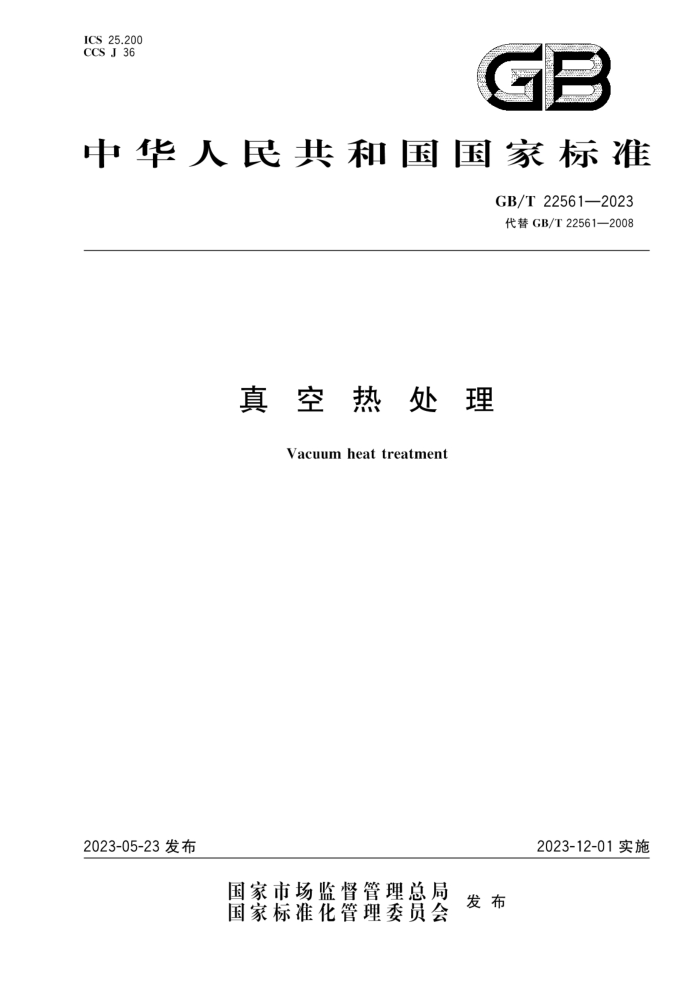
ICS25.200 CCS J 36
GB
中华人民共和国国家标准
GB/T22561—2023 代替GB/T22561—2008
真空热处理
Vacuum heat treatment
2023-12-01实施
2023-05-23发布
国家市场监督管理总局 发布
国家标准化管理委员会
GB/T22561—2023
目 次
前言 1 范围 2 规范性引用文件术语和定义
3
工艺分类及代号 5 设备技术要求
4
.
工艺过程与工艺规范质量控制与检验安全、卫生与环保· 能源消耗
6
8 9 10 人员要求
11 产品记录与报告单· 附录A(资料性) 常用金属材料真空热处理时的最大允许压升率附录B(资料性) 常用金属材料在真空下可以相互接触不黏合的最高允许温度附录C(资料性) 常用金属材料真空热处理参考数据附录D(资料性) 加热滞后时间的测定方法
L0
12
GB/T 22561—2023
前言
本文件按照GB/T1.1一2020《标准化工作导则第1部分:标准化文件的结构和起草规则》的规定
起草。
本文件代替GB/T22561一2008《真空热处理》,与GB/T22561一2008相比,除结构调整和编辑性
改动外,主要技术变化如下:
a)增加了“真空工作压强”“淬火转移时间”术语(见3.4、3.6),删除了“真空腐蚀”术语(见2008年
版的3.4); b) 更改了对真空加热室(见5.1.1,2008年版的5.1.1)、压升率测量(见5.1.5,2008年版的5.1.6)、
真空炉工作容积(见5.1.3,2008年版的5.1.4)和“温度测量”“温度均勾性及系统准确度测定” 的要求(见5.1.6,2008年版的5.1.7,5.1.8):
c) 更改了对真空气淬炉的要求(见5.1.11,2008年版的5.1.12),增加了对真空检测仪校准(见
5.1.4)、超载(超重)报警(见5.1.13)和淬火转移时间的要求(见5.1.14); d) 更改了对工装夹具(见6.1.3,2008年版的6.1.2.2)、真空压强(见6.2.2,2008年版的6.3.2)、工
件分段预热方法(见6.2.3,2008年版的6.3.3)、冷却介质(见6.4.1,2008年版的5.3)、气淬(见 6.4.3,2008年版的6.5.2)及出炉和清理的要求(见6.5,2008年版的6.6);
e)增加了工件热处理工艺规范(见6.14)和水率冷却的要求(见6.4.4),更改了工件最大截面厚度
或直径(见6.3.4,2008年版的6.4.5),删除了真空退火加热保温时间(见2008年版的6.4.4); f) 更改了质量控制和检验的要求(见第7章,2008年版的第7章); g) 更改了对能耗的要求(见9.2,2008年版的5.1.2); h)增加了人员要求(见第10章)。 本文件由全国热处理标准化技术委员会(SAC/TC75)提出并归口。 本文件起草单位:上海材料研究所有限公司、滁州华海中谊工业炉有限公司、江苏丰东热技术有限
公司、中航长城计量测试(天津)有限公司、北京航天新立科技有限公司、奇精机械股份有限公司、中国机械总院集团北京机电研究所有限公司、北京北方华创真空技术有限公司、北京华立精细化工公司、上海市轴承技术研究所有限公司、湖北三环锻造有限公司、北京星航机电装备有限公司、浙江国检检测技术股份有限公司、株洲中车天力锻业有限公司、天津市热处理研究所有限公司、常州新区河海热处理工程有限公司、西安福莱特热处理有限公司。
本文件主要起草人:卢军、徐跃明、李俏、胡东彪、韩伯群、吕国义、孙晓哲、汪守丰、刘双林、葛圣东、 黄雄荣、刘宏扬、田伟智、黄俊杰、姜影、高新宇、殷和平、杨祯、束东方、苏行、王宝平。
