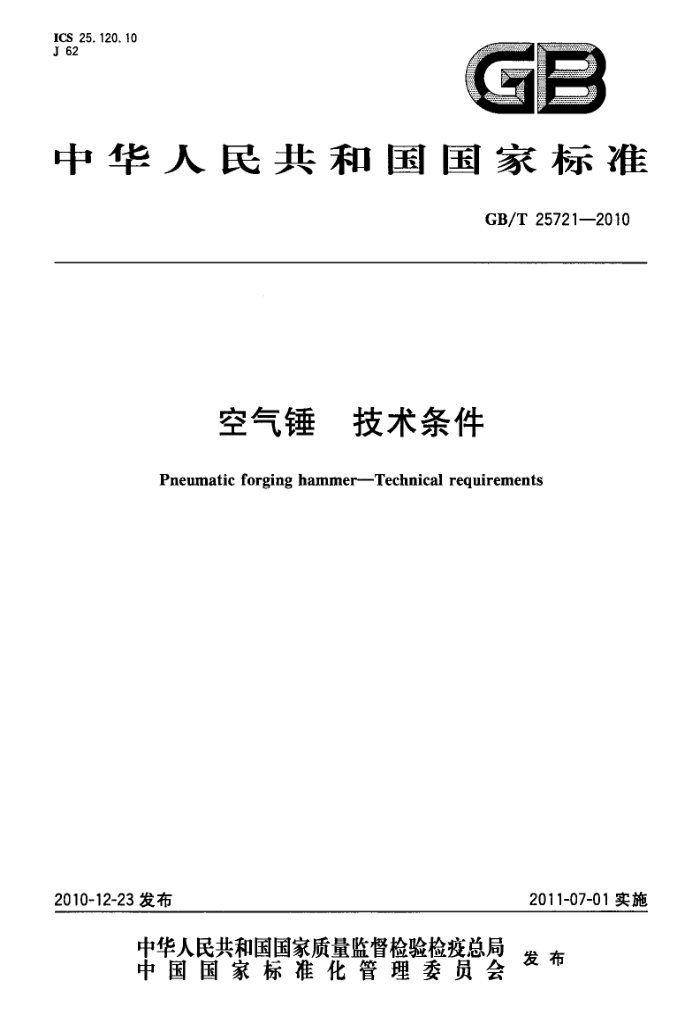
ICS 25.120.10 J 62
中华人民共和国国家标准
GB/T25721—2010
空气锤 技术条件
Pneumatic forging hammer--Technical reguirements
2010-12-23发布
2011-07-01实施
中华人民共和国国家质量监督检验检疫总局
中国国家标准化管理委员会 发布
GB/T 25721—2010
前言
本标准的附录A是规范性附录。 本标准由中国机械工业联合会提出。 本标准由全国锻压机械标准化技术委员会(SAC/TC220)归口。 本标准起草单位:安阳锻压机械工业有限公司、深圳市华测检测技术股份有限公司。 本标准主要起草人:王咏梅、韩涛、郭冰、周斌、范爱敏、华万红、孙华山、冯志刚、杨玉杰,
I
GB/T25721-—2010
空气锤技术条件
1 范围
本标准规定了空气锤的技术要求、试验方法、检验规则、标志、包装、运输和贮存。 本标准适用于热态金属自由锻造的空气锤。
2规范性引用文件
下列文件中的条款通过本标准的引用而成为本标准的条款。凡是注日期的引用文件,其随后所有的修改单(不包括勘误的内容)或修订版均不适用于本标准,然而,鼓励根据本标准达成协议的各方研究是否可使用这些文件的最新版本。凡是不注日期的引用文件,其最新版本适用于本标准。
GB/T191包装储运图示标志(GB/T191—2008,ISO780:1997,MOD) GB/T469—2005铅锭 GB/T1184—1996形状和位置公差末注公差值(eqvISO2768-2:1989) GB/T1801--2009产品几何技术规范(GPS)极限与配合公差带和配合的选择(ISO1829:
1975,MOD)
GB5226.1 机械电气安全机械电气设备第1部分:通用技术条件(GB5226.1一2008, IEC60204-1:2005,IDT)
GB/T9969工业产品使用说明书总则 GB/T13306 标牌 GB 17120 锻压机械 安全技术条件 GB/T23281 锻压机械噪声声压级测量方法(GB/T23281—2009,ISO11202:1995,NEQ) GB/T23282 锻压机械噪声声功率级测量方法(GB/T23282一2009,ISO3746:1995,NEQ) GB/T25720一2010空气锤型式与基本参数 JB/T1829 锻压机械通用技术条件 JB/T5775 锻压机械灰铸铁件技术条件 JB/T8356.1 机床包装技术条件 JB/T8609锻压机械焊接件技术条件 JB9973空气锤噪声限值
3技术要求
3.1基本要求 3.1.1空气锤应符合JB/T1829和本标准的规定,并按照经规定程序批准的图样及技术文件规定制造。 3.1.2 空气锤的安全与防护应符合GB17120的规定。 3.1.3铸铁件应符合JB/T5775的规定,焊接件应符合JB/T8609的规定。 3.1.4使用说明书应符合GB9969的规定。 3.1.5随机备件、附件应能互换,并应符合有关技术文件的规定。 3.2型式与基本参数
空气锤的型式和基本参数应符合GB/T25720的规定。用户有特殊要求的除外。
1
GB/T257212010
