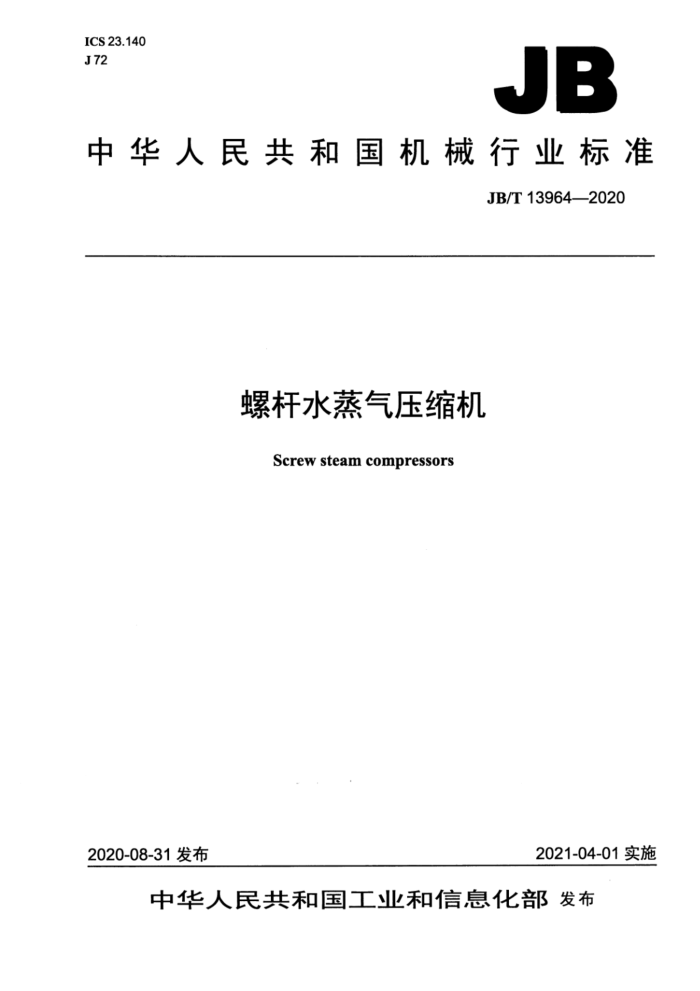
ICS23.140 J72
JB
中华人民共和国机械行业标准
JB/T13964—2020
螺杆水蒸气压缩机
Screwsteamcompressors
2021-04-01实施
2020-08-31发布
中华人民共和国工业和信息化部发布
JB/T13964-2020
目 次
前言 1范围 2规范性引用文件 3术语和定义. 4结构型式和型号 4.1结构型式. 4.2型号 5要求. 5.1 基本要求 5.2 材料要求... 5.3 辅助设备要求. 5.4 承压件及管路要求 5.5 安全要求. 5.6其他要求.. 5.7成套要求. 6质保.. 7试验和检验 7.1热运转试验.. 7.2机械运转试验 7.3性能试验.. 8标志、包装和贮存
T
2
-
表1. 喷水水质要求
JB/T13964—2020
前言
本标准按照GB/T1.1一2009给出的规则起草。 本标准由中国机械工业联合会提出。 本标准由全国压缩机标准化技术委员会(SAC/TC145)归口。 本标准起草单位:合肥通用机械研究院有限公司、浙江开山压缩机股份有限公司、中国船舶重工集
团公司第七一一研究所、上海汉钟精机股份有限公司。
本标准主要起草人:倪健、田兵兵、任芳、陆征、胡梦婷、王乐、连小松、张百洋、叶鹏、刘常峰、 李子亮。
本标准为首次发布。
II
JB/T13964—2020
螺杆水蒸气压缩机
1范围
本标准规定了螺杆水蒸气压缩机(以下简称压缩机)的术语和定义、结构型式、型号、要求、质保、 试验、检验及标志、包装和贮存。
本标准适用于最高许用工作压力不大于3MPa、最高许用温度不超过250℃的压缩机。
2 2规范性引用文件
下列文件对于本文件的应用是必不可少的。凡是注日期的引用文件,仅注日期的版本适用于本文件。凡是不注日期的引用文件,其最新版本(包括所有的修改单)适用于本文件。
GB/T150(所有部分)压力容器 GB/T 151 热交换器
GB/T 755 旋转电机定额和性能 GB/T2100 通用耐蚀钢铸件 GB 2894 安全标志及其使用导则 GB3836.1 爆炸性环境第1部分:设备通用要求 GB/T 3853 容积式压缩机验收试验 GB/T4272 设备及管道绝热技术通则 GB/T 4975 容积式压缩机术语总则 GB/T4980 容积式压缩机噪声的测定 GB/T5574—2008工业用橡胶板 GB7231工业管道的基本识别色、识别符号和安全标识 GB/T9239.1一2006机械振动恒态(刚性)转子平衡品质要求 第1部分:规范与平衡充差的
检验
GB/T10095.12008 圆柱齿轮 精度制第1部分:轮齿同侧齿面偏差的定义和充许值 GB/T13306标牌 GB/T15487—2015 容积式压缩机流量测量方法 GB18613中小型三相异步电动机能效限定值及能效等级 GB/Z19414工业用闭式齿轮传动装置 GB19517国家电气设备安全技术规范 GB/T25357 石油、石化及天然气工业流程用容积式回转压缩机 GB30254 高压三相笼型异步电动机能效限定值及能效等级 GB50316 工业金属管道设计规范 JB/T2589 容积式压缩机型号编制方法 JB/T 6441 压缩机用安全阀 JB/T6908 容积式压缩机用钢锻件 JB/T7663.1 容积式压缩机包装技术条件 JB/T7663.2 容积式压缩机涂装技术条件
