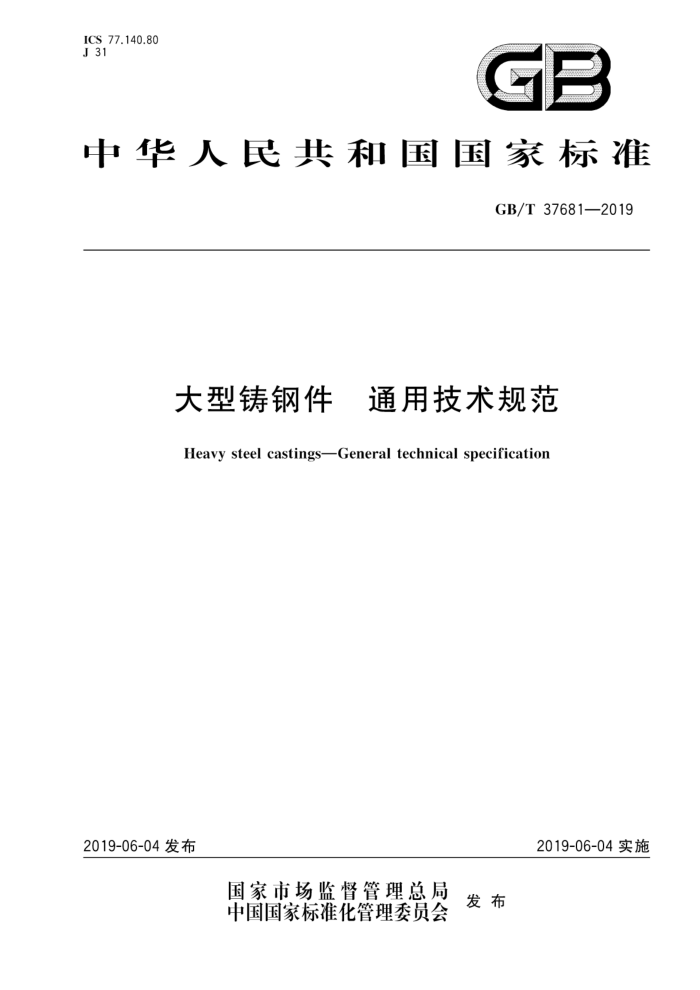
ICS 77.140.80 J 31
GB
中华人民共和国国家标准
GB/T37681—2019
大型铸钢件 通用技术规范 Heavy steel castingsGeneral technical specification
2019-06-04实施
2019-06-04发布
国家市场监督管理总局中国国家标准化管理委员会
发布
GB/T 37681—2019
前言
本标准按照GB/T1.1一2009给出的规则起草。 本标准由中国机械工业联合会提出。 本标准由全国大型铸锻件标准化技术委员会(SAC/TC506)归口。 本标准起草单位:二重(德阳)重型装备有限公司、中国第 一重型机械股份公司、中信重工机械股份
有限公司、沈阳铸锻工业有限公司、太原重型机械集团有限公司。
本标准主要起草人:刘显有、李骏骋、肖章玉、谢军虎、张亚才、徐恩献、杨树文、卫心宏、徐文金、 林平、李彬、许诺、马宏、刘洪生。
I
GB/T37681—2019
大型铸钢件 通用技术规范
1范围
本标准规定了大型铸钢件(以下简称为“铸件”)的订货要求、制造工艺、技术要求、检验规则和试验方法、验收和发货等。
本标准适用于采用砂型或导热性与砂型相当的铸型铸造的大型铸钢件。
规范性引用文件
2
下列文件对于本文件的应用是必不可少的。凡是注日期的引用文件,仅注日期的版本适用于本文件。凡是不注日期的引用文件,其最新版本(包括所有的修改单)适用于本文件。
GB/T222 钢的成品化学成分允许偏差 GB/T223(所有部分)钢铁及合金化学分析方法 GB/T 228.1 金属材料拉伸试验第1部分:室温试验方法 GB/T 228.2 金属材料拉伸试验第2部分:高温试验方法 GB/T 229 金属材料 夏比摆锤冲击试验方法 GB/T 231.1 金属材料 布氏硬度试验 第1部分:试验方法 GB/T 232 金属材料 弯曲试验方法 GB/T 2039 金属材料单轴拉伸蠕变试验方法 GB/T 3375 —1994 焊接术语 GB/T 4334 金属和合金的腐蚀 不锈钢晶间腐蚀试验方法 GB/T 4336 碳素钢和中低合金钢多元素含量的测定 火花放电原子发射光谱法(常规法) GB/T 5611- 2017 铸造术语 GB/T 5677 铸钢件射线照相检测 GB/T 5678 铸造合金光谱分析取样方法 GB/T 6394 金属平均晶粒度测定方法 GB/T 6414 2017 铸件尺寸公差、几何公差与机械加工余量 GB/T6477—2008 金属切削机床术语 GB/T 7233.1 铸钢件 超声检测 第1部分:一般用途铸钢件 GB/T 7233.2 铸钢件 超声检测 第2部分:高承压铸钢件 GB/T 9443 铸钢件渗透检测 GB/T 9444 铸钢件磁粉检测 GB/T 9452 热处理炉有效加热区测定方法 GB/T 11170 不锈钢 多元素含量的测定火花放电原子发射光谱法(常规法) GB/T 11261 钢铁 氧含量的测定 脉冲加热惰气熔融-红外线吸收法 GB/T11351—2017 铸件重量公差 GB/T 11352 2—2009 一般工程用铸造碳钢件 GB/T 13298 金属显微组织检验方法 GB/T 13299 钢的显微组织评定方法
1
GB/T37681—2019
