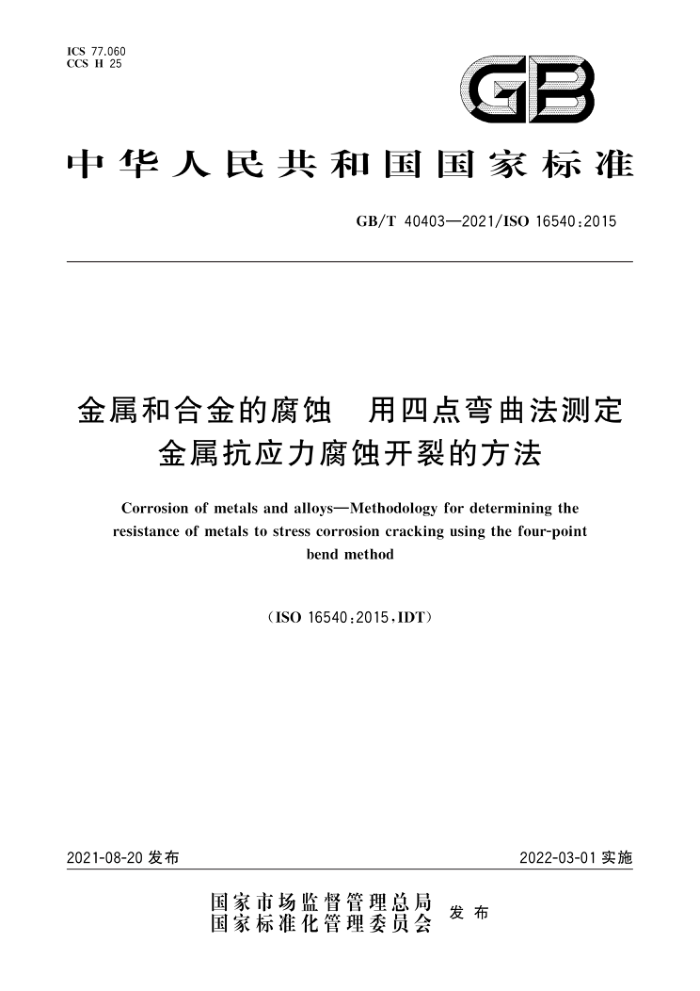
ICS 77.060 CCS H 25
GB
中华人民共和国国家标准
GB/T40403—2021/ISO16540:2015
金属和合金的腐蚀 用四点弯曲法测定
金属抗应力腐蚀开裂的方法
Corrosionof metals and alloysMethodology fordetermining the resistance of metals to stress corrosion cracking using thefour-point
bend method
(ISO 16540:2015,IDT)
2022-03-01实施
2021-08-20发布
国家市场监督管理总局国家标准化管理委员会
发布
GB/T40403—2021/IS016540:2015
前言
本文件按照GB/T1.1一2020《标准化工作导则 第1部分:标准化文件的结构和起草规则》的规定起草。
本文件使用翻译法等同采用ISO16540:2015《金属和合金的腐蚀 虫用四点弯曲法测定金属抗应力腐蚀开裂的方法》。
与本文件中规范性引用的国际文件有一致性对应关系的我国文件如下:
GB/T16545一2015金属和合金的腐蚀腐蚀试样上的腐蚀产物的清除(ISO8407:2009 IDT)。
本文件由中国钢铁工业协会提出。 本文件由全国钢标准化技术委员会(SAC/TC183)归口。 本文件起草单位:安科工程技术研究院(北京有限公司、安工腐蚀检测实验室科技(无锡)有限公
司、冶金工业信息标准研究院、帕博检测技术服务有限公司、国标(北京)检验认证有限公司、中车青岛四方机车车辆股份有限公司、北京科技大学。
本文件主要起草人:王修云、薛俊鹏、侯捷、张雷、樊志罡、曹炳亮、张志毅、田子健、李晓刚、杨志文、 樊学华、翟晓玮、吴绍泉、孙晓光、孙梦寒、杜翠薇、陈迎锋。
1
GB/T40403—2021/IS016540:2015
金属和合金的腐蚀用四点弯曲法测定
金属抗应力腐蚀开裂的方法
1范围
本文件提供了四点弯曲试验指南,用于评估包含碳钢、低合金钢和耐蚀合金在内的金属抗应力腐蚀开裂性能。本文件给出了对母材和焊缝的试验指导,包含了适用于应力应变行为中无明显和有明显屈服点金属的试验程序。本文件是四点弯曲试验的通用方法,由于服役环境的多样性,在适当情况下可参照相关标准。
2规范性引用文件
下列文件中的内容通过文中的规范性引用而构成本文件必不可少的条款。其中,注日期的引用文件,仅该日期对应的版本适用于本文件;不注日期的引用文件,其最新版本(包括所有的修改单)适用于本文件。
ISO8407 7金属和合金的腐蚀 虫腐蚀试验样品中腐蚀产物的去除(Corrosionofmetalsand alloysRemovalof corrosionproducts from corrosiontest specimens)
3术语和定义
下列术语和定义适用于本文件。
3.1
耐蚀合金 corrosion resistance alloy;CRA 在碳钢可发生腐蚀的环境中,耐全面腐蚀和局部腐蚀的合金。
3.2
热影响区heataffectedzone:HAZ 在焊接或切割过程中,母材金属未熔化但组织和性能因受热发生变化的部分
3.3
软区开裂 softzonecracking;SzC 当钢中含有低屈服强度的局部“软区”并在应力作用下暴露于含H.S的环境时,可能发生的一种硫
化物应力开裂形式。
注:在服役载荷下,软区可能会屈服并在局部累积塑性变形,增加抗开裂材料的开裂敏感性。这些软区通常与碳钢
焊缝有关。
4试验原理
