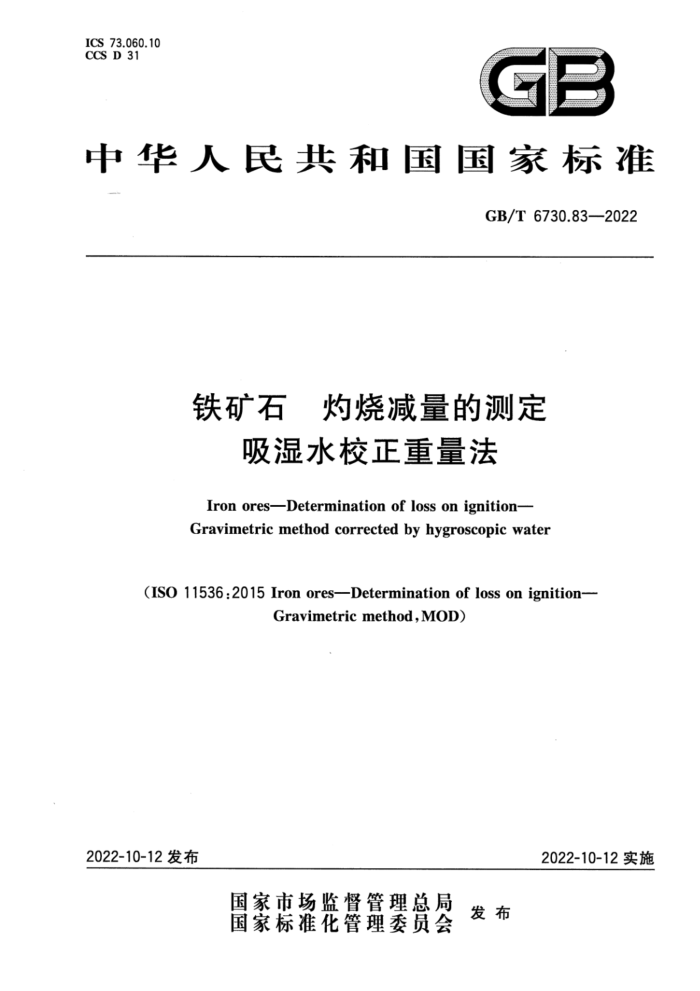
ICS 73.060.10 CCS D 31
G
中华人民共和国国家标准
GB/T6730.83—2022
铁矿石 灼烧减量的测定
吸湿水校正重量法
Iron ores—Determination of loss on ignition- Gravimetric method corrected by hygroscopic water
(ISO 11536:2015 Iron ores—Determination of loss on ignition-
Gravimetricmethod,MOD)
2022-10-12实施
2022-10-12发布
国家市场监督管理总局国家标准化管理委员会
发布
GB/T 6730.83—2022
前言
本文件按照GB/T1.1一2020《标准化工作导则第1部分:标准化文件的结构和起草规则》的规定起草。
本文件是GB/T6730的第83部分,GB/T6730已经发布的部分见附录A。 本文件修改采用ISO11536:2015《铁矿石灼烧减量的测定重量法》。 本文件与ISO11536:2015相比做了下述结构调整:
本文件增加了“术语和定义”一章。 附录B对应ISO11536:2015中的附录A。
本文件与ISO11536:2015中的技术差异及其原因如下:
-增加了对“GB/T6730.1”和“GB/T8170”的规范性引用(见第7章、9.2.5);以适应我国的技术条件;更改了实验室试样的制备(见第7章,ISO11536:2015的第6章),明确了具体要求,便于实际操作;
-增加了空气平衡样的制备方法(见8.1,IS011536:2015的7.1),原因是有必要规定制备空气
平衡样的具体要求;更改了试验终点的判定(见8.5,ISO11536:2015的7.5),以提高判定的准确性,并与 GB/T10322.5中水分测定终点的判定方式保持一致;更改了精密度的表达(见9.2.1,ISO11536:2015的8.2.1)和正确度检查中的C值的计算公式(见9.2.4,ISO11536:2015的8.2.4),以符合我国国家标准关于精密度的表达要求;更改了数值修约的表述(见9.2.5,ISO11536:2015的8.2.5),用GB/T8170代替ISO11536: 2015的8.2.5的文字描述。
本文件做了下列编辑性改动:
更改了标准名称;更改了灼烧减量的表示符号和公式(2)(见9.1,IS011536:2015的8.1); -增加了附录A“GB/T6730的组成文件”;增加了附录C“精密度试验原始数据”;删除了“参考文献”。
请注意本文件的某些内容可能涉及专利。本文件的发布机构不承担识别专利的责任。 本文件由中国钢铁工业协会提出。 本文件由全国铁矿石与直接还原铁标准化技术委员会(SAC/TC317)归口。 本文件起草单位:宁波检验检疫科学技术研究院、青岛远诚纵横科技有限公司、冶金工业信息标准
研究院、青岛理工大学、上海海关工业品与原材料检测技术中心、宝山钢铁股份有限公司、嵊泗海关综合技术服务中心、宁波市产品食品质量检验研究院。
本文件主要起草人:陈贺海、杨辉、王晶、陈雯、张爱珍、沙芬、廖海平、朱融、付冉冉、闵红、张庆建、 陈海岚、应海松。
I
GB/T 6730.83—2022
