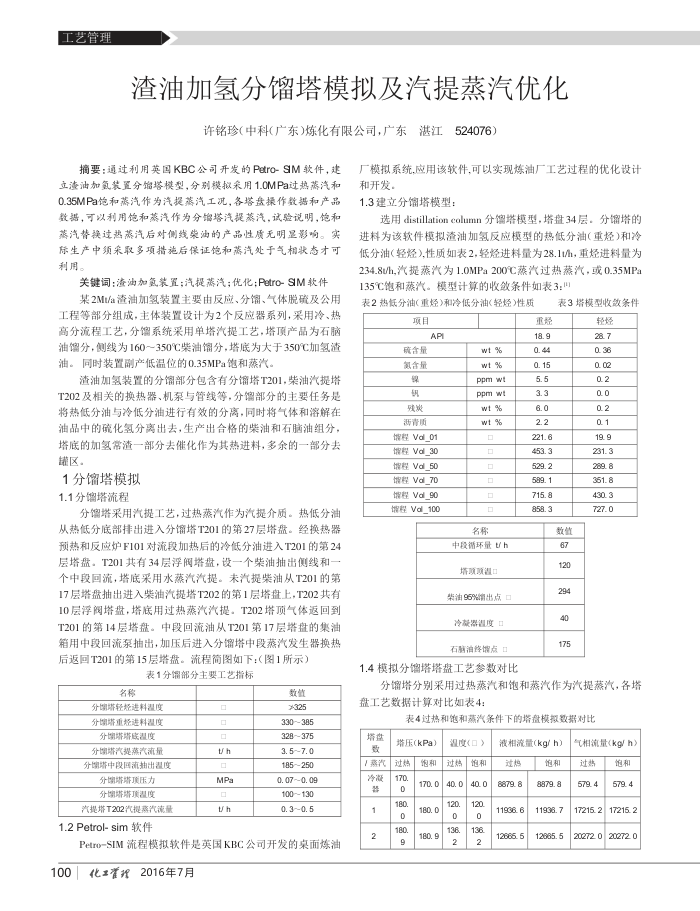
工艺管理
渣油加氢分馏塔模拟及汽提蒸汽优化
许铭珍(中科(广东)炼化有限公司,广东湛江
摘要:通过利用英国KBC公司开发的Petro-SM软件,建立渣油加氢装置分馅塔模型,分列模拟采用1.0MPa过热蒸汽和 0.35MPa饱和蒸汽作为汽提蒸汽工沉,各塔盘操作数据和产品数据,可以利用饱和蒸汽作为分增塔汽提蒸汽,试验说明,饱和蒸汽替换过热蒸汽后对侧线柴油的产品性质无明显影响。实际生产中须采取多项措施后保证饱和蒸汽处于气相状态才可利用。
关键词:澄油加氢装置;汽提蒸汽;优化;Petro-SIM软件某2Mt/a渣油加氢装置主要由反应、分馏、气体脱硫及公用
工程等部分组成,主体装置设计为2个反应器系列,采用冷、热高分流程工艺,分系统采用单塔汽提工艺,塔顶产品为石脑油分,侧线为160~350℃柴油馏分,塔底为大于350℃加氢渣油。同时装置副产低温位的0.35MPa饱和蒸汽。
渣油加氢装置的分馏部分包含有分馏塔T201,柴油汽提塔 T202及相关的换热器、机泵与管线等,分增部分的主要任务是将热低分油与冷低分油进行有效的分离,同时将气体和溶解在油品中的硫化氢分离出去,生产出合格的柴油和石脑油组分,塔底的加氢常渣一部分去催化作为其热进料,多余的一部分去罐区。
1分馏塔模拟 1.1分馏塔流程
分编塔采用汽提工艺,过热蒸汽作为汽提介质。
热低分油
从热低分底部排出进入分馈塔T201的第27层塔盘。
经换热器
预热和反应炉F101对流段加热后的冷低分油进入T201的第24 层塔盘。T201共有34层浮阀塔盘,设一个柴油抽出侧线和个中段回流,塔底采用水蒸汽汽提。未汽提柴油从T201的第 17层塔盘抽出进入柴油汽提塔T202的第1层塔盘上,T202共有 10层浮阀塔盘,塔底用过热蒸汽汽提。T202塔顶气体返回到 T201的第14层塔盘。中段回流油从T201第17层塔盘的集油箱用中段回流泵抽出,加压后进入分馏塔中段蒸汽发生器换热后返回T201的第15层塔盘。流程简图如下:(图1所示)
表1分镭部分主要工艺指标
名称
分螺塔轻经进料温度分馈塔重经进料温度分螺增增底温度分螺塔汽提燕汽殖量分馈塔中段国殖抽出温度分编塔塔项压力分螺塔塔项温度
汽提塔T202汽提盛汽流量 1.2Petrol-sim软件
口 th MPa th
数管 325 330-385 328-375 3.5--7.0 185~250 0.070. 09 100~130 0.3-0.5
Petro-SIM流程模拟软件是英国KBC公司开发的桌面炼油
100
化准理
2016年7月
524076)
厂模拟系统.应用该软件,可以实现炼油厂工艺过程的优化设计和开发。
1.3建立分馏塔模型:
选用distillationcolumn分馏塔模型,塔盘34层。分馏塔的进料为该软件模拟渣油加氢反应模型的热低分油(重烃)和冷低分油(轻烃),性质如表2,轻烃进料量为28.1t/h,重烃进料量为 234.8/h,汽提蒸汽为1.0MPa200℃蒸汽过热蒸汽,或0.35MPa
135℃饱和蒸汽。
模型计算的收效条件如表3:"
表2热低分油(重烃》和冷低分油(轻烃)性质
项目 API
含量鼠含量镍
残炭洒青质增程Vdi_01 增程Vd_30 增程Vd_50 增程Vd_70 程Vd_90 增程Val_100
wt % wt % ppm wt ppm wt wt % wt %
名称
中段循环量t/h 塔项项温口
柴油95%编出点口冷凝器温度口石脑油终增点口
1.4模拟分馏塔塔盘工艺参数对比
重经 18.9 0. 44 0.15 5.5 3.3 6.0 2.2 221.6 453.3 529.2 589. 1 715.8 858.3
表3塔模型收效条件
轻烃 28.7 0. 36 0.02 0.2 0.0 0.2 0.1 19.9 231.3 289. 8 351.8 430.3 727.0
数值 87 120
294 40 175
分馏塔分别采用过热蒸汽和饱和蒸汽作为汽提蒸汽,各塔盘工艺数据计算对比如表4:
表4过热和绝和蒸汽条件下的塔盘模报数据对比
塔盘燕汽冷凝
2
塔压(kPa)
过热 170. 0 180. 0 180. 9
绝和 170. 0 180. 0 180. 9
温度(口)
过热 40.0 120. 0 136. 2
饱和 40.0 120. 0 136.
液相流量(kg/h)
戏您 8879.8 11936. 6 12665. 5
饱和 8879.8 11936.7 12665.5
气相流量(kg/h)
过势 579. 4
17215.2 20272 0
饱和 579. 4 17215.2 20272 0