本文件于2008年首次发布,本次为第一次修订。
II
GB/T22561—2023
真空热处理
1范围
本文件规定了金属材料在真空状态下热处理设备、工艺过程与工艺规范、质量控制与检验、安全卫生与环保、能源消耗、人员要求、产品记录与报告等要求。
本文件适用于合金结构钢、工具钢、模具钢、不锈钢、耐热钢、钛合金、高温合金、难熔金属合金及精密合金等材料的真空热处理,包括真空淬火、真空回火、真空退火、真空固溶处理及时效等工艺。
本文件不适用于真空渗碳和真空渗氮等工艺
2 规范性引用文件
下列文件中的内容通过文中的规范性引用而构成本文件必不可少的条款。其中,注日期的引用文
件,仅该日期对应的版本适用于本文件;不注期的引用文件,其最新版本(包括所有的修改单)适用于本文件。
GB 3095 5环境空气质量标准 GB/T7232金属热处理术语 GB/T10066.1 电热和电磁处理装置的试验方法第1部分:通用部分 GB/T10067.1 电热和电磁处理装置基本技术条件第1部分:通用部分 GB/T10067.4 电热装置基本技术条件第4部分:间接电阻炉 GB/T10067.45电热装置基本技术条件第45部分:真空淬火炉 GB/T 10067.47 电热装置基本技术条件第47部分:真空热处理和钎焊炉 GB/T 12603 金属热处理工艺分类及代号 GB 15735 金属热处理生产过程安全、卫生要求 GB/T 17358 热处理生产电耗计算和测定方法 GB/T 19944 热处理生产燃料消耗计算和测定方法 GB/T 24487 氧化铝 GB/T 30823 测定工业火油冷却性能的镍合金探头试验方法 GB/T 30825 热处理温度测量 GB/T 32541 热处理质量控制体系 GB/T 34895 热处理金相检验通则 GB/T 38751 热处理件硬度检验通则 GB/T 38819 绿色热处理技术要求及评价 JB/T7530 热处理用氩气、氮气、氢气一般技术条件 JB/T11810 真空高压气率炉热处理技术要求 JB/T13026 热处理用油基淬火介质
3 :术语和定义
GB/T7232界定的以及下列术语和定义适用于本文件。
1
GB/T225612023
3.1
真空压强 vacuum pressure 真空状态下,用稀薄气体的压强表示的真空程度。 注:单位为帕(Pa)。
3.2
脱气 outgassing 在真空条件下,材料自然排放出气体或蒸汽。
3.3
加热滞后时间 heatinglagtime 真空加热条件下,真空炉内热电偶到达工艺设定温度与工件或试样心部热电偶到达工艺设定的下
限温度的时间差。 3.4
真空工作压强 working vacuumpressure 材料(工件)允许开始加热时的真空压强。
3.5
分压 partialpressure 真空气氛中任一气体组分的实际压强。 注:在真空热处理中,通常是指向炉内回充情性气体的压强。
3.6
淬火转移时间 quenching transfer time 材料(工件)从加热室取出至完全进人淬火介质中的时间。
工艺分类及代号
4
真空热处理工艺分类及代号应符合GB/T12603的规定,见表1。
表1 真空热处理工艺分类及代号
代号 500-02 511-02 513-02 514-02 517-02 518-02
工艺分类真空热处理真空退火真空加热火真空淬火回火真空固溶处理
真空固溶处理十时效
5 设备技术要求
5.1 真空加热设备 5.1.1 真空加热设备应符合GB/T10067.1、GB/T10067.4、GB/T10067.45及GB/T10067.47规定的技术条件。加热室内结构材料在热处理过程中不应与工件或介质气体发生反应。加热室在设计有惰性气体高压气淬功能时,应设置合理的超压排气装置。 2
