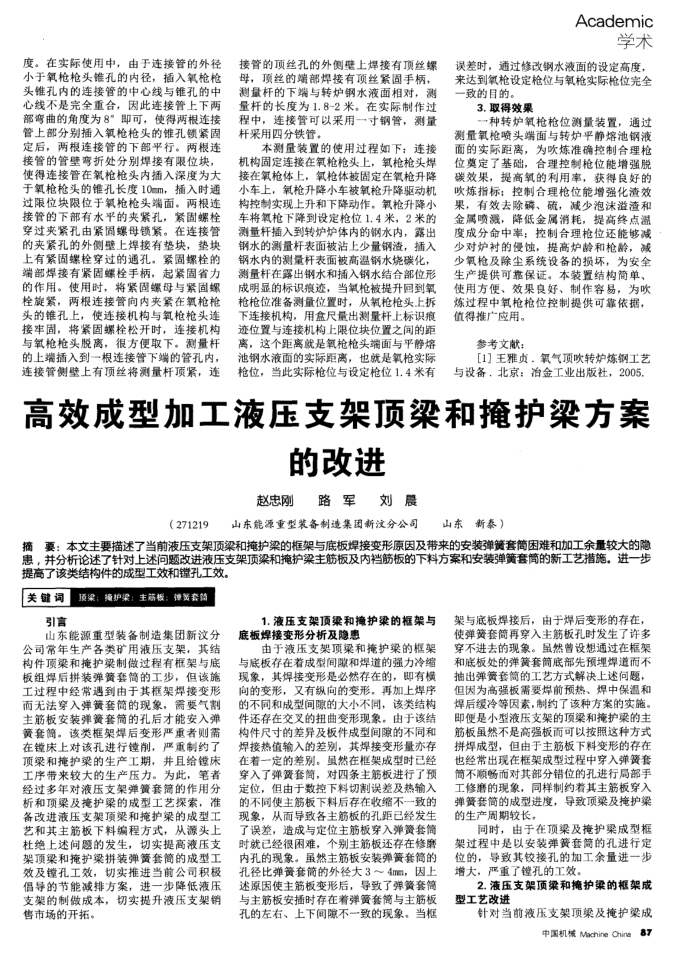
度。在实际使用中,由于连接管的外径小于氧枪枪头锥孔的内径,插入氧枪枪头锥孔内的连接管的中心线与锥孔的中心线不是完全重合,因此连接管上下两部弯曲的角度为8°即可,使得两根连接管上部分别插入氧枪枪头的锥孔锁紧固定后,两根连接管的下部平行。两根连接管的管壁弯折处分别焊接有限位块,使得连接管在氧枪枪头内插入深度为大于氧枪枪头的锥孔长度10mm,插入时通过限位块限位于氧枪枪头端面。两根连接管的下部有水平的夹紧孔,紫固螺栓穿过夹紧孔由紧固螺母锁紧。在连接管的夹紧孔的外侧壁上焊接有整块,垫块上有紧固螺栓穿过的通孔。紧固螺栓的端部焊接有紧固螺栓手柄,起紧固省力的作用。使用时,将紧固螺母与紧固螺栓靛紫,两根连接管向内夹紧在氧枪枪头的锥孔上,使连接机构与氧枪枪头连接牢固,将紧固螺栓松开时,连接机构与氧枪枪头脱离,很方便取下。测量杆的上端插入到一根连接管下端的管孔内,连接管侧壁上有顶丝将测量杆顶紧,连
接管的顶丝孔的外侧壁上焊接有顶丝螺母,顶丝的端部焊接有项丝紧固手柄,测量杆的下端与转炉钢水液面相对,测量杆的长度为1.8-2米。在实际制作过程中,连接管可以采用一寸钢管,测量杆采用四分铁管。
本测量装置的使用过程如下:连接机构固定连接在氧枪枪头上,氧枪枪头焊接在氧枪体上,氧枪体被固定在氧枪升降小车上,氧枪升降小车被氧枪升降驱动机构控制实现上升和下降动作。氧枪升降小车将氧枪下降到设定枪位1.4米,2米的测量杆插入到转炉炉体内的钢水内,露出钢水的测量杆表面被沾上少量钢渣,插入钢水内的测量杆表面被高温钢水烧碳化,测量杆在露出钢水和插入钢水结合部位形成明显的标识痕迹,当氧枪被提升回到氧枪枪位准备测量位置时,从氧枪枪头上拆下连接机构,用盘尺量出测量杆上标识痕迹位置与连接机构上限位块位置之间的距离,这个距离就是氧枪枪头端面与平静熔池钢水液面的实际距离,也就是氧枪实际枪位,当此实际枪位与设定枪位1.4米有
Academic
学术
误差时,通过修改钢水液面的设定高度,来达到氧枪设定枪位与氧枪实际枪位完全一致的目的。
3.取得效果
一种转炉氧枪枪位测量装置,通过测量氧枪喷头端面与转炉平静熔池钢液面的实际距离,为吹炼准确控制合理枪位奠定了基础,合理控制枪位能增强脱碳效果,提高氧的利用率,获得良好的吹炼指标;控制合理枪位能增强化渣效果,有效去除磷、硫,减少泡沫溢渣和金属喷溅,降低金属消耗,提高终点溢度成分命中率:控制合理枪位还能够减少对炉衬的侵蚀,提高炉龄和枪龄,减少氧枪及除尘系统设备的损坏,为安全生产提供可靠保证。本装置结构简单、使用方便、效果良好、制作容易,为吹炼过程中氧枪枪位控制提供可靠依据,值得推产应用。
参考文献:
[1]王雅贞.氧气顶吹转炉炼钢工艺与设备,北京:冶金工业出版社,2005.
