏度的表示方法(见9.2、11.4和表3);修改了图3说明(见图3,2006年版的图3);修改了LG-1型连杆原材料超声检测灵敏度试块(见附录A,2006年版的附录A)。
本标准由中国机械工业联合会提出本标准由全国无损检测标准化技术委员会(SAC/TC56)归口。 本标准起草单位:上海泰司检测科技有限公司、无锡市苏台工业检测技术研究所、上海材料研究所。 本标准主要起草人:孙岳宗、章怡明、金宇飞。 本标准所代替标准的历次版本发布情况为:
JB/T10659—2006。
III
JB/T10659—2015
引言
连接曲轴和气缸内活塞传递动力的部件称为连杆。连杆的大头孔套在曲轴的连杆轴颈上,连杆的小
头孔套在活塞内的活塞销上。曲轴每转动一周,在使连杆大头做一次圆周运动的同时,也便连杆小头带动活塞在气缸内做一次往复的直线运动。当曲轴高速运转时,连杆起到力的传递作用,同时也受到高频的交替拉伸力和压缩力的作用,其应力最集中部位为连杆的杆身部位,所以连杆杆身是最容易断裂的部位。一旦连杆断裂后发动机曲轴仍在运转,断裂后的连杆会打坏发动机的机体,将发生重大事故,因此加强连杆的无损检测是防止连杆断裂,保证发动机安全运行的一项十分重要的技术工作。
连杆是由钢材锻造而成的。连杆内部缺陷中的大部分是从锻造连杆的钢材(棒料)中带来的,而小部分是由锻造连杆的工艺不当造成的,为了防止连杆的断裂,对连杆的超声检测应分为两步:第一步,必须对锻造连杆的原材料(棒材)进行超声检测,不合格的原材料不能用来锻造连杆,这是一个基本原则:第二步,对锻成后的连杆逐根进行超声检测,合格连杆才能装配到发动机上。只有做好这两步检测工作,才能保证连杆的质量。
连杆的超声检测分为连杆大头、小头和杆身三部分,按不同的灵敏度分别进行超声检测。为了解决连杆杆身“工”字形,两横一竖部位及大、小头部位超声近场区干扰问题,在制定本标准的过程中,我们专门设计制造出一种专用超声探头,解决了连杆大、小头及杆身的超声检测问题。
由于连杆几何形状复杂,因此对连杆进行超声检测是一项技术水平要求较高的检测工作。要求检测
人员应通过连杆的超声检测专业培训,再经过连杆超声检测实践,能熟练掌握连杆的超声检测技能后才能在现场独立对连杆进行超声检测,以保证其检测结果的可靠性。
V
JB/T10659—2015
无损检测 锻钢材料超声检测
连杆的检测
1范围
本标准规定了锻钢材料制成的连杆的超声检测方法及质量分级。 本标准适用于发动机缸径在300mm以下连杆的超声检测,也适用于摩托车发动机连杆的超声检测。 GB/T5616规定的应用无损检测时应遵循的基本规则适用于本标准。
2规范性引用文件
下列文件对于本文件的应用是必不可少的。凡是注日期的引用文件,仅注日期的版本适用于本文件。 凡是不注日期的引用文件,其最新版本(包括所有的修改单)适用于本文件,
GB/T4162 锻轧钢棒超声检测方法 GB/T5616 无损检测应用导则 GB/T 9445 无损检测 人员资格鉴定与认证 GB/T12604.1 无损检测 术语超声检测 GB/T 18694 无损检测 超声检验探头及其声场的表征 GB/T18852 无损检测 超声检验测量接触探头声束特性的参考试块和方法 GB/T23908 无损检测 接触式超声脉冲回波直射检测方法 GB/T 23912 无损检测 液浸式超声纵波脉冲反射检测方法 JB/T 9214 无损检测 1A型脉冲反射式超声检测系统工作性能测试方法
3术语和定义
GB/T12604.1界定的术语和定义适用于本文件。
4连杆区域的划分
连杆分为I区、I区、IⅢI区三个部分,区域的划分按表1的规定,如图1所示。
表1超声检测连杆区域的划分
部位及范围杆身部分AD
区域 I区
图表的说明
a)AD=BC+2×0.1BC,单a为AD居中部位$2mm长横孔 b)B、C点为杆身与大小头圆弧的交点或切点 a)小头部分包括小头部分的各部位,$b为小头2mm长横孔 b)小头部分的计算长度为DE a)大头部分包括连杆盖的各部位,c为大头2mm长横孔 b)大头部分的计算长度为FA
II区
小头部分DE
III区
大头部分FA
-
JB/T10659—2015
切点或交点
I
图1连杆区域划分示意图
5人员要求
从事连杆超声检测的人员,应: a)按GB/T9445的要求进行资格鉴定与认证,并取得相应等级的证书; b)得到雇主或责任单位的工作授权,建议从事连杆超声检测人员在上岗之前,需要了解连杆的锻
造工艺、热处理工艺及加工工艺,并通过连杆超声检测专业技术培训,再经过500根连杆超声检测实践,考试合格,具备熟练的超声检测连杆操作技能后,才能在现场独立进行连杆的超声检测工作。
6检测系统 6.1 超声检测系统的性能
应按JB/T9214的规定进行系统性能测试,并符合下列要求:
水平线性偏差不大于1%;垂直线性偏差不大于5%: -动态范围不小于24dB;灵敏度余量不小于30dB(在CS-1型2mm×200mm平底孔试块上测得);
2
JB/T10659—2015
一衰减器范围不小于100dB。 6.2探头 6.2.1连杆超声检测探头为单晶片直探头、晶片直径为Φ14mm~Φ20mm,单晶片聚焦探头、晶片直径为=14mm~Φ18mm,斜探头、晶片尺寸为10mm×12mm,双晶片聚焦探头、晶片尺寸为6mm× 6mm或8mm×8mm 6.2.2单晶直探头、斜探头频率为2.5MHz;单晶片聚焦探头频率为5MHz 6.2.3单晶和双晶聚焦探头的会聚区范围应能满足检测连杆原材料和连杆缺陷深度的要求,且与被检测面有良好的配合。 6.2.4应按GB/T18694和GB/T18852的规定进行性能测试,其主声束偏移声轴方向不应大于1°。 6.2.5探头声场主声束不应出现双峰。 6.3耦合剂
接触式超声检测连杆视连杆表面粗糙度不同,可分别选用机油或化学糊(羧甲基纤维素的水溶液)做耦合剂。
7检测原则 7.1检测技术
可选用下列超声检测技术之一: a)接触式(见GB/T23908); b)液浸式(见GB/T23912)。
7.2连杆原材料的检测
为了确保锻造成形的连杆质量,应对锻造连杆的原材料进行超声检测。其检测方法可参照GB/T 4162的规定。若原材料内存在超过本标准中表2规定的缺陷,则此原材料就不适合用来锻造连杆。 7.3连杆的检测
由于连杆本身几何形状具有特殊性,故连杆的超声检测分为连杆杆身和连杆大、小头的检测,如图 3所示。若连杆中存在超过表3规定的缺陷,则此连杆评为不合格。
8检测准备
8.1表面清理 8.1.1原材料的表面清理。连杆原材料多为整根棒材,应在棒材表面的锈斑、毛刺、油污等全部清除、 打磨干净后才能进行超声检测。 8.1.2连杆的表面清理。应在连杆表面氧化皮锈斑、毛刺、油污等全部清理、打磨干净后才能进行超声检测。 8.2检测环境
检测现场应有水源、电源装置,无强磁场、振动、高温、灰尘和腐蚀气味,超声检测应在光线适中的环境中进行。
3