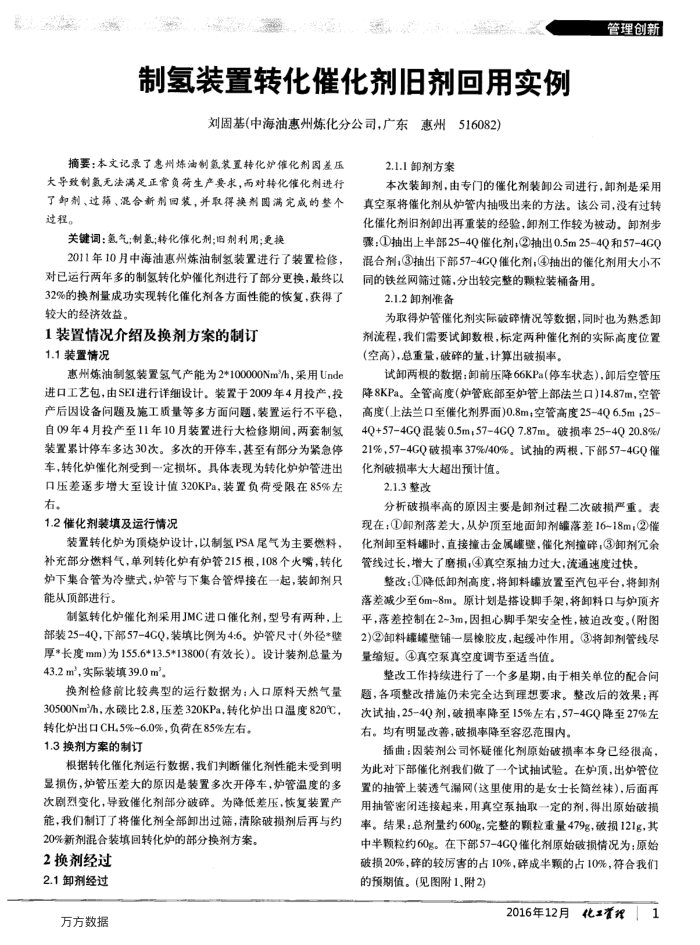
:
制氢装置转化催化剂旧剂回用实例
刘固基(中海油惠州炼化分公司,广东惠州516082)
摘要:本文记录了惠州炼油制氢装置转化炉催化剂固差压大导致制氢无法满足正常负荷生产要求,而对转化催化剂进行了卸剂、过筛、混合新剂回装,并取得换剂四满完成的整个过程。
关键词:氢气;制氢;转化催化剂;旧剂利用;更换
2011年10月中海油惠州炼油制氢装置进行了装置检修,对已运行两年多的制氢转化炉催化剂进行了部分更换,最终以 32%的换剂量成功实现转化催化剂各方面性能的恢复,获得了较大的经济效益。
1装置情况介绍及换剂方案的制订 1.1装置情况
惠州炼油制氢装置氢气产能为2*100000Nm/h,采用Unde 进口工艺包,由SEI进行详细设计。装置于2009年4月投产,投产后因设备间题及施工质量等多方面问题,装置运行不平稳,自09年4月投产至11年10月装置进行大检修期间,两套制氢装置累计停车多达30次。多次的开停车,基至有部分为紧急停车,转化炉催化剂受到一定损坏。具体表现为转化炉炉管进出口压差逐步增大至设计值320KPa,装置负荷受限在85%左右。
1.2催化剂装填及运行情况
装置转化炉为顶烧炉设计,以制氢PSA尾气为主要燃料,补充部分燃料气,单列转化炉有炉管215根,108个火嘴,转化炉下集合管为冷壁式,炉管与下集合管焊接在一起,装卸剂只能从顶部进行。
制氢转化炉催化剂采用JMC进口催化剂,型号有两种,上部装25-4Q,下部57-4CQ,装填比例为4:6。炉管尺寸(外径*壁厚*长度mm)为155.6*13.5*13800(有效长)。设计装剂总量为 43.2m,实际装填39.0m。
换剂检修前比较典型的运行数据为:人口原料天然气量 30500Nm/h,水碳比2.8,压差320KPa,转化炉出口温度820℃,
转化炉出口CH.5%~6.0%,负荷在85%左右。 1.3换剂方案的制订
根据转化催化剂运行数据,我们判断催化剂性能未受到明显损伤,炉管压差大的原因是装置多次开停车,炉管温度的多次剧烈变化,导致催化剂部分破碎。为降低差压,恢复装置产能,我们制订了将催化剂全部即出过筛,清除破损剂后再与约 20%新剂混合装填回转化炉的部分换剂方案。
2换剂经过 2.1卸剂经过
万方数据
2.1.1卸剂方案
管理创新
本次装卸剂,由专门的催化剂装卸公司进行,卸剂是采用真空泵将催化剂从炉管内抽吸出来的方法。该公司,没有过转化催化剂旧剂卸出再重装的经验,卸剂工作较为被动。卸剂步骤:①抽出上半部25-4Q催化剂;②抽出0.5m25-4Q和57-4GQ 混合剂;③抽出下部57-4GQ催化剂;④抽出的催化剂用大小不同的铁丝网筛过筛,分出较完整的颗粒装桶备用。
2.1.2卸剂准备
为取得炉管催化剂实际破碎情况等数据,同时也为熟悉卸剂流程,我们需要试卸数根,标定两种催化剂的实际高度位置(空高),总重量,破碎的量,计算出破损率。
试卸两根的数据:卸前压降66KPa(停车状态).卸后空管压降8KPa。全管高度(炉管底部至炉管上部法兰口)14.87m,空管高度(上法兰口至催化剂界面)0.8m;空管高度25-4Q6.5m,25 4Q+574GQ混装0.5m;574GQ7.87m破损率25-4Q20.8%/ 21%,57-4GQ破损率37%/40%。试抽的两根,下部57-4GQ催化剂破损率大大超出预计值。
2.1.3整改
分析破损率高的原因主要是卸剂过程二次破损严重。表现在:①卸剂落差大,从炉顶至地面卸剂罐落差16~18m;②催化剂卸至料罐时,直接撞击金属罐壁,催化剂撞碎,③卸剂余管线过长,增大了磨损,④真空泵抽力过大,流通速度过快。
整改:①降低卸剂高度,将卸料罐放置至汽包平台,将卸剂落差减少至6m~8m。原计划是搭设脚手架,将卸料口与炉顶齐平,落差控制在2~3m,因担心脚手架安全性,被迫改变。(附图 2)②卸料罐罐壁铺一层橡胶皮,起缓冲作用。③将卸剂管线尽量缩短。④真空泵真空度调节至适当值。
整改工作持续进行了一个多星期,由于相关单位的配合间题,各项整改措施仍未完全达到理想要求。整改后的效果:再次试抽,25-4Q剂,破损率降至15%左右,57-4GQ降至27%左右。均有明显改善,破损率降至容忍范围内。
插曲:因装剂公司怀疑催化剂原始破损率本身已经很高,为此对下部催化剂我们做了一个试抽试验。在炉顶,出炉管位置的抽管上装透气漏网(这里使用的是女士长筒丝袜),后面再用抽管密闭连接起来,用真空泵抽取一定的剂,得出原始破损率。结果:总剂量约600g,完整的颗粒重量479g,破损121g,其中半颗粒约60g。在下部57-4GQ催化剂原始破损情况为:原始破损20%,碎的较厉害的占10%,碎成半颗的占10%,符合我们的预期值。(见图附1、附2)
化省纪丨1
2016年12月