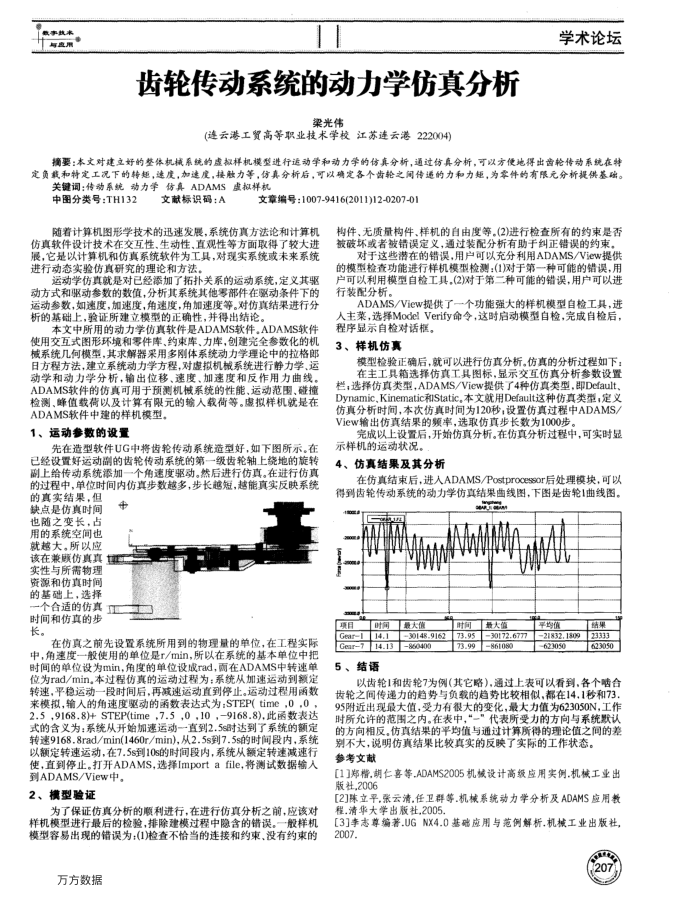
数字执本与度用
齿轮传动系统的动力学仿真分析
渠光伟
(连云港工贸高等职业授术学校江苏连云港222004)
学术论坛
损要:本文对建立好的整体机械系统的虚权样机模型进行运动争和动力学的仿真分新,通过仿真分析,可以方便地得出齿轮传动系统在特定负载和特定工况下的转矩,速度,加速度,接触力等,仿真分析后,可以确定各个齿轮之间传逐的力和力矩,为件的有限元分析提供基础。
关键调:传动系统动力季仿具ADAMS或拟样机
中图分类号:TH132
文献标识码:A
文章编号:1007-9416(2011)12-0207-01
随着计算机图形学技术的迅速发展,系统仿真方法论和计算机仿真软件设计技术在交互性、生动性,直观性等方面取得了较大进晨,它是以计算机和仿真系统软件为工具,对现实系统或未来系统进行动态实验仿真研究的理论和方法。
运动学仿真就是对已经添加了拓扑关系的运动系统,定义其驱动方式和驱动参数的数值,分析其系统其他零部件在驱动条件下的运动参数,如速度,加速度,角递度,角加速度等。对仿真结果进行分析的基础上,验证所建立模型的正确性,并得出结论。
本文中所用的动力学伤真软件是ADAMS软件。ADAMS软件使用交互式图形环境和零件库、约束库、力库,创建完全参数化的机械系统几何模型,其求解器采用多刚体系统动力学理论中的拉格郎日方程方法,建立系统动力学方程,对虚拟机械系统进行静力学、运动学和动力学分析,输出位移、速度、加速度和反作用力曲线。 ADAMS软件的伤真可用于预测机械系统的性能,运动范围,硅撞检测、峰值载荷以及计算有限元的输人载荷等。虑拟样机就是在
ADAMS软件中建的样机模型, 1、运动参数的设置
先在造型软件UG中将齿轮传动系统造型好,如下图所示。在已经设置好运动副的齿轮传动系的第一级齿轮轴上绕地的旋转副上给传动系统添加一个角速度驱动。然后进行仿真。在进行仿真的过程中,单位时间内仿真步数越多,步长越短,越能真实反映系统
的真实结果,但缺点是仿真时间也随之变长,占用的系统空间也就越大。所以应
该在兼顾仿真真证
实性与所需物理资源和仿真时间的基础上,选择一个合适的仿真时间和仿真的步长。
在伤真之前先设置系统所用到的物理量的单位,在工程实际中,角速度一般使用的单位是r/min,所以在系统的基本单位中把时间的单位设为min,角度的单位设成rad,两在ADAMS中转速单位为rad/min。本过程伤真的运动过程为:系统从加速运动到额定转速,平稳运动一段时间后,再减速运动直到停止。运动过程用函数来模拟,输人的角速度驱动的函数表达式为:STEP(time,00, 2.5,9168.8)+STEP(time,7.5,0,109168.8),此函数表达式的含义为:系统从开始加速运动一直到2.5s时达到了系统的额定转速9168.8rad/min(1460r/min),从2.5s到7.5s的时闻段内,系统以额定转速运动,在7.5s到10s的时间段内,系统从额定转速减速行使,直到停止。打开ADAMS,选择Importafile,将测试数据输人
