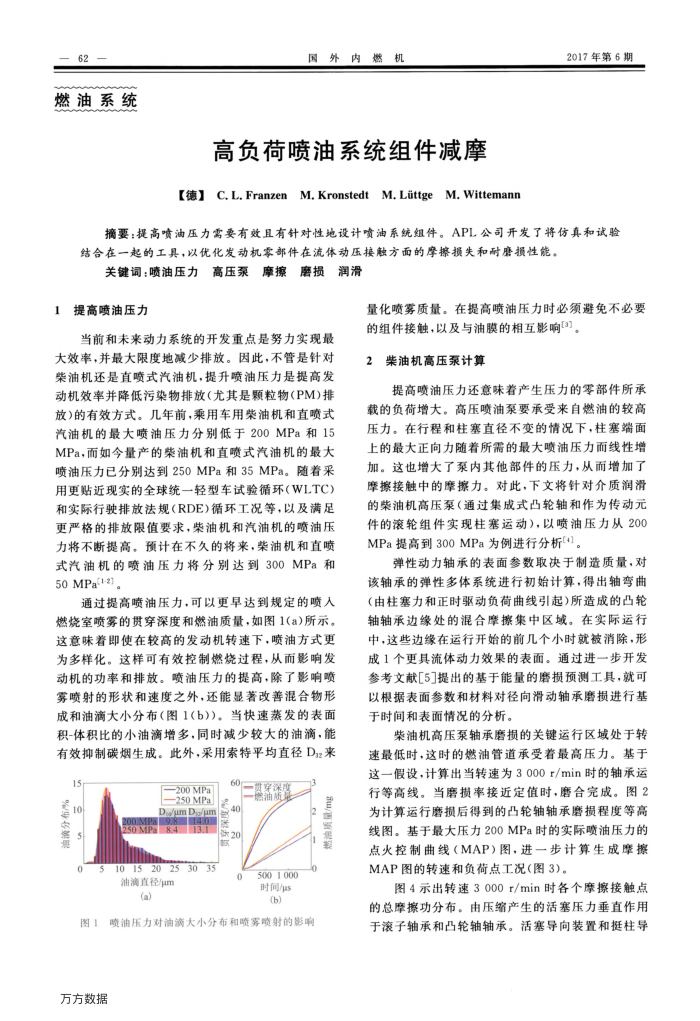
62
燃油系统
国外内燃机
高负荷喷油系统组件减摩
[德】C.L.FranzenM,Kronstedt
M.Littge
M.Wittemann
2017年第6期
摘要:提高喷油压力需要有效且有针对性地设计喷油系统组件。APL公司开发了将仿真和试验结合在一起的工具,以优化发动机零部件在流体动压接触方面的摩擦损失和耐磨损性能。
高压泵摩擦磨损润滑
关键词:喷油压力
1提高喷油压力
当前和未来动力系统的开发重点是努力实现最大效率,并最大限度地减少排放。因此,不管是针对柴油机还是直喷式汽油机,提升喷油压力是提高发动机效率并降低污染物排放(尤其是颗粒物(PM)排放)的有效方式。几年前,乘用车用柴油机和直喷式汽油机的最大喷油压力分别低于200MPa和15 MPa,而如今量产的柴油机和直喷式汽油机的最大喷油压力已分别达到250MPa和35MPa。随着采用更贴近现实的全球统一轻型车试验循环(WLTC) 和实际行驶排放法规(RDE)循环工况等,以及满足更严格的排放限值要求,柴油机和汽油机的喷油压力将不断提高。预计在不久的将来,柴油机和直喷式汽油机的喷油压力将分别达到300MPa和 50 MPa1-2)。
通过提高喷油压力,可以更早达到规定的喷人燃烧室喷雾的贯穿深度和燃油质量,如图1(a)所示。这意味着即使在较高的发动机转速下,喷油方式更为多样化。这样可有效控制燃烧过程,从而影响发动机的功率和排放。喷油压力的提高,除了影响喷雾喷射的形状和速度之外,还能显著改善混合物形成和油滴大小分布(图1(b))。当快速蒸发的表面积-体积比的小油滴增多,同时减少较大的油滴,能有效抑制碳烟生成。此外,采用索特平均直径Dz来
15
S
200MPa 250MPa D/umD/um
20OMPa
S0Pa8413. 101520253035 油滴直径/μm
(a)
60一赏穿深度一燃油质量
40 20
500 1000 时间/μs(b)
图1喷油压力对油滴大小分布和喷雾喷射的影响万方数据
量化喷雾质量。在提高喷油压力时必须避免不必要
的组件接触,以及与油膜的相互影响[3]。 2柴油机高压泵计算
提高喷油压力还意味着产生压力的零部件所承载的负荷增大。高压喷油泵要承受来自燃油的较高压力。在行程和柱塞直径不变的情况下,柱塞端面上的最大正向力随着所需的最大喷油压力而线性增加。这也增大了泵内其他部件的压力,从而增加了摩擦接触中的摩擦力。对此,下文将针对介质润滑的柴油机高压泵(通过集成式凸轮轴和作为传动元件的滚轮组件实现柱塞运动),以喷油压力从200 MPa提高到300MPa为例进行分析[+)。
弹性动力轴承的表面参数取决于制造质量,对该轴承的弹性多体系统进行初始计算,得出轴弯曲(由柱塞力和正时驱动负荷曲线引起)所造成的凸轮轴轴承边缘处的混合摩擦集中区域。在实际运行中,这些边缘在运行开始的前几个小时就被消除,形成1个更具流体动力效果的表面。通过进一步开发参考文献[5]提出的基于能量的磨损预测工具,就可以根据表面参数和材料对径向滑动轴承磨损进行基于时间和表面情况的分析。
柴油机高压泵轴承磨损的关键运行区域处于转速最低时,这时的燃油管道承受着最高压力。基于这一假设,计算出当转速为3000r/min时的轴承运行等高线。当磨损率接近定值时,磨合完成。图2 为计算运行磨损后得到的凸轮轴轴承磨损程度等高线图。基于最大压力200MPa时的实际喷油压力的点火控制曲线(MAP)图,进一步计算生成摩擦 MAP图的转速和负荷点工况(图3)。
图4示出转速3000r/min时各个摩擦接触点的总摩擦功分布。由压缩产生的活塞压力垂直作用于滚子轴承和凸轮轴轴承。活塞导向装置和挺柱导