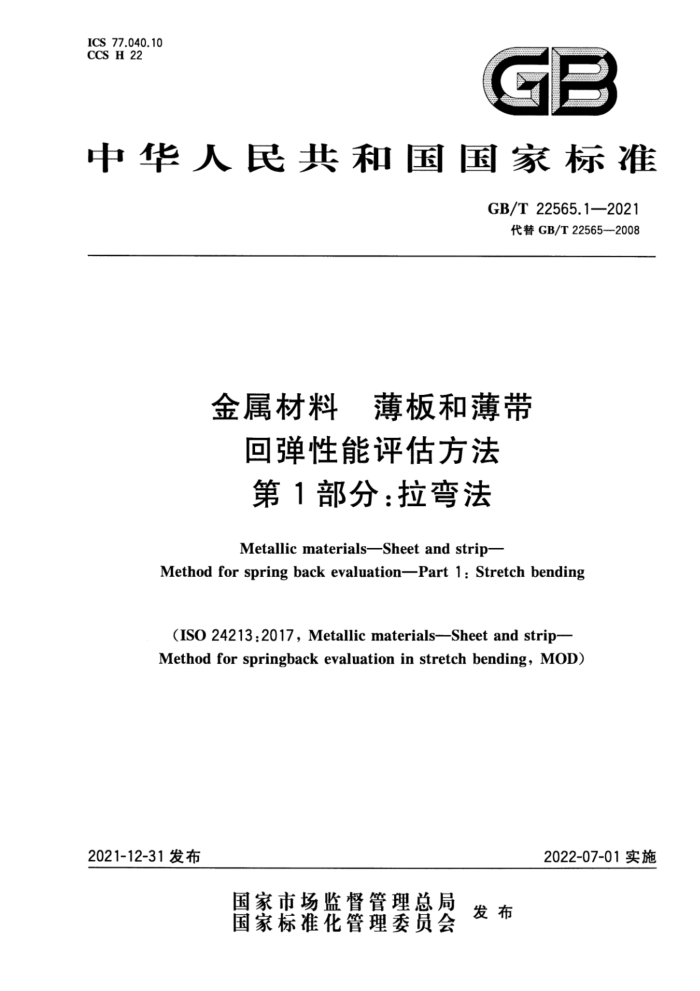
ICS 77.040.10 CCS H 22
GB
中华人民共和国国家标准
GB/T22565.1—2021
代替GB/T22565——2008
金属材料 薄板和薄带
回弹性能评估方法第1部分:拉弯法
Metallic materials-—Sheet and strip-
Method for spring back evaluation-Part 1: Stretch bending
(ISO 24213:2017, Metallic materials-Sheet and strip- Method for springback evaluation in stretch bending, MOD)
2021-12-31发布
2022-07-01实施
国家市场监督管理总局国家标准化管理委员会
发布
GB/T 22565.1—2021
前言
本文件按照GB/T1.1一2020《标准化工作导则第1部分:标准化文件的结构和起草规则》的规定起草。
本文件是GB/T22565《金属材料 +薄板和薄带回弹性能评估方法》的第1部分。GB/T22565 已经发布了以下部分:
一第1部分:拉弯法。 本文件代替GB/T22565一2008《金属材料薄板和薄带拉弯回弹评估方法》。与GB/T22565
-
2008相比,除结构调整和编辑性改动外,主要技术变化如下:
增加了试样的标识[见图2b)]; -增加了试样要求(见第7章);增加了试验程序(见第8章);在试验报告中增加了“试样相对于材料轧制方向的截取方向”(见第9章)。
本文件修改采用ISO24213:2017《金属材料薄板和薄带拉弯回弹评估方法》。 本文件与ISO24213:2017相比存在技术性差异,这些差异涉及的条款已通过在其外侧页边空白位
置的垂直单线(I)进行了标示,具体的技术性差异及其原因如下:
规范性引用文件用GB/T8170替换了ISO80000-1,以适应我国的技术条件、增加可操作性; -在试验报告中增加了“本文件编号”牌号、状态”,以符合我国国情。
本文件做了下列编辑性修改:
为与现有标准协调,将标准名称改为《金属材料薄板和薄带回弹性能评估方法第1部分:拉弯法》;在数值修约要求处增加了“建议保留三位有效数字”的注。
-
请注意本文件的某些内容可能涉及专利。本文件的发布机构不承担识别专利的责任。 本文件由中国钢铁工业协会提出。 本文件由全国钢标准化技术委员会(SAC/TC183)归口。 本文件起草单位:宝山钢铁股份有限公司、东莞材料基因高等理工研究院、浙江省特种设备科学研
究院、深圳万测试验设备有限公司、广州汽车集团股份有限公司、冶金工业信息标准研究院、上海海洋高端装备功能型平台有限公司。
本文件主要起草人:祝洪川、李荣锋、葛翔、吕超、董莉、黄星、李途、余立、陈麒琳、周路海、刘冬汤杰、侯慧宁、汪宏斌。
本文件于2008年首次发布,本次为第一次修订。
I
GB/T22565.1—2021
引言
在金属薄板和薄带的成形过程中,当零件从模具上取下来后,由于弹性回复,成形后零件的几何形状会不同于设计的几何形状,这种现象被称为回弹。