GB/T22561—2023
5.1.2真空系统应有足够的抽气能力并保证密封性,同时应严格控制分压气体流量和保持规定分压压力,满足工艺要求的真空水平。 5.1.3在空炉、干燥、除气的情况下,不同工作容积的真空炉应在表2规定的时间内抽到规定的真空工作压强。
表2真空炉空炉抽到规定真空工作压强时间
真空炉工作容积/m
抽到规定真空工作压强时间/min
>0.5~<1.0 ≥1.0~<5.0
20 ≤40 ≤60
≥5.0
5.1.4真空炉应配备真空压强指示、记录及自动控制装置。不同的真空压强区间宜配置不同的真空检测仪。真空检测仪应每3个月校准1次,特殊情况下应增加校准次数。真空检测仪的校准应按规定执行。 5.1.5真空炉在冷态空载充分干燥后的压升率应小于0.67Pa/h,测量方法按GB/T10066.1的规定执行。真空炉工作期间每周至少测量一次压升率。测量时真空压强到达正在执行工艺的初始真空压强设定值后,关闭真空炉的所有阀门,记录第一次真空压强,过15min后记录第二次真空压强,两次真空压强的差除以记录的间隔时间作为该真空炉的压升率。常用金属材料真空热处理允许的最大压升率见附录A。 5.1.6真空炉的温度测量应按GB/T30825的规定进行,温度均匀性及系统准确度测定周期应符合 GB/T32541的要求。 5.1.7真空炉炉壳的表面温升不应大于30℃。 5.1.8为准确控制工件温度,可使用一支或多支载荷热电偶。热电偶尽可能与工件接触。热电偶若与工件材料发生反应则应加护套。热电偶插入工件的深度应为热电偶直径的10倍以上,并与孔底部的表面紧密接触。 5.1.9真空炉的加热电极在通水冷却情况下,对地绝缘电阻应大于1kQ。 5.1.10真空炉冷却水进水口的压力应大于0.25MPa,流量可调节,并配有断水报警保护装置。冷却水进水口的水温为5℃~35℃,出水口的温升不应超过20℃(气淬时允许短时超温),快速冷却时冷却水压应大于0.3MPa。 5.1.11真空气炉应配有足够容积的贮气罐,并带有快速充气装置、气风扇及热交换系统,且有相应的减压阀和压力表,能准确指示及调节冷却气体压强,满足JB/T11810的要求。 5.1.12真空回火炉应带有热风搅拌或对流加热系统和快冷装置。 5.1.13真空油(水、气)淬炉应配备超载(超重)报警装置。 5.1.14真空油淬炉和真空水淬炉的工件淬火转移时间一般小于20s。对于大型真空炉和特殊材料的真空热处理,其淬火转移时间应根据工艺的技术要求协商确定。
5.2淬火冷却装置 5.2.1真空炉应根据需要配置容积足够大的油槽(水槽)及贮气罐,以保证连续淬火条件下有足够的冷却能力。 5.2.2油槽和水槽均应配有加热、冷却、控温、超温报警及搅拌装置,温控仪表的允许偏差应在土5℃范围内。 5.2.3油槽和水槽应设置液面下限和上限位置的报警装置,油槽和水槽的搅拌应设置故障报警装置。
3
GB/T 22561—2023
6工艺过程与工艺规范
6.1热处理前的准备 6.1.1应对真空炉进行常规检查,保证处于正常工作状态。对需处理钛合金的真空炉,若先前处理过非钛合金,应采用高温加热等方法清洁炉膛。 6.1.2人炉工件及工装夹具装炉前应进行清洗和烘干,不应有锈斑和对工件及炉膛产生有害影响的污物、低熔点涂层及镀层等。 6.1.3应防止夹具和工装在生产过程中与工件发生反应或黏合,材料在真空下可以相互接触不黏合的最高允许温度见附录B。为避免发生反应,可采用氧化铝块(板或棒)或氧化铝粉隔离。氧化铝粉的化学成分及性能应符合GB/T24487的规定, 6.1.4应根据不同工件的技术要求编制相应的真空热处理工艺规范。