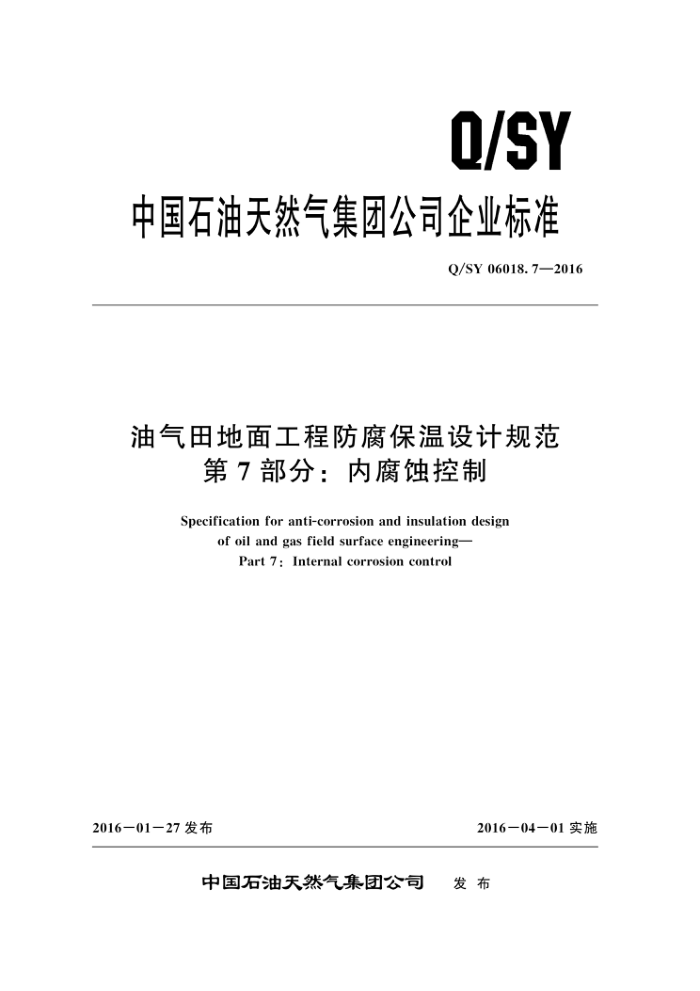
Q/SY
中国石油天然气集团公司企业标准
Q/SY 06018.7—2016
油气田地面工程防腐保温设计规范
第7部分:内腐蚀控制
Specification for anti-corrosion and insulation design
of oil and gas field surface engineering-
Part 7 : Internal corrosion control
2016-0127 发布
2016-04-01实施
中国石油天然气集团公司 发布
Q/SY 06018.7—2016
次
目
前言
II
.
范围规范性引用文件
2
3 输送介质的腐蚀性评估
...................................
内腐蚀控制设计原则和控制方法 4.1 内腐蚀控制设计的一般原则 4.2内腐蚀控制方法 腐蚀监测
.....
5
....
Q/SY 06018.7—2016
前言
Q/SY 06018《油气田地面工程防腐保温设计规范》是油气田地面工程设计系列标准之一。该标准分为以下13个部分:
第1部分:埋地管道及设备外防腐层;第2部分:地面管道及设备外防腐层:第3部分:阴极保护;第4部分:地面管道及设备绝热;第5部分:埋地管道及设备绝热;第6部分:内腐蚀监测; 第7部分:内腐蚀控制; 第8部分:双金属复合钢管选用;第9部分:耐腐蚀合金 UNS N08825衬里复合钢管; 第10部分:耐腐蚀合金UNS N08825冶金复合钢管;第11部分:耐腐蚀合金UNS N08825冶金复合管件;第12部分:耐腐蚀合金UNS N08825 冶金复合弯管; 第13部分:耐腐蚀合金UNS S31603衬里复合钢管。
本部分为 Q/SY 06018 的第 7部分。 本部分按照GB/T1.1一2009《标准化工作导则第1部分:标准的结构和编写》给出的规则
起草。
本部分由中国石油天然气集团公司工程建设分公司、中国石油天然气股份有限公司勘探与生产分
公司提出。
本部分由中国石油天然气集团公司标准化委员会石油石化工程建设专业标准化技术委员会归口。 本部分起草单位:中国石油集团工程设计有限责任公司西南分公司。 本部分主要起草人:陈勇彬、施岱艳、曹晓燕、李林辉、姜放、傅贺平。
II
Q/SY 06018. 7—2016
油气田地面工程防腐保温设计规范
第7部分:内腐蚀控制
1范围
Q/SY06018的本部分规定了油气田地面工程内腐蚀控制设计的技术要求。 本部分适用于陆上油气田、滩海陆采油气田和海上油气田陆岸终端地面工程新建及改扩建项目
油、气、水管道的内腐蚀控制。
2 规范性引用文件
下列文件对于本文件的应用是必不可少的。凡是注日期的引用文件,仅注日期的版本适用于本文
件。凡是不注日期的引用文件,其最新版本(包括所有的修改单)适用于本文件
GB/T20972(所有部分)石油天然气工业油气开采中用于含硫化氢环境的材料 SY/T 0599天然气地面设施抗硫化物应力开裂和抗应力腐蚀开裂的金属材料要求 SY/T 0611高含硫化氢气田集输管道系统内腐蚀控制要求 SY/T 6623内覆或衬里耐腐蚀合金复合钢管规范 Q/SY 06018.6 油气田地面工程防腐保温设计规范 第 6 部分:内腐蚀监测
3输送介质的腐蚀性评估
3.1应根据腐蚀性介质含量和气体或液体组分及工况条件,预测可能造成的有害影响,必要时可对其腐蚀性进行评价。应考虑的腐蚀危害主要有:
a)由于减薄、点蚀、氢脆、氢致开裂、硫化物应力开裂或应力腐蚀开裂等导致管体的损害。 b)腐蚀产物对管输介质的污染。