高效成型加工液压支架顶梁和掩护梁方案
的改进赵忠刚路军刘晨
(271219
山东新泰)
山东能源重型装备制造集团新汶分公司
摘要:本文主要描述了当前液压支架顶梁和掩护架的框架与底板焊接变形原因及带来的安装弹簧套简困难和加工余量较大的隐患,并分析论述了针对上述问题改进液压支架顶梁和掩护梁主筋板及内档筋板的下料方案和安装弹策套筒的新工艺措施,进一步提高了该类结构件的成型工效和镗孔工效。
顶梁:撞护梁:主筋板:弹黄套简
关键词
引言
山东能源重型装备制造集团新汉分公司常年生产各类矿用液压支架,其结构件顶梁和掩护梁制做过程有框架与底板组焊后拼装弹簧套简的工步,但该施工过程中经常遇到由于其框架焊接变形而无法穿入弹簧套简的现象,需要气割主筋板安装弹簧套简的孔后才能安入弹簧套筒。该类框架焊后变形严重者则需在镗床上对该孔进行镗削,严重制约了顶梁和掩护梁的生产工期,并且给镗床工序带来较大的生产压力。为此,笔者经过多年对液压支架弹簧套简的作用分析和顶梁及掩护梁的成型工艺探索,准备改进液压支架顶架和掩护梁的成型工艺和其主筋板下料编程方式,从源头上杜绝上述问愿的发生,切实提高液压支架顶梁和掩护梁拼装弹簧套简的成型工效及镗孔工效,切实推进当前公司积极倡导的节能减排方案,进一步降低液压支架的制做成本,切实提升液压支架销售市场的开拓。
1.液压支架顶梁和掩护梁的框架与底板焊接变形分析及隐惠
由于液压支架顶梁和捷护梁的框架与底板存在着成型间隙和焊道的强力冷缩现象,其焊接变形是必然存在的,即有模向的变形,又有纵向的变形,再加上焊序的不同和成型闻随的大小不同,该类结构件还存在交叉的扭曲变形现象。由于该结构件尺寸的差异及板件成型间隙的不同和焊接热值输入的差别,其焊接变形量亦存在着一定的差别。然在框架成型时已经穿入了弹簧套筒,对四条主筋板进行了预定位,但由于数控下料切割误差及热输入的不同使主筋板下料后存在收缩不一致的现象,从而导致各主筋板的孔距已经发生了误差,造成与定位主筋板穿入弹簧套筒时就已经很困难,个别主筋板还存在修磨内孔的现象。虽然主筋板安装弹簧套简的孔径比弹簧套简的外径大3~4mm,因上述原因使主筋板变形后,导致了弹簧套篇与主筋板安插时存在着弹簧套简与主筋板孔的左右、上下闻限不一致的现象。当框
架与底板焊接后,由于焊后变形的存在,使弹黄套简再穿入主筋板孔时发生了许多穿不进去的现象。虽然曾设想通过在框架和底板处的弹策套简底部先预埋焊道而不抽出弹费套筒的工艺方式解决上述问题,但因为高强板需要焊前预热、焊中保温和焊后缓冷等因素,制约了该种方案的实施。即便是小型液压支架的顶梁和捷护梁的主筋板虽然不是高强板面可以按照这种方式拼焊成型,但由于主筋板下料变形的存在也经常出现在框架成型过程中穿入弹簧套简不顺畅而对其部分错位的孔进行局部手工修磨的现象,同样制约着其主筋板穿入弹簧套简的成型进度,导致顶梁及掩护渠的生产周期较长
同时,由于在顶梁及掩护梁成型框架过程中是以安装弹黄套简的孔进行定位的,导致其铰接孔的加工余量进一步增大,严重了镗孔的工效。
2.液压支架顶梁和掩护梁的框架成型工艺改进
针对当前液压支架顶梁及掩护梁成
中国机械Machine China87