常用材料的真空热处理工艺参数见附录C。 6.2加热 6.2.1工件应放置在真空炉炉膛的有效加热区内,保证工件加热均匀。加热室的真空压强小于6.67Pa 时方可加热升温。升温过程中需注意工件脱气,若因脱气使真空压强高于临界值时,应停止加热并调节升温速度。 6.2.2应根据工件材料及工艺的要求,确定并控制加热温度和加热时的真空压强,该真空压强的控制可通过回充氮气或氩气调节分压而实施。真空炉回充的氮气或氩气应符合6.4.1.1的规定。 6.2.3工件达到设定加热温度之前需进行分段预热,分段预热方法参见表C.2。 6.2.4工件真空回火时,当炉内达到一定的真空压强(小于或等于0.133Pa)时,应向炉内通人高纯氮气到6.6×10*Pa~2.0×105Pa,并通过风扇循环保持此炉压直至结束。 6.2.5工件真空退火时,需避免因真空压强过低而产生表面合金元素挥发。 6.3 保温时间 6.3.1工件真空热处理时的加热保温时间需考虑工件加热时的滞后效应,加热滞后时间的确定可参考附录D。 6.3.2真空加热保温时间应包括加热滞后时间和组织均匀化时间 6.3.3真空回火加热保温时间不应少于2h。 6.3.4真空除氢时间应根据工件最大截面厚度或直径确定,真空除氢时间见表3。
表3真空除氢时间
时间/h 1~2 >2~3 >3
工件最大截面厚度或直径/mm
≤20 >20~<50 ≥50
6.4冷却 6.4.1冷却介质 6.4.1.1J 真空炉冷却用气应符合JB/T7530的规定。对合金钢一般采用99.995%纯度的氮气,对高温
4
GB/T 22561—2023
合金一般采用99.999%纯度的氩气,对钛合金应采用99.999%纯度的氩气。 6.4.1.2淬火油应符合JB/T13026中相关技术要求,满足工件真空淬火后的硬度及光亮度的要求。 6.4.1.3氢气不应作为钛和钛合金淬火冷却介质和分压气体。氮气作为分压气体应根据处理工件的材质来确定。 6.4.1.4应定期检测淬火油、水的冷却能力,检测方法按GB/T30823的规定执行。 6.4.2油淬
真空淬火油在淬火前应充分脱气并排除水分,必要时适当加热,将油温控制在20℃~100℃以内。 为控制油面压强,淬火时应充高纯氮气或氩气,一般控制在5X101Pa左右。淬火时,油槽内应进行搅拌。 6.4.3气淬
根据工艺要求,可采用正压气淬或负压气。正压气率时根据材料的淬透性通人1.5×105Pa~ 20×105Pa的高纯氮气或氩气;负压气时通人7.9×10*Pa~9.3×10Pa的高纯氮气或氩气进行淬火。高速钢和高合金模具钢工件宜采用正压气淬方法,钛合金应采用高纯氩气淬火
根据工艺要求,高速钢和模具钢等工件宜通过控制情性气体的流量、压强和风速进行分级萍火,以
减小被处理件的畸变量。 6.4.4水淬
真空水时需避免水蒸气对加热室的污染,工件转移速度应符合工艺要求,水温应控制在30℃以下。为控制水面压强,淬火时应充气(高纯氮气或氩气),一般控制在1.013×10°Pa左右。淬火时,水槽内应进行搅拌。 6.4.5气冷
工件进行真空回火时,回火加热结束后应根据工艺要求采用情性气体冷却。
6.4.6炉冷
按工艺规定随炉冷却(如退火等)时,冷却过程应保持一定的真空压强,当炉温降至一定温度后方可停止抽真空。 6.5出炉及清理
工件应冷却至低于65℃后出炉。对于真空油率,应排清预备室(冷却室)中的油气后方可充气和出
炉。油工件出炉后应进行去油清理。
7质量控制与检验
7.1外观 7.1.1真空热处理后的工件表面应光亮、无机械损伤 7.1.2真空热处理后的工件表面不应出现合金贫化或氧化。 7.2畸变 7.2.1真空热处理后工件的畸变量应在技术规定范围内。
