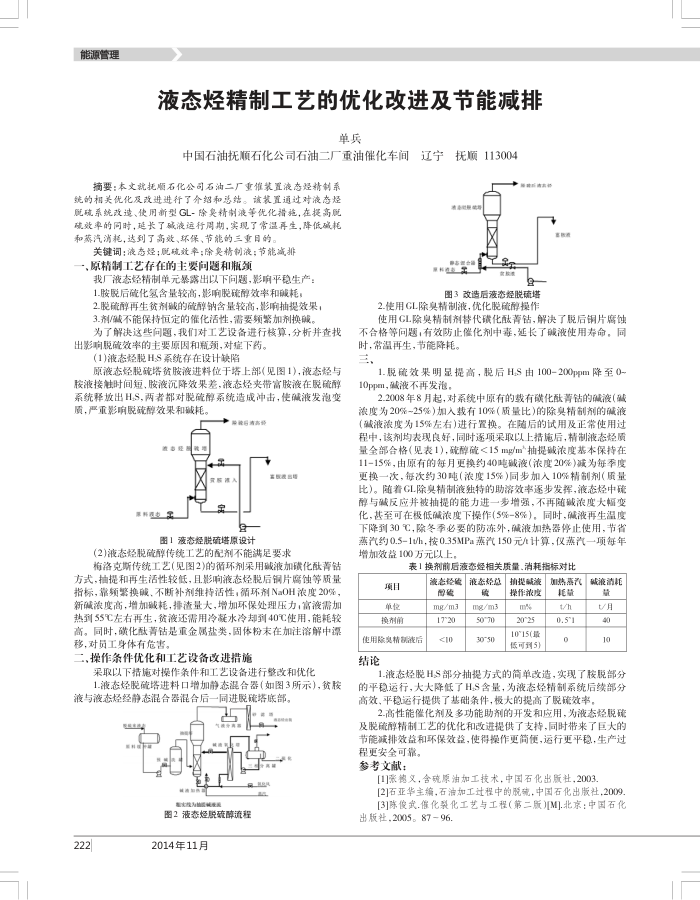
能源管理
液态烃精制工艺的优化改进及节能减排
单兵
中国石油抚顺石化公司石油二厂重油催化车间
摘要:本文就托顺石化公司石油二厂重维装置液变经精制系统的相关优化及改进进行了介绍和总结。该装置通过对液态烃既疏系统改造、使用新型GL-除臭精制液等优化指施,在提高既疏效率的同时,延长了碱液运行周期,实现了常温再生,降低碱耗和荔汽消耗,达到了高效、环保、节能的三重目的。
关键词:液态经;既硫效率;除臭精制液;节能减排、原精制工艺存在的主要问题和瓶颈
我厂液态经精制单元暴露出以下问题,影响平稳生产:
1.胺脱后硫化氢含量较高,影响脱硫醇效率和碱耗;
2.脱硫醇再生贫剂碱的硫醇钠含量较高,影响抽提效果, 3.剂/碱不能保持恒定的催化活性,需要频繁加剂换碱。
为了解决这些间题,我们对工艺设备进行核算,分析并查找出影响脱硫效率的主要原固和瓶颈,对症下药。
(1)液态经脱HS系统存在设计缺陷
原波态经脱疏塔贫胺波进料位于塔上部(见图1),液态经与胺液接触时间短胺液沉降效果差,液态烃夹带富胺液在脱硫醇系统释出H,S,两者都对脱硫醇系统造成冲击,使碱液发泡变
质,严重影响脱疏醇效果和碱耗。
经员
#R
#R6i亮
RS准
9
SE88
图1液态经脱硫塔原设计
(2)液态烃脱硫醇传统工艺的配剂不能满足要求
梅洛克斯传统工艺(见图2)的循环剂采用碱液加磺化菁站方式,抽提和再生活性较低,且影响液态脱后铜片腐蚀等质量指标,靠频繁换碱、不断补剂维持活性,循环剂Na0H浓度20%,新碱浓度高,增加碱耗,排查量大,增加环保处理压力,富液需加热到55%℃左右再生,贫液还需用冷凝水冷却到40C使用,能耗较高。同时,磺化献菁钴是重金属盐类,固体粉末在加注溶解中源移,对员工身体有危害。
二,操作条件优化和工艺设备改进措施
采取以下措施对操作条件和工艺设备进行整改和优化
1.液态经脱硫塔进料口增加静态混合器(如图3所示),贫胺液与液态烃经静态混合器混合后一同进脱硫塔底部。
a务RN8
a
888
达线AR
图2液态烃脱硫醇流程
222
2014年11月
辽宁
抚顺113004
要生 ea
原工
图3改造后液态经脱硫塔
2.使用GL除臭精制液,优化脱硫醇操作
使用CL除臭精制剂替代磺化酰菁钴,解决了脱后铜片腐蚀不合格等间题,有效防止催化剂中毒,延长了碱液使用寿命,同时,常温再生,节能降耗。
1.脱硫效果明显提高,脱后H,S由100200ppm降至0-10ppm,碱液不再发泡,
2.2008年8月起,对系统中原有的载有碳化酰菁钴的碱液(碱浓度为20%~25%)加入载有10%(质量比)的除臭精制剂的碱液(碱液浓度为15%左右)进行置换。在随后的试用及正常使用过程中,该剂均表现良好,同时逐项采取以上措施后,精制液态烃质量全部合格(见表1),疏醇硫<15mg/m~抽提碱浓度基本保持在 11-15%,由原有的每月更换约40吨碱液(浓度20%)减为每季度更换一次,每次约30吨(浓度15%)同步加入10%精制剂(质量比)。随着GL除臭精制液独特的助溶效率逐步发挥,液态烃中硫醇与碱反应并被抽提的能力进一步增强,不再随碱浓度大幅变化,甚至可在极低碱浓度下操作(5%-8%),同时,碱液再生温度下降到30℃,除冬率必要的防冻外,碱液加热器停止使用,节省蒸汽约0.5-1t/h,按0.35MPa蒸汽150元/计算,仅蒸汽一项每年增加效益100万元以上,
表1换剂前后液态经相关质量.消耗指标对比
项目单位换剂前
使用除实精制后结论
液态经总
液态经础酶酸
硫
mg/m3 17-20 <10
mg/m3 50~70 30~50
拍提就液操作激度 m% S2.0 10°15(最低可到5)
加热蒸气耗量 t/h 0.5~1 0
减液消量月 40 10
1.液态烃脱HS部分抽提方式的简单改造,实现了胺脱部分的平稳运行,大大降低了H,S含量,为液态烃精制系统后续部分高效,平稳运行提供了基础条件,极大的提高了脱硫效率。
2.高性能催化剂及多功能助剂的开发和应用,为液态经脱确及脱硫醇精制工艺的优化和改进提供了支持,同时带来了巨大的节能减排效益和环保效益,使得操作更简便,运行更平稳,生产过
程更安全可靠。参考文献:
[]涨糖义,含硫原油加工技术,中国石化出所社,2003
[2]石亚华主编,石油加工过程中的脱流,中国石化出版社,2009.[3]陈俊式.催化梨化工艺与工程(第二版)[M]北京:中国石化
出版社,2005。8796.