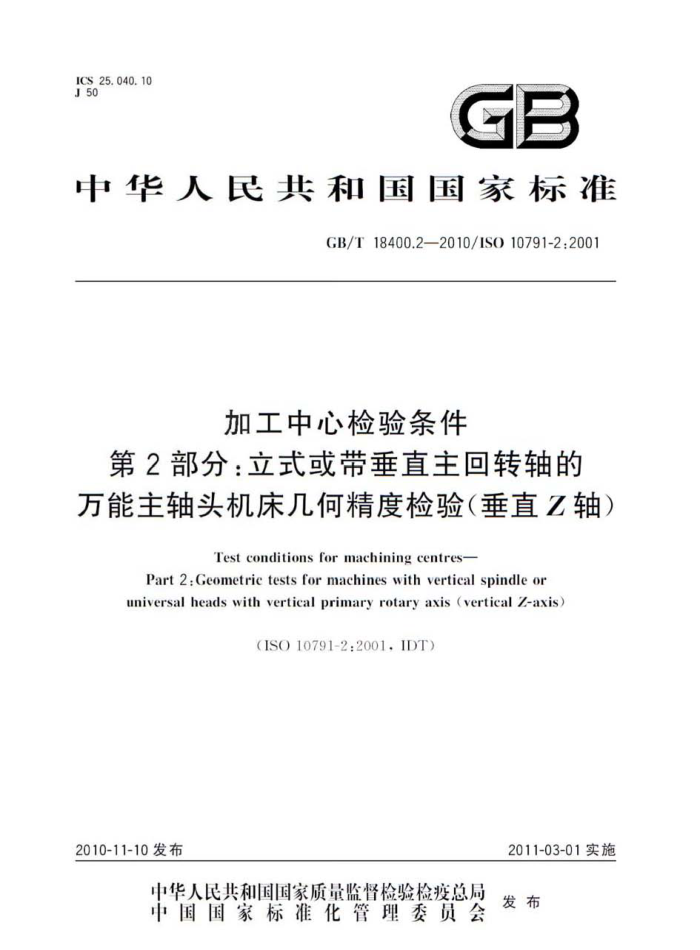
ICS25.040.10 J50
GB
中华人民共和国国家标准
GB/T18400.2-2010/IS010791-2:2001
加工中心检验条件
第2部分:立式或带垂直主回转轴的万能主轴头机床几何精度检验(垂直Z轴)
Test conditions for machining centres-
Part 2.Geometrie tests for machines with vertical spindle or universal heads with vertical primary rotary axis (vertical Z-axis)
(ISO10791-2:2001,IDT)
2011-03-01实施
2010-11-10发布
中华人民共和国国家质量监督检验检疫总局
中国国家标准化管理委员会 发布
GB/T18400.2—2010/ISO10791-2:2001
目 次
前言
范围规范性引用文件
I 2
3 般要求 3.1 测量单位 3.2 参照标准 3.3 检验顺序 3.4 检验项目 3.5 检验工具 3.6 简图 3.7 托板 3.8 软件补偿 3.9 机床结构 3.10 标志· 3.11 最小公差
儿何精度检验 4.1 线性运动的直线度 4.2线性运动的角度偏差 4.3 线性运动间的垂直度·· 4.4主轴· 4.5工作台或托板 4.6平行于Z轴线的附加轴线(W轴线)附录A(规范性附录) 任选水平轴附录B(规范性附录) 回转主轴头附录C《规范性附录) 回转摆动主轴头
N
11 14 19 2 25 31 33
GB/T18400.2—2010/ISO10791-2:2001
前言
GB/T18400《加工中心检验条件》分为以下十个部分:
第1部分:卧式和带附加主轴头机床几何精度检验(水平Z轴):第2部分:第2部分:立式或带垂直主回转轴的万能主轴头机床几何精度检验(垂直Z轴):
第3部分:带水平主回转轴的整体万能主轴头机床几何精度检验(垂直乙轴);
第4部分:线性和回转轴线的定位精度和重复定位精度检验:
一
第5部分:工件夹持托板的定位精度和重复定位精度检验:
第6部分:进给量、速度和插补精度检验:一第7部分:精加工试件精度检验;第8部分:三个坐标平面上轮廊特性的评定;一第9部分:刀具转换和托板转换动作时间的评定;
第10部分:热效应的评定。 本部分为GB/T18400的第2部分。 本部分等同采用ISO10791-2:2001《加工中心检验条件:第2部分:立式或带垂直主回转轴的万能
主轴头机床儿何精度检验(垂直Z轴)》(英文版)。
考虑到我国国情,在采用1S010791-2:2001时,本部分做了一些编辑性修改:
“本标准”一词改为”本部分”; - 第3章标题简要说明改为“一股要求”:一删除了ISO10791-2:2001的前言和引言,增加了国家标准的前言:
删除了ISO10791-2:2001的参考文献,
-
本部分的附录A、附录B和附录C为规范性附录。 本部分由中国机械工业联合会提出。 本部分由全国金属切削机床标准化技术委员会(SAC/TC22)归口本部分起草单位:北京机床研究所、北京第一机床厂、昆明机床股份有限公司、沈阳钻镗床研究所。 本部分主要起草人:李祥文、张维、胡瑞琳、唐其寿、许立亭
