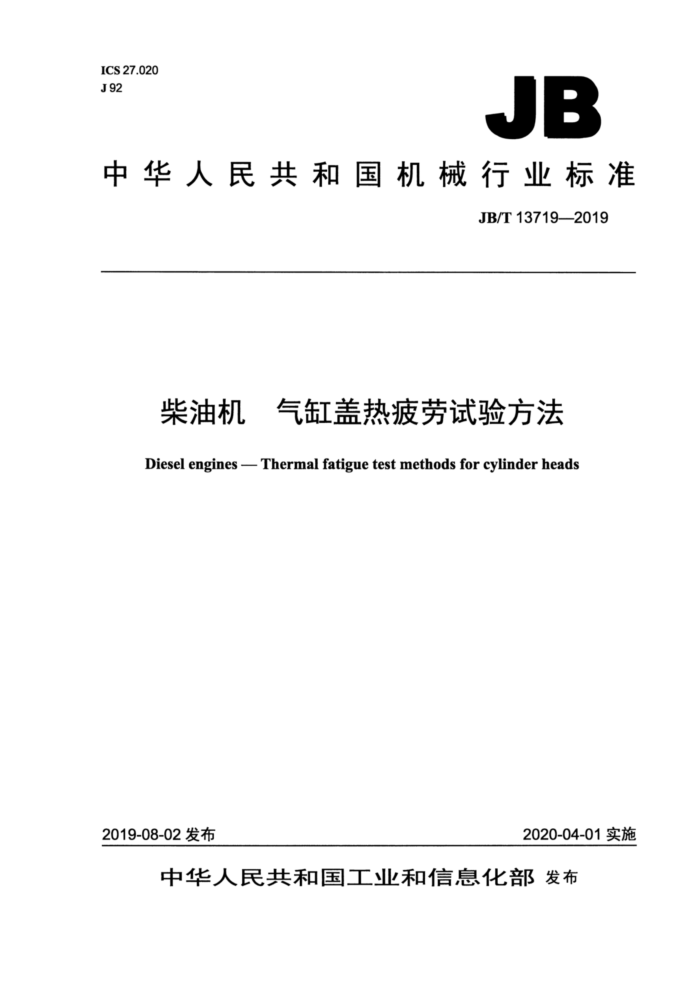
ICS 27.020 J92
JB
中华人民共和国机械行业标准
JB/T13719—2019
柴油机 气缸盖热疲劳试验方法 Diesel engines - Thermal fatigue test methods for cylinder heads
2019-08-02 发布
2020-04-01实施
中华人民共和国工业和信息化部发布
JB/T 13719—2019
目 次
前言. 1 范围. 2规范性引用文件 3术语和定义 4试验条件.. 5试验方法.. 5.1 试验原理 5.2 试验装置. 5.3 试验准备. 5.4 试验规范. 5.5 试验规范的参数调整 5.6试验步骤, 5.7 试验数据记录 6试验结果整理 6.1寿命分布规律分析. 6.2寿命比较及寿命预测模型. 7试验报告
0
.....
+4
6
6
图1 气缸盖受热区域温度场变化规律图2电磁感应加热器结构示意图. 图3热电偶测点分布示意图.
n
表 1 热疲劳试验记录表
JB/T 13719—2019
前言
本标准按照GB/T1.1一2009给出的规则起草。 本标准由中国机械工业联合会提出。 本标准由全国内燃机标准化技术委员会(SAC/TC177)归口。 本标准起草单位:北京理工大学、潍柴动力股份有限公司、上海内燃机研究所、广西玉柴机器股份
有限公司、上海汽车集团股份有限公司商用车技术中心、昆明理工大学。
本标准主要起草人:张卫正、原彦鹏、王志坚、乔亮亮、黎华文、孟红霞、王潇嵩、于惠、陈国争、 雷基林、吴定勇、陈翠翠、贾德文。
本标准为首次发布。
I
JB/T 13719—2019
柴油机气缸盖热疲劳试验方法
1范围
本标准规定了采用电磁感应加热方式的柴油机气缸盖热疲劳试验方法。 本标准适用于气缸直径小于或等于300mm的柴油机气缸盖(以下简称气缸盖)。
2 规范性引用文件
下列文件对于本文件的应用是必不可少的。凡是注日期的引用文件,仅注日期的版本适用于本文件。凡是不注日期的引用文件,其最新版本(包括所有的修改单)适用于本文件。
GB/T26142010镍铬-镍硅热电偶丝 GB/T10623-一2008金属材料力学性能试验术语
3 术语和定义
GB/T10623一2008界定的以及下列术语和定义适用于本文件。
3.1
热疲劳 thermal fatigue 由温度场变化引起受热零件内部应力、应变改变而导致的材料损伤以致开裂的现象。
3.2
稳态温度steadytemperature 柴油机工作时,某一稳定工况下受热零件上各点的时间平均温度。
3.3
瞬态温度transient temperature 在柴油机工作循环(进气一压缩一燃烧一膨胀一排气)中,受热零件上与燃气接触区域的瞬时变化
温度。 3.4
高频温度波幅high frequency temperature range 柴油机的一个工作循环中,受热零件表面瞬态温度的变化幅值。
3.5
低频热疲劳low-cyclethermal fatigue 由柴油机起动一工作一停机循环或柴油机负荷大幅度变化引起受热零件稳态温度发生变化,进而引
发的零件材料热疲劳失效的现象。 3.6
高频热疲劳high-cycle thermal fatigue 由柴油机工作循环引起受热零件表面瞬态温度发生高频的变动,进而引发的零件材料热疲劳失效的
现象。 3.7
热疲劳寿命thermal fatigue lifetime 柴油机受热零件达到热疲劳失效判据时所对应的实际循环数。
1
JB/T 13719—2019
4试验条件
试验环境的相对湿度不应高于70%。环境中不应有其他能够造成气缸盖温度变化的热辐射和电磁波辐射干扰的影响因素存在。
