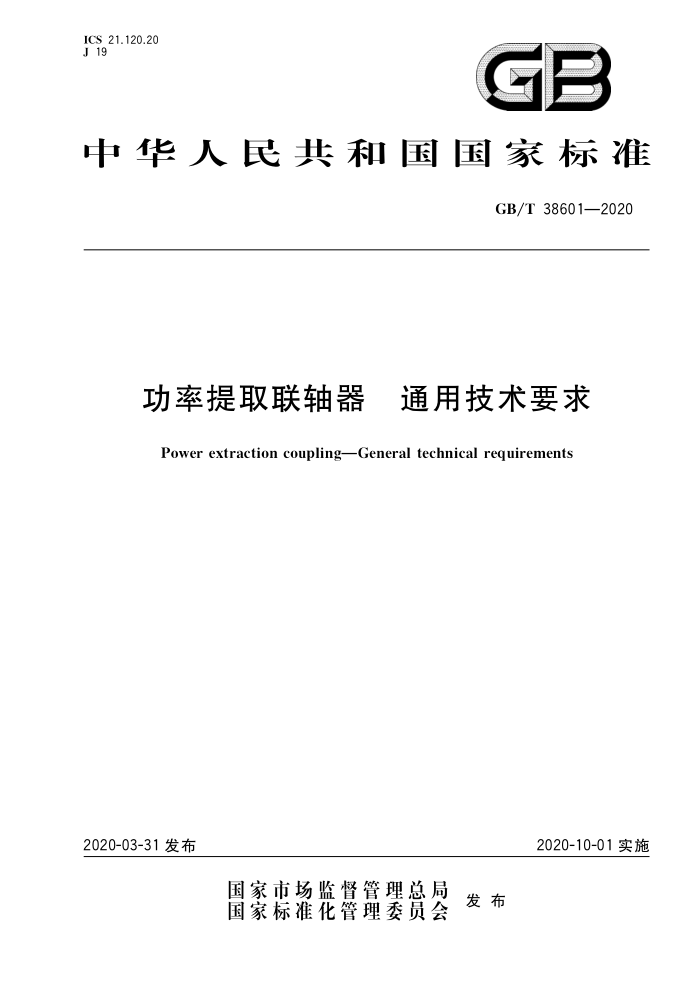
ICS 21.120.20 J 19
GB
中华人民共和国国家标准
GB/T38601—2020
功率提取联轴器 通用技术要求
Power extraction couplingGeneral technical requirements
2020-10-01实施
2020-03-31发布
国家市场监督管理总局
国家标准化管理委员会 发布
GB/T 38601—2020
前言
本标准按照GB/T1.1一2009给出的规则起草。 本标准由全国机器轴与附件标准化技术委员会(SAC/TC109)提出并归口。 本标准起草单位:太原重工股份有限公司、中机生产力促进中心、衡水刘杨联轴器厂、泰尔重工股份
有限公司、中国船舶重工集团公司第七一一研究所、山西奥盟传动科技发展有限公司、二重(德阳重型装备有限公司。
本标准主要起草人:王晓凌、明翠新、夏清华、朱悦、刘路明、邵翰民、孔曼军、杨勇波。
1
GB/T38601—2020
功率提取联轴器 通用技术要求
1范围
本标准规定了功率提取联轴器(以下简称联轴器)的术语和定义、设计、制造和检验、试验、标记、包
装和贮存等。
本标准适用于功率提取联轴器,其他联轴器也可参照执行,
规范性引用文件
2
下列文件对于本文件的应用是必不可少的。凡是注日期的引用文件,仅注日期的版本适用于本文件。凡是不注日期的引用文件,其最新版本(包括所有的修改单)适用于本文件。
GB/T1031产品几何技术规范(GPS)表面结构轮廓法表面粗糙度参数及其数值 GB/T1184形状和位置公差未注公差值 GB/T 1800.2 2产品几何技术规范(GPS) 极限与配合第2部分:标准公差等级和孔、轴极限偏
差表
GB/T 3931 联轴器术语 GB/T 9239.1 机械振动恒态(刚性)转子平衡品质要求 交第1部分:规范与平衡允许的检验 GB/T12458J 联轴器分类 JB/T 7511 机械式联轴器选用计算 JB/T 8556 选用联轴器的技术资料 JB/T 8557 挠性联轴器平衡分类 ISO 4863 弹性联轴器用户和制造者提供的数据资料(Resilientshaftcouplings一Information
to be supplied by users and manufacturers)
3 术语和定义
GB/T3931界定的以及下列术语和定义适用于本文件。
3.1
功率提取联轴器 power extraction coupling 动力系统或动力传动系统带附加传动功能时,其附加传动装置驱动机械输出轴(或回转件)与从动
机械输入轴(或回转件)之间联接的具有特定功能的联轴器
4联轴器的设计
4.1 联轴器具备的功能 4.1.1有效实现两轴线的联接,传递转矩和运动。并较精确保证相应的缓冲、减振性能,以及满足工作转速、工作环境、使用寿命要求等。 4.1.2具有相应精确的径向补偿能力。 4.1.3具有相应精确的轴向补偿能力。
1
GB/T38601—2020