3.3性能 3.3.1落下部分质量的偏差应在规定的落下部分质量的0~10%之间。 3.3.2锤头实际打击频次的偏差(在锤头行程不小于工作空间高度3/4的条件下),不应超过额定打击频次的士5%。 3.3.3各种工作规范的操作应灵活可靠,提锤时应能上升至悬吊位置。锤头处于悬吊位置时,上砧底面不应露出导程端面。 3.4外观 3.4.1空气锤的外观质量应符合JB/T1829的规定。 3.4.2铸件外部表面清除型砂、粘砂、结疤、多肉以后,用500mm的直尺检查不加工表面的平面度,其误差不应大于2.5mm。 3.4.3外部不加工表面清除铁锈、型砂与油污后,应根据表面情况打底、抹腻子、涂漆。砧座及埋人件只涂防锈漆。铆焊件可不抹腻子。腻子层厚度不应大于1.5mm,局部加厚处不应大于3mm。涂漆应符合JB/T1829的规定。 3.4.4工作缸盖、压缩缸盖、气阀盖、分体结构的底座和气缸结合面的错偏量,不应超过表1的规定。
表 1
单位为毫米
零部件结合面的边缘尺寸
允许错偏盘
3 4 5
≤500 >500~1 250 >1 250~3 150
注:边缘尺寸指直径或相对应的边长。 3.5主要零件 3.5.1机身 3.5.1.1材料的主要机械性能指标为抗拉强度不低于200MPa,抗弯强度不低于400MPa,汽缸的硬度不低于表2的规定。
表 2
铸件主要壁厚/mm
硬度/HB 170 163
>15~50 >50
气缸内壁的加工要求不低于GB/T1801一2009中的9级公差,圆度公差值不应低于GB/T1184 1996中的9级,表面粗糙度不大于Ra1.6μm。 3.5.1.2气缸内壁不应有气孔、砂眼等影响工作性能的缺陷。 3.5.2锤杆 3.5.2.1材料的主要机械性能指标为届服点不低于360MPa,抗拉强度不低于610MPa,经热处理后硬度不低于220HB。 3.5.2.2锤杆导向平面和杆部外圆的加工要求不低于GB/T1801-2009中的9级公差,圆度公差不低于GB/T1184—1996中的9级,两导向平面的平面度不低于GB/T1184—1996中的7级,平行度不低于GB/T1184一1996中的7级,轴线的对称度不低于GB/T1184一1996中的9级,表面粗糙度不应大于Ral.6μm。 3.5.2.3燕尾槽底平面的平面度及对锤杆轴线的垂直度,均不低于GB/T1184一1996中的7级要求。 2
-
GB/T25721—2010
3.5.3压缩活塞 3.5.3.1材料的主要机械性能指标为抗拉强度不低于200MPa,抗弯强度不低于400MPa,其硬度值不低于表2的规定。 3.5.3.2活塞杆部外圆的加工要求不低于GB/T18012009中的9级公差。表面粗糙度不应大于 Ral.6μm。 3.5.4活塞环应符合有关技术文件的规定。 3.5.5上砧块和下砧块 3.5.5.1上、下砧块工作面的硬度应在40HRC~45HRC范围内。 3.5.5.2上、下砧块之上、下两平面的平行度不低于GB/T1184一1996中的6级。 3.5.5.3上、下砧块不应有锻造和热处理缺陷。 3.6装配 3.6.1对分体结构机身的气缸与底座经用烘装圈热装后(或用螺栓紧固后),其接触面之间的间隙不应大于0.05mm。若局部接触面之间的间隙大于0.05mm时,则用0.10mm的塞尺检查,插人深度不大于20mm,其累计长度不应超过接触面周长的10%。 3.6.2活塞环装人气缸后应与缸壁均匀接触,其不接触面在高度方向不应大于1/3,在圆周方向局部不接触长度不应大于周长的1/12,累计不应大于周长的1/4。活塞环与气缸壁内壁的间隙应符合表3的规定。
表 3
落下部分重量/kg
活塞环和气缸内壁的间隙/mm
250 >250
≤0.05 ≤0.10
3.6.3上砧楔铁打入后,局部不接触面积不大于10%,累计不接触面积不大于25%,或每25mm× 25mm面积内接触点不应小于6点。 3.6.4传动齿轮啮合应均匀,接触斑点在齿高方向上不应小于40%。在齿宽方向不应少于50%。 3.6.5啮合齿轮的轴向错位量不应超过表4的规定。
表4
单位为毫米
齿宽度B B≤100 B>100
轴向错位量 0. 05B
5
