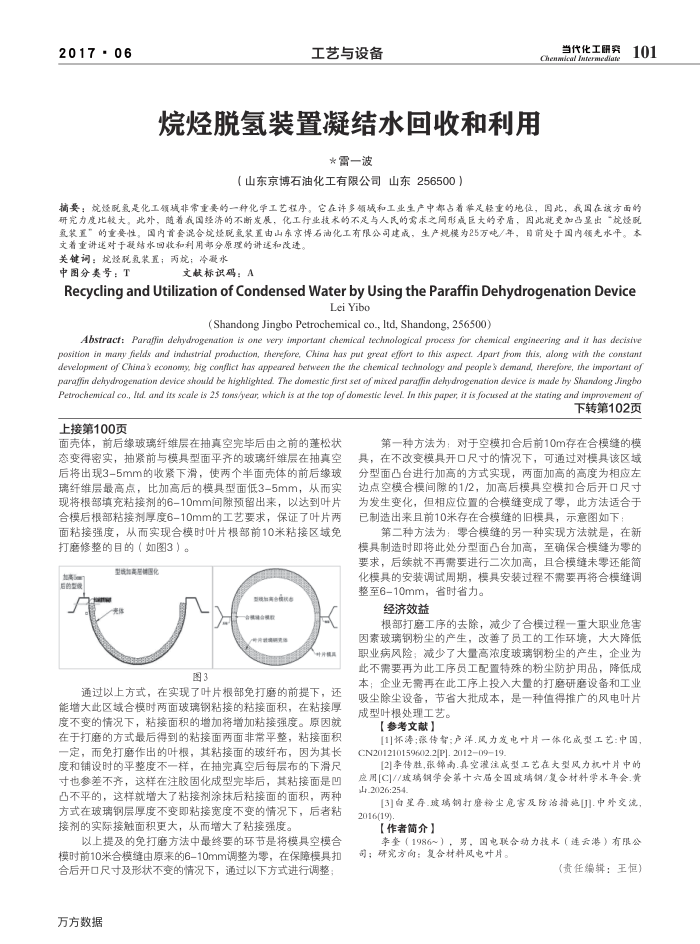
2017-06
工艺与设备
Chem
烷烃脱氢装置凝结水回收和利用
*雷一波
(山东京博石油化工有限公司山东256500)
当代化工研
101
摘要:烷烃配氢是化工领域非常重要的一种化学工艺程序。它在许多额域和工业生产中都占着举足轻重的地位,国此,我国在该方面的研究力度比较大,此外,随着我国经济的不断发展,化工行业技术的不足与人民的需求之间形成巨大的予盾,固此就更加吕星出“烷烃既氢装置”的重要性。国内首套混合烷烃脱氢装置由山东京博石油化工有限公司建成,生产规模为25万吨/年,助前处于国内领先水平。本
文着重讲述对于凝结水回收和利用部分原理的讲逐和改逐。关键词:烷经脱氢装置;丙烷;冷覆水
中图分美号:T
文献标识码:A
RecyclingandUtilizationofCondensedWaterbyUsingtheParaffinDehydrogenationDevice
Lei Yibo
(Shandong Jingbo Petrochemical co., Itd, Shandong, 256500)
Abstracf: Pargfin dehydrogenarion is one very imporfan chemical technological process for chemical engineering and it has decisive
position in mary fields and indaestrial prodnction, therefone, China has put gneal efort to this aspecf. Apart from this, along with the costan developmen of China 3 economy, big confict has appeared berween the rhe chemical technology and people 3 demand, zherefore, rhe importanr oy parafin dehydrogenarion device shourld be highlighted. The domestic first ser of mired parafin dekydrogenation device is made by Shandong Jingbo Petrochemical co., Itd. and its scale is 25 tons/jyear, which is at the top of domestic leveL. In zhis paper, it is focarsed ar the staring and improvemem of
下转第102页
上接第100页
面壳体,前后缘玻璃纤维层在抽真空完毕后由之前的蓬松状态变得密实,抽紧前与模具型面平齐的玻璃纤维层在抽真空后将出现3-5mm的收紧下滑,使两个半面壳体的前后缘玻璃纤维层最高点,比加高后的模具型面低3-5mm,从而实现将根部填充粘接剂的6-10mm间隙预留出来,以达到叶片合模后根部粘接剂厚度6-10mm的工艺要求,保证了叶片两面粘接强度,从面实现合模时叶片根部前10米粘接区域免打磨修整的目的(如图3)。
型线加高量销国R
型股加高含质状限
图3
通过以上方式,在实现了叶片根部免打磨的前提下,还能增大此区域合模时两面玻璃钢粘接的粘接面积,在粘接厚度不变的情况下,粘接面积的增加将增加粘接强度。原因就在于打磨的方式最后得到的粘接面两面非常平整,粘接面积一定,而免打磨作出的叶根,其粘接面的玻纤布,因为其长度和铺设时的平整度不一样,在抽完真空后每层布的下滑尺寸也参差不齐,这样在注胶固化成型完毕后,其粘接面是凹口不平的,这样就增大了粘接剂涂抹后粘接面的面积,两种方式在玻璃钢层厚度不变即粘接宽度不变的情况下,后者粘接剂的实际接触面积更大,从而增大了粘接强度。
以上提及的免打磨方法中最终要的环节是将模具空模合模时前10米合模缝由原来的6-10mm调整为零,在保障模具扣合后开口尺寸及形状不变的情况下,通过以下方式进行调整
方方数据
第一种方法为:对于空模扣合后前10m存在合模缝的模
具,在不改变模具开口尺寸的情况下,可通过对模具该区域分型面凸台进行加高的方式实现,两面加高的高度为相应左边点空模合模间隙的1/2,加高后模具空模扣合后开口尺寸为发生变化,但相应位置的合模缝变成了零,此方法适合于已制造出来且前10米存在合模缝的旧模具,示意图如下:
第二种方法为:零合模缝的另一种实现方法就是,在新模具制造时即将此处分型面凸台加高,至确保合模缝为零的要求,后续就不再需要进行二次加高,且合模缝未零还能简化模具的安装调试周期,模具安装过程不需要再将合模缝调整至6-10mm,省时省力。
经济效益
根部打磨工序的去除,减少了合模过程一重大职业危害因素玻璃钢粉尘的产生,改善了员工的工作环境,大大降低职业病风险;减少了大量高浓度玻璃钢粉尘的产生,企业为此不需要再为此工序员工配置特殊的粉尘防护用品,降低成本;企业无需再在此工序上投入大量的打磨研磨设备和工业吸尘除尘设备,节省大批成本,是一种值得推广的风电叶片成型叶根处理工艺。
【参考文献】
[1]怀涛;张传智;卢洋.风力发电叶片一体化成型工艺:中国, CN2012101596(02.2[P]. 20120919.
[2]李传胜,张锦南.真空灌注成型工艺在大型风力机叶片中的应用[C]//玻瑞钢学会第十六届全国玻璃钢/复合材料学术年会.黄山.2026:25-4.
[3]白星存.玻璃钢打磨粉尘危害及防治措范[川].中外交流, 2016(19)
【作者简介】
李奎(1986~),男,国电联含动力技术(连云港)有限公司;研究方向:复合材料风电叶片。
(责任编辑:王恒)