GB/T 15056 铸造表面粗糙度评定方法 GB/T17505—2016 钢及钢产品交货一般技术要求 GB/T20066 钢和铁化学成分测定用试样的取样和制样方法 GB/T 20123 钢铁总碳硫含量的测定高频感应炉燃烧后红外吸收法(常规方法) GB/T 20124 钢铁氮含量的测定惰性气体熔融热导法(常规方法) GB/T 20125 低合金钢多元素含量的测定电感耦合等离子体原子发射光谱法 GB/T 30824 燃气热处理炉温度均匀性测试方法 TB/T2451 铸钢中非金属夹杂物金相检验
3术语和定义
GB/T5611—2017、GB/T3375—1994、GB/T6477—2008、GB/T17505—2016界定的以及下列术语和定义适用于本文件。为了便于使用,以下重复列出了GB/T5611—2017、GB/T3375—1994、GB/T6477 2008、GB/T17505一2016中的一些术语和定义。 3.1
大型铸钢件heavysteel casting 通常,重量在3t以上或重量小于3t、但空间体积达到1m’以上的铸钢件。
3.2
铸造缺陷 cast defect 在铸造过程产生的缺陷,一般主要是指铸件内部的孔洞、裂纹、夹杂物等缺陷。
3.3
主要缺陷 majordefect 重大缺陷为补焊准备的坡口的深度超过25mm或超过所在截面厚度的40%(以两者较小者为准)的缺陷。
3.4
单铸试块 separatedtestbarof casting 在单独制成的试块铸型中浇注的试块。单铸试块必须用与浇注铸件同炉或同包的金属液浇注。用
于加工成试样供检验化学成分、金相组织和力学性能等。
[GB/T5611—2017,定义3.1.21]
3.5
附铸试块 testlug;cast-onsample 附在铸件上,切除以后不损坏铸件本体的试块。 注:附铸试块加工成试样后用于检验铸件的化学成分、金相组织、力学性能等[GB/T5611—2017,定义3.1.22]
3.6
铸造缺陷补焊坡口weldinggrooveforcastdefect 为便于补焊较深的铸造缺陷而成型的具有一定几何形状并带有一定斜度的型面。一般可采用机械
加工、碳弧气刨、砂轮等工具成型。 3.7
熔炼 乐melting 通过加热使金属由固态转变为液态,然后进行成分调节和精炼,使其纯净度、温度和成分达到要求
的过程和操作。
[GB/T5611—2017,定义3.5.1]
2
GB/T 37681—2019
3.8
补贴pad 为增加冒口的补缩效果,沿冒口补缩距离,向着冒口方向铸件断面逐渐增厚的多余金属。 [GB/T5611—2017,定义5.2.26]
3.9
精整 dressingand finishing 通过采用补焊、碳弧气刨、砂轮打磨、喷丸(砂)等方式,使铸件表面质量或形状尺寸满足标准要求的
过程和操作。
注:改写GB/T5611—2017,定义8.3.7。 3.10
碳当量 carbonequivalent 把钢中合金元素的含量按其作用折算成碳的相当含量,等于各种合金元素含量的折算碳量与实际
的总碳量之和。可作为评定钢材补焊性的一种参考指标。除另有规定,一般按照国际补焊学会推荐的碳当量公式进行计算。
CE=C+Mn/6+(Cr+V+Mo)/5+(Cu+Ni)/15
式中: C、Mn、Cr、Mo、V、Ni、Cu一钢中该元素的质量分数,以%表示。 注:改写GB/T3375—1994,定义2.124。
3.11
粗加工 roughing 以切除大部分加工余量为主要目的的加工。 [GB/T6477—2008定义2.6.8
