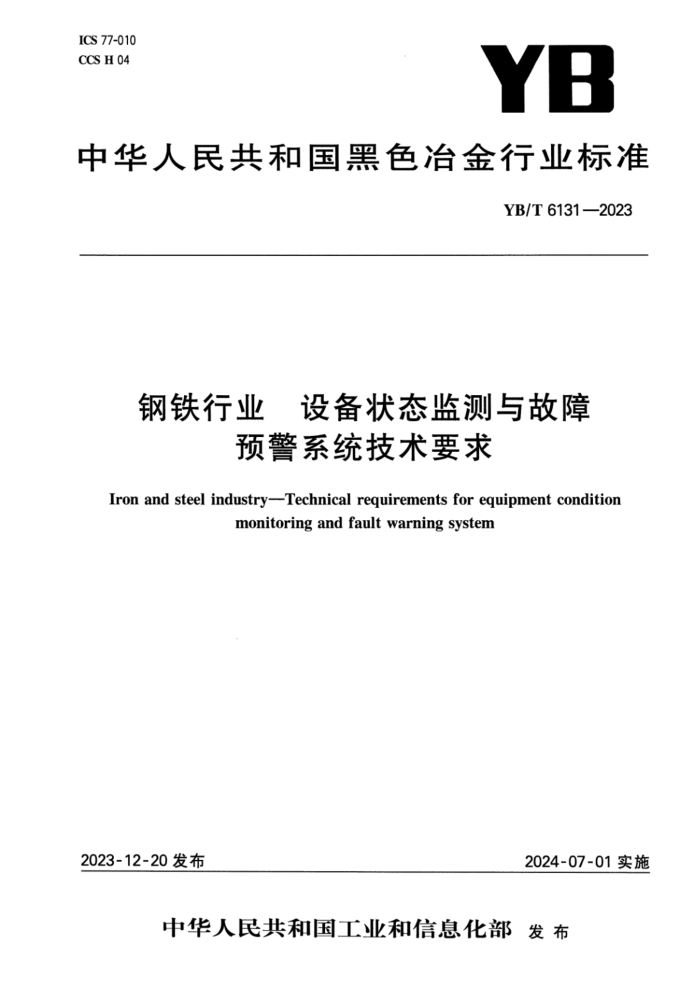
ICS 77-010
CCS H 04
YB
中华人民共和国黑色冶金行业标准
YB/T 6131—2023
钢铁行业 设备状态监测与故障预警系统技术要求
Iron and steel industry——Technical requirements for equipment condition monitoring and fault warning system
2023-12-20发布 2024-07-01实施
中华人民共和国工业和信息化部发 布
YB/T 6131—2023
前 言
本文件按照GB/T1.1——2020《标准化工作导则 第1部分:标准化文件的结构和起草规则》的规定起草。
请注意本文件的某些内容可能涉及专利。本文件的发布机构不承担识别专利的责任。
本文件由中国钢铁工业协会提出。
本文件由全国钢标准化技术委员会(SAC/TC 183)归口。
本文件起草单位:鞍山钢铁集团有限公司、北京科技大学、本溪钢铁(集团)信息自动化有限责任公司、江苏永钢集团有限公司、河北天柱钢铁集团有限公司、冶金工业信息标准研究院、承德建龙特殊钢有限公司、江阴华润制钢有限公司、中冶赛迪信息技术(重庆)有限公司、安徽容知日新科技股份有限公司、宝武装备智能科技有限公司。
本文件主要起草人:阳建宏、黎敏、孟劲松、赵庆涛、刘斓冰、李静、王雪原、张可、施建忠、林西强、罗显科、顾玉萍、何天庆、赵伟、赵俊杰、刘国栋、康立军、常莘东、陈士英、彭燕华、王兴、刘学功、石凤康、姚结兵、荣守起、朱献忠、程本俊。
YB/T 6131—2023
钢铁行业 设备状态监测与故障预警系统技术要求
1 范围
本文件规定了钢铁行业设备状态监测与故障预警系统的系统架构、数据采集、数据存储和系统功能组成等技术要求。
本文件适用于钢铁行业工艺设备、主要辅助设备的状态监测与故障预警系统的建设和改造。
2 规范性引用文件
下列文件中的内容通过文中的规范性引用而构成本文件必不可少的条款。其中,注日期的引用文件,仅该日期对应的版本适用于本文件;不注日期的引用文件,其最新版本(包括所有的修改单)适用于本文件。
GB/T6075.1 机械振动 在非旋转部件上测量评价机器的振动 第1部分:总则
GB/T19873.1 机器状态监测与诊断 振动状态监测 第1部分:总则
GB/T19873.2 机器状态监测与诊断 振动状态监测 第2部分:振动数据处理、分析与描述
ISO/IEC TR 30166 物联网-工业物联网
3 术语和定义
下列术语和定义适用于本文件。
3.1
故障 fault
当设备由于性能退化导致无法有效完成预定功能的设备状态。
3.2
状态监测 condition monitoring
对设备运行中的振动、温度、压力、转速等物理状态数据和物料尺寸、生产计划、控制模型参数等影响设备功能精度及寿命的工艺过程数据进行实时采集和分析,结合状态评价方法,对设备的实时工作状态进行监测。
3.3
故障诊断 fault diagnosis
通过设备的核心状态数据和相关重要数据,利用一系列分析方法,结合当前设备的异常现象,确定设备的故障位置、故障类型、故障原因、故障程度等。
3.4
寿命预测 lifetime prognosis
根据设备的当前状态和历史变化过程,在一定的时间范围内预测设备状态劣化趋势和设备剩余寿命变化的可能性。
1
标准
YB/T 6131—2023
、系统架构
4.1 系统架构组成