GB/T22565将规范金属薄板和薄带的回弹试验和检测方法,使我国的金属薄板和薄带成形性能试验标准更加完善,指导相关试验分析,推动行业发展,提升我国金属薄板和薄带研究的技术水平。
GB/T22565拟由两部分构成。 第1部分:拉弯法。规范金属薄板在平面应变拉弯变形方式下的回弹量评估方法。
第2部分:拉延法。规范金属薄板和薄带在已知能够表现出显著回弹的拉延弯曲变形方式下的回弹角评估方法。
本文件是为了评估金属薄板和薄带拉弯变形中的回弹量而建立。它可以用于材料表征、成形过程控制、模具设计或有限元程序的校准。
=
GB/T22565.1—2021
金属材料薄板和薄带
回弹性能评估方法第1部分:拉弯法
1范围
本文件规定了金属薄板和薄带在平面应变拉弯变形方式下的回弹性能评估方法。平面应变拉弯是一种典型的冲压成形件变形方式,能够表现出显著回弹量。应用本方法可准确定量评估拉弯回弹量。
本文件适用于金属薄板和薄带有回弹控制需求的材料表征、成形过程控制、模具设计和有限元程序校准。
规范性引用文件
2
下列文件中的内容通过文中的规范性引用而构成本文件必不可少的条款。其中,注日期的引用文件,仅该日期对应的版本适用于本文件;不注日期的引用文件,其最新版本(包括所有的修改单)适用于本文件。
GB/T8170 数值修约规则与极限数值的表示和判定
3 术语和定义
下列术语和定义适用于本文件。
3.1
曲率 curvature K 拉弯试样内表面中间沿纵向测定的曲率半径的倒数。 注:见公式(1)。
1
(1)
K =
r
3.2
回弹量 amount of springback n 试样加载和卸载后曲率的相对变化。 注:见公式(2),如图1所示。
("—)
(2)
7=
K
1
GB/T22565.1—2021
加载时
b) 卸载后
a)
图1 试样加载时和卸载后的曲率半径
3.3
拉弯stretchbending 在试样承受拉伸力时进行弯曲的方法。
3.4
单位面积压边力 blank holding pressure p 作用于试样厚度方向的力除以试样同模具的接触面积。 注:单位面积压边力的计算方法见附录A。
3.5
名义拉伸应力 norminal tensile stress T 试样单位横截面上的拉力。 注:名义拉伸应力的计算方法见附录B。
符号和说明
4
本文件使用的符号和说明见表1。
表1 符号和说明
符号 a 试样厚度 b 试样宽度 Fs 压边力 h 冲头行程 Fp 冲压力 p 单位面积压边力 Rp 冲头半径
说明
单位 mm mm N mm N MPa mm mm mm
试样在加载时内表面的曲率半径
r' 试样卸载后内表面的曲率半径
2
GB/T22565.1—2021
表1 符号和说明(续)
符号 rd s T 作用于试样的名义拉伸应力 W 模具间距 w
说明
单位 mm mm? MPa mm mm mm mm"! mm=1
凹模圆角半径试样与模具的总接触面积
用于测量试样卸载后曲率的量规的基准座宽度,见附录C 用于测量试样卸载后曲率的量规测量得到的数值(图C.1中AD的长度) 试样加载时内表面的曲率(=r-1)
1 X k' 试样卸载后内表面的曲率[=(r")-1]
回弹量
7 28 试样沿冲头的张开角度注:1MPa=1N/mm。
rad
5 原理
