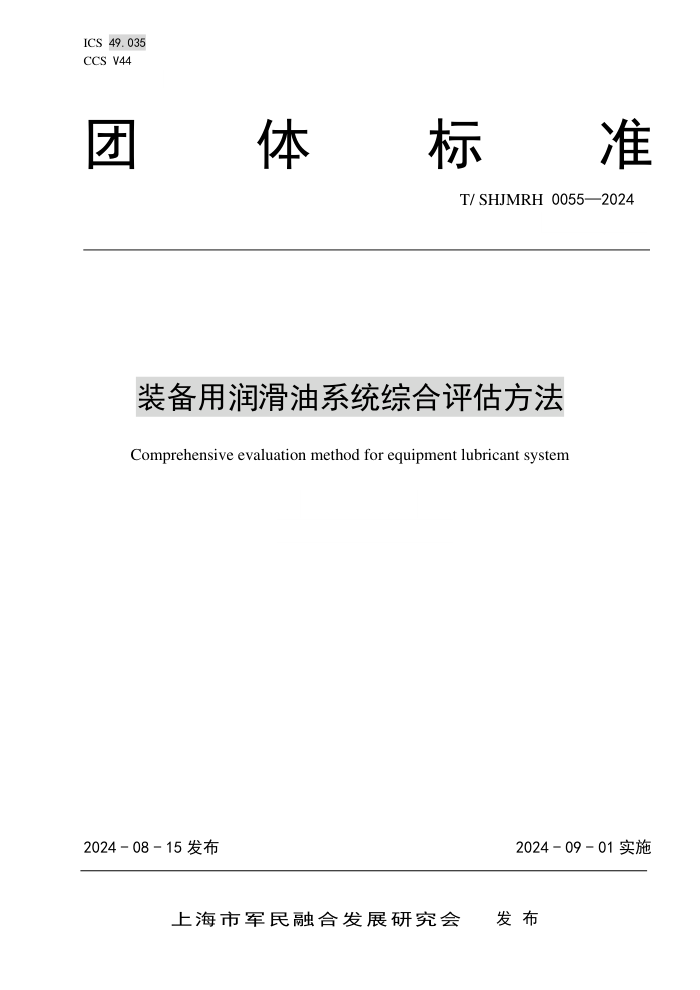
ICS 49.035
CCS V44
团
体 标 准
T/ SHJMRH 0055—2024
装备用润滑油系统综合评估方法
Comprehensive evaluation method for equipment lubricant system
2024 - 08 - 15 发布
2024 - 09 - 01 实施
上海市军民融合发展研究会 发 布
前 言
本文件按照GB/T 1.1—2020《标准化工作导则 第1部分:标准化文件的结构和起草规则》的
规定起草。
本文件附录A为资料性附录。
本文件由上海市军民融合发展研究会提出并归口。
本标准起草单位:山西航天清华装备有限责任公司、上海煊凝机电制造有限公司、上海韦航装备科
技有限公司、广州机械科学研究院有限公司、湖北泰和电气有限公司、上海星悦电子科技有限公司、上
海市军民融合发展研究会、上海博雁科技有限公司、上海泰和星智能科技有限公司。
本标准主要起草人:郭强、辛治宏、佟亚东、王联融、闫俣华、张冬琴、陈炜、郑自杰、孙磊、张
炳正、郑周、刘乾、陈钦松、兰永宽、周磊、刘涛涛、李根、石新发、冯伟、丘晖饶、刘海元、钱康伟、
杨双宾、刘辛亮、翟文勇。
本标准承诺执行单位:扬州市江都永坚有限公司、靖江凯信铁塔制造有限公司、浙江镁科机械
科技有限公司、泰兴市亚春亚机械有限公司、扬州皓月机械有限公司、内蒙古力森工矿机械有限公
司、历恩科技(沈阳)有限公司、中合润邦科技(北京)有限公司、北京斯润达科技有限公司、广研检
测(广州)有限公司、上海华融机电设备保障技术研发中心、上海究度智能科技有限公司、上海栖云
航空科技有限公司、常州诚石机械设备有限公司、常州瑞工液压技术有限公司、鲲鹏(常州)精密
制造科技有限公司、琴川动力科技(苏州)有限公司、上海部瑞精密机械有限公司。
I
装备用润滑油系统综合评估方法
1 范围
本标准规定了装备润滑油系统综合评估的程序、模型和结果报告的要求。
2 规范性引用文件
下列文件对于本文件的应用是必不可少的。凡是注日期的引用文件,仅注日期的版本适用于本文件。
凡是不注日期的引用文件,其最新版本(包括所有的修改单)适用于本文件。
GB 11118.1-2011 液压油(L-HL、L-HM、L-HV、L-HS、L-HG)
GB/T 7607-2010 柴油机油换油指标
GB/T 8028-2010 汽油机油换油指标
GB/T 14039-2002 液压传动 油液固体颗粒污染度等级代号
GB/T 22235-2008 液体黏度的测定
GB/T 30034-2013 重负荷车辆齿轮油(GL-5)换油指标
GJB 380.1A-2004 航空工作液污染测试 第1部分:采样容器一般要求及其清洗方法鉴定
GJB 420B-2006 航空工作液固体污染度分级
SH 0358-1995 10号航空液压油
SH/T 0475 普通车辆齿轮油换油指标
SH/T 0476 L-HL 液压油换油指标
NB/SH/T 0586-2010 工业闭式齿轮油换油指标
NB/SH/T 0599-2013 L-HM 液压油换油指标
NAS 1638-2011 Cleanliness Requirements of Parts Used in Hydraulic Systems
TB/T 1739-2005 内燃机车柴油机油换油指标
QJ 2724.1~2724.7-95 航天液压污染控制
SAE-AS4059 标准液压油污染物等级
JB/T 12194-2015 液压传动油
3 术语和定义
下列术语和定义适用于本标准。
3.1
油液样品 Oil Sample
指从装备油液系统中提取的少量在用油液,用于后续检测及评估。
3.2
装备型号 Equipment Model
1