钢铁行业设备状态监测与故障预警系统架构图见图1。整个系统分为设备层、平台层和应用层。设备层涵盖钢铁冶金领域全工序关键设备,通过与原有系统交互及新增数据感知设备的方式采集设备状态相关的数据,并上传至平台层,在平台层对数据进行清洗降噪、特征提取和时空匹配,并分别存入各类设备主题数据库,同时平台层提供信号分析方法库、故障诊断规则库、设备故障诊断模型、设备寿命预测模型等多种分析工具及模型,以实现对数据的分析处理,形成相关结论,为构建状态监测和故障预警应用提供基础。应用层基于设备层和平台层的支撑,形成具备在线监测、数据分析、智能报警、故障诊断等多种功能的设备状态监测与故障预警应用。
设备状态监测与故障预警应用
多层次监测
历史查询
数据分析
智能报警
故障诊断
设备过程
远程诊断
系统管理
皮用层
决策支持
能力评价
信号分析方法库
故障诊断规则库
设备故障诊断模型
设备寿命预测模型
设备状态与工艺
质量联动分析模型
设备状态监测核心数据
设备状态监测辅助支撑数据
平台层
设备运行
设备基础
产品质量
生产过程
备件仓储
设备维修
设备相关
状态数据库
信息数据库
统计数据库
工艺数据库
物流数据库
历史数据库
标准数据库
数据汇集、数据清洗、数据转换、数据重整
新增数据感知设备
原有系统数据交互
钢铁行业工艺设备、主要辅助设备等
设备层
机械类设备
液压类设备
电气类设备
温度
振动
位移
…
液位
压力
流量
…
电流
绝缘
温度
…
图1 钢铁行业设备状态监测与故障预警系统架构图
用于建立设备状态主题数据库的设备状态数据应进行清洗、转换、时空匹配、预处理等操作。
宜开发基于大数据分析的故障特征提取、设备故障诊断、设备寿命预测等多种模型,提供时域分析、频域分析、精密分析、趋势分析、过程监测、状态报警、故障诊断和规则推理等各类分析工具,支撑应用层对设备状态数据进行统计、分析、综合、归纳和诊断,为设备管理系统中功能精度管理、维修维护管理、备件采购管理等提供有效的决策支持。
网络架构应符合ISO/IEC TR 30166要求,应具有远程访问接口,授权用户可以根据相应权限通过企业内部网远程登录和访问本系统的功能。用户访问形式支持移动终端、PC机、工程师站等多种访问方式。
2
YB/T 6131—2023
4.2 基本要求
4.2.1 设备对象
钢铁行业设备状态监测与故障预警系统中的设备对象覆盖钢铁冶金生产行业涉及的各类冶炼设备、铸造设备、轧制设备和精整设备等工艺设备和主要辅助设备。其中冶炼设备主要包括高炉、转炉、电炉,以及原料存储和转运设备,烧结、球团和焦炉设备,铁液预处理和钢液炉外精炼设备等;铸造设备主要包括板坯、方坯、管坯、异型坯连铸成套设备等;轧制设备主要包括板材、管材、型材和线材各类热轧机、冷轧机成套设备等;精整设备主要包括各种轧材的后步处理和深加工成套设备,如纵、横剪切线成套设备、连续酸洗机组、连续退火机组、热镀锌、电镀锌、电镀锡、有机涂层等涂镀层和复合材料生产成套设备,以及拉丝制绳设备等。
4.2.2 设备状态感知
传感器类型可包括振动传感器、位移传感器、位置传感器、温度传感器、转速传感器、扭矩传感器、电流传感器、绝缘传感器、流量传感器、压力传感器、液位传感器、声音传感器、图像传感器等。传感器可检测的物理参数和测量精度应能准确反映钢铁行业设备的工作状况及其控制系统的效果。
4.2.3 数据通讯
设备状态监测与故障预警系统与外部系统的通讯应能支持多种主流协议的接入,可识别多种数据交换格式,实现所有相关系统和设备数据的采集,实现向工单系统、设备管理系统等系统的数据交互。
4.2.4 数据分析流程
钢铁行业设备状态监测与故障预警系统数据分析应按照以下流程:
a) 设置合理的数据采集参数和通讯接口,完成设备状态数据与工艺过程数据、内外在质量数据的数据获取;
b)对数据进行清洗、转换、特征提取、时空匹配,并存入数据库;
