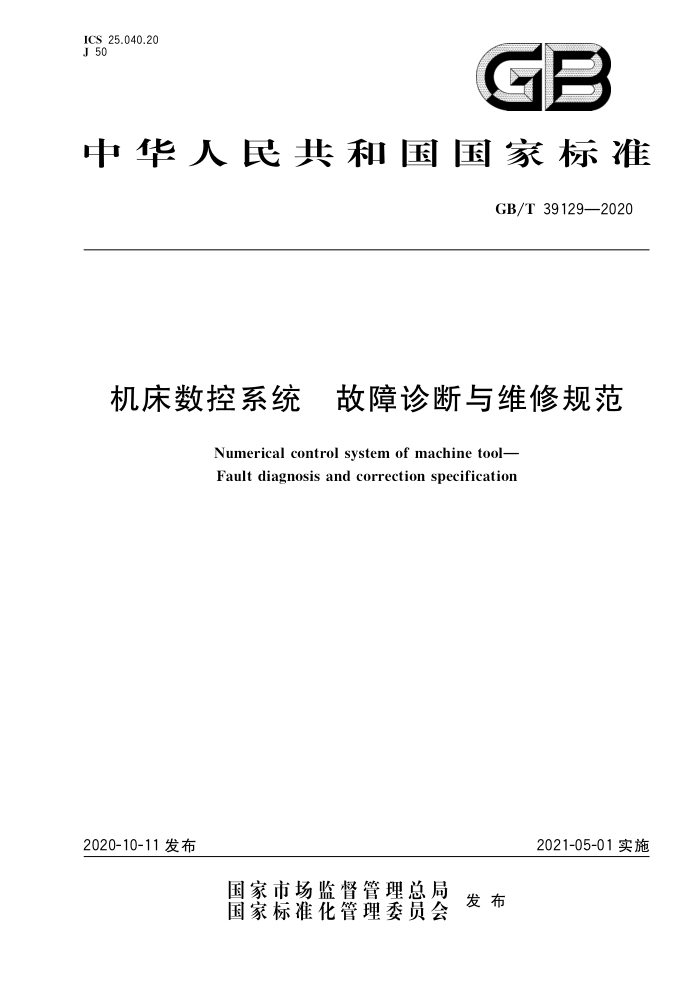
ICS 25.040.20 J 50
GB
中华人民共和国国家标准
GB/T 39129—2020
机床数控系统 故障诊断与维修规范
Numerical control system of machine tool- Fault diagnosis and correction specification
2021-05-01实施
2020-10-11 发布
国家市场监督管理总局
国家标准化管理委员会 发布
GB/T 39129—2020
前言
本标准按照GB/T 1.1一2009 给出的规则起草本标准由中国机械工业联合会提出。 本标准由全国机床数控系统标准化技术委员会(SAC/TC 367)归口。 本标准起草单位:华中科技大学、武汉华中数控股份有限公司、广州数控设备有限公司、北京航空航
天大学、沈阳高精数控智能技术股份有限公司、长春禹衡光学有限公司、沈机(上海)智能系统研发设计有限公司、科德数控股份有限公司。
本标准主要起草人:金健、张航军、何英武、彭、吴文江、林长友、王声文
1
GB/T 39129—2020
引言
数控机床是制造装备的装备,有“工作母机”之称,在装备制造业中具有极为重要的地位,广泛应用
于航空、航天、造船、轻工、汽车、纺织等产业领域。数控系统是数控机床的核心部件,在很大程度上决定着数控机床的功能和性能。随着功能的逐步强大,数控系统在高速、高精、曲面、柔性、复合等复杂工艺中的应用越来越多。然而功能越强大,发生故障时造成的危害就越大。因故障诊断与维修不及时或诊断与维修不当造成的直接和间接损失(包括坏料、刀具、工作台、机床本体、数控系统本身等的损坏、对人身及环境的伤害以及因停机误工造成的损失等)大约在数亿元量级(数控系统行业产值在百亿元量级)。 为了降低这些危害,减少损失,采取并实施行之有效的故障诊断与维修方法,对故障进行定位并使其得到快速修复显得尤为重要。制定数控系统故障诊断与维修技术标准,对数控系统故障诊断与维修方法、 故障诊断与维修流程、故障与维修数据统计等加以规范,对于提高故障诊断和维修效率具有重要的意义,能够有效提升数控系统的可靠性,减少用户损失。
Ⅱ
GB/T 39129—2020
机床数控系统 故障诊断与维修规范
1范围
本标准规定了机床数控系统在故障诊断与维修方面的技术要求本标准适用于机床数控系统。
2 术语和定义
下列术语和定义适用于本文件。
2.1
机床数控系统 numerical control system of machine tool 采用数值控制方式控制机床加工功能的控制系统。 注1:机床数控系统一般包含硬件装置和相应的软件。机床数控系统主要由数控装置(也称控制单元)、驱动装置
(电动机的驱动单元和电动机、传感器)等组成。数控装置是机床数控系统的主要部分,主要包括微处理器、运动(位置)控制器、存储器、输人/输出(I/O)与通信接口、人机界面(显示与键盘)、操动按钮(按键)等硬件(和)或电路)以及相应的控制软件。
注2:机床数控系统有多种分类方法。根据功能的不同,机床数控系统通常分为简易型、高性能型和普及型三种;根