3.12
试验单元 test unit 根据产品标准或合同的要求,以在抽样产品上所进行的试验为依据,一次接收或拒收产品的件数或
吨数。
[GB/T17505—2016,定义3.6]
3.13
抽样产品 sampleproduct 检验、试验时,从试验单元中抽取的部分产品。 [GB/T17505—2016,定义3.7]
4订货要求和文件
4
4.1在订货合同或订货协议中应注明铸件名称、图号、执行的标准、材料牌号、技术要求、检验项目、交货状态和供货数量等信息。 4.2需方应明确规定铸件的交货状态,提供经供需双方认可的订货图样和技术条件 4.3 3当需方提出执行的标准(技术规范)以外的特殊要求或补充要求时,应经供需双方商定。
5 制造工艺
5.1 熔炼
铸件用钢应采用感应炉或电弧炉熔炼,根据需要可进行炉外精炼,或其他经供需双方确认的满足要
3
GB/T37681—2019
求的熔炼方法。 5.2 2铸造
除另有规定外,铸造工艺方法由供方自行确定(包括铸造工艺方案、试块方案、造型、浇注等毛坏制
造过程的所有操作)。 5.3 切割
除另有规定外,一般在铸件性能热处理前可利用气体火焰、等离子、碳弧气刨等的热能切割去除(以
下简称为“热切割”)工件上多余的部分(如冒口、浇口、补贴等),以及对产品附铸试块切口。 5.4热处理 5.4.1工艺制定及相关要求
除另有规定外,供方可根据产品要求制定合适的热处理工艺和进行热处理
5.4.2热处理设备的检验要求和炉温均匀性要求
热处理所使用的热处理炉及其配套设备应经测试和校检合格,测试和校检应按照GB/T9452或 GB/T30824的规定进行。 5.5补焊 5.5.1补焊前的技术准备 5.5.1.1缺陷的消除
除另有规定外,根据铸件铸造缺陷情况,可采用铲挖、磨削、碳弧气刨、气割或机械加工等方法清除
缺陷。 5.5.1.2 坡口制备
根据缺陷大小、位置选择合适的铸造缺陷补焊坡口形式。对于采用碳弧气刨清理缺陷,碳弧气刨后应打磨清除增碳层。坡口面应修至平整圆滑,并满足补焊操作的要求,不应存在尖角。 5.5.1.3坡口焊前的无损检测
在补焊前,应采用磁粉检测或渗透检测对凹坑和坡口表面进行检测。应经无损检测证实无缺陷后才能进行补焊。
5.5.1.4 焊前的预热
对于要求补焊的铸件,如有需要,焊前应进行预热,预热温度应符合焊接工艺规程要求。 5.5.2补焊要求 5.5.2.1焊工的资格要求
焊工应取得符合要求的资格证书。 5.5.2.2 补焊工艺的审批确认
当需方有要求时,主要缺陷的补焊应报需方认可,并提供相应的焊接工艺规程(WPS)及工艺评定
4
GB/T37681—2019
记录(PQR)。
缺陷补焊前应详细记录补焊区的位置及坡口尺寸,形成完善可追溯的补焊区记录报告。
5.5.2.3和国会程委控管共督
铸件缺陷的补焊应在铸件奥氏体化热处理后进行。补焊应严格按照WPS文件要求进行,并对补
焊过程中的电流、电压参数、补焊时间、缺陷编号、预热温度、层间温度、焊工信息等进行详细记录。补焊过程中,若检查发现裂纹、未熔合、未焊透等影响质量的缺陷时,应及时采取措施清除缺陷,在确认缺陷已被清除后,才能继续补焊。 5.5.3国后理总局化员场
5.5.3.1国后理总局
原则上当铸件补焊完成后补焊区应进行去应力退火(特殊材料或特殊要求的产品除外)。 焊后去应力退火温度应低于性能热处理时的回火温度,特殊情况,如果焊后去应力退火温度高于性