3.6.6操纵机构应灵活、轻便、准确。手柄操纵力不大于50N,脚踏杆操纵力不大于80N。 3.7电气设备
空气锤的电气设备应符合GB5226.1的规定。 3.8噪声
空气锤的噪声应符合JB9973的规定。测量方法应符合GB/T23281、GB/T23282的规定。 4 试验方法 4.1试验前的调整
在试验前应调整安装空气锤,下砧块工作面的水平度、上砧块与下砧块之间的间隙、气缸中心线对水平面的垂直度不应超过表5的规定。
3
GB/T25721—2010
表5
允差 mm
示意图
序号
调整项目
检验方法
按图示把框式水平仪放在下块工作面上, 在1000长
下砧块工作面的水平度
度上为0.1
调平下砧(下砧块、砧垫、砧座装在一起)
将上块落到已校平的下砧块工作面上,用塞尺测量接触面的间隙(如图)。误差以最大间隙值计
上块与下砧块之间的间隙
0. 1
将上块落到已校平的下砧块工作面上,用塞尺测量导板与锤杆两侧导向平面的最大及最小间隙,垂直度误差以最大及最小间隙之差值(如图)计。同样,再用塞尺测盘导程与锤杆两圆柱面的最大及最小间隙,应在与
气缸中心线对水平面的垂直度
实测平均间隙的2/3
塞尺
导板 导向平面成90°处测量(如图),垂直度误差
以最大及最小间隙之差值计
4.2试验条件
试验应在电压、润滑正常的条件下进行。 4.3运转试验 4.3.1运转试验时间不应少于2h。 4.3.2在运转试验时间内,锤头连续行程时间不应小于1.5h,且行程不小于工作空间高度3/4。 4.3.3试验时各部分应运转平稳,不应有不正常的尖叫声。 4.3.4运转试验应在正常的润滑条件下进行,润滑系统及接合面的密封处不应漏油漏气。 4.3.5运转试验结束时,工作缸和压缩缸的温度应从测试孔或润滑孔进行测量,最高温升不应超过 70℃. 4.3.6运转试验结束后,应进行提锤,连续打击,压锤三种工作规范的检查。检查操纵机构是否灵活、 轻便、准确。在进行上述检查时,手柄操纵力不大于50N,脚踏杆操纵力不大于80N。 4.3.7运转试验后,测量空气锤的噪声。 4.3.8连续(自动)打击时,轻打不应出现重打。 4.3.9运转试验结束后拆开缸盖,吊出锤杆及压缩活塞,检查缸壁、锤杆、活塞与活塞环,不应有拉伤和不正常的磨损等现象。 4.4打击能量试验 4.4.1用测量上砧块落下部分速度的方法确定锤的打击能量,应符合GB/T25720—2010中4.3的规定。 4.4.2亦可按附录A的规定确定锤的打击能量。 4.4.3打击能量不应小于公称打击能量。 5检验规则 5.1空气锤的检验分为出厂检验和型式检验。 x
GB/T25721--2010
5.2每台空气锤都应进行出厂检验。检验合格并填写产品合格证明书后才能出厂。 5.3对于新产品、更新产品(包括结构、主要零件、工艺有较大改变的产品),应进行型式检验。 5.4空气锤的出厂检验、型式检验应符合表6的规定。
表 6
检验类别出厂检验
技术要求
检验项目
检验方法
型式检验
+ + + + + + + + + - + 一
+ + + + + + + + + + + +
基本要求基本参数主要尺寸性能外观主要零件装配电气设备噪声声压级噪声声功率级运转试验打击能量试验
3. 1 3. 2 3. 2 3. 3 3. 4 3. 5 3. 6 3. 7 3. 8 3. 8 4. 3 4. 4
直接测量和检查直接测量直接测量直接测量目测和直接测量直接测量直接测量测量和检查按GB/T23281 按GB/T23282 按4.3 按4.4
注:“十”表示进行检验,“一”表示不进行检验。
6标志、包装、运输和贮存 6.1空气锤的各类标志和标牌应固定在锤身上明显的位置。 6.2标牌的型式与尺寸应符合GB/T13306的规定。在标牌上应注明:
a) 制造厂名称; b)产品名称; c)产品编号; d) 生产日期或出厂日期;