四点弯曲试验是一种恒位移试验,在两个加载辊(轴承圆柱)上支撑弯梁试样,另外两个加载辊施加载荷以使试样的一个面处于拉伸状态(在内加载辊之间均匀受力),而另一个面处于压缩状态来实现。 试样截面中间厚度处的应力为零,应力梯度在厚度方向有显著的变化,薄试样变化更为明显。裂纹可能萌生,但随后裂纹会停止扩展或其扩展速率降低。因此,在试验暴露期内发生完全断裂的可能性比较
1
GB/T40403—2021/IS0 16540:2015
低。重要的参数包括加载辑间距、内外加载辊跨度比、试样尺寸、宽厚比和加载辊直径。由于焊接试样在焊根形貌、表面粗糙度、微观裂纹缺陷程度、错边角度上的显著差异,对焊接试样进行试验难度较大。
5加载夹具设计
5.1应使用与图1类似的加载夹具,对试样施加恒定挠度。通常选择尺寸使A=H/4。
H
.
标引序号说明: 1—试样厚度; A-相邻内外支点间的距离; H--外支点间的距离。
图1典型四点弯曲加载夹具设计
5.2通常母材试样的厚度最大可取到5mm,这样的试样连同典型尺寸的加载具可比较容易地放入常规试验容器内。典型的加载夹具尺寸如下:内加载辑辊间的距离为50mm~60mm;外加载辊的距离为100mm~130mm;加载辊直径为6mm~10mm。 5.3焊接试样建议采用较厚的试样(厚度可以是全壁厚)进行测试。此处,可通过增大支点间距来减小加载载荷,但需要确保尺寸增加后的夹具能够放人合适规格的测试容器内。此处可自行判断。 5.4试样和加载夹具之间应电绝缘,以避免电偶腐蚀和缝隙腐蚀。优先选用陶瓷材料的支撑辑可实现电绝缘,同时试验过程中陶瓷支撑辊无屈服变形或蠕变。 5.5应尽可能减小支撑辑与试样间的摩擦力,以确保摩擦约束不影响试样上的应力分布。通过使用低摩擦接触表面的陶瓷辊可很好地达到此目的。如试样加载时低摩擦接触表面的陶瓷辊可以自由转动,此影响可进一步减少。如陶瓷辑不可自由转动,摩擦力的存在将会影响达到所需应变所用的加载力大小。如试样经过应变仪测试且摩擦力不大,摩擦将不会影响测试结果。尽管如此,摩擦的增加会使得内加载点拉伸表面局部的应力应变增加,提高试样中这些位置裂纹形成的可能性(见第11章)。在特定测试条件下,可通过该区域的应变测量来评估特定加载夹具的过度应变程度 5.6加载夹具用材料应在测试环境中抗应力腐蚀开裂,同时夹具应有足够的刚度。通过选用耐蚀合金材料制作夹具或在夹具上增加涂层的方式均可避免夹具腐蚀产物对试验溶液的污染,从而避免对测试结果产生影响。当用耐蚀合金的夹具进行碳钢或低合金钢测试时,可能发生由腐蚀产物导致试样和夹具之间的电连接,为此需要在试验结束时进行电阻检查。如果没有进行电绝缘处理,那么夹具应选用与试样相似的材质。在对碳钢和低合金钢进行测试时,优先采用低合金钢夹具可避免电偶效应的影响。 在这种情况下,为夹具选择合适的惰性涂层能够尽可能减少腐蚀产物的堆积。
2
GB/T40403—2021/ISO16540:2015
6试样制备
6.1概述 6.1.1四点弯曲试样应是具有均匀矩形截面和均匀厚度的平直条带,除非测试一面是原始焊缝截面非均匀的焊接试样、测试管材内侧原始表面状态(截面下凹)的试样或测试管材外侧原始表面状态(截面上凸)的试样。 6.1.2试样两端应有永久性标记或编号。因端部应力最低,标记不会诱发裂纹萌生。 6.1.3对氢致损伤敏感的材料,不应使用可能在样品表面产生氢的制备方法,如电火花切割等。如果采用这类加工方式,需要对试样外表面进行研磨以消除材料表面残留的氢,研磨应尽可能快地进行以缩短氢从外表面扩散到试样内的时间。研磨移除的厚度宜根据材料中有效氢扩散系数进行保守评估。对大多数耐蚀合金而言,从试样每个表面去除500um是足够的。也可以考虑烘烤除氢,但是这种方法不可导致材料微观组织的变化。 6.2母材试样 6.2.1母材试样经机加工制备,避免尖锐边缘。从管或板的纵向取样,除非另有规定。 6.2.2典型四点弯曲母材试样如图2a)所示。
