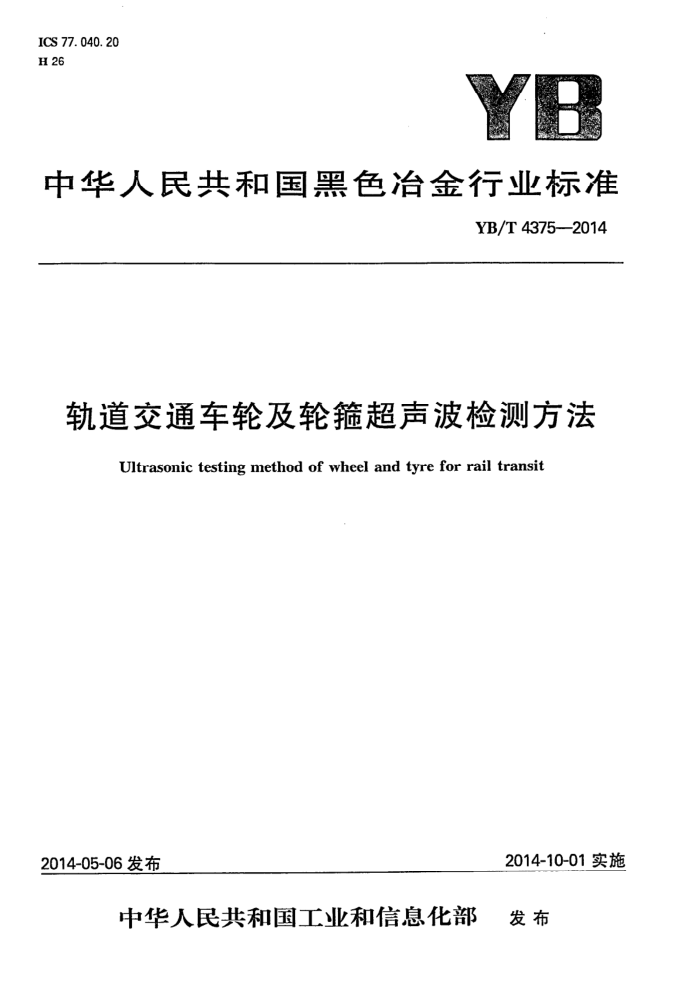
ICS 77. 040. 20 H 26
8
中华人民共和国黑色冶金行业标准
YB/T4375-2014
轨道交通车轮及轮箍超声波检测方法
Ultrasonic testing method of wheel and tyre for rail transit
2014-10-01实施
2014-05-06发布
中华人民共和国工业和信息化部 发布
YB/T 4375--2014
前 言
本标准按照GB/T1.1—2009给出的规则起草。 本标准由中国钢铁工业协会提出。 本标准由全国钢标准化技术委员会(SAC/TC183)归口。 本标准起草单位:马钢(集团)控股有限公司,冶金工业信息标准研究院。 本标准主要起草人:肖峰、李翔、张明如、方拓野、刘玉兰、陈昌华、王翔、董莉。
YB/T4375—2014
轨道交通车轮及轮箍超声波检测方法
1范围
本标准规定了轨道交通车轮及轮箍超声波检测的协议条款、人员、设备、试块、检测时机、产品表面状态、灵敏度校准、扫查、系统复核与重新校准、缺陷评定和检测报告。
本标准适用于铁路机车和车辆、城市轨道交通车辆用辗钢和铸钢整体车轮、钢轮箍的超声波检测。 2规范性引用文件
下列文件对于本文件的应用是必不可少的。凡是注日期的引用文件,仅所注日期的版本适用于本文件。凡是不注日期的引用文件,其最新版本(包括所有的修改单)适用于本文件。
GB/T9445无损检测人员资格鉴定与认证 GB/T23905无损检测超声检测用试块 JB/T9214A型脉冲反射式超声探伤系统工作性能测试方法 JB/T10061A型脉冲反射式超声探伤仪通用技术条件 JB/T10062超声探伤用探头性能测试方法
3协议条款
采用本标准作为车轮、轮箍产品内部完好性超声波检测的规范性方法时,供需双方应至少确定以下内容:
a)检测部位,以及相应部位的检测数量或比例; b)验收标准。
4人员 4.1超声波检测人员,应按GB/T9445或需方要求的程序和体系进行资格鉴定与认证,并通过雇主组织的培训和考核,掌握相应产品标准、生产工艺、检测设备的基本知识以及超声波检测规程的要求,经雇主认可和授权。 4.2超声波检测Ⅱ级及Ⅱ级以上人员,可独立从事GB/T9445中所述的无损检测工作。I级人员应在 Ⅱ级或Ⅱ级以上人员的监督、指导下从事超声波检测。 5设备 5.1扫查装置
批量检测时应采用与自动报警和自动记录关联的自动扫查装置,并能保证匀速、稳定、声耦合良好。 5.2检测仪器
手工扫查和自动扫查用超声波检测仪均应符合JB/T10061要求。每年至少对仪器性能进行一次检验。每隔3个月至少对仪器的水平线性和垂直线性进行次检验。
自动扫查用超声波检测仪还应具有以下功能: a)自检功能:开机后应能自动启动自检程序,并能显示和存贮自检结果 b)监测和报警功能:应能对仪器状态进行实时监测。工作过程中出现监测信号偏离设定值时,应
能白动显示、报警和记录;
1
YB/T4375--2014
c)内置DAC和TCG曲线功能:通过预先测试,保存DAC和TCG曲线,能够根据缺陷波的声程对波幅进行自动修正;
d)缺陷报警功能:当始波和回波低于或超过预先设定的水平高度时应能自动报警; e)记录、存贮功能:应能自动记录和存贮仪器的设置参数和检测结果; f)界面波自动跟踪功能:当采用液浸式检测方法时,超声波检测仪应能自动跟踪界面波并自动调
节扫描范围和闸门位置。 5.3探头
缺陷检测采用频率为2MHz~5MHz的纵波探头,包括直探头、双晶探头、聚焦探头和相控阵探头等。当探伤灵敏度要求达到$1mm平底孔时,探头的频率应选择4MHz或5MHz。透声检测采用频率为 2.5MHz的直探头。晶片的有效尺寸为10mm~40mm(对于相控阵探头,指虚拟探头)。