产品编号。
e
6.3空气锤包装应符合JB/T8356.1的有关规定。 6.4每台空气锤均应随机附带下列文件:
a)合格证明书; b)装箱单; c) 使用说明书。
6.5空气锤的包装应符合水路、陆路运输的规定,在运输时不应产生机械性损害;包装运输标志应符合 GB/T191的规定。
5
GB/T25721—2010
附录A (规范性附录)
以镦粗铅柱测定打击能量的方法
A.1铅柱材料应符合GB/T469一2005中的1号铅,其尺寸应符合表A.1的规定,一次锻击后铅柱的高度不应大于表A.1的规定。镦粗铅柱测定打击能量的试验示意图见图A.1。
表A.1
落下部分质量/kg 9 15 25 40 55 75 150 250 400 560 750 1 000 2 000 铅柱尺寸 直径d。 15 20 25 30 34 37 50 67 80 83 90 100 128
高度ho 25 30 37.5 45 50 55.5 75 85 100 125 135 150 192
mm 一次锻击后的铅柱高度hz/mm 打击能量/
16 18 23 26 27 32 43 50.2 59. 5 65. 5 67 73 96.5 90 160 270 530 700 1000 2500 5 600 9500 13700 19000 27 000 54 000
1
W
doh7
//0.05
240
(A
图A.1镦粗铅柱测定打击能量的试验示意图
A.2实际打击能量E,按式(A.1)计算。
E,=K·d.[2.7a+4(a"+at)]
(A.1)
式中: E——打击能量,单位为焦耳(J); d。—打击前铅柱直径,单位为毫米(mm); a=(h。一h)/ho h。—-打击前铅柱高度,单位为毫米(mm); h1- 一次打击后铅柱高度,单位为毫米(mm); K=0.01J/mm
6
ICS 25.120.10 J 62
中华人民共和国国家标准
GB/T25721—2010
空气锤 技术条件
Pneumatic forging hammer--Technical reguirements
2010-12-23发布
2011-07-01实施
中华人民共和国国家质量监督检验检疫总局
中国国家标准化管理委员会 发布
GB/T 25721—2010
前言
本标准的附录A是规范性附录。 本标准由中国机械工业联合会提出。 本标准由全国锻压机械标准化技术委员会(SAC/TC220)归口。 本标准起草单位:安阳锻压机械工业有限公司、深圳市华测检测技术股份有限公司。 本标准主要起草人:王咏梅、韩涛、郭冰、周斌、范爱敏、华万红、孙华山、冯志刚、杨玉杰,
I
GB/T25721-—2010
空气锤技术条件
1 范围
本标准规定了空气锤的技术要求、试验方法、检验规则、标志、包装、运输和贮存。 本标准适用于热态金属自由锻造的空气锤。
2规范性引用文件
下列文件中的条款通过本标准的引用而成为本标准的条款。凡是注日期的引用文件,其随后所有的修改单(不包括勘误的内容)或修订版均不适用于本标准,然而,鼓励根据本标准达成协议的各方研究是否可使用这些文件的最新版本。凡是不注日期的引用文件,其最新版本适用于本标准。
GB/T191包装储运图示标志(GB/T191—2008,ISO780:1997,MOD) GB/T469—2005铅锭 GB/T1184—1996形状和位置公差末注公差值(eqvISO2768-2:1989) GB/T1801--2009产品几何技术规范(GPS)极限与配合公差带和配合的选择(ISO1829:
1975,MOD)
GB5226.1 机械电气安全机械电气设备第1部分:通用技术条件(GB5226.1一2008, IEC60204-1:2005,IDT)
