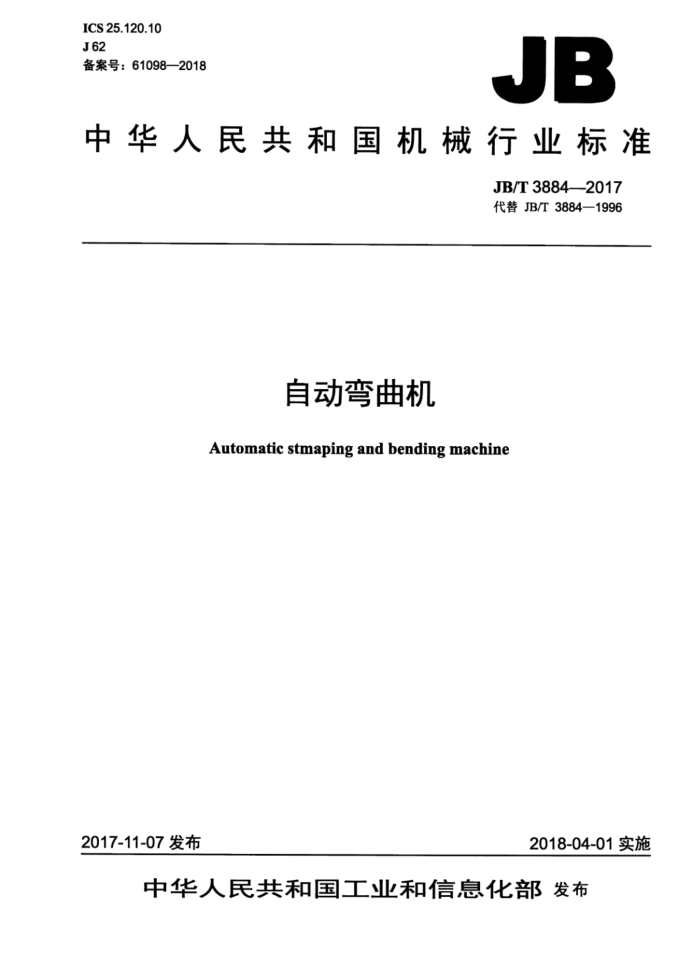
ICS25.120.10 J62 备案号:61098—2018
JB
中华人民共和国机械行业标准
JB/T3884—2017 代替JB/T3884—1996
自动弯曲机
Automatic stmaping and bending machine
2017-11-07发布
2018-04-01实施
中华人民共和国工业和信息化部发布
JB/T3884—2017
目 次
前言 1 范围 2 规范性引用文件
II
型式与基本参数精度 4.1 检验要求 4.2 几何精度检验. 4.3 送料精度检验 5技术要求 5.1 一般要求 5.2 安全防护 5.3 铸件、锻件和焊接件 5.4 加工 5.5 装配. 5.6 电气设备 5.7 润滑系统 5.8 外观. 试验方法
3 4
6
6.1 一般要求. 6.2 空运转试验 6.3 负荷试验 6.4 超负荷试验 6.5 基本参数 6.6 加工. 6.7 装配. 6.8 安全防护 6.9 噪声. 6.10 电气系统 6.11 润滑系统 6.12 外观 6.13 精度检验, 7检验规则. 7.1 检验分类。 7.2 出厂检验, 7.3 型式检验, 8标志、包装、运输和贮存 9 保证 9.1 制造厂 9.2 用户
6
6
i
JB/T3884—2017
前言
本标准按照GB/T1.1一2009给出的规则起草。 本标准代替JB/T3884—1996《自动弯曲机》,与JB/T3884—1996相比主要技术变化如下:
修改了规范性引用文件:一一删去了寿命要求;
修改了精度要求。
一
本标准由中国机械工业联合会提出。 本标准由全国锻压机械标准化技术委员会(SAC/TC220)归口。 本标准起草单位:福建省闽旋科技股份有限公司、厦门正黎明冶金机械有限公司、马鞍山机床及刃
模具产品质量监督检验中心、嵊州市机械行业协会、南安市中机标准化研究院有限公司。
本标准主要起草人:朱斌、黄溢忠、陈立贵、庄鸿辉、楼宇、郑华婷。 本标准所代替标准的历次版本发布情况为
JB3884.1—1985JB3884.2—1985; JB/T3884—1996。
II
JB/T38842017
自动弯曲机
1范围
本标准规定了自动弯曲机的型式与基本参数、精度、技术要求、试验方法、检验规则、标志、包装、 运输、贮存、保证。
本标准适用于冲压、弯曲线材或带料成制件的机械传动的自动弯曲机,不适用于卧式四滑块自动弯曲机。
2规范性引用文件
下列文件对于本文件的应用是必不可少的。凡是注日期的引用文件,仅注日期的版本适用于本文件。凡是不注日期的引用文件,其最新版本(包括所有的修改单)适用于本文件。
GB/T191包装储运图示标志 GB5226.1 机械电气安全机械电气设备第1部分:通用技术条件 GB/T6576 机床润滑系统 GB/T10923一2009锻压机械精度检验通则 GB/T13306标牌 GB/T 23281 锻压机械噪声声压级测量方法 GB/T23282 锻压机械噪声声功率级测量方法 GB28244 自动锻压机安全技术要求 GB/T28245 自动锻压机噪声限值 JB/T1829 锻压机械通用技术条件 JB/T5775 锻压机械灰铸铁件技术条件 JB/T6580.1一2014开式压力机第1部分:技术条件 JB/T8356机床包装技术条件 JB/T 8609 锻压机械焊接件技术条件
