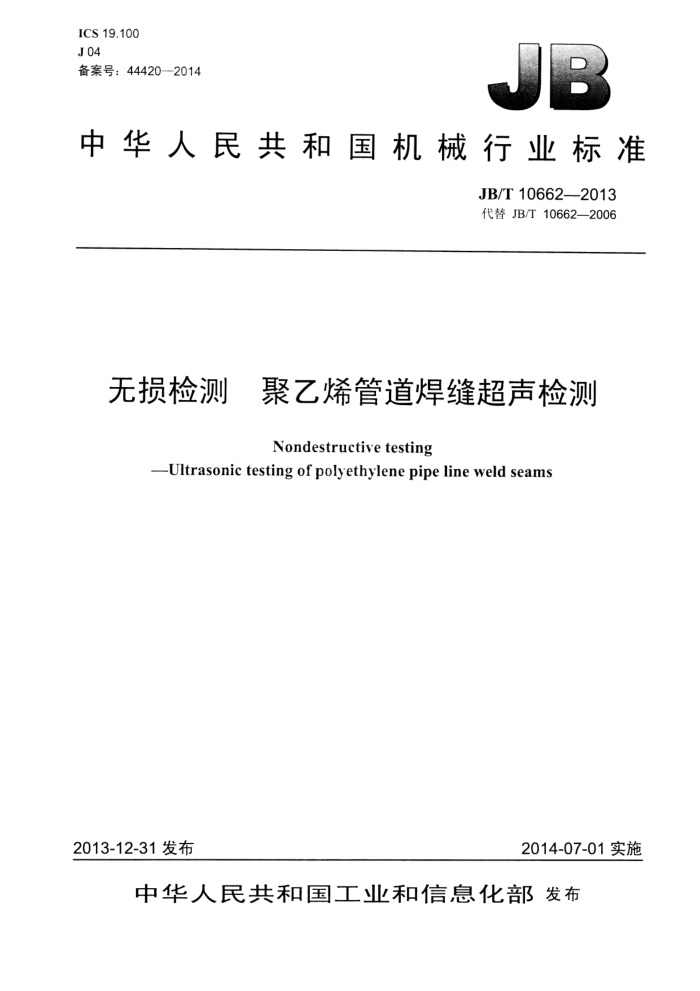
ICS 19.100 J04 备案号:44420——2014
中华人民共和国机械行业标准
JB/T10662——2013 代替JB/T10662—2006
无损检测 聚乙烯管道焊缝超声检测
Nondestructivetesting
Ultrasonic testing of polyethylene pipe line weld seams
2014-07-01实施
2013-12-31发布
中华人民共和国工业和信息化部发布
JB/T10662—2013
目 次
前言引言 1范围. 2规范性引用文件 3术语和定义 4人员要求... 5检测系统.. 5.1超声检测系统性能 5.2探头.. 5.3耦合剂 6检测准备.. 6.1表面清理 6.2表面粗糙度 7检测灵敏度.. 8检测... 8.1检测时机 8.2对接焊缝的超声检测. 8.3套接焊缝的超声检测, 9结果解释和评价, 10质量分级, 10.1 聚乙烯管道对接焊缝质量分级 10.2聚乙烯管道套接焊缝质量分级 11检测报告附录A(规范性附录)对比试块 A.1要求. A.2应用附录B(资料性附录)检测报告示例. 图1 聚乙烯管道对接焊缝(单壁)剖面示意图图2 聚乙烯管道套接焊缝剖面示意图... 图 3 从对接焊缝两侧入射检测(单壁剖面图)图4 从焊接顶部入射检测(单壁剖面图)图5 矩形槽表面的套接焊缝的检测... 图6 无矩形槽表面的套接焊缝的检测图A.1PE-2型试块表1 缺欠的分级... 表2 内层套管内壁回波幅度的分级
..II III
t
4
III .II
*
"
*
V
6
I
JB/T10662—2013
前言
本标准按照GB/T1.1一2009给出的规则起草。 本标准代替JB/T10662—2006《无损检测 聚乙烯管道焊缝超声检测》,与JB/T10662--2006相比主
要技术变化如下:
一扩大了应用范围(见第1章,2006年版的第1章);修改了探头的性能要求(见5.2,2006年版的5.2);修改了结果解释和记录(见第9章,2006年版的第9章);修改了质量分级(见第10章,2006年版的第10章);修改了对比试块(见附录A,2006年版的附录A)。
本标准由中国机械工业联合会提出。 本标准由全国无损检测标准化技术委员会(SAC/TC56)归口I。 本标准起草单位:上海泰司检测科技有限公司、无锡市苏台工业检测技术研究所、上海材料研究所。 本标准主要起草人:孙岳宗、章怡明、金宇飞。 本标准所代替标准的历次版本发布情况为:
JB/T10662—2006。
II
JB/T10662—2013
引言
聚乙烯是一种非金属材料,聚乙烯管道具有耐腐蚀、价格低的特点。目前聚乙烯管道已成为各城市用来代替钢管,进行输送燃气和自来水到各单位及居民新村的主要燃气管道和自来水管道。
聚乙烯管道的焊接方法是将两根聚乙烯管子对接,通电热熔化方法焊接起来,而形成对接焊缝,如图1所示。在两个聚乙烯管子转弯处,采用套接热熔化焊接方法:即在两根直管接头处的外圆面上套上一个事先已弯成某一角度(如90°)的聚乙烯管子,然后通电热熔化焊接起来而形成套接焊缝,如图2 所示。
图1聚乙烯管道对接焊缝(单壁)剖面示意图
图2聚乙烯管道套接焊缝剖面示意图