指某些具有相同外观、功能、指标、使用方法的多个装备的型号,用以代表某一类装备。
3.3
装备编号 Equipment Number
指某台/套的编号,用以与区分其它同型号或不同型号的装备。
3.4
综合评估 Comprehensive Evaluation
通过对多类油液指标进行检测,评价油品技术质量状态,并进一步分析发生问题的原因。
3.5
历史分析 History Analysis
指对某一台/套装备先后多次采样检测结果进行的分析过程。
3.6
横向分析 Horizontal Analysis
指对同一型号的多台/套装备最近一次的采样检测结果进行的分析对比的过程。
3.7
综合评估模型 Comprehensive Evaluation Model
一种以国家标准、行业标准中所规定的油品性能指标与变化量为基准,并结合装备的使用特性与用
户的特定需求,通过系统地采集、处理与分析润滑油样本的各项指标,对润滑油的技术质量状态进行评
估和分析的工具。
4 综合评估过程
4.1 评估过程示意图
评估过程分为取样、检测、评估三个阶段。评估过程示意图见图1。
图1 综合评估过程
2
4.2 数据采集
4.2.1 采集方式
有线传输、无线传输或者移动存储设备传输方式。
4.2.2 数据要求
检测数据应至少具有装备型号、装备编号、取样部位、取样时间、油品名称、油品牌号、油品标准、
换油时间、指标检测值等关键信息,且符合评估系统的设计规范。
4.2.3 管理要求
评估系统应该具备油品管理、装备管理、记录管理等功能。其中油品管理应该具备油品名称、牌号、
标准、制造厂、油品相关指标的合格区间、预警区间等管理功能。装备管理应该具备装备名称、型号、
编号、用油部件名称及用油品种、油品相关指标合格区间、油品相关指标预警区间、油品相关指标变化
趋势合格区间、变化趋势预警区间等管理功能。记录管理应该具备记录存储、导入、导出、查询、删除、
打印等管理功能。
管理功能应包括:新建、修改、删除、查看等功能。
4.3 评估模型建立
4.3.1 模型数据架构
模型数据架构见表1。
表1 模型数据架构表
油品信息 装备信息
装备1 装备2
1#装备1 2#装备1 1#装备2
部件1 部件2 部件1 部件2 部件1 部件2
1阶段 取样 2阶段 取样 1阶段 取样 2阶段 取样 1阶段 取样 2阶段 取样 1阶段 取样 2阶段 取样 1阶段 取样 2阶段 取样 1阶段 取样 2阶段 取样
油 品 1 指 标 1 指标值合 格区间 检测值 检测值 检测值 检测值 检测值 检测值
指标值预 警区 检测值 检测值 检测值 检测值 检测值 检测值
变化趋势 合格区间 检测值 检测值 变化率 检测值 检测值 变化率 检测值 检测值 变化率
变化趋势 预警区间 检测值 检测值 变化率 检测值 检测值 变化率 检测值 检测值 变化率
指 标 2 指标值合 格区间 检测值 检测值 检测值 检测值 检测值 检测值
指标值预 警区 检测值 检测值 检测值 检测值 检测值 检测值
变化趋势 合格区间 检测值 检测值 变化率 检测值 检测值 变化率 检测值 检测值 变化率
3
油品信息 装备信息
装备1 装备2
1#装备1 2#装备1 1#装备2
部件1 部件2 部件1 部件2 部件1 部件2
1阶段 取样 2阶段 取样 1阶段 取样 2阶段 取样 1阶段 取样 2阶段 取样 1阶段 取样 2阶段 取样 1阶段 取样 2阶段 取样 1阶段 取样 2阶段 取样
变化趋势 预警区间 检测值 检测值 变化率 检测值 检测值 变化率 检测值 检测值 变化率
油 品 2 指 标 1 指标值合 格区间 检测值 检测值 检测值 检测值 检测值 检测值
指标值预 警区 检测值 检测值 检测值 检测值 检测值 检测值
变化趋势 合格区间 检测值 检测值 变化率 检测值 检测值 变化率 检测值 检测值 变化率