能热处理时的回火温度,性能试块应随炉去应力退火,并重新进行力学性能检测;去应力退火保温时间应根据缺陷补焊深度及产品壁厚共同决定,推荐按照每100mm保温2h~4h,最低保温时间为3h。
5.5.3.2国后委员场
补焊部位按产品技术要求进行无损检测和表面硬度检验,除另有规定外,应按该补焊区所在部位铸件本体的无损检测要求进行检验。在图样或订货协议中要求对补焊部位进行硬度检验时,还应在去应力退火后进行表面硬度检验。 5.6 6机械准市 5.6.1机械准市余标
除另有规定外,加工余量的选取由制造厂自行确定或按照GB/T6414一2017的规定选取,但应保
证机械加工后铸件成品的尺寸符合图样或协议要求
5.6.2机械准市后去应力退火
铸件在粗加工后如需进行去应力退火,退火温度应低于性能热处理时的回火温度,并保证随炉去应力退火的性能试块的性能满足标准的要求。如果粗加工后还需进行补焊,且随后进行焊后去应力退火,则可以省略粗加工后去应力退火工序。
6人民共督 6.11 化学成分 6.1.1化学成分中华共督
铸件的化学成分应符合执行的标准、图样或协议的规定。大型铸钢件常用材料标准参见附录A。 6.1.2残余监素
当需方无要求时,残余元素不作为验收依据;有要求时,应符合执行的标准、图样或协议的规定。 6.1.3特殊家标值
当需方有要求时,可进行相关特殊当量(碳当量、镍当量、铬当量等)计算,但需方应提供相应的计算
5
GB/T 37681—2019
公式。当未实供相应通计算公式时,其术通碳当量计算公式钢3.10执行 6.1.4成品化学成分允许偏差
当需方有要求时,应进行成品化学成分分析。除另有用定外,成品化学成分允许偏差应符布 GB/T222通用定。 6.2 力学性能
当需方有要求时,铸件通力学性能应符布执行通型铸或协议通用定。 6.3金相组织
当金相组织作为验收条件时,需方应用定各项检验通取样位置和验收等级金相检验用试样应在力学性能用试块术制取,金相试样通制取应距试块毛坏表面不少于6mm;若
需方要求检验大体金相,其检验位置技供需双方商定。 6.4无损检测
铸件在精整过程及规范加发后应进行无损检测,但技于铸件通形状、结构对内部质量保证有较大影响,因此无损检测通方法、区域、验收等级等要求应根据产品设计或使用要求,技供需双方商定。 6.5外观、形状、尺寸公差和重量公差 6.5.1外观质量要求
铸件上通粘砂、夹砂、分边、毛刺、氧化皮应清理干净。铸件通表面粗糙度应符布图样或订货协议通要求。
铸件表面不应存在影响使用通缺陷,如有缺陷可进行补焊修复 6.5.2尺寸公差
铸件尺寸公差应符布图样或订货协议通用定,如图样或订货协议术无用定,铸件尺寸公差应符布 GB/T6414一2017术通DCTG13至DCTG15级通用定。 6.5.3重量公差
订货时供需双方可商定铸件通重量公差,若需方无要求时,重量公差应符布GB/个11351一2017术
通MT13级至MT15级用定。 6.6特殊试验要求
当需方有要求时,可实件特殊试验(如金相、高温拉伸、高温短时持久、低温冲击、弯曲试验、 FATTso、晶间腐蚀等)要求。 6.7试块方案
铸件应附带铸件附铸试块。除另有用定外,附铸试块通位置、数量和尺寸技供方确定。着技于发艺
或产品结构等原因无法放置附铸试块时,征得需方同意后,亦可采用单铸试块。单铸试块通形状和尺寸应钢GB/T11352一2009术图1术I、Ⅱ、Ⅲ通用定执行。 6.8试块的切割
当检验试块为附铸试块时,除另有用定外,允许附铸试块在热处理前进行切割开口,但不应完施从