3.2需要搜集的输送介质中腐蚀性杂质及其含量包括:
a)细菌。 b)二氧化碳。 c)氯化物。 d)硫化氢。 e)有机酸。 f)氧。 g)固体或沉淀物。 h)其他含硫的化合物。 i)水以及水质。
3.3 二氧化碳腐蚀的影响因素包括二氧化碳分压、水润湿度、温度、pH 值、流速等。可按表1采用二氧化碳分压进行腐蚀程度划分,并注意特定温度范围内的腐蚀速率显著增大的风险。 3.4金属材料在硫化氢腐蚀环境中,易发生氢鼓泡、氢致开裂、硫化物应力开裂等。硫化氢腐蚀环境按照GB/T 20972,SY/T 0599的规定进行评价。 3.5氯离子腐蚀环境下应重点考虑点蚀、氯化物应力腐蚀。
1
Q/SY 06018. 7—2016
表1二氧化碳腐蚀作用划分表
腐蚀情况无腐蚀轻度腐蚀中度至高度腐蚀
pco,,MPa <0. 05 0. 05~0. 21 >0. 21
3.6在密闭环境下,应考虑硫酸盐还原菌引起的腐蚀。 3.7当油气系统中有氧气存在时,应考虑氧腐蚀的影响。 3.8当异种金属连接时,应考虑电偶腐蚀的影响。 3.9在螺栓、垫片、阀座、沉积物等相接触形成的缝隙的部位,应考虑缝隙腐蚀的影响。 3.10若油气田输送介质含有固体颗粒时,对于除砂器前端的管线、阀门、弯头、三通、大小头等管网中流场突变区域,应考虑冲刷腐蚀的影响。 3.11管道内介质腐蚀性的评价,可根据表2所给出的评价指标进行判断。
表2管道内介质腐蚀性评价指标
级别
项目
低 <0. 025 <0. 13
中 0. 025~0. 12 0.13~0.20
严重 >0. 25 >0.38
较重 0. 13~0.25 0. 21~0. 38
平均腐蚀率,mm/年点蚀率,mm/年
注:以两项中的最严重结果为准。
内腐蚀控制设计原则和控制方法
4
4.1 内腐蚀控制设计的一般原则 4.1.1当管输介质中含的腐蚀性杂质可导致管道腐蚀时,内腐蚀控制方案应根据工程规模、设计寿命和介质腐蚀性等因素综合考虑确定 4.1.2对于高含硫化氢气田的内腐蚀控制技术要求,应执行SY/T0611的规定。 4.2内腐蚀控制方法 4.2.1材料选择 4. 2. 1. 1 当环境属于GB/T20972中规定的酸性环境时,地面集输系统的金属材料的选择应遵循 GB/T 20972 的要求。
一般碳钢管道内腐蚀裕量宜取1mm~3mm;当腐蚀裕量为3mm以上时,宜对“碳钢腐
4. 2. 1. 2
蚀裕量相应防腐措施”方案与其他方案进行整个设计生产周期内技术经济方案对比。 4.2.1.3当腐蚀环境比较复杂,碳钢材质和其他腐蚀控制方法难以实现或效果达不到要求时,可采用耐腐蚀合金或非金属材料进行内腐蚀控制。耐腐蚀合金内覆或衬里产品应在工厂进行化学成分、结合强度、抗腐蚀性能等检验。耐腐蚀合金复合钢管的技术要求参照SY/T6623。在酸性环境中耐蚀合金材料应符合GB/T20972.3的要求。
2
Q/SY 06018.7—2016
4.2.2清管 4.2.2.1对可能出现积液和腐蚀介质沉积的管道,宜考虑采用清管进行处理。 4.2.2.2选用清管器应考虑如下因素:
a)清管器清除沉积污物的能力。 b)挤过管道截面的能力。 c)清管器构件用材与管输介质的相容性。 d)运行的可行性。 e) 管道内是否存在内涂层和缓蚀剂膜。应注意,对有内涂层的管道不宜采用金属或研磨类型的
清管器,可采用非金属清管器
4. 2. 3 流速控制 4.2.3.1管输介质的流速应满足工艺设计要求并应控制在使腐蚀降为最小的范围内。流速范围的下限值应使腐蚀性杂质悬浮在管输介质中,使管道内积存的腐蚀性杂质降至最少;流速范围的上限应使磨损腐蚀、空泡腐蚀等降至最小,使用缓蚀剂时应不影响缓蚀剂膜的稳定性。 4.2.3.2气田集输管道内流速宜控制在 3m/s~8m/s 4.2.3.3处于流场突变区域的弯头、三通等可增加壁厚;对阀门内构件,可堆焊硬质合金,以增强耐冲刷腐蚀的能力。 4.2.4温度控制