聚乙烯管道的焊接现场,通常是在露天工地现场的地沟里。受露天施工现场的环境影响,再加上聚乙烯管接头处焊缝热熔合的通电时间、电流大小、焊接温度等如果不能达到焊接工艺要求,就容易造成两根聚乙烯管子对接焊缝360°范围内的不同部位出现未熔合、未焊透、气孔等焊接缺欠。还有工地上的泥土、污水等杂物,往往附着在聚乙烯管子接头处的表面,如果表面末清理干净就进行焊接,也会在焊缝内造成未熔合、夹杂物(泥土)等焊接缺欠。这些缺欠,将导致聚乙烯输气管焊缝处漏气,给输送燃气带来不安全的隐患。因而在工地焊接施工过程中,同时进行超声检测,可及时检测出聚乙烯管道焊缝内的各种缺欠,消除隐患。
由于各城市居民小区内输送燃气(主要是煤气)的聚乙烯管道焊缝中缺欠处漏气而造成煤气中毒事件常有发生。为了根本上杜绝由于聚乙烯管道焊缝漏气而造成煤气中毒事件的发生,保障人民生命安全,及时检测出聚乙烯管道焊缝内的各种缺欠的工作,在聚乙烯管道工程施工过程中,同时对各个聚乙烯管道焊缝内的质量进行检测,防止漏气。只有这样才能保证人民的生命安全。
IⅡI
JB/T10662—2013
通过对多种检测技术的试验研究得出结论:用超声检测方法对聚乙烯管道焊缝中缺欠的检测是十分有效而可行的。
对聚乙烯材料声学特性的研究得知,聚乙烯材料的声速小,聚乙烯管道超声纵波声速在2000m/s~ 2200m/s范围内变化,这对超声检测用的探头材料,带来特殊性。
聚乙烯材料超声波衰减系数u值大,对聚乙烯管道材料超声测试结果表明,聚乙烯管道材料对超声波的衰减系数:μ=490dB/m~510dB/m(即0.49dB/mm0.51dB/mm)范围内变化。这一衰减系数决定对聚乙烯管道焊缝的超声检测方法有特殊的要求。
根据聚乙烯材料以上声学特性,为了实现现场对聚乙烯管道的焊缝超声检测,专门研制出用于聚乙烯管道焊缝的超声检测探头和仪器,从而解决这种特殊材料的超声检测的技术问题,同时也研究出一套检测方法,对现场各种不同型号的聚乙烯管道焊缝能够顺利进行超声检测,从而保证聚乙烯输气管道输气到用户的安全问题
由于聚乙烯管道具有以上的声学特性,它也决定了聚乙烯管道焊缝超声检测方法的特殊性。要求从事聚乙烯管道焊缝超声检测人员,通过聚乙烯管道焊缝超声检测的专业培训,再经过聚乙烯管道焊缝超声检测实践,考试合格后,具备熟练的检测操作技能,才能独立进行聚乙烯管道焊缝的超声检测,从而保证其检测结果的可靠性。
IV
JB/T10662—2013
无损检测聚乙烯管道焊缝超声检测
1范围
本标准规定了聚乙烯管道焊缝的A型脉冲反射式超声检测方法及质量分级。 本标准适用于符合GB15558.1、GB15558.2或其他类似标准的外径(50~1000)mm、壁厚(4~
60)mm的聚乙烯管道的焊缝
2规范性引用文件
2
下列文件对于本文件的应用是必不可少的。凡是注日期的引用文件,仅注日期的版本适用于本文件。 凡是不注日期的引用文件,其最新版本(包括所有的修改单)适用于本文件。
GB/T9445无损检测人员资格鉴定与认证 GB/T12604.1无损检测术语超声检测 GB15558.1燃气用埋地聚乙烯(PE)管道系统 第1部分:管材 GB15558.2 燃气用埋地聚乙烯(PE)管道系统 第2部分:管件 GB/T 20737 无损检测通用术语和定义 JB/T9214无损检测A型脉冲反射式超声检测系统工作性能测试方法