c) 应对单一特征值进行分析,对特征值变化趋势进行分析,对同类设备的状态监测数值进行比对分析,对设备不同工况下数据进行比对分析,进行设备状态预警;
d)应开发专用模型对设备的状态进行分析、仿真、诊断等;
e) 应结合设备状态数据与工艺过程数据、内外在质量数据,分析设备状态对产品质量的影响;
f)应结合故障与维修履历,根据设备当前状态给出维修建议。
4.2.5 系统安全性
设备状态监测与故障预警系统的设计应当考虑数据访问的安全性,并保障在与外部系统的通讯时,不对外部原有系统造成不良影响。
5 数据采集技术要求
5.1 基本要求
数据采集系统基础架构及功能宜参照GB/T38619要求设计,且针对钢铁行业的行业特点,系统应通过数据采集软件或平台,获取钢铁冶金生产过程的设备状态数据、生产工艺数据、产品质量等数据信
3
标准
YB/T 6131——2023
息。为了能够采集到各种必要的设备运行状态数据,宜在现有生产过程控制系统及相关系统基础上,根据需要完善相关的检测仪表及系统功能。
各数据采集系统之间应当进行时间同步。
5.2 数据采集范围
5.2.1 设备状态监测核心数据
在确定设备状态数据采集范围时,应根据设备类别,选择能有效表征设备工作特点的物理量,包括但不限于以下类型:
a) 风机类、水泵类、齿轮箱类:转速、载荷,各轴承座振动、温度等;
b) 载荷轴类:轴承温度,传动扭矩等;
c) 电气类:电机转速、电流,各轴承座振动、温度,定子温度,电机绝缘状态,轴端位移等;变压器振动、温度、局部放电状态等;高压电气柜母排温度、触头温度等;电缆温度、绝缘状态等;
d) 剪切类:剪刃平行度、剪切轨迹,轴承座振动、温度等;
e) 液压类:各管路压力,油箱液位,泵体、阀体、液压缸、蓄能器等部件的工作状态;
f) 高温反应及储运容器类:容器壁壳温度、热流,容器压力,冷却系统压力及流量等;
g) 支撑、基座类:振动、温度、应力与应变等。
为更好地实现设备状态数据的分析诊断,宜采集设备型号、设备图纸、设备三维模型、设备零部件型号参数、设备编码等设备相关的基础信息数据。如企业中已有数字化交付系统,应通过与已有数字化交付系统交互的方式获取设备基础信息数据。
5.2.2 设备状态监测相关重要数据
为更好地实现设备状态数据的统计分析诊断,宜采集以下数据:
a) 与设备状态分析相关的生产工艺、物料与产品质量数据,包括但不限于:生产计划信息、订单信息、物料信息(钢种、规格、重量、化学成分等)、物料跟踪数据(物料ID及其在各设备/工序的开始和结束时刻等)、各工序的关键工艺过程参数(温度、压力、速度、载荷等)、产品质量数据(内部质量、表面质量、尺寸偏差等);
b)设备运维管理相关数据,包括但不限于:设备故障履历、设备维修履历,设备点检记录、设备点检数据,备件数量、机旁库信息、备件领用状态,设备维修技术标准、点检标准、给油脂标准和维修作业标准等数据。
5.3传感器类型选择与采集参数设置
5.3.1 传感器类型选择总体要求
传感器类型及其防护等级、外形尺寸、测量范围及灵敏度等传感器参数的选择,应充分考虑以下因素:
a) 现场环境温度、湿度、粉尘、噪声、强振、电磁干扰等因素;
b)设备运动轨迹、安装操作空间、是否影响设备维修操作、供电方式等因素;
c) 被测状态量变化范围、灵敏度、精度、重复度,测量方式(接触式、非接触式)等因素。
5.3.2 采集参数设置总体要求
传感器采集参数设置应充分考虑设备工况变化程度、被测物理量变化快慢等特点,合理设置采样频率、采样时间、采样间隔、触发采集方式等传感器采集参数。
4
YB/T 6131—2023
5.3.3 传感器安装总体要求
传感器安装位置及方式应充分考虑以下情况:
a) 应确保传感器在长期工作中能准确、稳定、可靠地获取相应的测量结果;
b)应保障传感器数据可稳定、有效地进行通讯与传输;
c) 充分考虑设备运行中的局部高温、强振和形位变换等因素,避免出现传感器损坏;
d)应避免与设备维护等作业的干涉;
e) 应便于拆卸更换和后续维护。
5.3.4数据传输方式总体要求
传感器的数据传输,应从供电持续性、相对性运动、数据精度等方面充分考虑设备状态监测的需求,合理选择有线或无线传输策略及供电方式。
5.3.5 需要特殊考虑的情况
传感器类型选择与采集参数设置,还应结合具体情况进行考虑,包括但不限于以下类型:
a) 振动类传感器:应满足GB/T19873.1和GB/T 6075.1相关要求。应充分考虑设备转速变化与载荷变化的特点、故障频率范围、设备共振频率范围等因素,合理选择传感器的类型、频率响应范围等传感器参数以及采样时间、采样频率、频率分辨率、采样间隔和触发方式等采样参数。对于低速重载设备,加速度传感器应具有较好的低频响应特性,振动监测的最高分析频率宜设为40kHz以上,频率分辨率应满足分析要求;对于变速变载设备,应根据设备转速及载荷变化的速率和范围,选择合适的采样频率进行30s以上的连续采集,并宜同步采集设备的转速变化数据;
b)扭矩传感器:应充分考虑工作扭矩范围和安全系数。应根据扭矩载荷的特点、现场安装维护的条件选择合适的安装位置。扭矩传感器宜采用无线数据传输方式,选择通讯协议时应考虑主轴旋转带来的传感器位置变化以及引起的信号干扰;
c) 转速传感器:应充分考虑设备转速范围、测量精度要求、传感器安装距离、现场油泥/铁屑等环境因素对传感器精度影响等;
d)声音传感器:应充分考虑异响及噪声的频率范围,宜选择的频响范围为20 Hz~20kHz;
e) 电气绝缘传感器:应考虑被测系统的中性点接地情况。
5.4 数据处理
各类设备状态采集系统获取的多源异构数据,宜通过工业物联网平台传输到数据库。为保证数据可靠性和准确性,宜对数据进行处理操作,包括数据清洗、数据转换、时空匹配等。其中,对振动数据的处理应符合GB/T 19873.2的规定。
5.5 数据通讯接口
数据通讯中以太网现场总线的各层协议规范宜满足GB/T31230系列的相关标准要求,无线网络数据通讯宜参照GB/T 26790系列的相关标准要求,数据通讯网络架构宜参照GB/T 38619标准要求。
传感器到对应采集设备间的无线通讯方式可采用无线局域网、远距离无线电、蓝牙、射频通讯、窄带物联网等。
采集设备宜通过以太网完成数据通讯,对于温度、湿度等缓变型数据宜采用主流串行通信协议、消息队列遥测传输协议等方式进行上传。对于振动、位移、扭矩等快变型数据的通讯协议可采用自定义的协议格式,且协议宜采用无状态风格设计。
5
标准
YB/T 6131—2023
数据通讯接口应包含数据标识、测点ID、时间戳、校验码等内容。在此基础上,对不同类别数据的通讯接口要求包括但不限于以下数据类型:
a) 快变型数据:如振动、扭矩、位移等相对快速变化的数据,宜包含采样频率、采样时长、数据长度、数据包编号、波形数据等;
b) 缓变型数据:如振动特征值、温度、压力、流量、液位等相对缓慢变化的数据,宜包含数量值总数、数据值名称/编号、数据值等;
c) 报警类数据:应包含设备编码、监测点编号、监测量数值、报警时间、报警级别、报警现象描述等,宜包含诊断结论、处理建议等内容。
6 数据存储要求
6.1 总体要求
应根据数据的特征,选择数据仓库、数据湖、湖仓一体数据平台等形式存储设备状态监测与故障预警相关数据。对于不同的数据应有不同的存储策略,应具有批处理、流处理等数据加工处理能力,应具有较高的可配置性、较高的数据安全性。
6.2 存储策略