5试验方法
5.1试验原理 5.1.1采用高频电磁感应加热和强制气冷的方法对气缸盖进行快速加热和冷却,使气缸盖的工作受热区域产生试验所要求的温度场变化。 5.1.2热疲劳试验中,气缸盖受热区域的温度变化规律如图1所示,气缸盖经历加热一保温一冷却过程完成一个热疲劳循环,模拟在柴油机工作中的起动一工作一停机的低频热疲劳循环过程。
T/℃ + Tmax
BW
Tmin
加热保温图1气缸盖受热区域温度场变化规律
t/s
冷却
5.1.3气缸盖的热疲劳试验不考虑机械负荷的影响,气缸盖在热载荷作用下由结构的自约束产生热应力。 5.1.4气缸盖在正常工作状态下会因工作循环而产生高频的温度变化,通过对气缸盖关键区域(火力面气门鼻梁区)进行最高温度的修正,在一定程度上考虑气缸盖高频热疲劳对寿命的影响。 5.2试验装置 5.2.1气缸盖安装试验台
气缸盖安装试验台用于热疲劳试验中气缸盖的安装和固定。 5.2.2感应加热台架
感应加热台架用于对气缸盖进行感应加热。输出功率应可调,能满足气缸盖的加热时间要求。 5.2.3吹风冷却系统
吹风冷却系统用于对气缸盖进行冷却。风机的功率和通风量应能满足气缸盖的冷却时间要求。可以对气缸盖进、排气道(推荐)或冷却水道进行吹风冷却。需要设计冷却导风与气量控制装置,以实现冷却气流的导向与调节。 5.2.4控制与数据采集系统
控制与数据采集系统用于采集热疲劳试验过程中气缸盖热电偶测点的温度数据,并进行气缸盖热疲劳试验过程的控制,同时记录热疲劳循环次数。
2
JB/T 13719—2019
5.3试验准备 5.3.1获取气缸盖稳态温度场及高频温度波幅
通过柴油机的台架试验测量或仿真计算得到气缸盖的稳态温度场以及火力面的瞬态温度,确定气缸盖关键区域的稳态温度和高频温度波幅。 5.3.2设计电磁感应加热器 5.3.2.1根据气缸盖的具体结构型式和实际温度场分布规律进行电磁感应加热器的设计制作。 5.3.2.2电磁感应加热器推荐采用单匝矩形截面纯铜材质的感应线圈,其结构如图2所示。
母母
? 由
$
D-D
回
DL
图2电磁感应加热器结构示意图
5.3.3试验温度场测量 5.3.3.1在火力面上选择合适位置钻取热电偶安装孔,并加装热电偶(推荐采用K型热电偶和符合 GB/T2614一2010规定的热电偶丝材质)。 5.3.3.2应沿气门鼻梁区至少布置10个热电偶测点,以提高温度场测量精度,热电偶测点分布示意图如图3所示。
排气门
排气门
15 16
10
9
4
进气门
进气门
+8
图3热电偶测点分布示意图
3
JB/T 13719—2019
5.3.3.3气缸盖试验温度场的测量在感应加热台架上进行。 5.3.4温度场对比 5.3.4.1将试验条件下测量的气缸盖温度场与实际台架测量(或仿真预测)的温度场数据进行对比。 5.3.4.2应保证气缸盖关键区域的最高平均温度与实测值之间的误差不高于10℃,非加热背侧面(气缸盖的外壁面)最高温度不高于其实测温度,由温度控制调节引起的关键区域温度波动△Tmax不高于30℃ (△Tmax为图1中的控制温度震荡幅度)。 5.3.5温度监控点的选择 5.3.5.1热疲劳试验中温度监控点的选择应避开气缸盖关键区域,推荐选择图3中的测点9、10、15、 16位置之一作为热疲劳试验过程中的温度监控点。 5.3.5.2温度监控点的控制参数应根据热疲劳加载过程中监控点与关键区域的温度变化规律进行设定,保证关键区域能够达到试验要求的最高温度。 5.4试验规范 5.4.1加热时间 5.4.1.1加热时间宜为30s,通过调节感应加热台架的加热功率来保证。 5.4.1.2为了减少材料循环软硬化的影响,要求热疲劳试验过程中的气缸盖台架寿命高于200循环 5.4.1.3当气缸盖的试验热疲劳寿命高于3000循环时,可以通过提高加热速度使零件加速破坏,降低气缸盖的台架寿命。 5.4.2最低控制温度