a) 母材试样
b)焊接试样
图2典型四点弯曲试样
6.2.3试样宽度应是试样厚度的1.5倍~5倍。对这一要求的任何偏离,如非常厚的碳钢,需要证明试样平面外侧的弯曲不明显。 6.2.4可对拉伸测试表面处于原始表面状态未经表面打磨处理的试样进行测试。对表面的打磨处理通常会使近表面材料性能出现预期外的变化。否则,需征得用户同意对试样表面采用一致的、可重复的表面处理方法,通常要求任何非焊接试样表面粗糙度Ra≤0.25um。试样在加工过程中应避免过热和
3
GB/T40403—2021/IS016540:2015
不必要的表面冷加工。润滑剂的使用可影响试样表面化学特性,需选用适当试剂对试样除油,并采用丙酮等溶剂清洗。清洗步骤的效果应进行验证,如雾化试验。 6.2.5试样边缘的毛刺可通过手工打磨的方法去除。 6.3 焊接试样 6.3.1焊接试样应垂直于焊缝取样,并且焊缝应位于试样中部,除非另有规定, 6.3.2典型四点弯曲焊接试样如图2b)所示。 6.3.3当试样一面为焊接状态(表面未经过打磨处理)时,由于焊接错边的存在,只从单侧加工通常会导致焊缝两侧厚度的差异,这种情况应注意记录。厚度的变化会导致试样不均匀形变,但对较厚试样影响较小。可优选近全厚度的试样进行测试。 6.3.4当试样的一面为焊缝时,与外支点接触的位置应加工平整,防止因试样弧度导致陶瓷支点处存在局部高应力集中。否则,加载辊可能断裂。 6.3.5两面均加工的焊接试样,试样宽度应是试样母材厚度的1.5倍~5倍。偏离这一要求,如非常厚的碳钢,需要证明试样平面外侧的弯曲不明显。 6.3.6由锥度、错边、弯曲(如果是从管件加工成的焊缝)导致的试样厚度差异应进行记录。 6.3.7当测试焊缝经完整加工时,受张应力表面宜尽可能贴近原始表面,因为沿厚度方向可能会存在硬度和组织的差异。尤其应保留打底焊焊道(或盖面焊的最后一个焊道)。因此,在测试前对硬度和组织特征进行详细表征有助于评估差异程度、指导试样准备、识别任何影响测试结果的因素。厚度方向的残余应力也有差异。因此,相对于原始表面的受拉表面应进行标注,试样切割方式要保持一致。试样表面按6.2.4处理。通常表面粗糙度Ra≤0.25μm。试样在加工过程中应避免过热和不必要的表面冷加工。润滑剂的使用可影响试样表面化学特性,按6.2.4选用适当试剂对试样除油,并采用丙酮等溶剂清洗。 6.3.8试样边缘的毛刺可通过手工打磨的方法去除。 6.4覆层试样 6.4.1当试样取自复合管或压力容器壁的耐蚀合金时,应通过机加工彻底去除碳钢基体。这意味着采用薄试样进行试验。
注:例如可通过硫酸铜测试检查碳钢基体的清除效果 6.4.2除非用户另有规定,对焊接试样,焊缝余高应去除。余高的去除应尽可能小地损伤附近热影响区和母材区,因为这些区域的表面状况会影响试验结果。
7应变测量
7.1当试样加载可能导致塑性变形时,需要进行应变测量。应变测量指南见附录B。 7.2在加载应力导致塑性变形条件下对母材试样进行测试,应将应变片贴附在校准试样受拉应力面的中心位置。 7.3对焊缝试样进行测试,应将应变片贴附在试样母材中心位置、焊缝金属对称的两侧,尽可能贴近焊趾处但具有足够的距离,使得测得的应变值不受任何局部应力/应变集中、非均匀表面或热影响区机械性能的直接影响。应变仪传感器距离焊趾通常是3mm~5mm,测量时应记录应变片位置。 7.4在对焊接试样进行应变测量时,应变片的贴附和移出应尽量减少对试样表面状态的影响。可在尽可能小的区域内按6.2.4进行脱脂处理。应注意尽量减小受影响的面积
7