在使用接触式检测方法对车轮、轮箍的踏面或轮箍的内径面进行扫查时,为保证探头与接触面垂直以及有良好、均匀的声耦合,在需要时可安装仿形的探头靴。
新购探头使用前应进行性能测试,测试方法执行JB/T10062,并应满足以下要求: a)回波频率误差:Af/f<15% b)声轴偏向角:≤1° c)声束宽度:应能满足扫查盖的要求
5.4系统组合性能
系统组合性能应满足以下要求,更换探头时以及每隔3个月至少进行一次测试,测试方法执行JB/T 9214:
a)灵敏度余量直探头:≥46dB 双晶探头:≥40dB($2mm平底孔,埋藏深度与探头焦距对应)聚焦探头:≥30dB($2mm平底孔,埋藏深度与探头焦距对应) b)分辨力:≥26dB c)盲区
辐板探头:≤5mm 径向检测探头:≤10mm 轴向检测探头:≤20mm
5.5耦合剂
采用水(可添加防腐剂或软化剂)、机油、甘油和水质浆糊作为耦合剂。 校准和检测时应使用相同耦合剂。
6试块 6.1一般要求
用于灵敏度校准、缺陷大小评定的对比试块应采用与被检车轮、轮箍产品相同规格型号(或外形尺寸和声学性能相近)、无自然缺陷、透声能良好的车轮、轮箍,或其一部分制作,并应符合GB/T23905要求。 6.2参考反射体的形状和大小
对比试块中参考反射体的形状和大小见表1。
表1对比试块中参考反射体的形状和尺寸
部位车轮轮辋 (轮箍) 2
用途缺陷检测灵敏度校准
参考体形状平底孔
直径/mm 1或2或3
备注
依据产品标准或订货协议选择
YB/T4375—2014
表1 对比试块中参考反射体的形状和尺寸(续)
部位
用途
参考体形状
备注
直径/mm
除非产品标准或订货协议另有规定,di值需经试验确定,以使底波损失为4dB为准除非产品标准或订货协议另有规定除非产品标准或订货协议另有规定除非产品标准或订货协议另有规定,dz值需经试验确定,以使底波损失为6dB为准
车轮轮辋 轴向透声检测灵敏度校准 120°锥底孔车轮辐板 缺陷检测灵敏度校准
di
(轮箍)
平底孔平底孔
3和5 3和5
缺陷检测灵敏度校准
车轮轮毂
轴向透声检测灵敏度校准
120°锥底孔
d2
6.3参考反射体的位置、深度和分布 6.3.1 车轮轮辋轴向缺陷检测校推用对比试块见图1。 轮箍轴向缺陷检测校推用对比试块参照此图。
100
60
超声探头
超声探头
最小距离100
图1车轮轮辋轴向缺陷检测校准用对比试块
6.3.2车轮轮辋轴向透声检测校准用对比试块见图2。轮箍轴向透声检测校准用对比试块和车轮轮毂轴向透声检测校准用对比试块参照此图。
福
超声探火
钻孔角度120°
图2车轮轮辋轴向透声检测校准用对比试块
6.3.3车轮轮辋径向缺陷检测校准用对比试块见图3。轮箍径向(踏面扫查)缺陷检测校准用对比试块参照此图。
3
YB/T4375—2014
超声探头
-
1511
3
滚动圆
最小距离100
图3车轮轮辋径向缺陷检测校准用对比试块
6.3.4车轮辐板缺陷检测校准试块中平底孔在圆周方向的分布距离至少为100mm,其距离扫查面的距离为"e"的函数,“e”被定义为辐板平均厚度[e二(s1十s2)/2,“s”和“sz”分别为辐板轮辋侧和轮毂侧的厚度]。
当e<10mm时:在辐板内表面5mm下有一直径为3mm的平底孔;在辐板内表面5mm下有一直径为5mm的平底孔。
当10mm
当e>20mm时:在辐板内表面5mm、0.5emm和(e-5)mm下有三个直径为3mm的平底孔;在辐板内表面5mm,0.5emm和(e一5)mm下有三个直径为5mm的平底孔。
6.3.5车轮轮毂轴向缺陷检测校准用对比试块见图4。 6.3.6车轮轮毂轴向透声检测校准用对比试块见图5。
检测时机超声波检测应在产品热处理以后进行,并应考虑在钢温降至环境温度以后的一定时间内缺陷仍会产
7
生和发展的可能性。