最低控制温度宜为120℃,应保证能将气缸盖冷却到一个整体基本均匀的温度。 5.4.3最高控制温度 5.4.3.1热疲劳试验过程中气缸盖关键区域的最高温度应等于稳态温度与高频温度波幅(用于考虑高频热疲劳的影响)之和。 5.4.3.2温度控制点的最高控制温度应为关键区域达到最高温度时所对应的温度控制点的温度 5.4.4保温时间
推荐保温时间为60s,以使气缸盖温度场与工作过程实际温度场基本一致,进而模拟整体热约束状况。 5.4.5冷却时间 5.4.5.1不同缸径气缸盖的冷却时间要求不同。 5.4.5.2对缸径为150mm及以下的气缸盖,冷却时间不应超过2min。 5.4.5.3对缸径大于150mm气缸盖,冷却时间不应超过4min。 5.4.5.4采取强化冷却的措施时,若在冷却空气中喷雾强化冷却,冷却时间应超过1min。 5.4.6热疲劳试验的件数要求
每一个工况点应测试3个或3个以上试验件,热疲劳试验用气缸盖应选用成品合格气缸盖。
4
JB/T 13719—2019
5.4.7试验终止条件(破坏条件) 5.4.7.1以气缸盖关键区域出现2mm以上的可视裂纹作为气缸盖热疲劳试验的终止条件。 5.4.7.2若气缸盖关键区域始终未出现裂纹,则按照气缸盖热疲劳试验考核要求的循环数作为终止条件。 5.5试验规范的参数调整 5.5.1加热时间的调整 5.5.1.1当气缸盖热疲劳试验寿命高于3000循环时,可提高加热速度以减少加热时间,调整方法如下:
-加热时间为20s~30s时,每次调整可减少5s的加热时间,并进行3个试验件的热疲劳试验,以保证热疲劳寿命结果的可靠性;加热时间为10s20s时,每次调整可减少3s的加热时间,并进行3个试验件的热疲劳试验,以保证热疲劳寿命结果的可靠性;加热时间为10s以内时,每次调整可减少2s的加热时间,并进行3个试验件的热疲劳试验,以保证热疲劳寿命结果的可靠性,加热时间不应低于2S。
5.5.1.2当气缸盖热疲劳试验寿命低于200循环时,需降低加热速度以增加加热时间,调整方法如下:每次调整增加5s的加热时间,并进行3个试验件的热疲劳试验,以保证热疲劳寿命结果的可靠性。
注:加热时间参数调整时所进行的气缸盖热疲劳试验数据可用来进行该型号气缸盖的热疲劳寿命规律的模型拟合。 5.5.2保温时间的调整 5.5.2.1当保温过程结束时气缸盖的非加热背侧面(气缸盖的外壁面)温度低于实测温度30℃以上时,应增加保温时间,调整范围为60s~120s。 5.5.2.2当保温过程结束时气缸盖的非加热背侧面(气缸盖的外壁面)温度高于实测温度时,应减少保温时间,调整范围为0 s~60s。 5.6 试验步骤 5.6.1根据试验温度场测量的数据结果确定热疲劳试验的试验参数,在控制器中进行参数设置。 5.6.2在气缸盖安装试验台上安装固定气缸盖,将温度控制点热电偶引线连接控制器,启动感应加热台架,对气缸盖进行预热。 5.6.3开始试验,气缸盖经加热一保温一冷却过程完成一个热疲劳循环,计数器增加1,并重新开始下一个热疲劳循环。 5.6.4每隔100循环进行一次气缸盖检测,观察气缸盖关键区域是否出现可视裂纹,出现裂纹后,应缩短检测的循环间隔。 5.6.5当试验达到终止条件时,试验结束,获得一个气缸盖的台架热疲劳寿命数据。 5.7试验数据记录
气缸盖的热疲劳试验数据按表1的规定,可根据试验中实际的测点数量对表1做相应调整。
表1热疲劳试验记录表 」最高控制温度 」最低控制温度
裂纹长度 mm
序号 加热时间 保温时间」冷却时间
裂纹位置
循环次数
℃
℃
S
s
S
1 2 .
5