3术语和定义
GB/T12604.1和GB/T20737界定的术语和定义适用于本文件。
4人员要求
按本标准实施检测的人员,应按GB/T9445或合同各方同意的体系进行资格鉴定与认证,并由雇主或其代理对其进行职位专业培训和操作授权。
对从事聚乙烯管道焊缝超声检测的人员进行职位专业培训的内容应包括: a)了解聚乙烯管道的制造工艺和焊接工艺; b)经过聚乙烯管道焊缝超声检测的专业技术培训和实践。
5检测系统
5.1超声检测系统性能
应按JB/T9214对超声检测系统性能进行测试,并符合下列要求:
水平线性偏差不大于1%;垂直线性偏差不大于5%:一动态范围不小于30dB:一当来自于附录A所述的PE-2型试块上Φ2mm×60mm横孔的回波幅度为80%时,仪器与探头组合灵敏度余量不小于30dB。
1
JB/T10662—2013
5.2探头
宜使用双晶聚焦直探头。双晶聚焦直探头的品片尺寸为6mm×8mm~8mm×10mm,频率范围为
4MHz~8MHz,声束汇聚区宜为聚乙烯管道焊缝厚度的1/2。
应根据聚乙烯管道焊缝厚度和表面形状的不同,选用适宜的品片尺寸、频率和焦距,以及外形适合的探头。 5.3耦合剂
采用接触技术检测聚乙烯管道焊缝时,宜选用化学浆糊(羧甲基纤维素水溶液)作耦合剂。
6 检测准备
6.1表面清理
聚乙烯管道对接焊缝两侧,沿圆周360°方向,宽度80mm范围内应清理干净,套接管焊缝整个外套管的焊接区域表面360°方向全部清理干净。超声检测现场应有水源和电源装置。 6.2表面粗糙度
被检的聚乙烯管道焊缝表面应光洁,凡是由于施工过程造成的毛糙表面应打磨光洁,使表面粗糙度 Ra≤12.5 μm。
7检测灵敏度
采用附录A所述的PE-2型试块上,将Φ2mm×60mm横孔的回波幅度调至80%屏高,以此作为起始灵敏度,对聚乙烯管道焊缝进行超声检测。
8检测
8.1检测时机
聚乙烯管道对接焊缝、套接焊缝的超声检测,应在热熔合焊接工作全部完成,并经过5h后进行。 8.2对接焊缝的超声检测 8.2.1从焊缝两侧入射检测
选择对接焊缝两侧与管道面结合处的任一点为探头入射点的位置,如图3所示。 探头最初放置时,与管道面大约成50°。检测时,在不改变入射点位置的前提下,左右摆动探头
摆动幅度各不超过20°,使声束从此点位置入射和扫查焊缝。
探头分别沿对接焊缝两侧与管道面结合处作360°周向移动扫查焊缝,并在每一入射点位置按上述要求左右摆动探头。 8.2.2从焊缝顶部入射检测
选择对焊缝顶部凹槽处的任一点为探头入射点,如图4所示。 探头最初放置时,与管道横截面大约成垂直。检测时,在不改变入射点位置的前提下,左右摆动探
头,摆动幅度各不超过20°,使声束从此点位置入射和扫查焊缝。
2
JB/T10662—2013
探头分别沿对接焊缝顶部凹槽处作360°周向移动扫查焊缝,并在每一入射点位置按上述要求左右摆动探头。
70
图3从对接焊缝两侧入射检测(单壁剖面图)
图4从焊接顶部入射检测(单壁剖面图)
8.3套接焊缝的超声检测 8.3.1有矩形槽表面的套接焊缝的检测
当套接焊缝管表面有矩形槽时,探头应分别在焊缝区域内的矩形槽顶部和底部做轴向扫查,同时沿矩形槽顶部和底部做360°周向扫查(见图5,探头A和探头B分别位于矩形槽的顶部和底部)。