对于不同的特征数据宜设置不同的存储策略。对振动、位移、扭矩等快变型数据宜采用索引加波形文件的形式存储,对温度、湿度、电流等缓变型数据宜在数据库表中直接存储,对中长期的数据宜进行压缩存储,节省存储空间,提高数据访问性能。
7 平台层功能组成
平台层应集成以下设备状态监测与故障预警的通用模型和工具:
a) 信号分析方法库:宜包括对各类状态数据的降噪处理、相关分析、时域分析、频域分析、统计分析、趋势分析等方法工具;
b) 故障诊断规则库:宜包括齿轮故障规则库、轴承故障规则库、轴类故障规则库、电机故障规则库、液压故障规则库等;
c) 设备故障诊断模型:宜包含各类设备常见故障的诊断模型,可根据特定设备的状态数据进行分析处理,给出故障诊断结论,为科学评价设备状态提供决策支持;
d)设备寿命预测模型:可通过积累全生命周期的设备状态数据,结合设备运维管理相关数据、设备状态数据的变化趋势和故障诊断结论,预测设备剩余寿命,为设备的科学运维提供决策支持;
e) 设备状态与工艺质量联动分析模型:可结合生产工艺、物料与产品质量数据,对设备工作状态数据进行综合分析,为设备功能精度和服役状态提供综合诊断与评价手段。
8 应用层功能组成
应用层宜包括以下功能:
a) 多层次监测:以曲线、表格、柱状图等丰富的表现形式,结合生产线或设备的结构示意图,提供全线监测、机组监测、测点监测、特征值监测的逐级监测界面;
b)历史查询:能根据指定监测测点、时间范围等条件查询设备状态的历史数据,支持主流格式的数据导出、数据备份和数据管理等功能;
6
YB/T 6131—2023
c) 数据分析:能集成调用平台层的各类信号分析方法,并展示分析结果,包括多变量数据趋势分析、同比分析、环比分析和统计分析等功能;
d)智能报警:根据设备状态监测数据,结合设备自身特点、生产工艺、物料与产品质量数据等,构建智能报警指标体系,采用阈值报警、规则报警、趋势报警等多种报警策略,用短信、微信、邮件、画面、声光等各种方式对设备工作状态进行分级报警提示;
e) 故障诊断决策支持:结合设备状态数据、生产工艺、物料与产品质量数据等,基于平台层的设备故障诊断规则和设备诊断模型,对设备故障位置、故障类型、故障原因、故障程度等进行分析,给出设备维修维护的决策建议;
f) 设备过程能力评价:在各种工艺参数、操作条件、原料参数、环境参数组合的条件下,对设备状态及功能精度进行统计分析,以判断设备功能精度的保障水平;
g)远程会诊:为授权领域专家开展远程分析和故障诊断,提供各类信号分析方法和数据展示功能的调用接口和界面;
h) 系统管理:具备用户管理、权限管理、日志管理等功能,提供系统参数设置、设备信息管理、测点管理与配置等功能,包括文件地址设置、存储策略选择、采样参数设置等功能。
标准
YB/T 6131—2023
参 考 文献
[1] GB/T 19873.3 机器状态监测与诊断 振动状态监测 第3部分:振动诊断指南
[2] GB/T 2298 机械振动、冲击与状态监测 词汇
[3] GB/T 20921 机器状态监测与诊断词汇
[4] GB/T29716.1 机械振动与冲击 信号处理 第1部分:引论
[5] GB/T 38619 工业物联网 数据采集结构化描述规范
[6] GB/T 31230.1 工业以太网现场总线EtherCAT 第1部分:概述
[7] GB/T 26790.1 工业无线网络WIA规范 第1部分:用于过程自动化的WIA系统结构与通信规范
[8] GB/T 26790.2 工业无线网络WIA规范 第2部分:用于工厂自动化的WIA系统结构与通信规范
[9] GB/T 25742.2 机器状态监测与诊断 数据处理、通信与表示 第2部分:数据处理