I
GB/T18400.2—2010/ISO10791-2:2001
加工中心检验条件
第2部分:立式或带垂直主回转轴的万能主轴头机床几何精度检验(垂直Z轴)
1.范围
GB/T18400的本部分规定了立式(即:垂直Z轴)加工中心(或数控铣床、数控镗床等)的儿何精度
检验。
本部分适用于基本上具有三个数控轴线.即三个线性轴线(X,Y和Z)至2000mm的立式加工中心,也适用于滑枕、套简或万能主轴头的附加运动,如:回转轴线(A、B、和C)
本部分在附录中列出了可能的附加任选水平轴和二种附加万能主轴头的检验项目:附录A:任选水平轴(检验项目AGI~AG6):一附录B:回转摇摆主轴头,具有一个数控回转轴线(检验项目BG1~BG2):一附录C:回转主轴头,具有相互垂直的两数控回转轴线(检验项目CG1~CG7)。 本部分仅适用于机床的儿何精度检验,不适用于机床的运动精度检验。通常情况下这两种检验是
分别进行的。在无负荷或精加工条件下机床的某些其他检验将包括在GB/T18400的其他部分中。 2规范性引用文件
下列文件中的条款通过GB/T18400的本部分的引用而成为本部分的条款。凡是注日期的引用文件,其随后所有的修改单(不包括勘误的内容)或修订版均不适用于本部分,然而,鼓励根据本部分达成协议的各方研究是否可使用这些文件的最新版本,凡是不注日期的引用文件,其最新版本适用手本部分。
GB/T17421.1一1998机床检验通则第1部分:在无负荷或精加工条件下机床的几何精度(eqV ISO230-1:1996)
ISO8526-1:1990机床通用部件随行托板第1部分:名义尺寸至800mm的工件随行托板 ISO8526-2:1990机床通用部件随行托板第2部分:名义尺寸大于800mm的工件随行托板
3一般要求 3.1测量单位
本部分中的所有线性尺寸,偏差和相应的公差的单位为毫米(mm):角度尺寸的单位为度(),角度
偏差和相应的公差用比值表示,但在某些情况下为了清晰,可用微弧度(urad)或角秒(")表示。表达式的等效关系如下:
0.010/1000=10×10-=10μrad~2
3.2参照标准
使用本部分时应参照GB/T17421.1一1998,尤其是机床检验前的安装,主轴和其他运动部件的升温,检验方法和检验工具的推荐精度。
在第4章和附录A至附录C的"检验方法”一栏中,其说明应符合该项检验参照的GB/T17421.1一 1998中相应章节的规定, 3.3检验顺序
本部分所列出的检验项目的顺序,并不表示实际的检验顺序,为了装拆检验工具和检验方便,可按
1
GB/T18400.2-2010/1S010791-2:2001
任意次序进行检验。 3.4检验项目
检验机床时,根据结构特点并不是必须检验本部分中的所有项目。为了验收目的而要求检验时,可由用户取得制造厂同意选择一些感兴趣的检验项目,但这些项目必须在机床订货时明确提出, 3.5检验工具
本部分所规定的检验工具仅为举例,可以使用相同指示量和至少具有相同精度的其他检验工具。 指示器应具有0.001mm的分辨率。 3.6简图
为简明起见,本部分的几何精度检验项目仅附一种结构形式的机床简图。 3.7托板