试验采用拉弯方法评估金属薄板和薄带的回弹性能。回弹量通过测定试样加载时和卸载后曲率的相对变化来确定(见3.1和3.2)。作用于试样上的名义拉伸应力利用冲头行程和冲压力的测量值来确定(见附录B)。
6 试验设备
6.1 回弹评估拉弯试验装置
试验中用到的一个拉弯试验装置示例,如图2所示。半圆柱冲头半径应为(100土1)mm。其半径和尺寸公差可由相关方协议确定。
3
GB/T22565.1—2021
单位为毫米
600
019
b) 模具装配
a)试验装置
标引序号说明: 1- 力传感器; 2- 一压边力; 3- —凹模顶板;
一凹模; 5- 压边模;
M
冲头(R100);凹模底板;拉延筋;一试样。
6
8
9-
图2回弹评估拉弯试验装置示例
6.2测量试样曲率半径的装置
曲率半径测量原理如附录C所示,所使用的量规分辨率应为0.001mm。也可采用光学测微计及其他非接触测量探头。
7试样
用于试验的试样要求如下:
GB/T22565.1—2021
a)应为长(500士10)mm,宽(50士1)mm的矩形; b)厚度应为薄板或薄带的原始厚度; c)J 应按相关方协议确定的平行或垂直于轧制方向裁剪; d) 边部应为剪切边;除非另有规定或是由剪切导致的,试样应避免不必要的改变或受热; e) 表面应没有可能影响试验结果的缺陷,如划痕。
8试验程序
试验应遵循如下步骤。 a)i 试验温度:通常在10℃~35℃环境温度下进行试验,如有必要,应记录温度。对温度有严格
要求的试验,应在(23士5)℃范围内进行。 b) 拉弯试验:试样应置于压边模上(见图2),然后对试样施加压边力,按照附录A计算单位面积
压边力,最大单位面积压边力应在试验材料抗拉强度的2%~3%范围内。冲头运动直到冲头行程(h)达到预定的数值。应确定冲头行程大小以便试样沿冲头的张开角度(2)不小于120 (见图B.1),润滑剂应由相关方协议确定。试样与冲头之间的摩擦应尽可能小,摩擦系数宜小于0.05,则名义拉伸应力能够均匀分布于冲头上的试样中。建议采用聚合薄膜和机油作为冲压表面的润滑剂。使用聚合薄膜润滑时,每次试验都要用新的。冲头行程(h)和冲压力(Fp)应分别采用位移计和力传感器测量。用于冲头行程测量的位移计和用于冲压力测量的力传感器的分辨力宜分别小于0.5mm和100N。
c) 名义拉伸应力计算:应按附录B计算。 d) 曲率半径的测定和回弹计算:试样卸载后内表面的曲率半径(r")应按附录C的规定用量规在
拉弯试样中间沿纵向测定。试样加载时内表面的曲率半径(r)应为冲头顶部的半径。回弹量 (n)采用公式(2)计算。测量试样卸载后曲率的量规基准座宽度(w)建议取20mm(见附录 C)。这是基于对前期试验的观察,试样回弹后的曲率在试样中间20mm区域几乎是一致的。
e)1 修约:测量数据应根据GB/T8170进行修约。 注:保留三位有效数字。
试验报告
9
如需试验报告,报告包含的项目应由相关方协议确定并从下列项目中选取: a)本文件编号; b)测试条件:冲头半径、冲头行程、润滑剂、聚合薄膜的类型和厚度、冲压力、单位面积压边力,试
样相对于材料轧制方向的截取方向; c)i 试验结果:名义拉伸应力、回弹量(); d)i 试验材料类型、厚度、牌号、状态; e) 测量不确定度(或者精密度和偏差)的评定。
5