某些加工(如扫查面机加工成台阶或沟槽、扫查面冷打印标识、车轮轮毂钻注油孔等)会响超声波检测的实施,检测应在热处理之后和这些加工之前进行。 8产品表面状态 8.1扫查面应无氧化皮、油漆、凹凸不平等任何造成耦合失效、阻碍探头移动和引起判断错误的物质和结构。 8.2扫查面可以是机加工状态或者非机加工状态,但其粗糙度须符合表2规定。 4
YB/T4375-2014
0
30
图4 车轮轮毂轴向缺陷检测校准用对比试块
10/
31
图5车轮轮毂轴向透声检测校准用对比试块表2扫查面粗糙度要求与探伤灵敏度的对应关系
$2mm平底孔
1mm平底孔 Ra<3.2μm
探伤灵敏度扫查面粗糙度
3mm平底孔
Ra<6.3μm
8.3透声检测的底面应无造成判断错误的物质和结构。 9灵敏度校准 9.1一般要求
检测灵敏度的校准应在与检测相同的条件下进行。当校准与检测存在表面耦合、材质衰减和声程等差异时,应进行相应增益补偿。
缺陷检测灵敏度的设置应满足在检测对象最大声程范围内能够可靠检测出产品标准或订货协议中规定的定量水平缺陷。 9.2校准方法 9.2.1对车轮轮辋、轮箍和车轮轮毂的轴向检测,可采用以图1、图4试块中平底孔为基准的DAC方法;使用单晶直探头时,也可采用底波反射法。 9.2.2对车轮轮辋、轮箍的径向检测,以及对车轮辐板的检测,采用以图2、图3试块中平底孔为基准的 DAC方法。 9.2.3对车轮轮辋、轮箍和车轮轮毂的轴向透声检测,将锥底孔处最低回波调至垂直满幅度的60%~
5
YB/T4375—2014
80%;或将透声试块无缺陷处回波调整到垂直满幅度的60%~80%,再将增益提高产品标准或订货协议规定的最大允许底波损失。 9.3替代基准或方法
允许使用替代基准或替代校准方法,但应符合9.1的要求。 当采用替代基准或校准方法时,供方应提供书面材料,说明所采用替代基准或校准方法与需方要求
达到灵敏度之间的相互关系。 10扫查 10.1检测部位、检测方向与扫查面
除非另有协议,应至少对车轮轮辋和轮箍进行轴向和径向检测。轴向检测时一般选择轮辋内侧面作为扫查面,径向检测应选择踏面作为扫查面。若产品标准或订货协议未对车轮轮辋和轮箍检测的扫查面做出明确规定,则供方可根据需要选择轮辋外侧面作为轴向检测的扫查面,以及选择轮箍内径面作为径向检测的扫查面。
当产品标准和订货协议中要求对车轮辐板和轮毂进行检测时,应分别从辐板和轮毂的两个面进行扫
查。 10.2 扫查方式
采用单探头移动或多探头排列进行100%扫查,相邻扫查的重叠区域应至少为有效声束宽度的 10%。
扫查时,应保证探头轴线与扫查面垂直,以及探头与扫查面之间的耦合层充满和稳定。 10.3扫查范围
对于所有检测部位和检测方向,应考虑车轮、轮箍的结构、形状和尺寸,做最大可能范围的扫查。应采用对比试块中的参考反射体来验证声束的最大扫查范围。 10.4扫查速度
自动检测的扫查速度应以可靠检出对比试块中各平底孔为准。 手工检测时扫查速度不应超过150mm/s。
10.5扫查灵敏度
应在探伤灵敏度基础上至少提高3dB作为扫查灵敏度。 11系统复核与重新校准 11.1复核
遇到以下情况应对检测系统的扫描比例和灵敏度进行复核: a)检测结束后; b)连续工作达8h; c)检测人员怀疑扫描比例或灵敏度有变化。 若任一点在扫描线上的偏移超过扫描线读数的10%时,则需重新校准扫描比例,并对上一次校准以
来所有检测部位进行复检。
若自动检测灵敏度下降3dB及以上,手工检测灵敏度下降2dB及以上,则需重新校准灵敏度,并对上一次校准或复核以来的所有检测部位进行复检。若自动检测灵敏度上升3dB及以上,手工检测灵敏度上升2dB及以上,则需重新校准灵敏度,并对上一次校准或复核以来的所有记录信号进行重新评定。 11.2重新校准
生产过程中,当发生下列任一情况时应重新校准检测系统: a)更换产品,检测对象的形状、尺寸和材质声学特性发生变化:
6