1
JB/T13964—2020
JB/T8935工艺流程用压缩机安全要求 JB/T9104容积式压缩机用球墨铸铁件技术条件 NB/T47007空冷式热交换器 TSG21固定式压力容器安全技术监察规程
3术语和定义
GB/T4975、GB/T25357和GB/T3853界定的术语和定义适用于本文件。
4结构型式和型号
4.1结构型式
压缩机的结构型式为干螺杆压缩机。 于螺杆压缩机是指不用液体密封转子间隙和不用啮合转子来传动的螺旋式回转压缩机,注1:干螺杆压缩机用转子上的同步齿轮保证转子之间的相互啮合关系并通过同步齿轮带动从动转子。 注2:在干螺杆压缩机中转子与转子不发生接触,
4.2型号
压缩机的型号编制应符合JB/T2589的规定。
5要求
5.1基本要求 5.1.1压缩机应符合本标准的规定,并按经规定程序批准的图样和技术文件制造。 5.1.2压缩机运行参数包括压缩机吸气温度和压力、排气温度和压力、实际容积流量及其波动范围。 5.1.3压缩机内部间隙的设置应考虑水蒸气温度、压力及其波动范围。 5.1.4# 技术协议中应明确水蒸气中所含杂质的组分、物态、含量。所含杂质气体的体积分数不应超过 3%。 5.1.5 压缩机及系统的设计和选型应按5.1.25.1.4中的参数进行。在满足所需电、水、油、气等公用工程条件下,压缩机在规定的工况下应能连续稳定运行。 5.1.6除非另有规定,压缩机主机设计寿命应不低于20年,大修周期应不低于24000h。 5.1.7驱动电动机、电气部件和电气设备应符合GB/T755和GB19517的规定。其中异步电动机应满足GB18613或GB30254规定的2级能效要求。 5.1.8当压缩机由电动机驱动时,电动机额定功率应按服务系数1.0来确定,且应至少为任何额定运行工况要求的最大功率(包括齿轮箱和/或联轴器损失)的110%。 5.1.9压缩机的密封应能确保水蒸气或凝结水不向轴承箱侧泄漏。若有情性气体或密封油等密封介质进入压缩腔,则泄漏量应确保不对下游工艺产生影响,并经用户同意。除非另有规定,压缩机工作时禁止空气泄漏至水蒸气内。 5.1.10压缩机的同步齿轮、轴等回转组合部件应做动平衡试验,平衡品质级别应不低于GB/T9239.1一 2006规定的G2.5级。 5.1.11机壳振动速度应在压缩机最大连续转速或规定运行转速范围内测量,若有规定还应测量轴振动。 压缩机的振动极限值应符合GB/T25357的规定。
2
JB/T13964—2020
5.1.12机组噪声应符合GB/T25357的规定。 5.2材料要求 5.2.1压缩机材料应按运行工况和现场环境条件进行选用。 5.2.2转子应采用锻件制造。转子及壳体材料应耐腐蚀。若表面进行防腐处理,则至少应满足大修周期的要求。 5.2.3球墨铸铁件应符合JB/T9104的规定,耐蚀钢铸件应符合GB/T2100的规定,锻钢件应符合JB/T 6908的规定。 5.3辅助设备要求 5.3.1工艺流程对水蒸气流量需求变化较大时,应设有流量自动调节装置,宜用变频方式调节,同时充许采用旁路回流方式作为辅助调节。 5.3.2当压缩机出口水蒸气状态为饱和态时,宜在压缩机出口加装气液分离器,并增加循环喷液管路。 气液分离器应符合以下要求:
—GB/T150(所有部分)和TSG21的规定;一分离效果满足下游水蒸气管网工艺要求;一在规定工况下,水蒸气经过气液分离器后的压降不得超过排气压力的1%;一设置有自动排液阀。
5.3.3在压缩带压水蒸气时,压缩机前应配置调节阀或旁路阀等节流装置。 5.3.4压缩机的进气管路、入口喷液管路均应安装过滤器,过滤精度不宜大于50μm。入口喷液管路过滤器滤芯的强度应能保证在压缩机起动或运行过程中滤芯不被损坏。 5.3.5油泵电动机、油冷风机等辅助用电设备的选型,应按GB/T25357的规定。 5.3.6当压缩机和主电动机之间采用齿轮箱传递转矩和变速时,齿轮箱的设计应符合GB/Z19414的规定。当采用内置齿轮箱时,齿轮的设计精度至少应达到GB/T10095.1一2008规定的5级要求。 5.4承压件及管路要求 5.4.1 压缩机系统冷却器应符合GB/T151或NB/T47007的规定。 5.4.2容器焊接接头的形状尺寸、外观及质量要求应符合GB/T150(所有部分)的规定。 5.4.3 压缩机机壳应进行液压试验,液压试验应符合GB/T25357的要求。 5.4.4管道焊接结构应符合GB50316的规定。 5.4.5压缩机腔体、容器及管道设计时应在可能积水的地方设置疏水口。疏水应排入疏水容器中,不得随意排放。疏水管道上应安装阀门和集水器。 5.4.6压缩机系统中与水蒸气接触的管道应做保温隔热处理,隔热处理应符合GB/T4272的规定, 5.4.7保温结构由保温层和保护层组成。保温结构的强度应能保证在机组多次起停和长期运行过程中保温层不被损坏。 5.4.8保温结构应不妨碍压缩机的检修,宜采用可拆卸结构。 5.4.9压缩机排气管路应安装出口单向阀。 5.4.10辅助管路应选用无缝管并考虑腐蚀的影响。紧固件、法兰及垫片应符合相关标准的要求,并在现场环境条件下能耐腐蚀。 5.5安全要求 5.5.1当水蒸气中混有易燃、易爆气体或者机组处于易燃、易爆环境时,驱动电动机、电气部件和电气设备应符合GB3836.1的规定。 5.5.2压缩机排气管路应安装安全阀,安全阀应安装在压缩机出口与出口单向阀之间。安全阀在高温
3
JB/T13964—2020
高压水蒸气条件下应能可靠工作,且符合以下要求:
-JB/T6441的规定;开启压力应高于被保护系统的最高工作压力,但不应高于最高工作压力的1.1倍;一泄放能力不得小于压缩机的安全泄放量,泄放的水蒸气应回收或泄放至安全处。
5.5.3压缩机系统至少应设有下列自动防护功能,在发生下列情况之一时,系统应能按照预先设定的故障处理流程进行报警或报警停机:
排气温度超过限值;一排气压力超过限值;吸气压力高于或低于限值;润滑油供油压力低于限值;润滑油供油温度高于限值:轴承温度高于限值:振动高于限值。
5.5.4在以下任何一种情况单独发生时,压缩机系统不应引发机组故障及漏水、漏气和管道爆裂等事故:
台远传仪表故障;台自动阀门故障; -软水或循环冷却水断水;仪表风断气:全厂断电。
-