引 言
铁矿石是钢铁工业的主要原材料,在钢铁领域标准体系中,铁矿石化学成分测定方法标准体系是其中非常重要的部分,在保证铁矿石产品质量方面发挥着重要作用,该系列方法标准服务于铁矿石的生产、贸易和应用,为我国钢铁工业高质量发展提供技术支撑。
GB/T6730包括了铁矿石化学成分测定方法系列标准,分别规定了铁矿石产品中水分、全铁、金属铁、亚铁、硅、铝、钙、镁、硫、磷、锰、钛、稀土总量、钡、铬、钒、锡、铜、钴、镍、锌、锯、铋、钾、钠、碳、铅、砷、 镉、汞、氟、氯、灼烧减量和化合水等化学成分的测定方法。
1986年,GB/T6730首次发布了51项铁矿石化学成分测定方法国家标准,随着铁矿石领域分析技术的发展和生产实际需求,经过多年来持续不断地制修订工作,形成了目前比较完善的标准体系,现行的GB/T6730组成文件详见附录A。
GB/T6730.83给出吸湿水校正重量法测定铁矿石中灼烧减量的方法。
I
GB/T6730.83—2022
铁矿石灼烧减量的测定
吸湿水校正重量法
警示一使用本文件的人员应有正规实验室工作的实践经验。本文件并未指出所有可能的安全问题。使用者有责任采取适当的安全和健康措施,并保证符合国家有关法规规定的条件。
1范围
本文件规定了吸湿水校正重量法测定铁矿石中灼烧减量。 本文件适用于天然铁矿石、铁精矿和人造块铁矿,测定范围(质量分数):1.0%~10.0%。 以下情况不适用本文件: a)含有金属铁的加工铁矿石(直接还原铁); b)硫含量超过0.2%的天然或加工铁矿石; c)氧化亚铁含量超过1.0%(质量分数)的天然或加工铁矿石。
2规范性引用文件
下列文件中的内容通过文中的规范性引用而构成本文件必不可少的条款。其中,注日期的引用文件,仅该日期对应的版本适用于本文件;不注日期的引用文件,其最新版本(包括所有的修改单)适用于本文件。
GB/T6730.1铁矿石分析用预干燥试样的制备(GB/T6730.1--2016,ISO7764:2006,MOD) GB/T6730.3铁矿石分析样中吸湿水分的测定重量法、卡尔费休法和质量损失法
(GB/T6730.3—2017,ISO2596:2006,MOD)
GB/T8170数值修约规则与极限数值的表示和判定 GB/T10322.1铁矿石取样和制样方法(GB/T10322.1--2014,ISO3082:2009,IDT)
3术语和定义
本文件没有需要界定的术语和定义。
4原理
试料在1000℃灼烧至恒重,并在干燥器中冷却。测定试料的质量损失,并表示为相对于原始质量的质量分数,即灼烧减量。
5试剂
分析过程中除另有说明外,仅使用认可的分析纯试剂。 硅胶干燥剂,105℃干燥4h。
1
GB/T 6730.83—2022
6仪器
6.1埚(瓷埚或铂埚):容量为15mL~25mL,带盖。埚及其盖子应在1000℃的马弗炉中预处理60min。使用前,埚及其盖子应存放在真空干燥器(见6.4)中。如果用于灼烧减量分析的铂用于熔剂熔融,应彻底清洁铂器皿,以防止交叉污染。 6.2天平:感量0.1mg。 6.3马弗炉:能够保持1000℃士25℃的温度,并提供足够的空气循环,以防止水蒸气滞留。 6.4真空干燥器:内径150mm~250mm,带真空旋塞,可保持空气压力平衡。干燥器底盘应为金属、 陶瓷或其他耐热材料,在1000℃C下与埚接触时不会破裂。干燥器边缘应涂上少量硅脂或凡士林。 每天应更换150g200g硅胶(见第5章)。如果使用铂埚,则不应使用金属干燥器底盘。