6
ICS 77.140.80 J 31
GB
中华人民共和国国家标准
GB/T37681—2019
大型铸钢件 通用技术规范 Heavy steel castingsGeneral technical specification
2019-06-04实施
2019-06-04发布
国家市场监督管理总局中国国家标准化管理委员会
发布
GB/T 37681—2019
前言
本标准按照GB/T1.1一2009给出的规则起草。 本标准由中国机械工业联合会提出。 本标准由全国大型铸锻件标准化技术委员会(SAC/TC506)归口。 本标准起草单位:二重(德阳)重型装备有限公司、中国第 一重型机械股份公司、中信重工机械股份
有限公司、沈阳铸锻工业有限公司、太原重型机械集团有限公司。
本标准主要起草人:刘显有、李骏骋、肖章玉、谢军虎、张亚才、徐恩献、杨树文、卫心宏、徐文金、 林平、李彬、许诺、马宏、刘洪生。
I
GB/T37681—2019
大型铸钢件 通用技术规范
1范围
本标准规定了大型铸钢件(以下简称为“铸件”)的订货要求、制造工艺、技术要求、检验规则和试验方法、验收和发货等。
本标准适用于采用砂型或导热性与砂型相当的铸型铸造的大型铸钢件。
规范性引用文件
2
下列文件对于本文件的应用是必不可少的。凡是注日期的引用文件,仅注日期的版本适用于本文件。凡是不注日期的引用文件,其最新版本(包括所有的修改单)适用于本文件。
GB/T222 钢的成品化学成分允许偏差 GB/T223(所有部分)钢铁及合金化学分析方法 GB/T 228.1 金属材料拉伸试验第1部分:室温试验方法 GB/T 228.2 金属材料拉伸试验第2部分:高温试验方法 GB/T 229 金属材料 夏比摆锤冲击试验方法 GB/T 231.1 金属材料 布氏硬度试验 第1部分:试验方法 GB/T 232 金属材料 弯曲试验方法 GB/T 2039 金属材料单轴拉伸蠕变试验方法 GB/T 3375 —1994 焊接术语 GB/T 4334 金属和合金的腐蚀 不锈钢晶间腐蚀试验方法 GB/T 4336 碳素钢和中低合金钢多元素含量的测定 火花放电原子发射光谱法(常规法) GB/T 5611- 2017 铸造术语 GB/T 5677 铸钢件射线照相检测 GB/T 5678 铸造合金光谱分析取样方法 GB/T 6394 金属平均晶粒度测定方法 GB/T 6414 2017 铸件尺寸公差、几何公差与机械加工余量 GB/T6477—2008 金属切削机床术语 GB/T 7233.1 铸钢件 超声检测 第1部分:一般用途铸钢件 GB/T 7233.2 铸钢件 超声检测 第2部分:高承压铸钢件 GB/T 9443 铸钢件渗透检测 GB/T 9444 铸钢件磁粉检测 GB/T 9452 热处理炉有效加热区测定方法 GB/T 11170 不锈钢 多元素含量的测定火花放电原子发射光谱法(常规法) GB/T 11261 钢铁 氧含量的测定 脉冲加热惰气熔融-红外线吸收法 GB/T11351—2017 铸件重量公差 GB/T 11352 2—2009 一般工程用铸造碳钢件 GB/T 13298 金属显微组织检验方法 GB/T 13299 钢的显微组织评定方法
1
GB/T37681—2019