GB/T9969工业产品使用说明书总则 GB/T13306 标牌 GB 17120 锻压机械 安全技术条件 GB/T23281 锻压机械噪声声压级测量方法(GB/T23281—2009,ISO11202:1995,NEQ) GB/T23282 锻压机械噪声声功率级测量方法(GB/T23282一2009,ISO3746:1995,NEQ) GB/T25720一2010空气锤型式与基本参数 JB/T1829 锻压机械通用技术条件 JB/T5775 锻压机械灰铸铁件技术条件 JB/T8356.1 机床包装技术条件 JB/T8609锻压机械焊接件技术条件 JB9973空气锤噪声限值
3技术要求
3.1基本要求 3.1.1空气锤应符合JB/T1829和本标准的规定,并按照经规定程序批准的图样及技术文件规定制造。 3.1.2 空气锤的安全与防护应符合GB17120的规定。 3.1.3铸铁件应符合JB/T5775的规定,焊接件应符合JB/T8609的规定。 3.1.4使用说明书应符合GB9969的规定。 3.1.5随机备件、附件应能互换,并应符合有关技术文件的规定。 3.2型式与基本参数
空气锤的型式和基本参数应符合GB/T25720的规定。用户有特殊要求的除外。
1
GB/T257212010
3.3性能 3.3.1落下部分质量的偏差应在规定的落下部分质量的0~10%之间。 3.3.2锤头实际打击频次的偏差(在锤头行程不小于工作空间高度3/4的条件下),不应超过额定打击频次的士5%。 3.3.3各种工作规范的操作应灵活可靠,提锤时应能上升至悬吊位置。锤头处于悬吊位置时,上砧底面不应露出导程端面。 3.4外观 3.4.1空气锤的外观质量应符合JB/T1829的规定。 3.4.2铸件外部表面清除型砂、粘砂、结疤、多肉以后,用500mm的直尺检查不加工表面的平面度,其误差不应大于2.5mm。 3.4.3外部不加工表面清除铁锈、型砂与油污后,应根据表面情况打底、抹腻子、涂漆。砧座及埋人件只涂防锈漆。铆焊件可不抹腻子。腻子层厚度不应大于1.5mm,局部加厚处不应大于3mm。涂漆应符合JB/T1829的规定。 3.4.4工作缸盖、压缩缸盖、气阀盖、分体结构的底座和气缸结合面的错偏量,不应超过表1的规定。
表 1
单位为毫米
零部件结合面的边缘尺寸
允许错偏盘
3 4 5
≤500 >500~1 250 >1 250~3 150
注:边缘尺寸指直径或相对应的边长。 3.5主要零件 3.5.1机身 3.5.1.1材料的主要机械性能指标为抗拉强度不低于200MPa,抗弯强度不低于400MPa,汽缸的硬度不低于表2的规定。
表 2
铸件主要壁厚/mm
硬度/HB 170 163
>15~50 >50
气缸内壁的加工要求不低于GB/T1801一2009中的9级公差,圆度公差值不应低于GB/T1184 1996中的9级,表面粗糙度不大于Ra1.6μm。 3.5.1.2气缸内壁不应有气孔、砂眼等影响工作性能的缺陷。 3.5.2锤杆 3.5.2.1材料的主要机械性能指标为届服点不低于360MPa,抗拉强度不低于610MPa,经热处理后硬度不低于220HB。 3.5.2.2锤杆导向平面和杆部外圆的加工要求不低于GB/T1801-2009中的9级公差,圆度公差不低于GB/T1184—1996中的9级,两导向平面的平面度不低于GB/T1184—1996中的7级,平行度不低于GB/T1184一1996中的7级,轴线的对称度不低于GB/T1184一1996中的9级,表面粗糙度不应大于Ral.6μm。 3.5.2.3燕尾槽底平面的平面度及对锤杆轴线的垂直度,均不低于GB/T1184一1996中的7级要求。 2