5
ICS25.200 CCS J 36
GB
中华人民共和国国家标准
GB/T22561—2023 代替GB/T22561—2008
真空热处理
Vacuum heat treatment
2023-12-01实施
2023-05-23发布
国家市场监督管理总局 发布
国家标准化管理委员会
GB/T22561—2023
目 次
前言 1 范围 2 规范性引用文件术语和定义
3
工艺分类及代号 5 设备技术要求
4
.
工艺过程与工艺规范质量控制与检验安全、卫生与环保· 能源消耗
6
8 9 10 人员要求
11 产品记录与报告单· 附录A(资料性) 常用金属材料真空热处理时的最大允许压升率附录B(资料性) 常用金属材料在真空下可以相互接触不黏合的最高允许温度附录C(资料性) 常用金属材料真空热处理参考数据附录D(资料性) 加热滞后时间的测定方法
L0
12
GB/T 22561—2023
前言
本文件按照GB/T1.1一2020《标准化工作导则第1部分:标准化文件的结构和起草规则》的规定
起草。
本文件代替GB/T22561一2008《真空热处理》,与GB/T22561一2008相比,除结构调整和编辑性
改动外,主要技术变化如下:
a)增加了“真空工作压强”“淬火转移时间”术语(见3.4、3.6),删除了“真空腐蚀”术语(见2008年
版的3.4); b) 更改了对真空加热室(见5.1.1,2008年版的5.1.1)、压升率测量(见5.1.5,2008年版的5.1.6)、
真空炉工作容积(见5.1.3,2008年版的5.1.4)和“温度测量”“温度均勾性及系统准确度测定” 的要求(见5.1.6,2008年版的5.1.7,5.1.8):
c) 更改了对真空气淬炉的要求(见5.1.11,2008年版的5.1.12),增加了对真空检测仪校准(见
5.1.4)、超载(超重)报警(见5.1.13)和淬火转移时间的要求(见5.1.14); d) 更改了对工装夹具(见6.1.3,2008年版的6.1.2.2)、真空压强(见6.2.2,2008年版的6.3.2)、工
件分段预热方法(见6.2.3,2008年版的6.3.3)、冷却介质(见6.4.1,2008年版的5.3)、气淬(见 6.4.3,2008年版的6.5.2)及出炉和清理的要求(见6.5,2008年版的6.6);
e)增加了工件热处理工艺规范(见6.14)和水率冷却的要求(见6.4.4),更改了工件最大截面厚度
或直径(见6.3.4,2008年版的6.4.5),删除了真空退火加热保温时间(见2008年版的6.4.4); f) 更改了质量控制和检验的要求(见第7章,2008年版的第7章); g) 更改了对能耗的要求(见9.2,2008年版的5.1.2); h)增加了人员要求(见第10章)。 本文件由全国热处理标准化技术委员会(SAC/TC75)提出并归口。 本文件起草单位:上海材料研究所有限公司、滁州华海中谊工业炉有限公司、江苏丰东热技术有限
公司、中航长城计量测试(天津)有限公司、北京航天新立科技有限公司、奇精机械股份有限公司、中国机械总院集团北京机电研究所有限公司、北京北方华创真空技术有限公司、北京华立精细化工公司、上海市轴承技术研究所有限公司、湖北三环锻造有限公司、北京星航机电装备有限公司、浙江国检检测技术股份有限公司、株洲中车天力锻业有限公司、天津市热处理研究所有限公司、常州新区河海热处理工程有限公司、西安福莱特热处理有限公司。
本文件主要起草人:卢军、徐跃明、李俏、胡东彪、韩伯群、吕国义、孙晓哲、汪守丰、刘双林、葛圣东、 黄雄荣、刘宏扬、田伟智、黄俊杰、姜影、高新宇、殷和平、杨祯、束东方、苏行、王宝平。