4.1.4 具有相应精确的角向补偿能力。 4.1.5 具有相应精确的扭转刚度。 4.1.6 具有相应精确的相对阻尼。 4.1.7 具有相应精确的轴向、径向和角向刚度, 4.2 联轴器的技术性能与选用 4.2.1 用户与制造厂对弹性联轴器提供的数据资料项目按照ISO4863的规定。 4.2.2 联轴器的技术资料项目按照JB/T8556的规定选用。 4.2.3 联轴器的选用计算按照JB/T7511的规定进行。 4.2.4 特殊行业、特种设备用联轴器的技术性能及设计选用技术资料可根据具体情况特殊规定 4.3 联轴器的设计计算 4.3.1 联轴器设计的技术性能指标项目 4.3.1.1 联轴器设计时,根据用户要求应确定相关的载荷值和振动变化值,以及联轴器转速、刚度、补偿量和温度等指标值,主要性能指标项目见表1。特殊情况还需增加特定的指标。
表 1
序号 1 2 3 4 5 6 7 驱动机械侧的激振转矩
序号 13 联轴器的转速 14 联轴器的临界转速 15 联轴器的平衡要求 16 联轴器的扭转刚度 17 联轴器的轴向、径向刚度 18 联接器的轴向、径向和角向补偿量 19 联轴器的环境温度 20 联轴器的工作温度 21 联轴器的阻尼数据 22 联轴器的最大扭转角 23 联轴器的转动惯量 24 联轴器的弹性回差
项目名称
项目名称
驱动机械侧的公称(或额定)转矩从动机械侧的公称(或额定)转矩驱动机械侧的最大转矩从动机械侧的最大转矩驱动机械侧的冲击转矩从动机械侧的冲击转矩
从动机械侧的激振转矩驱动机械侧的转动惯量
8 9 10 从动机械侧的转动惯量 11 驱动机械的启动次数 12 转矩变化的频率
4.3.1.2 联轴器设计时,根据工作要求确定相关的无量纲系数,主要项目见表2。
表 2
序号 1 2 3 驱动机械的质量系数
序号 5 驱动机械的冲击系数
项目名称
项目名称
起动系数频率系数
从动机械的冲击系数
6 7 温度系数
放大系数
从动机械的质量系数
80
4
2
GB/T38601—2020
4.3.1.3 3联轴器设计时,根据使用设备要求和现场条件考虑安全系数和工况系数。 4.3.2联轴器的型式与尺寸 4.3.2.1联轴器应根据驱动机械和从动机械联接以及工作环境的要求等合理选择其类别、品种及其结构型式,保证各种技术性能要求。典型联轴器的型式按照GB/T12458的规定选择,有特殊要求时可特殊设计其结构型式。 4.3.2.2联轴器应根据驱动机械和从动机械联接的要求及安装空间等确定相关的尺寸及公差。可以按照选用型式的相关标准联轴器尺寸和公差,也可以按特殊设计型式确定尺寸和公差。 4.3.3联轴器的转矩和转速 4.3.3.1联轴器转矩计算的基本原则是:计算转矩T。小于或等于联轴器最薄弱环节的失效(强度、变形、打滑、磨损和温升等)条件限制而允许长期传递的转矩,即如式(1)所示:
T
..(1)
式中: T T. T. [T] T max [T max]
理论转矩,单位为牛米(N·m);计算转矩,单位为牛米(N·m);公称转矩(额定转矩),单位为牛米(N·m);许用转矩,单位为牛米(N·m);最大转矩,单位为牛米(N·m);许用最大转矩,单位为牛米(N·m)。
4.3.3.2 承受长期平稳载荷时的计算转矩T。按式(2)进行计算:
T.=K..K.K..K..TST.