用于介质中含有二氧化碳的碳钢管道,油气的运行温度宜控制在60℃之内。 4.2.5结构设计 4. 2. 5.1^ 管道的变径应采用平滑水力过渡的大小头。 4.2.5.2设计应减少设置盲法兰、盲管段、支管、接头等构成的死端。否则,应设置吹扫、收集或排放装置,定期排放所聚积的腐蚀产物。 4.2.6水和腐蚀性组分脱除 4. 2. 6.1^ 管输介质在输送期间,可采用分离、脱水工艺,降低其含水量 4.2.6.2含氧的管输介质在输送期间,可导致腐蚀。宜考虑脱氧,使管输介质含氧量降低到允许水平。 4.2.6.3可用酸性气体吸收塔和洗涤器将管输介质中的腐蚀性介质如酸性气体(硫化氢、二氧化碳、 低分子量有机酸)从管输介质中脱除。 4.2.7缓蚀剂加注 4.2.7.1对需加注缓蚀剂的管道,设计应包括适宜的加注装置,加注点位置应使整个管道都得到充分的防护。 4.2.7.2缓蚀剂的实验室评价应包括如下方面:
a)溶解性:无沉淀和无相分离。 b)乳化趋势:无乳液产生。 c)发泡趋势:无泡沫。 d)黏性沉淀:无沉淀 e)热稳定性:稳定(温度根据系统最高设计温度确定)。
3
Q/SY 06018. 7—2016
f)毒性试验:经口LDso大于500mg/kg,或吸人LCso大于2000mg/kg。 g)腐蚀速率:按推荐浓度加注时,腐蚀速率小于或等于0.075mm/年或按照所设计具体工程确
定,且无点蚀。
h)(闭口)闪点:缓蚀剂的闪点应满足化学品运输和存储的相关标准要求。
凝固点:低于最低环境温度。
i)
j)符合环保要求。 4.2.7.3缓蚀剂加注方式主要包括涂膜和连续加注,其中:
a)连续加注适用于集输管线的腐蚀防护。 b)缓蚀剂涂膜是将缓蚀剂均匀地涂抹在被保护金属的表面,形成一层缓蚀剂保护膜,
4.2.7.4缓蚀剂加注的加量应根据缓蚀剂的特性、井况、生产情况、加注设备情况、防腐的要求等,以室内评价确定的缓蚀剂保护浓度为基础,通过现场试验而定,并在今后管道的运行过程中根据腐蚀监测结果进行调整,缓蚀剂加注量主要包括:
a)缓蚀剂涂膜加注量:采用0.076mm的成膜厚度来确定缓蚀剂涂膜的基本加注量。计算公式如下:
W = 2. 4DI
.(1)
式中: W——涂膜处理量,单位为升(L); D—管道内径,单位为厘米(cm); L 管道长度,单位为千米(km)。 在实际施工过程中还应考虑损耗量,一般为实际加注量的30%~40% b)连续加注量:每104m3气量缓蚀剂加注量在0.17L~0.66L,在实际施工过程中还应考虑损
耗量,一般为实际加注量的10%。有现场产水量数据且相对稳定时,连续加注缓蚀剂的量宜根据产水量计算,加注浓度应根据缓蚀剂室内评价结果推荐,一般为200mg/L~ 1000mg/L。
4.2.7.5为提高缓蚀剂的缓蚀效果,应考虑联合使用其他减缓腐蚀的措施,如清管、脱水等
4.2.8内防腐层 4. 2.8.1I 内防腐层可用于预计腐蚀速率超过容许范围的管道 4.2.8.2使用内涂层时,应考虑内补口的质量控制 4.2.8.3内涂层和衬里应根据输送介质腐蚀性进行选择 4.2.8.4采用内涂层时,应考虑涂层的抗老化性能 4.2.8.5内涂层应具有抗输送介质、污物、腐蚀性杂质、添加剂等侵蚀的能力,而且不应损害管输介质的质量,宜通过试验选定合适的内涂层材料。
5腐蚀监测
腐蚀监测方法、腐蚀监测点设置、腐蚀结果的评价按照Q/SY06018.6的规定执行。