5.5.5当机组设置隔音罩时,应确保隔音罩内的散热及设置罩内高温报警。 5.5.6压缩机应在显著且易于操作的位置设置红色的紧急停机按钮。 5.5.7压缩机系统中对表面高温部件以及可能喷出水蒸气的部位应设置安全标志,安全标志应符合GB 2894的要求。 5.5.8压缩机的其他安全要求应符合JB/T8935的规定。 5.6其他要求 5.6.1压缩机组宜具备手动和自动两种操作模式,手动操作模式应具有单独控制任何一台自动阀门与电动设备的功能。 5.6.2机组在正常运行时不允许有水蒸气或热水向环境中连续排放。在机组起动和停机时,允许排出少量水蒸气和热水。 5.6.3压缩机的补水宜采用除氧水,当采用凝结水、脱盐水或软水时须经用户审核和认可。喷入压缩机体内的水质应满足表1的要求。
表1喷水水质要求
硬度 ≤0.6mmol/L
pH值(25℃)
氯离子含量 ≤2.5×10*5
悬浮物含量 <5mg/L
6.5~8.5
5.6.4与润滑油接触的橡胶件应采用耐油橡胶制成,其耐油性能应达到GB/T5574一2008规定的C 类要求。 5.6.5转子、壳体主要加工尺寸以及装配间隙应检测并记录。 5.6.6压缩机系统应按图样和技术文件的要求进行涂装。涂装应符合JB/T7663.2的规定,管道的基本识别色、识别符号和安全标识应符合GB7231的规定。
4
JB/T13964—2020
5.7成套要求
成套供给用户的压缩机至少应包括:一压缩机主机及附属设备;一驱动机和控制装置:传动装置:一专用工具:一随机备件(包括易损件和保用期内需要更换的其他零件);
一随机文件(包括产品合格证、产品使用说明书、装箱单、安装图、装配示意图及压力容器合格证及竣工图)。
6质保
制造厂对按产品使用说明书正常使用的压缩机保用一年,但从发货之日起计,不超过18个月。在
保用期内,产品确因设计或制造不良而损坏或不能正常工作时,制造厂应免费予以修理或更换
?
7试验和检验
7.1热运转试验
在机械运转试验之前应进行热运转试验。热运转试验可以水蒸气或空气作为介质,并以合同中规定的最高工作温度至少加8℃作为排气温度。热运转试验应在最高连续转速下至少稳定进行30min。 7.2机械运转试验 7.2.1每台压缩机出厂前须进行机械运转试验,允许用空气作为工作介质。 7.2.2机械运转试验应在最高连续转速或额定功率下进行,并应至少连续进行2h。 7.2.3机械运转试验的内容及要求应符合下列规定:
a)检查各零、部件的装配质量、工作情况和相互动作的准确性; b)试验期间应记录振动值,振动值应符合5.1.11的规定; c)若振动值超标、轴封失效或声音异常,拆检并排除故障后应重新进行机械运转试验。
7.3性能试验 7.3.1 每台压缩机机械运转试验合格后还应进行性能试验。 7.3.2 压缩机的性能试验应以水蒸气为介质,按规定的实际工况或模拟实际工况进行。 7.3.3 压缩机的性能试验应按GB/T3853的规定。 7.3.4 压缩机的容积流量宜按GB/T15487一2015中附录D的规定检测,流量计应安装在压缩机出口。 7.3.5 压缩机的振动测定应按GB/T25357的规定。 7.3.6 压缩机的噪声测定应按GB/T4980的规定。 7.3.7 性能试验应在压缩机至少连续运行1h后进行,性能试验的内容及要求应符合下列规定:
a)当性能试验条件满足实际工况要求时,测量压缩机在实际工况(包括吸、排气压力,吸、排气
温度及转速)下的实际容积流量和轴功率; b)若性能试验条件为模拟实际工况时,应在与实际工况相同压比的情况下测量压缩机的实际容积
流量和轴功率; c)测得的实际容积流量和轴功率应符合合同或技术协议的规定
5