-
GB/T25721—2010
3.5.3压缩活塞 3.5.3.1材料的主要机械性能指标为抗拉强度不低于200MPa,抗弯强度不低于400MPa,其硬度值不低于表2的规定。 3.5.3.2活塞杆部外圆的加工要求不低于GB/T18012009中的9级公差。表面粗糙度不应大于 Ral.6μm。 3.5.4活塞环应符合有关技术文件的规定。 3.5.5上砧块和下砧块 3.5.5.1上、下砧块工作面的硬度应在40HRC~45HRC范围内。 3.5.5.2上、下砧块之上、下两平面的平行度不低于GB/T1184一1996中的6级。 3.5.5.3上、下砧块不应有锻造和热处理缺陷。 3.6装配 3.6.1对分体结构机身的气缸与底座经用烘装圈热装后(或用螺栓紧固后),其接触面之间的间隙不应大于0.05mm。若局部接触面之间的间隙大于0.05mm时,则用0.10mm的塞尺检查,插人深度不大于20mm,其累计长度不应超过接触面周长的10%。 3.6.2活塞环装人气缸后应与缸壁均匀接触,其不接触面在高度方向不应大于1/3,在圆周方向局部不接触长度不应大于周长的1/12,累计不应大于周长的1/4。活塞环与气缸壁内壁的间隙应符合表3的规定。
表 3
落下部分重量/kg
活塞环和气缸内壁的间隙/mm
250 >250
≤0.05 ≤0.10
3.6.3上砧楔铁打入后,局部不接触面积不大于10%,累计不接触面积不大于25%,或每25mm× 25mm面积内接触点不应小于6点。 3.6.4传动齿轮啮合应均匀,接触斑点在齿高方向上不应小于40%。在齿宽方向不应少于50%。 3.6.5啮合齿轮的轴向错位量不应超过表4的规定。
表4
单位为毫米
齿宽度B B≤100 B>100
轴向错位量 0. 05B
5
3.6.6操纵机构应灵活、轻便、准确。手柄操纵力不大于50N,脚踏杆操纵力不大于80N。 3.7电气设备
空气锤的电气设备应符合GB5226.1的规定。 3.8噪声
空气锤的噪声应符合JB9973的规定。测量方法应符合GB/T23281、GB/T23282的规定。 4 试验方法 4.1试验前的调整
在试验前应调整安装空气锤,下砧块工作面的水平度、上砧块与下砧块之间的间隙、气缸中心线对水平面的垂直度不应超过表5的规定。
3
GB/T25721—2010
表5
允差 mm
示意图
序号
调整项目
检验方法
按图示把框式水平仪放在下块工作面上, 在1000长
下砧块工作面的水平度
度上为0.1
调平下砧(下砧块、砧垫、砧座装在一起)
将上块落到已校平的下砧块工作面上,用塞尺测量接触面的间隙(如图)。误差以最大间隙值计
上块与下砧块之间的间隙
0. 1
将上块落到已校平的下砧块工作面上,用塞尺测量导板与锤杆两侧导向平面的最大及最小间隙,垂直度误差以最大及最小间隙之差值(如图)计。同样,再用塞尺测盘导程与锤杆两圆柱面的最大及最小间隙,应在与
气缸中心线对水平面的垂直度
实测平均间隙的2/3
塞尺
导板 导向平面成90°处测量(如图),垂直度误差
以最大及最小间隙之差值计
4.2试验条件
试验应在电压、润滑正常的条件下进行。 4.3运转试验 4.3.1运转试验时间不应少于2h。 4.3.2在运转试验时间内,锤头连续行程时间不应小于1.5h,且行程不小于工作空间高度3/4。 4.3.3试验时各部分应运转平稳,不应有不正常的尖叫声。 4.3.4运转试验应在正常的润滑条件下进行,润滑系统及接合面的密封处不应漏油漏气。 4.3.5运转试验结束时,工作缸和压缩缸的温度应从测试孔或润滑孔进行测量,最高温升不应超过 70℃. 4.3.6运转试验结束后,应进行提锤,连续打击,压锤三种工作规范的检查。检查操纵机构是否灵活、 轻便、准确。