据应用工艺的不同,可分为专用和通用数控系统两种;根据反馈控制形式的不同,可分为开环控制、半闭环控制和闭环控制三种;根据加工控制方式的不同,可分为点位控制、直线控制和轮廓控制三种。
注3:改写JB/T11989—2014,定义2.1.3。
2.2
故障fault 机床数控系统不能完成要求的功能的状态。预防性维修或其他计划的行动或因缺乏外部资源的情
况除外。
注1:故障通常是产品自身失效引起的,但即使失效未发生,故障也可能存在。 注2:改写 GB/T 2900.13—2008,定义 191-05-01。
2.3
故障诊断 fault diagnosis 为故障识别、故障定位和分析故障原因所采取的行动。 [GB/T 2900.13—2008,定义191-07-22]
2.4
故障维修 fault correction 故障修复故障定位后,为使故障产品恢复到能完成要求的功能的状态所采取的行动。 注:改写 GB/T 2900.13—2008,定义191-07-23。
3机床数控系统故障
3
3.1概述
机床数控系统常与其控制对象(如机床)配合运行,二者之间具有复杂的结构和功能关系,机床数控
GB/T 39129—2020
系统故障也因此涉及机床数控系统本体及其控制对象两个层面。通常以故障现象判定故障发生,以故障原因或机理判定故障归属
3.2故障判据
故障判据是判断某事件是否为故障的依据。如无特别约定,一般认为在机床数控系统发生下列任何一项事件时,即判定发生故障:
a)不 在规定的工作条件下,不能进人工作状态; b)在规定的工作条件下,不能完成规定的功能; c) 在规定的工作条件下,任一性能参数值偏离规定的范围; d)不 在规定的工作条件下,对人员、环境、能源和物资等方面的影响超出了允许范围;
出现机械零部件、结构件或元器件的松动、断裂或损毁;
e)
f)其他约定的和/或技术文件中规定的事件。 注:故障判据用来判断是否发生故障,不用来判定故障归属。
3.3故障类型
3.3.1概述
对机床数控系统故障进行分类,其目的在于对故障形成多角度、多层面的认识和理解,有利于故障数据的统计、分析和应用。 3.3.2关联故障
关联故障通常指在规定条件使用、存储、运输等情况下由机床数控系统内在原因造成的故障,主要用来分析数控系统内在的可靠性状况,是机床数控系统主要的故障统计对象。机床数控系统出现下列任何一种事件即应判为关联故障:
a)设计缺陷或制造工艺缺陷造成的故障; b) 元器件缺陷造成的故障; c)耗损件在寿命期内造成的故障; d) 由于软件造成的故障; e) 测试期间由于非从属性故障原因产生的故障征兆(未超出性能极限)而引起的更换; f) 原因不明的故障。
3.3.3非关联故障
非关联故障通常指由机床数控系统外部原因造成的故障,主要用来分析外部条件对数控系统可靠
性的影响。机床数控系统出现下列任何一种事件即应判为非关联故障:
a) 由于安装、调试不当造成的故障; b)测试设备、检测设备、仪器等故障引起的受试机床数控系统的故障; c) 由于意外事故或误操作引起的故障; d) 由机床本体、负载电机等其他产品引起的从属故障; e) 由测试程序、规程等方面的错误引起的故障; f) 在正常筛选、寻找故障、修复验证或维护调整中发生的故障; g) 由于超过设计引起的过应力所造成的故障; h) 超寿命期工作时出现的故障;