本文件于2008年首次发布,本次为第一次修订。
II
GB/T22561—2023
真空热处理
1范围
本文件规定了金属材料在真空状态下热处理设备、工艺过程与工艺规范、质量控制与检验、安全卫生与环保、能源消耗、人员要求、产品记录与报告等要求。
本文件适用于合金结构钢、工具钢、模具钢、不锈钢、耐热钢、钛合金、高温合金、难熔金属合金及精密合金等材料的真空热处理,包括真空淬火、真空回火、真空退火、真空固溶处理及时效等工艺。
本文件不适用于真空渗碳和真空渗氮等工艺
2 规范性引用文件
下列文件中的内容通过文中的规范性引用而构成本文件必不可少的条款。其中,注日期的引用文
件,仅该日期对应的版本适用于本文件;不注期的引用文件,其最新版本(包括所有的修改单)适用于本文件。
GB 3095 5环境空气质量标准 GB/T7232金属热处理术语 GB/T10066.1 电热和电磁处理装置的试验方法第1部分:通用部分 GB/T10067.1 电热和电磁处理装置基本技术条件第1部分:通用部分 GB/T10067.4 电热装置基本技术条件第4部分:间接电阻炉 GB/T10067.45电热装置基本技术条件第45部分:真空淬火炉 GB/T 10067.47 电热装置基本技术条件第47部分:真空热处理和钎焊炉 GB/T 12603 金属热处理工艺分类及代号 GB 15735 金属热处理生产过程安全、卫生要求 GB/T 17358 热处理生产电耗计算和测定方法 GB/T 19944 热处理生产燃料消耗计算和测定方法 GB/T 24487 氧化铝 GB/T 30823 测定工业火油冷却性能的镍合金探头试验方法 GB/T 30825 热处理温度测量 GB/T 32541 热处理质量控制体系 GB/T 34895 热处理金相检验通则 GB/T 38751 热处理件硬度检验通则 GB/T 38819 绿色热处理技术要求及评价 JB/T7530 热处理用氩气、氮气、氢气一般技术条件 JB/T11810 真空高压气率炉热处理技术要求 JB/T13026 热处理用油基淬火介质
3 :术语和定义
GB/T7232界定的以及下列术语和定义适用于本文件。
1
GB/T225612023
3.1
真空压强 vacuum pressure 真空状态下,用稀薄气体的压强表示的真空程度。 注:单位为帕(Pa)。
3.2
脱气 outgassing 在真空条件下,材料自然排放出气体或蒸汽。
3.3
加热滞后时间 heatinglagtime 真空加热条件下,真空炉内热电偶到达工艺设定温度与工件或试样心部热电偶到达工艺设定的下
限温度的时间差。 3.4
真空工作压强 working vacuumpressure 材料(工件)允许开始加热时的真空压强。
3.5
分压 partialpressure 真空气氛中任一气体组分的实际压强。 注:在真空热处理中,通常是指向炉内回充情性气体的压强。
3.6
淬火转移时间 quenching transfer time 材料(工件)从加热室取出至完全进人淬火介质中的时间。
工艺分类及代号
4
真空热处理工艺分类及代号应符合GB/T12603的规定,见表1。
表1 真空热处理工艺分类及代号
代号 500-02 511-02 513-02 514-02 517-02 518-02
工艺分类真空热处理真空退火真空加热火真空淬火回火真空固溶处理
真空固溶处理十时效
5 设备技术要求
5.1 真空加热设备 5.1.1 真空加热设备应符合GB/T10067.1、GB/T10067.4、GB/T10067.45及GB/T10067.47规定的技术条件。加热室内结构材料在热处理过程中不应与工件或介质气体发生反应。加热室在设计有惰性气体高压气淬功能时,应设置合理的超压排气装置。 2