到ADAMS/View中, 2、模型验证
为了保证仿真分析的顺利进行,在进行仿真分析之前,应该对样机模型进行最后的检验,排除建模过程中隐含的错误。一般样机模型容易出现的错误为:1)检查不恰当的连接和约束、没有约束的
万方数据
构件、无质量构件、样机的自由度等。(2)进行检查所有的约束是否被破坏或者被错误定义,通过装配分析有助于纠正错误的约束。
对于这些潜在的错误,用户可以充分利用ADAMS/View提供的模型检查功能进行样机模型检测:(1)对于第一种可能的错误,用户可以利用模型自检工具。(2)对于第二种可能的错误,用户可以进行装配分析,
ADAMS/View提供了一个功能强大的样机模型自检工具,进人主菜,选择ModelVerify命令,这时启动模型自检,完成自检后,
程序显示自检对话框。 3、样机仿真
模型检验正确后,就可以进行仿真分析。仿真的分析过程如下:在主工具箱选择仿真工具图标,显示交互仿真分析参数设置
栏,选择仿真类型,ADAMS/View提供了4种伤真类型,即Default、 Dynamic,Kinematic和Static,本文就用Default这种仿真类型,定义仿真分析时间,本次仿真时间为120秒,设置仿真过程中ADAMS/ View输出仿真结果的频率,选取仿真步长数为1000步
完成以上设置后,开始仿真分析。在仿真分析过程中,可实时显示样机的运动状况。
仿真结巢及其分析 4
在仿真结束后,进人ADAMS/Postprocessor后处理模块,可以得到齿轮传动系统的动力学仿真结果曲线图,下图是齿轮1曲线图。 0
我
项目
时间
最大衡
Gear114.1 Gear-714.13
5、结语
时间
30148.916273.95
860400
最大值
30172.6777
73.99
861080
结果
21832.180923333
623050
623050
以齿轮1和齿轮7为例(其它略),通过上表可以看到,各个啮合齿轮之间传递力的趋势与负载的趋劳势比较相似,都在14.1移和73. 95附近出现最大值,受力有很大的变化,最大力值为623050N,工作时所允许的范围之内。在表中,“二”代表所受力的方向与系统默认的方向相反,仿真结果的平均值与通过计算所得的理论值之间的差
别不大,说明仿真结果比较真实的反映了实际的工作状态。参考文献
[1]郑槽.胡仁喜等.ADAMS2005机械设计高级应用实例.机械工业出版社,2006
[2]陈立平.张云清.任卫群等.机械系统动力学分析及ADAMS应用款程.清华大学出版社,2005
[3]李志尊编著.UGNX4.0基础应用与范例解析.机械工业出版社, 2007
207