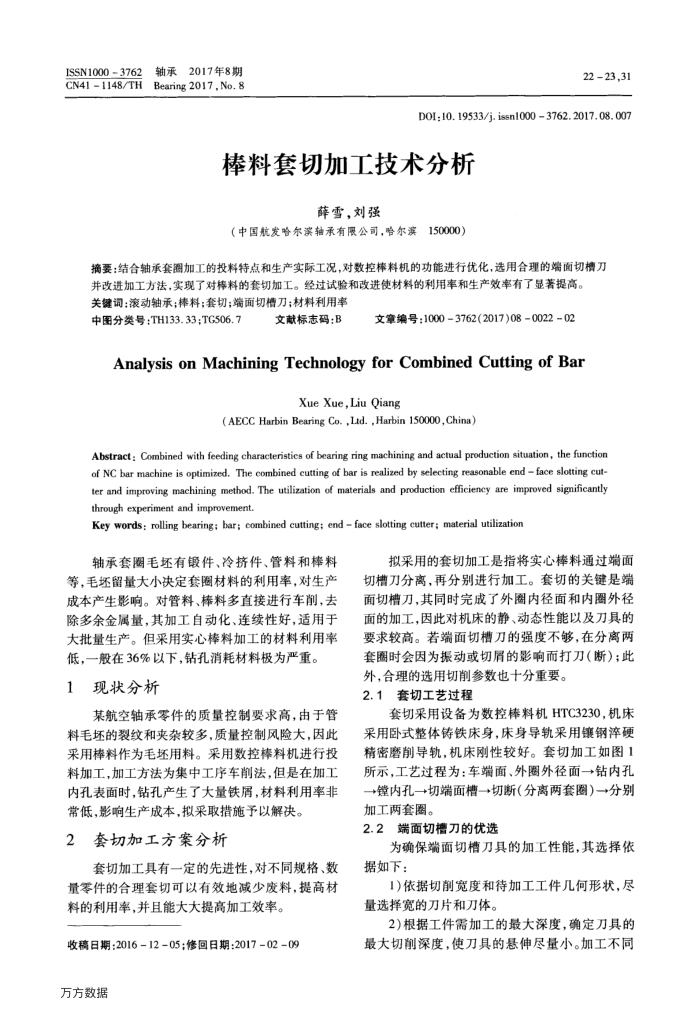
ISSN10003762 CN41 1148/TH
轴承2017年8期 Bearing 2017, No. 8
22 23,31
D0I:10. 19533/j. issn1000 3762. 2017. 08. 007
棒料套切加工技术分析
薛雪,刘强
(中国航发哈尔溪轴承有限公司,哈尔滨150000)
摘要:结合轴承套圈加工的投料特点和生产实际工况,对数控棒料机的功能进行优化,选用合理的端面切槽刀
并改进加工方法,实现了对棒料的套切加工。经过试验和改进使材料的利用率和生产效率有了显著提高。关键调:滚动轴承;棒料;套切;端面切槽刀;材料利用率
中图分类号:TH133.33;TG506.7
文献标志码:日
文章编号:10003762(2017)08002202
AnalysisonMachiningTechnologyforCombinedCuttingofBar
Xue Xue,Liu Qiang
( AECC Harbin Bearing Co. ,Lid. , Harbin 150000, China)
Abstract : Combined with feeding characteristics of bearing ring machining and actual production situation, the function of NC bar machine is optimized, The combined cutting of bar is realized by selecting reasonable end face slotting cut ter and improving machining method. The utilization of materials and production efficiency are improved significantly through experiment and improvement.
Key words: rolling bearing; bar; combined cutting; end face slotting cutter; material utilization
轴承套圈毛坏有锻件、冷挤件、管料和棒料等,毛坏留量大小决定套圈材料的利用率,对生产成本产生影响。对管料、棒料多直接进行车削,去除多余金属量,其加工自动化、连续性好,适用于大批量生产。但采用实心棒料加工的材料利用率
低,一般在36%以下,钻孔消耗材料极为严重。 1现状分析
某航空轴承零件的质量控制要求高,由于管料毛坏的裂纹和夹杂较多,质量控制风险大,因此采用棒料作为毛坏用料。采用数控棒料机进行投料加工,加工方法为集中工序车削法,但是在加工内孔表面时,钻孔产生了大量铁屑,材料利用率非常低,影响生产成本,拟采取措施予以解决。
套切加工方案分析 2
套切加工具有一定的先进性,对不同规格、数量零件的合理套切可以有效地减少废料,提高材料的利用率,并且能大大提高加工效率。
收稿日期:2016-12-05;修回日期:2017-0209 万方数据
拟采用的套切加工是指将实心棒料通过端面切槽刀分离,再分别进行加工。套切的关键是端面切槽刀,其同时完成了外圈内径面和内圈外径面的加工,因此对机床的静、动态性能以及刀具的要求较高。若端面切槽刀的强度不够,在分离两套圈时会因为振动或切屑的影响而打刀(断);此
外,合理的选用切削参数也十分重要。 2.1套切工艺过程
套切采用设备为数控棒料机HTC3230,机床采用卧式整体铸铁床身,床身导轨采用镶钢率硬精密磨削导轨,机床刚性较好。套切加工如图1 所示,工艺过程为:车端面、外圈外径面一→钻内孔 →镗内孔一→切端面槽一→+切断(分离两套圈)一→分别加工两套圈。
2.2端面切槽刀的优选
为确保端面切槽刀具的加工性能,其选择依据如下:
1)依据切削宽度和待加工工件几何形状,尽量选择宽的刀片和刀体,
2)根据工件需加工的最大深度,确定力具的最大切削深度,使刀具的悬伸尽量小。加工不同