GB/T22561—2023
5.1.2真空系统应有足够的抽气能力并保证密封性,同时应严格控制分压气体流量和保持规定分压压力,满足工艺要求的真空水平。 5.1.3在空炉、干燥、除气的情况下,不同工作容积的真空炉应在表2规定的时间内抽到规定的真空工作压强。
表2真空炉空炉抽到规定真空工作压强时间
真空炉工作容积/m
抽到规定真空工作压强时间/min
>0.5~<1.0 ≥1.0~<5.0
20 ≤40 ≤60
≥5.0
5.1.4真空炉应配备真空压强指示、记录及自动控制装置。不同的真空压强区间宜配置不同的真空检测仪。真空检测仪应每3个月校准1次,特殊情况下应增加校准次数。真空检测仪的校准应按规定执行。 5.1.5真空炉在冷态空载充分干燥后的压升率应小于0.67Pa/h,测量方法按GB/T10066.1的规定执行。真空炉工作期间每周至少测量一次压升率。测量时真空压强到达正在执行工艺的初始真空压强设定值后,关闭真空炉的所有阀门,记录第一次真空压强,过15min后记录第二次真空压强,两次真空压强的差除以记录的间隔时间作为该真空炉的压升率。常用金属材料真空热处理允许的最大压升率见附录A。 5.1.6真空炉的温度测量应按GB/T30825的规定进行,温度均匀性及系统准确度测定周期应符合 GB/T32541的要求。 5.1.7真空炉炉壳的表面温升不应大于30℃。 5.1.8为准确控制工件温度,可使用一支或多支载荷热电偶。热电偶尽可能与工件接触。热电偶若与工件材料发生反应则应加护套。热电偶插入工件的深度应为热电偶直径的10倍以上,并与孔底部的表面紧密接触。 5.1.9真空炉的加热电极在通水冷却情况下,对地绝缘电阻应大于1kQ。 5.1.10真空炉冷却水进水口的压力应大于0.25MPa,流量可调节,并配有断水报警保护装置。冷却水进水口的水温为5℃~35℃,出水口的温升不应超过20℃(气淬时允许短时超温),快速冷却时冷却水压应大于0.3MPa。 5.1.11真空气炉应配有足够容积的贮气罐,并带有快速充气装置、气风扇及热交换系统,且有相应的减压阀和压力表,能准确指示及调节冷却气体压强,满足JB/T11810的要求。 5.1.12真空回火炉应带有热风搅拌或对流加热系统和快冷装置。 5.1.13真空油(水、气)淬炉应配备超载(超重)报警装置。 5.1.14真空油淬炉和真空水淬炉的工件淬火转移时间一般小于20s。对于大型真空炉和特殊材料的真空热处理,其淬火转移时间应根据工艺的技术要求协商确定。
5.2淬火冷却装置 5.2.1真空炉应根据需要配置容积足够大的油槽(水槽)及贮气罐,以保证连续淬火条件下有足够的冷却能力。 5.2.2油槽和水槽均应配有加热、冷却、控温、超温报警及搅拌装置,温控仪表的允许偏差应在土5℃范围内。 5.2.3油槽和水槽应设置液面下限和上限位置的报警装置,油槽和水槽的搅拌应设置故障报警装置。
3
GB/T 22561—2023
6工艺过程与工艺规范
6.1热处理前的准备 6.1.1应对真空炉进行常规检查,保证处于正常工作状态。对需处理钛合金的真空炉,若先前处理过非钛合金,应采用高温加热等方法清洁炉膛。 6.1.2人炉工件及工装夹具装炉前应进行清洗和烘干,不应有锈斑和对工件及炉膛产生有害影响的污物、低熔点涂层及镀层等。 6.1.3应防止夹具和工装在生产过程中与工件发生反应或黏合,材料在真空下可以相互接触不黏合的最高允许温度见附录B。为避免发生反应,可采用氧化铝块(板或棒)或氧化铝粉隔离。氧化铝粉的化学成分及性能应符合GB/T24487的规定, 6.1.4应根据不同工件的技术要求编制相应的真空热处理工艺规范。