型式与基本参数
3
3.1 自动弯曲机的型式如图1所示。
I
JB/T3884—2017
图1
3.2 自动弯曲机的主参数为线材最大直径。 3.3 自动弯曲机的基本参数应符合表1的规定。
表 1
参数值
参数名称
3 16 40 63 10 40 1.5 150
4.5 25 45 100 20 50 2.0 180
6
8
2 10 3.5 40 10 30 1.0 100
线材最大直径 mm
1
40 50 160 25 60 2.5 210
63 60 250 30 70 3.0 240
6.3
最大弯曲力KN 弯曲滑块行程压力机公称力 KN 压力机滑块行程 mm
30 25 5 20 0.5 60
带料最大宽度 mmn
带料最大厚度 mm
最大送料长度 mm
4精度
4.1检验要求 4.1.1精度检验前,应调整自动弯曲机的安装水平,在自动弯曲机底座上平面放置水平仪,水平仪的读数不应超过0.20/1000。 4.1.2当被检平面最大外形尺寸L≤1000mm时,在距边缘0.1L的范围内不检测,当最大外形尺寸 L>1000mm时,在距边缘100mm的范围内不检测。 4.1.3检验应符合GB/T10923的规定。 4.2几何精度检验
几何精度检验应符合表2的规定。
2
JB/T3884—2017
表2
单位为毫米
检验工具
序号
简图
检验项目
允差
检验方法
按GB/T10923—2009 的5.3.2.2,在被检平面上选择a、b、c三点作为测量基准【见图a],将三个等高量块放在这三点上。通过可调量块确定延伸点d。将平尺放在a、b、C、d的任意两
最大外形尺寸
允差
≤400
0.04
a)
弯曲滑块安装平面的平面度
平尺、
>400~630 0.05 量块、 点上即可测得被检面上
G1
C
各点的偏差误差以各偏差的最大代数差值计尺寸大于1600mm的平面按GB/T10923 2009中5.3.2.4.1用水平仪检验【见图b】】 允许在装配前进行检验按GB/T10923—2009 中5.4.2.2.1检验,将检验棒紧固在弯曲滑块上,指示器固定在检验棒上,指
指示器
>630~1 000 0.07 >1000~1 600 0.10
>1 600 0.12
b
允差
行程
弯曲滑块行程对弯曲滑块安装平面的平行度
G2
0.02 指示器 示器测头垂直触及安装
≤40
平面。在各弯曲滑块的行程内分别进行测量误差以指示器的最大读数差值计
0.03
>40
按GB/T10923—2009 中5.5.2.2.1检验,在最
允差
行程
大和最小装模高度进行测量在工作台上放一直角尺,将指示器紧固在滑块上,使其测头触在直
压力机滑块行程对工
作台面的垂 ≤10 0.01 直角尺、
G3
指示器 角尺检验面,当滑块自
直度
上死点向下运行时,按图a)、图b)两个方向分别进行测量误差以指示器的最大读数差值计
0.02
>10
b)
3
JB/T3884—2017
表2(续)
单位为毫米
检验工具
简图
允差下平面最大 允
检验方法
序号
检验项目
按GB/T10923—2009 中5.4.1.2.1检验,将检验棒紧固在弯曲滑块上,指示器固定在检验棒上,指示器测头垂直触及安装平面,在各弯曲滑块的行程内分别进行测量误差以指示器的最大读数差值计