i) 其他数控系统外部原因引起的故障; j) 其他规定或约定的非关联故障(如间歇性的故障)。 2
GB/T 39129—2020
3.3.4阶段故障
根据在寿命周期中发生阶段的不同,故障可分为以下几种: a)早期故障:一般指出厂投人使用后的一段时间内发生的故障,主要由设计和制造的缺陷引起。
早期故障发生概率通常随时间推移呈现由高到低的变化趋势。
b)稳定期故障:在早期故障期和后期故障期之间发生的故障,也称偶发故障。此期间故障发生概
率较低,故障率趋于平稳,具有一定的偶然性。 c) 后期故障:也称损耗故障。稳定期之后发生的故障,故障发生概率随时间的推移而增大。一般
认为后期阶段时数控系统处于加剧损耗甚至报废状态。
3.3.5环节故障
根据所处生产、使用等环节的不同,故障可分为以下几种: a)7 材料故障:由于材质不当引起的故障; b)设计故障:由于设计不当引起的故障; c) 制造故障:由于制造不当引起的故障; d) 运输故障:由于运输不当引起的故障; e) 贮存故障:由于贮存不当引起的故障(正常的老化除外); f) 安装调试故障:由于安装调试不当引起的故障; g) 使用故障:由于使用不当引起的故障。
3.3.6严重度故障
根据造成后果严重程度的不同,故障可分为以下几种: a)致命故障:导致数控系统无法运行、人员受到伤害、故障之外物件受到损毁或其他严重后果的
故障。 b)i 重度故障:导致数控系统主要功能无法实现的故障 c)轻度故障:除致命故障和重度故障外的其他故障。 注:定性分析时,严重度故障各等级之间没有十分清晰的界限。定量分析时,可根据需要设定指标给各等级划分具
体的数值边界,可参考 GB/T 7826 的有关做法。
3.3.7持续性与非持续性故障
根据是否具有持续性,故障可分为以下两种: a)持续性故障:直到实施修复性维修前持续存在的故障。也叫持久性故障。 b)非持续性故障:在有限的持续时间内出现,随后未经任何修复性维修即能恢复完成要求功能的
故障。
3.4 故障原因
故障原因即导致故障发生的原因。根据来源的不同,故障原因可分为内部原因和外部原因两种。 其中,内部原因指机床数控系统材料、设计、制造等内在的原因;外部原因包括外部人为原因和非人为原因。外部人为原因指操作、管理等人员误操作、人为提高机床数控系统工作强度、条件应力或恶化工作条件等原因;外部非人为原因指外界产生的电磁干扰、电源中断、雷击、振动等原因。
根据导致故障原因数量的不同,故障原因可分为单原因和多原因两种。
4机床数控系统故障诊断与维修
4.1概述
机床数控系统故障诊断与维修一般指对故障进行定位、确认并排除的做法和过程。机床数控系统
3
GB/T 39129—2020
的故障诊断与维修工作可人为执行,也可利用具有相应功能的设备来执行
机床数控系统故障诊断与维修可能需要与其控制对象的故障诊断与维修结合起来进行。 4.2故障诊断与维修基本流程
机床数控系统故障诊断与维修的基本流程如图 1 所示。
故障现象发生
查看状态及向现场人员了解情况
有损坏、断裂、 松动、异味等
否
查看报警信息及故障代码
是
有报警信息或故障代码
是
进行故障诊断与维修
否
开机调试试运行
运行数控系统
是
否
故障是否再现
故障是否排除
否
N