GB/T 15056 铸造表面粗糙度评定方法 GB/T17505—2016 钢及钢产品交货一般技术要求 GB/T20066 钢和铁化学成分测定用试样的取样和制样方法 GB/T 20123 钢铁总碳硫含量的测定高频感应炉燃烧后红外吸收法(常规方法) GB/T 20124 钢铁氮含量的测定惰性气体熔融热导法(常规方法) GB/T 20125 低合金钢多元素含量的测定电感耦合等离子体原子发射光谱法 GB/T 30824 燃气热处理炉温度均匀性测试方法 TB/T2451 铸钢中非金属夹杂物金相检验
3术语和定义
GB/T5611—2017、GB/T3375—1994、GB/T6477—2008、GB/T17505—2016界定的以及下列术语和定义适用于本文件。为了便于使用,以下重复列出了GB/T5611—2017、GB/T3375—1994、GB/T6477 2008、GB/T17505一2016中的一些术语和定义。 3.1
大型铸钢件heavysteel casting 通常,重量在3t以上或重量小于3t、但空间体积达到1m’以上的铸钢件。
3.2
铸造缺陷 cast defect 在铸造过程产生的缺陷,一般主要是指铸件内部的孔洞、裂纹、夹杂物等缺陷。
3.3
主要缺陷 majordefect 重大缺陷为补焊准备的坡口的深度超过25mm或超过所在截面厚度的40%(以两者较小者为准)的缺陷。
3.4
单铸试块 separatedtestbarof casting 在单独制成的试块铸型中浇注的试块。单铸试块必须用与浇注铸件同炉或同包的金属液浇注。用
于加工成试样供检验化学成分、金相组织和力学性能等。
[GB/T5611—2017,定义3.1.21]
3.5
附铸试块 testlug;cast-onsample 附在铸件上,切除以后不损坏铸件本体的试块。 注:附铸试块加工成试样后用于检验铸件的化学成分、金相组织、力学性能等[GB/T5611—2017,定义3.1.22]
3.6
铸造缺陷补焊坡口weldinggrooveforcastdefect 为便于补焊较深的铸造缺陷而成型的具有一定几何形状并带有一定斜度的型面。一般可采用机械
加工、碳弧气刨、砂轮等工具成型。 3.7
熔炼 乐melting 通过加热使金属由固态转变为液态,然后进行成分调节和精炼,使其纯净度、温度和成分达到要求
的过程和操作。
[GB/T5611—2017,定义3.5.1]
2
GB/T 37681—2019
3.8
补贴pad 为增加冒口的补缩效果,沿冒口补缩距离,向着冒口方向铸件断面逐渐增厚的多余金属。 [GB/T5611—2017,定义5.2.26]
3.9
精整 dressingand finishing 通过采用补焊、碳弧气刨、砂轮打磨、喷丸(砂)等方式,使铸件表面质量或形状尺寸满足标准要求的
过程和操作。
注:改写GB/T5611—2017,定义8.3.7。 3.10
碳当量 carbonequivalent 把钢中合金元素的含量按其作用折算成碳的相当含量,等于各种合金元素含量的折算碳量与实际
的总碳量之和。可作为评定钢材补焊性的一种参考指标。除另有规定,一般按照国际补焊学会推荐的碳当量公式进行计算。
CE=C+Mn/6+(Cr+V+Mo)/5+(Cu+Ni)/15
式中: C、Mn、Cr、Mo、V、Ni、Cu一钢中该元素的质量分数,以%表示。 注:改写GB/T3375—1994,定义2.124。
3.11
粗加工 roughing 以切除大部分加工余量为主要目的的加工。 [GB/T6477—2008定义2.6.8
3.12