(2)
式中: Kw—-动力机系数; K 一工况系数; K。起动系数; Kt - - 温度系数。 计算转矩T。的确定可以按照上述动力机功率计算,也可以根据特殊专业方法计算。
4.3.3.3 3承受冲击载荷时的最大转矩Tmax按式(3)进行计算:
Tmax=(T+Ts·Ksi·KA+Ts2·Ks·K)K,·K,<[Tmax]
..(3)
式中: Ts1 驱动机械侧的冲击转矩,单位为牛米(N·m); Ksi 驱动机械侧的冲击系数; KAl 驱动机械侧的质量系数; Ts2 从动机械侧的冲击转矩,单位为牛米(N·m); Ks2 从动机械侧的冲击系数; KLJ 从动机械侧的质量系数。
4.3.3.4 承受长期循环变化载荷时的最大转矩Tmaxc按式(4)进行计算:
Tmaxe=(Tm+T.·K·Kv)K.·K.·K≤LT)
·(4)
式中: Tm T. K,
平均转矩,单位为牛米(N·m);激振转矩最大幅值,单位为牛米(N·m);转动轴质量系数;
3
GB/T38601—2020
Kv振动系数; K:激振转矩频率变化系数;[T]—许用交变转矩,单位为牛米(N·m)。
4.3.3.5联轴器的转速应不超过材质强度极限、连接结构件变形等条件限制的最高使用转速,即如式(5)所示:
n<[n]
·(5)
式中:联轴器工作转速,单位为转每分(r/min); [n」——联轴器许用转速,单位为转每分(r/min)。
4.3.3.6联轴器由于长度、质量和速度等因素影响可能产生共振时,应校核其自身的临界转速nc。临界转速n。的计算根据专业的规定计算。
联轴器工作转速n应满足:n<0.7n。或n>1.3n。 4.3.4联轴器的动平衡 4.3.4.1联轴器高速旋转时,旋转零件由于质量偏心将承受较大的径向力和切向力,相关零件可能产生应力或变形等超限,也可能影响驱动机械和从动机械的正常运行。此时,联轴器应进行动平衡校正。 4.3.4.2联轴器动平衡等级的选择一般按照GB/T9239.1或JB/T8557的规定。 4.3.5联轴器的材质及热处理 4.3.5.1联轴器零件选用的材质(金属和非金属)一般应符合相应国家标准、行业标准及规范的规定,特殊零件可选用具有成熟工艺的特制材质。 4.3.5.2联轴器的型式与尺寸选用标准联轴器时,零件材质一般符合相应标准规定力学性能(物理性能)的材质。 4.3.5.3联轴器的型式与尺寸特殊设计时,根据承受载荷、刚度和补偿量等各项要求,零件选择合理的材质,保证联轴器充分满足正常运行的可靠性和寿命。 4.3.5.4联轴器在有高湿度、水、酸碱、盐雾、油类、腐蚀介质和高低温等工作环境工作时,除有有效的防腐措施外,应使用耐腐蚀和耐高低温的材质。 4.3.5.5联轴器主要金属零件都需要规定相应合理的热处理要求,包括:正火、调质、渗碳、氮化和淬火等,充分满足各种强度、弹性和耐磨等性能。 4.3.5.6联轴器主要非金属零件材质应规定相应的物理性能要求,充分满足强度、阻尼、磨损、耐水、耐油和耐高低温等性能。 4.3.6联轴器的精度 4.3.6.1联轴器零件应根据使用要求和配合精度规定相适应的尺寸公差、形位公差及粗糙度。其中,主要加工面:尺寸的精度不低于GB/T1800.2规定的7级;形位公差不低手GB/T1184规定的8级;配合表面粗糙度Ra值不大于GB/T1031规定的1.6,被接触的零件端面表面粗糙度Ra值不大于3.2。 4.3.6.2联轴器应根据使用要求确定其传动精度,包括同步性、滞后性和周期性。对于由角位移带来的周期性角速度可能引起的附加转矩进行评估 4.3.7联轴器设计的其他要求 4.3.7.1联轴器设计应有计算书,但不作为提交用户的资料,只用于可追溯性备查。 4.3.7.2联轴器关键金属零件应规定无损探伤要求。 4.3.7.3联轴器关键非金属零件应规定杂质、气泡、裂纹及表面质量要求。