在进行上述检查时,手柄操纵力不大于50N,脚踏杆操纵力不大于80N。 4.3.7运转试验后,测量空气锤的噪声。 4.3.8连续(自动)打击时,轻打不应出现重打。 4.3.9运转试验结束后拆开缸盖,吊出锤杆及压缩活塞,检查缸壁、锤杆、活塞与活塞环,不应有拉伤和不正常的磨损等现象。 4.4打击能量试验 4.4.1用测量上砧块落下部分速度的方法确定锤的打击能量,应符合GB/T25720—2010中4.3的规定。 4.4.2亦可按附录A的规定确定锤的打击能量。 4.4.3打击能量不应小于公称打击能量。 5检验规则 5.1空气锤的检验分为出厂检验和型式检验。 x
GB/T25721--2010
5.2每台空气锤都应进行出厂检验。检验合格并填写产品合格证明书后才能出厂。 5.3对于新产品、更新产品(包括结构、主要零件、工艺有较大改变的产品),应进行型式检验。 5.4空气锤的出厂检验、型式检验应符合表6的规定。
表 6
检验类别出厂检验
技术要求
检验项目
检验方法
型式检验
+ + + + + + + + + - + 一
+ + + + + + + + + + + +
基本要求基本参数主要尺寸性能外观主要零件装配电气设备噪声声压级噪声声功率级运转试验打击能量试验
3. 1 3. 2 3. 2 3. 3 3. 4 3. 5 3. 6 3. 7 3. 8 3. 8 4. 3 4. 4
直接测量和检查直接测量直接测量直接测量目测和直接测量直接测量直接测量测量和检查按GB/T23281 按GB/T23282 按4.3 按4.4
注:“十”表示进行检验,“一”表示不进行检验。
6标志、包装、运输和贮存 6.1空气锤的各类标志和标牌应固定在锤身上明显的位置。 6.2标牌的型式与尺寸应符合GB/T13306的规定。在标牌上应注明:
a) 制造厂名称; b)产品名称; c)产品编号; d) 生产日期或出厂日期;
产品编号。
e
6.3空气锤包装应符合JB/T8356.1的有关规定。 6.4每台空气锤均应随机附带下列文件:
a)合格证明书; b)装箱单; c) 使用说明书。
6.5空气锤的包装应符合水路、陆路运输的规定,在运输时不应产生机械性损害;包装运输标志应符合 GB/T191的规定。
5
GB/T25721—2010
附录A (规范性附录)
以镦粗铅柱测定打击能量的方法
A.1铅柱材料应符合GB/T469一2005中的1号铅,其尺寸应符合表A.1的规定,一次锻击后铅柱的高度不应大于表A.1的规定。镦粗铅柱测定打击能量的试验示意图见图A.1。
表A.1
落下部分质量/kg 9 15 25 40 55 75 150 250 400 560 750 1 000 2 000 铅柱尺寸 直径d。 15 20 25 30 34 37 50 67 80 83 90 100 128
高度ho 25 30 37.5 45 50 55.5 75 85 100 125 135 150 192
mm 一次锻击后的铅柱高度hz/mm 打击能量/
16 18 23 26 27 32 43 50.2 59. 5 65. 5 67 73 96.5 90 160 270 530 700 1000 2500 5 600 9500 13700 19000 27 000 54 000
1
W
doh7
//0.05
240
(A
图A.1镦粗铅柱测定打击能量的试验示意图
A.2实际打击能量E,按式(A.1)计算。
E,=K·d.[2.7a+4(a"+at)]
(A.1)
式中: E——打击能量,单位为焦耳(J); d。—打击前铅柱直径,单位为毫米(mm); a=(h。一h)/ho h。—-打击前铅柱高度,单位为毫米(mm); h1- 一次打击后铅柱高度,单位为毫米(mm); K=0.01J/mm
6