差 0.03
尺寸 ≤100
压力机滑块下平面对工作台面的平行度
>100~160 0.04 指示器
G4
>160~250 0.05
0.06
a)
b)
>250
4.3送料精度检验
送料精度检验应符合表3的规定。
表3
单位为毫米
序号
检验项目
检验工具
简图
允差
检验方法取自动弯曲机所允许的带料最大厚度的钢带,以中等速度在Q235 钢带上冲20个圆孔。其
允差 0.05
孔距L
$10
≤30
送料长度变动量
>30~50 0.06 游标卡尺 孔距L为最大送料长度
P
的一半,用游标卡尺测量各相邻两孔的孔距误差值以最大读数差值计
>50~80
0.07
0.09
>80
5技术要求
5.1一般要求 5.1.1 自动弯曲机应符合本标准的规定,并按照经规定程序批准的图样及技术文件制造。 5.1.2 设计应考虑人类工效学的要求,外形美观,便于使用、维修、装配、拆卸和运输。 5.1.3备件、附件、工具应能互换,并符合技术文件的规定。 5.1.4 随机技术文件应包括合格证明书、装箱单和使用说明书。使用说明书的内容应包括性能及结构简介、安装、运输、贮存、使用、维修和安全等规定。 5.2安全防护 5.2.1 自动弯曲机的安全防护应符合GB28244的规定。
4
JB/T3884—2017
5.2.2压力机应有可靠的过载保险装置。 5.3铸件、锻件和焊接件 5.3.1自动弯曲机的灰铸铁件应符合JB/T5775的规定。 5.3.2自动弯曲机的焊接件应符合JB/T8609的规定。 5.3.3重要铸件、锻件、焊接件应取得合格证明。 5.3.4机身、送料箱体、压力机机身、压力机滑块、曲轴、中心齿轮等重要铸件、锻件、焊接件,应进行去应力处理。 5.4加工 5.4.1零件的加工应符合JB/T1829的规定。 5.4.2重要摩擦副,包括压力机曲轴与连杆瓦、滑块与导轨、弯曲滑块与导轨、送料滑块与滑杆等,应采取耐磨措施。 5.5装配 5.5.1装配应符合JB/T1829的规定。 5.5.2在部装和总装时,不允许安装图样上没有的垫片等零件。 5.5.3机身与送料箱体机身与底座的固定结合面应紧密贴合。用0.05mm塞尺检验,塞尺塞入的深度不得超过接触面宽度的20%,塞尺塞入的累计长度不得超过周长的10%。 5.5.4手轮、手柄的反向空程量应不大于1/10转。 5.6电气设备
自动弯曲机的电气设备应符合GB5226.1的规定。 5.7润滑系统 5.7.1自动弯曲机的润滑系统应符合GB/T6576的规定。 5.7.2自动弯曲机一般应采用集中润滑。 5.7.3自动弯曲机应有润滑标牌,标牌上应注明润滑部位。 5.8外观 5.8.1外露表面不应有图样未规定的凸起、凹陷和粗糙不平。 5.8.2防护罩应平整、美观。 5.8.3零部件外露接合面的边缘要整齐、匀称,不应有明显的错位,其错位和不匀称量不应超过表4 的规定。
表4
单位为毫米
结合面边缘及门盖边缘尺寸(长边)
错位量 1.5 2.0 3.0
错位不匀称量 贴合缝隙量 缝隙不匀称量
≤500 >500~1250 >1250
1.0 1.0 1.5
1.0 1.5 2.0
1.0 1.5 2.0
5.8.4涂漆应符合技术文件的规定。金属表面不同颜色油漆分界线应清晰,可拆卸的装配接合面的接缝处,在涂漆后应切开,切开时不应扯破边缘。 5.8.5外露的焊缝应修整平直、均匀。
5