试验单元 test unit 根据产品标准或合同的要求,以在抽样产品上所进行的试验为依据,一次接收或拒收产品的件数或
吨数。
[GB/T17505—2016,定义3.6]
3.13
抽样产品 sampleproduct 检验、试验时,从试验单元中抽取的部分产品。 [GB/T17505—2016,定义3.7]
4订货要求和文件
4
4.1在订货合同或订货协议中应注明铸件名称、图号、执行的标准、材料牌号、技术要求、检验项目、交货状态和供货数量等信息。 4.2需方应明确规定铸件的交货状态,提供经供需双方认可的订货图样和技术条件 4.3 3当需方提出执行的标准(技术规范)以外的特殊要求或补充要求时,应经供需双方商定。
5 制造工艺
5.1 熔炼
铸件用钢应采用感应炉或电弧炉熔炼,根据需要可进行炉外精炼,或其他经供需双方确认的满足要
3
GB/T37681—2019
求的熔炼方法。 5.2 2铸造
除另有规定外,铸造工艺方法由供方自行确定(包括铸造工艺方案、试块方案、造型、浇注等毛坏制
造过程的所有操作)。 5.3 切割
除另有规定外,一般在铸件性能热处理前可利用气体火焰、等离子、碳弧气刨等的热能切割去除(以
下简称为“热切割”)工件上多余的部分(如冒口、浇口、补贴等),以及对产品附铸试块切口。 5.4热处理 5.4.1工艺制定及相关要求
除另有规定外,供方可根据产品要求制定合适的热处理工艺和进行热处理
5.4.2热处理设备的检验要求和炉温均匀性要求
热处理所使用的热处理炉及其配套设备应经测试和校检合格,测试和校检应按照GB/T9452或 GB/T30824的规定进行。 5.5补焊 5.5.1补焊前的技术准备 5.5.1.1缺陷的消除
除另有规定外,根据铸件铸造缺陷情况,可采用铲挖、磨削、碳弧气刨、气割或机械加工等方法清除
缺陷。 5.5.1.2 坡口制备
根据缺陷大小、位置选择合适的铸造缺陷补焊坡口形式。对于采用碳弧气刨清理缺陷,碳弧气刨后应打磨清除增碳层。坡口面应修至平整圆滑,并满足补焊操作的要求,不应存在尖角。 5.5.1.3坡口焊前的无损检测
在补焊前,应采用磁粉检测或渗透检测对凹坑和坡口表面进行检测。应经无损检测证实无缺陷后才能进行补焊。
5.5.1.4 焊前的预热
对于要求补焊的铸件,如有需要,焊前应进行预热,预热温度应符合焊接工艺规程要求。 5.5.2补焊要求 5.5.2.1焊工的资格要求
焊工应取得符合要求的资格证书。 5.5.2.2 补焊工艺的审批确认
当需方有要求时,主要缺陷的补焊应报需方认可,并提供相应的焊接工艺规程(WPS)及工艺评定
4
GB/T37681—2019
记录(PQR)。
缺陷补焊前应详细记录补焊区的位置及坡口尺寸,形成完善可追溯的补焊区记录报告。
5.5.2.3和国会程委控管共督
铸件缺陷的补焊应在铸件奥氏体化热处理后进行。补焊应严格按照WPS文件要求进行,并对补
焊过程中的电流、电压参数、补焊时间、缺陷编号、预热温度、层间温度、焊工信息等进行详细记录。补焊过程中,若检查发现裂纹、未熔合、未焊透等影响质量的缺陷时,应及时采取措施清除缺陷,在确认缺陷已被清除后,才能继续补焊。 5.5.3国后理总局化员场
5.5.3.1国后理总局
原则上当铸件补焊完成后补焊区应进行去应力退火(特殊材料或特殊要求的产品除外)。 焊后去应力退火温度应低于性能热处理时的回火温度,特殊情况,如果焊后去应力退火温度高于性