7实验室试样的制备
按照GB/T10322.1进行取制样。一般试样粒度应小于100μm。如试样中化合水或易氧化物含量高时,其粒度应小于160μm。
化合水和易氧化物含量高的规定按照GB/T6730.1进行。
8分析步骤
8.1试样
充分混匀实验室试样(见第7章),分取多份试料,确保每个试料都能代表实验室样品。试料应进行空气平衡。
空气平衡是将试验样品平铺在托盘中,样层密度不大于0.1g/cm,实验室环境下空气平衡2h,测试前快速混匀。 8.2测定次数
按照附录B,对同一试样,至少独立测定两次。 注:“独立”是指再次及后续任何一次测定结果不受前面测定结果的影响。本分析方法中,此条件意味着在同一实
验室,由同一操作员使用相同的设备、按相同的测试方法,在短时间内对同一被测对象独立进行重复测定,包括进行适当的再校准。
8.3吸湿水的测定
应同步对两份平行试料进行测定,一份用于测定灼烧减量,另一份用于测定吸湿水,吸湿水测定按照GB/T6730.3进行。 8.4试料量
称取约2.0g士0.2g试料(见8.1),精确至0.0001g。 8.5测量
将试料置于盖有盖子的埚(见6.1)中,放人马弗炉(见6.3)内,1000℃土25℃灼烧60min士10min (确保马弗炉腔内没有可能黏附在埚上的松散材料)。将埚从马弗炉中取出,放人干燥器(见6.4),并立即将盖子放在埚上,冷却至室温。缓慢卸压,取出并快速完成称量。如此反复操作,直至两次连
2
GB/T 6730.83—2022
续灼烧后质量差不超过试料初始质量的0.05%为止,以最后一次灼烧后的质量为计算依据。
试料称量与空埚称量的操作温度和速度尽可能保持一致。
9结果计算及其表示
9.1灼烧减量的计算
灼烧减量(LOI)以质量分数表示,按干基计算。 总的灼烧减量(LOI),包括水分,以质量分数表示,按式(1)计算:
m2 - ms × 100
LOI=
....(1)
m2-m1
式中: m," 埚和盖子的质量,单位为克(g); m2" 埚、盖子和空气平衡试料的质量,单位为克(g); ms 灼烧后、盖子和试料的质量,单位为克(g)。 吸湿水校正后的试料灼烧减量(LOI)按式(2)计算:
LOI -WM ×100 100-WM
LOI=
(2)
式中: WM 吸湿水的量,以质量分数表示。
9.2 分析结果的一般处理 9.2.1 精密度
本文件的精密度函数关系式见表1。
表1精密度函数关系式
灼烧减量(质量分数)/%
重复性限r r=0.05164+0.00323X
再现性限R
1.0~10.0
R=0.05302+0.00509X
注:式中X是分析结果的平均值(质量分数)。
9.2.2分析结果的确定
按照附录B的步骤,根据式(2)计算独立重复测量的结果,与重复性限r做比较,确定最终分析结果μ。 9.2.3实验室间精密度
实验室间精密度用以评价两个实验室报告的最终结果之间的一致性。两个实验室按照9.2.2中规定的相同步骤报告结果后,按式(3)计算:
μ1 +μ2
..(3)
μ12 = 2
式中: μ12 最终结果的平均值; μ1 实验室1报告的最终结果;
3
GB/T 6730.83—2022
附录A (资料性)
GB/T6730的组成文件
:
GB/T6730的组成文件如下:
GB/T6730.1—2016 铁矿石 分析用预干燥试样的制备 GB/T6730.22018 铁矿石 水分含量的测定重量法 GB/T6730.3—2017 铁矿石 分析样中吸湿水分的测定 重量法、卡尔费休法和质量损失法 GB/T6730.5—2007 铁矿石 全铁含量的测定 三氯化钛还原法 GB/T6730.6—2016 铁矿石 金属铁含量的测定 三氯化铁-乙酸钠滴定法 GB/T6730.7—2016 铁矿石 金属铁含量的测定 磺基水杨酸分光光度法 GB/T6730.8—2016 铁矿石 亚铁含量的测定 重铬酸钾滴定法 GB/T6730.9—2016 铁矿石 硅含量的测定 硫酸亚铁铵还原-硅钼蓝分光光度法 GB/T6730.10—2014 铁矿石 硅含量的测定 重量法 GB/T 6730.11—2007 铁矿石 铝含量的测定 EDTA滴定法 GB/T6730.12—2016 铁矿石 铝含量的测定 铬天青S分光光度法 GB/T6730.13—2007 铁矿石 钙和镁含量的测定 EGTA-CyDTA滴定法 GB/T6730.14—2017 铁矿石 钙含量的测定 火焰原子吸收光谱法 GB/T6730.16—2016 铁矿石 硫含量的测定 硫酸锁重量法 GB/T6730.17—2014 铁矿石 硫含量的测定 燃烧碘量法 GB/T6730.18—2006 铁矿石 磷含量的测定 钼蓝分光光度法 GB/T6730.19-—2016 铁矿石 磷含量的测定 铋磷钼蓝分光光度法 GB/T6730.202016 铁矿石 磷含量的测定 滴定法 GB/T6730.21—2016 铁矿石 锰含量的测定 高碘酸钾分光光度法 GB/T6730.22—2016 铁矿石 钛含量的测定 二安替吡啉甲烷分光光度法 GB/T6730.23—2006 铁矿石 钛含量的测定 硫酸铁铵滴定法 GB/T6730.24—2006 铁矿石 稀土总量的测定 萃取分离-偶氮氯麟mA分光光度法 GB/T6730.25—2021 铁矿石 稀土总量的测定 草酸盐重量法 GB/T6730.26—2017 铁矿石 氟含量的测定 硝酸钰滴定法 GB/T6730.27—2017 铁矿石 氟含量的测定 -茜素络合腺分光光度法 GB/T6730.28—2021 铁矿石 氟含量的测定 离子选择电极法 GB/T6730.29—2016 铁矿石 锁含量的测定 硫酸锁重量法 GB/T6730.30—2017 铁矿石 铬含量的测定 二苯基碳酰二肼分光光度法 GB/T6730.31—2017 铁矿石 钒含量的测定 N-苯甲酰苯眩萃取分光光度法 GB/T6730.32—2013 铁矿石 钒含量的测定 硫酸亚铁铵滴定法 GB/T6730.34—2017 铁矿石 锡含量的测定 邻苯二酚紫-溴化十六烷基三甲胺分光光度法 GB/T6730.35—2016 铁矿石 铜含量的测定 双环已酮草酰二腺分光光度法 GB/T6730.36—2016 铁矿石 铜含量的测定 火焰原子吸收光谱法 GB/T6730.37—2017 铁矿石 钻含量的测定 4-[(5-氯-2-吡啶)偶氮]-1,3-二氨基苯分光光
度法
GB/T6730.38—2017 铁矿石 钻含量的测定 亚硝基-R盐分光光度法 GB/T 6730.39-2017 铁矿石 镍含量的测定 丁二酮分光光度法
5