故障诊断与维修记录
故障诊断与维修结束
注1:本流程仅为机床数控系统故障诊断与维修工作的开展提供基本参考,并不是唯一流程。 注2:数控系统电源有控制电源和动力电源两种,两者的接通与断开可能会对故障诊断与维修造成不同的影响。
图 1机床数控系统故障诊断与维修的基本流程
4.3故障诊断与维修方法 4.3.1故障诊断方法
故障诊断方法有很多种,原则上可分为自诊断和人工诊断两类:
GB/T 39129—2020
a)自诊断:主要利用机床数控系统的自诊断功能来对故障进行定位;常用的自诊断方法包括开机
自诊断、运行自诊断、脱机自诊断三种: 1)开机自诊断:机床数控系统通电后,系统内部自诊断软件对系统中关键的硬件和控制软件
(如装置中的CPU、RAM等芯片、MDI、I/O等模块及监控软件、系统软件等)逐一进行检测,并将检测的结果显示出来。
2)运行自诊断:机床数控系统正常(或部分正常)运行时,运行内部诊断程序,对系统本身、
PLC、伺服驱动装置、主轴驱动装置等及与数控装置相连的其他外部装置进行自动测试、 检查,并显示有关的状态信息和故障信息。
3)脱机自诊断:机床数控系统出现故障时,利用外部的诊断程序对系统进行诊断并显示有关
的状态信息和故障信息。
b)人工诊断:主要利用人力的介人对故障进行定位。常用的人工故障诊断方法包括以下几种:
1)感官诊断法:主要通过观察、听、嗅、触摸以及询问等来了解故障信息,从而对故障进行
定位。 2)互换诊断法:主要通过互换相同元器件或相容模块等来观察故障的转移情况,从而对故障
进行定位。 3)隔离诊断法(也叫拆分诊断法):主要通过拆分或隔离的方法将故障所涉及的较长链条分
段处理,从而对故障进行定位。 4)# 接口信号法:通过PLC程序等,检查机床数控系统的接口信号,并与接口手册的正确信号
相对比,以确定相应的故障点。 5)参数调整法:通过调整一个或多个参数来观察故障的状态变化,从而对故障进行定位。主
要用于使用时间较久的机床数控系统,其机械或电气性能的变化打破了最初的匹配状态和最佳的状态,调整相关的一个或多个参数方可使故障状态发生变化
6)功能程序测试法:是利用数控系统的 G、M、S、T、F 等功能程序进行测试,可对机床数控系
统功能故障进行定位。一般在机床出现随机性故障时或因闲置时间较长而出现故障时使用。
7)远程诊断法:远程诊断方利用机床数控系统的网络通信接口向机床数控系统发送诊断程
序,同时接收返回的测试数据。通过对测试数据进行分析、运算、处理,对故障进行定位。
8)测量法、敲击法、局部升温法、插拔法、分段程序检查法、原理分析法等其他诊断法。
4.3.2故障维修方法
故障维修是故障诊断的后续工作。不同类型的故障可能需要采用不同的维修方法。常用的维修方法包括以下几种:
a)直接修复法:主要针对松动、开裂、磨损、系统失调、参数丢失等类型的故障; b)器件更换法:主要针对硬件损坏的故障; c)隔离法:主要针对绝缘、干扰、病毒等类型故障; d)其他维修法
4.4故障诊断与维修记录 4.4.1故障诊断记录
故障诊断记录,其目的在于对故障诊断的过程进行记录,以便于对机床数控系统故障信息进行统计、分析和反馈,为可靠性改进提供参考和依据。
54C
机床数控系统故障诊断记录应包含但不限于以下内容:
5