对于带有儿个托板工作的机床,涉及到托板的固有几何特性或与机床轴线有关的运行状态的检验(检验项目G15至G22),如果在机床订货协议中没有明确规定,仅对锁紧在工作位置上的任意一个代表性托板进行 3.8软件补偿
当软件设备可用来补偿某些检验项目偏差时,按用户和制造厂的协议,可在使用或不使用这些补偿的情况下进行相关项目的检验。当使用软件补偿时,应在检验项目中标明。 3.9机床结构
本部分中的机床按照它们的结构和沿线性轴线运动的部件.刻分为12种基本结构型式,这些结构型式分别用数字01至12标明,如图1所示,其结构型式分类见表1 3.10标志
本部分推荐用一种短代码的标志来表示机床的结构型式,这种标志由下列部分给定的顺序组成: a)“加工中心” b) 本部分标准编号: c) 字母“V"代表立式” d 图1中相应框图和表1序号栏内标明的数字。 示例:工作台沿X轴线运动,立柱沿Y轴线运动,主轴箱沿Z轴线运动的立式加工中心的标志为:
加工中心
型式 Vo7
GB/T18400.2
3.11最小公差
当实测长度与本部分规定的长度不同时,公差应根据GB/T17421.1一1998中2.3.1.1的规定,按能够测量的长度折算。折算结果小于0.005mm时,仍按0.005mm计
1)一些立式加工中心的结构型式与型式V10(龙门固定式)和型式V11(龙门移动式)类似,但只有一个立柱。
GB/T18400的本部分也适用于它们,在这种情况下,必要时应修改条文·用术语“立柱”代替“龙门”“摇臂”代替”横架”
2
GB/T18400.2—2010/ISO10791-2:2001
2
O
2
12
图1 机床结构型式图
GB/T18400.2—2010/ISO10791-2:2001
表1 立式加工中的结构型式分类
序号 01 02 03 04 .05 滑鞍上的立柱 06 07
x
X 滑鞍上的工作台
Y 工作台滑鞍工作台工作台滑鞍滑较上的工作台
Y
Z
Z 主轴箱主轴箱
立柱
滑鞍上的工作台工作台滑鞍
升降台
主轴箱主轴箱
立柱滑鞍主轴箱立柱滑鞍上的立柱
升降台工作台
升降台滑校
主轴箱主轴箱
立柱滑鞍
08 09 10
升降台
主轴箱横梁上的主轴箱滑板横梁上的主轴箱滑板横梁上的主轴箱
升降台滑鞍工作台
滑板上的主轴箱
龙门
11 12 主轴箱滑板
滑板上的主轴箱
升降台
4
GB/T18400.2-2010/IS010791-2:2001
4几何精度检验 4.1 线性运动的直线度检验项目
G1
X轴线运动的直线度: a)在ZX垂直平面内; b) 在XY水平面内。
简图
@
HO
b)
?
公差
a)和b) X500 0.010
500X<800 0.015 800
标
com
局部公差:在任意300测量长度上为0.007
检验工具
a)平尺 指示器或光学方法 b)平尺指示器或钢丝和显微镜或光学方法
检验方法(参照GB/T17421.11998的有关条文:5.2.1.1:5.2.35.2.3.1.2:5.2.3.2.1和5.2.3.3.1)
对所有结构型式的机床,平尺或钢丝或直线度反射器都应置于工作台上,如主轴能锁紧,则指示
器或显微镜或干涉仪可装在主轴上,否则检验工具应装在机床的主轴箱上。
测量线应尽可能靠近工作台的中央。
5