图5矩形槽表面的套接焊缝的检测
ICS 19.100 J04 备案号:44420——2014
中华人民共和国机械行业标准
JB/T10662——2013 代替JB/T10662—2006
无损检测 聚乙烯管道焊缝超声检测
Nondestructivetesting
Ultrasonic testing of polyethylene pipe line weld seams
2014-07-01实施
2013-12-31发布
中华人民共和国工业和信息化部发布
JB/T10662—2013
目 次
前言引言 1范围. 2规范性引用文件 3术语和定义 4人员要求... 5检测系统.. 5.1超声检测系统性能 5.2探头.. 5.3耦合剂 6检测准备.. 6.1表面清理 6.2表面粗糙度 7检测灵敏度.. 8检测... 8.1检测时机 8.2对接焊缝的超声检测. 8.3套接焊缝的超声检测, 9结果解释和评价, 10质量分级, 10.1 聚乙烯管道对接焊缝质量分级 10.2聚乙烯管道套接焊缝质量分级 11检测报告附录A(规范性附录)对比试块 A.1要求. A.2应用附录B(资料性附录)检测报告示例. 图1 聚乙烯管道对接焊缝(单壁)剖面示意图图2 聚乙烯管道套接焊缝剖面示意图... 图 3 从对接焊缝两侧入射检测(单壁剖面图)图4 从焊接顶部入射检测(单壁剖面图)图5 矩形槽表面的套接焊缝的检测... 图6 无矩形槽表面的套接焊缝的检测图A.1PE-2型试块表1 缺欠的分级... 表2 内层套管内壁回波幅度的分级
..II III
t
4
III .II
*
"
*
V
6
I
JB/T10662—2013
前言
本标准按照GB/T1.1一2009给出的规则起草。 本标准代替JB/T10662—2006《无损检测 聚乙烯管道焊缝超声检测》,与JB/T10662--2006相比主
要技术变化如下:
一扩大了应用范围(见第1章,2006年版的第1章);修改了探头的性能要求(见5.2,2006年版的5.2);修改了结果解释和记录(见第9章,2006年版的第9章);修改了质量分级(见第10章,2006年版的第10章);修改了对比试块(见附录A,2006年版的附录A)。
本标准由中国机械工业联合会提出。 本标准由全国无损检测标准化技术委员会(SAC/TC56)归口I。 本标准起草单位:上海泰司检测科技有限公司、无锡市苏台工业检测技术研究所、上海材料研究所。 本标准主要起草人:孙岳宗、章怡明、金宇飞。 本标准所代替标准的历次版本发布情况为:
JB/T10662—2006。
II
JB/T10662—2013
引言
聚乙烯是一种非金属材料,聚乙烯管道具有耐腐蚀、价格低的特点。目前聚乙烯管道已成为各城市用来代替钢管,进行输送燃气和自来水到各单位及居民新村的主要燃气管道和自来水管道。
聚乙烯管道的焊接方法是将两根聚乙烯管子对接,通电热熔化方法焊接起来,而形成对接焊缝,如图1所示。在两个聚乙烯管子转弯处,采用套接热熔化焊接方法:即在两根直管接头处的外圆面上套上一个事先已弯成某一角度(如90°)的聚乙烯管子,然后通电热熔化焊接起来而形成套接焊缝,如图2 所示。
图1聚乙烯管道对接焊缝(单壁)剖面示意图
图2聚乙烯管道套接焊缝剖面示意图