4
GB/T38601—2020
4.3.7.4联轴器零件应规定相应有效的表面防腐措施要求 4.3.7.5联轴器中标准件型式及材质的选择应充分满足强度、弹性、耐磨和防腐等要求 4.3.7.6 联轴器关键部位使用紧固件时应有防松措施要求 4.3.7.7联轴器设计过程中应考虑零件的互换性
4.3.7.8 联轴器装配图中应规定装配过程中和装配后的相关技术要求。 4.3.7.9 联轴器润滑方式一般采用密封润滑,并规定润滑油脂的品种和牌号。 4.3.7.10联轴器设计过程中应考虑零部件制造的经济性。 4.3.7.11联轴器设计后应有说明书,通用联轴器可按通用安装使用说明书;特殊设计时,应单独编制安装使用说明书
5联轴器的制造和检验
5.1联轴器制造和检验部门应按规定程序批准的产品图样及设计文件进行制造、检验和验收,并应附有质量合格证 5.2联轴器零件材质、热处理及表面防腐处理等应严格按产品图样规定和相关标准规定执行。 5.3联轴器零部件应制定详细的制造工艺,充分保证零件成品的合格。 5.4联轴器零件加工尺寸误差、形位误差和表面粗糙度应符合产品图样规定的公差和粗糙度要求 5.5联轴器零件未注公差、未注形位公差和未注粗糙度等应按照行业、专业的相关标准及规范执行 5.6联轴器配套的标准件及其他外购件应按相应标准和规范(或样本)要求验收,并且供方应提供合格证明资料, 5.7联轴器装配应严格按装配图的要求和相关装配技术要求的规定进行,并按规定涂装防锈油和油漆。 5.8 检验部门应对所有零件和装配件进行检验验收,并保存各种检验记录。抽检验收时,应按相应标准、设计文件或与用户商定的抽检方法进行。出厂时,出具产品质量合格证。
6联轴器试验
6.1试验条件 6.1.1联轴器试件试验前应检验合格,按表3中的部分或全部试验项目执行。 6.1.2联轴器试件试验前,应保证相关试验仪器精度标定合格。 6.1.3联轴器试验按使用要求规定试验温度。 6.2试验分类 6.2.1 型式试验
6.2.1.1 联轴器有下列情况之一者,应进行型式试验:
a) 新产品在批量生产前; b)j 产品正式投人生产后,如果结构、材料、工艺有较大改动,可能影响产品性能时; c) 产品停产一年以上,并被恢复生产前; d) 国家质量监督机构或其他第三方产品论证机构提出进行型式试验的要求时; e) 用户提出要求时。
6.2.1.2 型式试验时,应抽取不少于1套产品进行试验
5
GB/T 38601—2020
6.2.2 出厂试验
6.2.2.1 联轴器产品出厂前均应进行出厂试验, 6.2.2.2 联轴器出厂试验项目应根据具体机械设备和工作要求确定。 6.3 试验类型及试验项目 6.3.1 试验类型:
a) 空转试验; b) 静态试验; c) 动态性能试验; d) 疲劳寿命试验; e) 超载试验。 试验类型的试验项目见表3。
表3 试验项目振动噪声转矩扭转刚度效率转矩温升振动噪声疲劳超载转矩
试验类型
备注可选项可选项
空转试验
静态试验
可选项
可选项可选项可选项可选项
动态性能试验
疲劳寿命试验超载试验
6.3.2 试验项目的检测方法见表4。
表4
试验类型
试验项目
检 测 方 法
1.在联轴器试验台上,通过传感器实时监控、采集信号值并转换为相应振动、声
振动、噪声 音数据;
空转试验
2.观察、记录保存相关现象或数据 1.在联轴器试验台上,通过传感器实时监控、采集信号并转换为相应转矩数据: 2.通过传感器实时监控、采集信号并转换为相应轴向位移、径向位移或角向位移数据; 3.观察、记录保存相关现象或数据
静态试验 转矩、扭转刚度
54C
6