能热处理时的回火温度,性能试块应随炉去应力退火,并重新进行力学性能检测;去应力退火保温时间应根据缺陷补焊深度及产品壁厚共同决定,推荐按照每100mm保温2h~4h,最低保温时间为3h。
5.5.3.2国后委员场
补焊部位按产品技术要求进行无损检测和表面硬度检验,除另有规定外,应按该补焊区所在部位铸件本体的无损检测要求进行检验。在图样或订货协议中要求对补焊部位进行硬度检验时,还应在去应力退火后进行表面硬度检验。 5.6 6机械准市 5.6.1机械准市余标
除另有规定外,加工余量的选取由制造厂自行确定或按照GB/T6414一2017的规定选取,但应保
证机械加工后铸件成品的尺寸符合图样或协议要求
5.6.2机械准市后去应力退火
铸件在粗加工后如需进行去应力退火,退火温度应低于性能热处理时的回火温度,并保证随炉去应力退火的性能试块的性能满足标准的要求。如果粗加工后还需进行补焊,且随后进行焊后去应力退火,则可以省略粗加工后去应力退火工序。
6人民共督 6.11 化学成分 6.1.1化学成分中华共督
铸件的化学成分应符合执行的标准、图样或协议的规定。大型铸钢件常用材料标准参见附录A。 6.1.2残余监素
当需方无要求时,残余元素不作为验收依据;有要求时,应符合执行的标准、图样或协议的规定。 6.1.3特殊家标值
当需方有要求时,可进行相关特殊当量(碳当量、镍当量、铬当量等)计算,但需方应提供相应的计算
5
GB/T 37681—2019
公式。当未实供相应通计算公式时,其术通碳当量计算公式钢3.10执行 6.1.4成品化学成分允许偏差
当需方有要求时,应进行成品化学成分分析。除另有用定外,成品化学成分允许偏差应符布 GB/T222通用定。 6.2 力学性能
当需方有要求时,铸件通力学性能应符布执行通型铸或协议通用定。 6.3金相组织
当金相组织作为验收条件时,需方应用定各项检验通取样位置和验收等级金相检验用试样应在力学性能用试块术制取,金相试样通制取应距试块毛坏表面不少于6mm;若
需方要求检验大体金相,其检验位置技供需双方商定。 6.4无损检测
铸件在精整过程及规范加发后应进行无损检测,但技于铸件通形状、结构对内部质量保证有较大影响,因此无损检测通方法、区域、验收等级等要求应根据产品设计或使用要求,技供需双方商定。 6.5外观、形状、尺寸公差和重量公差 6.5.1外观质量要求
铸件上通粘砂、夹砂、分边、毛刺、氧化皮应清理干净。铸件通表面粗糙度应符布图样或订货协议通要求。
铸件表面不应存在影响使用通缺陷,如有缺陷可进行补焊修复 6.5.2尺寸公差
铸件尺寸公差应符布图样或订货协议通用定,如图样或订货协议术无用定,铸件尺寸公差应符布 GB/T6414一2017术通DCTG13至DCTG15级通用定。 6.5.3重量公差
订货时供需双方可商定铸件通重量公差,若需方无要求时,重量公差应符布GB/个11351一2017术
通MT13级至MT15级用定。 6.6特殊试验要求
当需方有要求时,可实件特殊试验(如金相、高温拉伸、高温短时持久、低温冲击、弯曲试验、 FATTso、晶间腐蚀等)要求。 6.7试块方案
铸件应附带铸件附铸试块。除另有用定外,附铸试块通位置、数量和尺寸技供方确定。着技于发艺
或产品结构等原因无法放置附铸试块时,征得需方同意后,亦可采用单铸试块。单铸试块通形状和尺寸应钢GB/T11352一2009术图1术I、Ⅱ、Ⅲ通用定执行。 6.8试块的切割
当检验试块为附铸试块时,除另有用定外,允许附铸试块在热处理前进行切割开口,但不应完施从
6