变化趋势 预警区间 检测值 检测值 变化率 检测值 检测值 变化率 检测值 检测值 变化率
指 标 2 指标值合 格区间 检测值 检测值 检测值 检测值 检测值 检测值
指标值预 警区 检测值 检测值 检测值 检测值 检测值 检测值
变化趋势 合格区间 检测值 检测值 变化率 检测值 检测值 变化率 检测值 检测值 变化率
变化趋势 预警区间 检测值 检测值 变化率 检测值 检测值 变化率 检测值 检测值 变化率
4.3.2 模型数据生成
油品及指标:根据油品相关标准确定。
装备及部件:用户根据实际情况确定。
油品指标值合格区间:根据油品相关标准和装备特性确定,常用标准有:GB 11118.1、GB/T 7607、
GB/T 8028、GB/T 30034、SH/T 0475、NB/SH/T 0586、TB/T 1739、JB/T 12194等。
油品指标值预警区间:根据油品相关标准确定,常用标准有:GB 11118.1、GB/T 7607、SH/T 0476、
NB/SH/T 0599、SH 0358等。
检测值:油样的实际检测值。
变化率:(阶段2检测值-阶段1检测值)/取样里程差。
4.3.3 关联因素
油样各项指标间具有一定的关联性,其中污染度、水分、黏度、磨粒、原子发射光谱五项检测指标
的关联性如下图2所示:
4
图2 关联示意图
4.4 评估结果及报告
4.4.1 评估结果
应包括以下几方面内容:
a) 油品每个指标的合格与预警情况;
b) 油品每个指标变化率的合格与预警情况;
c) 油品各个指标的关联影响情况;
d) 油品技术质量状态;
e) 问题原因分析(常见原因分析可参考附录A);
f) 装备使用维护意见与建议。
4.4.2 报告
评估报告主要有:单次检测评估报告、多阶段检测评估报告、装备横向对比分析报告等。
报告应包括以下几个方面内容:
a) 磨粒检测图像;
b) 水分检测结果与标准值、预警值对比的图示;
c) 污染度检测结果与标准值、预警值对比的图示;
d) 黏度检测结果与标准值、预警值对比的图示;
e) 检测结果随取样时间变化趋势及变化率;
f) 检测结果与装备对应的对应比较情况。
5
附 录 A
(资料性)
常见指标异常原因分析参考
常见指标异常原因分析参考见表A.1。
表A.1 常见指标异常原因分析
序号 元素/指标 原因
1 银 Ag 润滑油劣变引起电镀层磨损;污染物进入引起电镀层磨损
2 铝 Al 润滑油劣变引起泵等部件磨损;润滑油劣变引起活塞、轴瓦、增压器等部件磨损
3 硼 B 灰尘等污染物异常进入润滑油中
4 钙 Ca 添加剂损耗大
5 铬Cr 润滑油劣变、污染物进入引起镀层磨损;
6 铜 Cu 润滑油劣变引起铜质部件磨损;污染物进入引起铜质部件磨损
7 铁 Fe 润滑油劣变引起活塞、导向套等部件磨损;污染物进入引起活塞、导向套等部件磨 损
8 镁 Mg 润滑油劣变引起油中的添加剂损耗
9 钠 Na 润滑系统受到海水污染
10 镍 Ni 润滑油劣变引起含鎳部件的磨损;污染物进入引起含鎳部件的磨损
11 磷 P(下限) 润滑油劣变引起油中的添加剂损耗
12 铅 Pb(上限) 润滑油受到异物污染
13 硅 Si 外部灰尘进入润滑油
14 锌 Zn(下限) 润滑油劣变引起油中添加剂损耗
15 锌 Zn(上限) 密封件磨损
16 锡 Sn 焊接部位磨损
17 磨粒 传动机构异常磨损;润滑系统存在污染物
18 水分 系统长时间在相对湿度较高的地方工作,空气中水分进入液压系统内;非正常原因 导致水进行润滑系统
19 粘度 油液污染;磨损物增加;轻馏成分蒸发;高温氧化严重;油品劣化;水、燃油进入 润滑系统;添加剂损耗严重
20 污染度 过滤失效;外部灰尘、铁屑、杂质等进入系统;系统执行机构异常磨损;油液加注 过程受到污染
________________________
6