常用材料的真空热处理工艺参数见附录C。 6.2加热 6.2.1工件应放置在真空炉炉膛的有效加热区内,保证工件加热均匀。加热室的真空压强小于6.67Pa 时方可加热升温。升温过程中需注意工件脱气,若因脱气使真空压强高于临界值时,应停止加热并调节升温速度。 6.2.2应根据工件材料及工艺的要求,确定并控制加热温度和加热时的真空压强,该真空压强的控制可通过回充氮气或氩气调节分压而实施。真空炉回充的氮气或氩气应符合6.4.1.1的规定。 6.2.3工件达到设定加热温度之前需进行分段预热,分段预热方法参见表C.2。 6.2.4工件真空回火时,当炉内达到一定的真空压强(小于或等于0.133Pa)时,应向炉内通人高纯氮气到6.6×10*Pa~2.0×105Pa,并通过风扇循环保持此炉压直至结束。 6.2.5工件真空退火时,需避免因真空压强过低而产生表面合金元素挥发。 6.3 保温时间 6.3.1工件真空热处理时的加热保温时间需考虑工件加热时的滞后效应,加热滞后时间的确定可参考附录D。 6.3.2真空加热保温时间应包括加热滞后时间和组织均匀化时间 6.3.3真空回火加热保温时间不应少于2h。 6.3.4真空除氢时间应根据工件最大截面厚度或直径确定,真空除氢时间见表3。
表3真空除氢时间
时间/h 1~2 >2~3 >3
工件最大截面厚度或直径/mm
≤20 >20~<50 ≥50
6.4冷却 6.4.1冷却介质 6.4.1.1J 真空炉冷却用气应符合JB/T7530的规定。对合金钢一般采用99.995%纯度的氮气,对高温
4
GB/T 22561—2023
合金一般采用99.999%纯度的氩气,对钛合金应采用99.999%纯度的氩气。 6.4.1.2淬火油应符合JB/T13026中相关技术要求,满足工件真空淬火后的硬度及光亮度的要求。 6.4.1.3氢气不应作为钛和钛合金淬火冷却介质和分压气体。氮气作为分压气体应根据处理工件的材质来确定。 6.4.1.4应定期检测淬火油、水的冷却能力,检测方法按GB/T30823的规定执行。 6.4.2油淬
真空淬火油在淬火前应充分脱气并排除水分,必要时适当加热,将油温控制在20℃~100℃以内。 为控制油面压强,淬火时应充高纯氮气或氩气,一般控制在5X101Pa左右。淬火时,油槽内应进行搅拌。 6.4.3气淬
根据工艺要求,可采用正压气淬或负压气。正压气率时根据材料的淬透性通人1.5×105Pa~ 20×105Pa的高纯氮气或氩气;负压气时通人7.9×10*Pa~9.3×10Pa的高纯氮气或氩气进行淬火。高速钢和高合金模具钢工件宜采用正压气淬方法,钛合金应采用高纯氩气淬火
根据工艺要求,高速钢和模具钢等工件宜通过控制情性气体的流量、压强和风速进行分级萍火,以
减小被处理件的畸变量。 6.4.4水淬
真空水时需避免水蒸气对加热室的污染,工件转移速度应符合工艺要求,水温应控制在30℃以下。为控制水面压强,淬火时应充气(高纯氮气或氩气),一般控制在1.013×10°Pa左右。淬火时,水槽内应进行搅拌。 6.4.5气冷
工件进行真空回火时,回火加热结束后应根据工艺要求采用情性气体冷却。
6.4.6炉冷
按工艺规定随炉冷却(如退火等)时,冷却过程应保持一定的真空压强,当炉温降至一定温度后方可停止抽真空。 6.5出炉及清理
工件应冷却至低于65℃后出炉。对于真空油率,应排清预备室(冷却室)中的油气后方可充气和出
炉。油工件出炉后应进行去油清理。
7质量控制与检验
7.1外观 7.1.1真空热处理后的工件表面应光亮、无机械损伤 7.1.2真空热处理后的工件表面不应出现合金贫化或氧化。 7.2畸变 7.2.1真空热处理后工件的畸变量应在技术规定范围内。
5