聚乙烯管道的焊接现场,通常是在露天工地现场的地沟里。受露天施工现场的环境影响,再加上聚乙烯管接头处焊缝热熔合的通电时间、电流大小、焊接温度等如果不能达到焊接工艺要求,就容易造成两根聚乙烯管子对接焊缝360°范围内的不同部位出现未熔合、未焊透、气孔等焊接缺欠。还有工地上的泥土、污水等杂物,往往附着在聚乙烯管子接头处的表面,如果表面末清理干净就进行焊接,也会在焊缝内造成未熔合、夹杂物(泥土)等焊接缺欠。这些缺欠,将导致聚乙烯输气管焊缝处漏气,给输送燃气带来不安全的隐患。因而在工地焊接施工过程中,同时进行超声检测,可及时检测出聚乙烯管道焊缝内的各种缺欠,消除隐患。
由于各城市居民小区内输送燃气(主要是煤气)的聚乙烯管道焊缝中缺欠处漏气而造成煤气中毒事件常有发生。为了根本上杜绝由于聚乙烯管道焊缝漏气而造成煤气中毒事件的发生,保障人民生命安全,及时检测出聚乙烯管道焊缝内的各种缺欠的工作,在聚乙烯管道工程施工过程中,同时对各个聚乙烯管道焊缝内的质量进行检测,防止漏气。只有这样才能保证人民的生命安全。
IⅡI
JB/T10662—2013
通过对多种检测技术的试验研究得出结论:用超声检测方法对聚乙烯管道焊缝中缺欠的检测是十分有效而可行的。
对聚乙烯材料声学特性的研究得知,聚乙烯材料的声速小,聚乙烯管道超声纵波声速在2000m/s~ 2200m/s范围内变化,这对超声检测用的探头材料,带来特殊性。
聚乙烯材料超声波衰减系数u值大,对聚乙烯管道材料超声测试结果表明,聚乙烯管道材料对超声波的衰减系数:μ=490dB/m~510dB/m(即0.49dB/mm0.51dB/mm)范围内变化。这一衰减系数决定对聚乙烯管道焊缝的超声检测方法有特殊的要求。
根据聚乙烯材料以上声学特性,为了实现现场对聚乙烯管道的焊缝超声检测,专门研制出用于聚乙烯管道焊缝的超声检测探头和仪器,从而解决这种特殊材料的超声检测的技术问题,同时也研究出一套检测方法,对现场各种不同型号的聚乙烯管道焊缝能够顺利进行超声检测,从而保证聚乙烯输气管道输气到用户的安全问题
由于聚乙烯管道具有以上的声学特性,它也决定了聚乙烯管道焊缝超声检测方法的特殊性。要求从事聚乙烯管道焊缝超声检测人员,通过聚乙烯管道焊缝超声检测的专业培训,再经过聚乙烯管道焊缝超声检测实践,考试合格后,具备熟练的检测操作技能,才能独立进行聚乙烯管道焊缝的超声检测,从而保证其检测结果的可靠性。
IV
JB/T10662—2013
无损检测聚乙烯管道焊缝超声检测
1范围
本标准规定了聚乙烯管道焊缝的A型脉冲反射式超声检测方法及质量分级。 本标准适用于符合GB15558.1、GB15558.2或其他类似标准的外径(50~1000)mm、壁厚(4~
60)mm的聚乙烯管道的焊缝
2规范性引用文件
2
下列文件对于本文件的应用是必不可少的。凡是注日期的引用文件,仅注日期的版本适用于本文件。 凡是不注日期的引用文件,其最新版本(包括所有的修改单)适用于本文件。
GB/T9445无损检测人员资格鉴定与认证 GB/T12604.1无损检测术语超声检测 GB15558.1燃气用埋地聚乙烯(PE)管道系统 第1部分:管材 GB15558.2 燃气用埋地聚乙烯(PE)管道系统 第2部分:管件 GB/T 20737 无损检测通用术语和定义 JB/T9214无损检测A型脉冲反射式超声检测系统工作性能测试方法
3术语和定义
GB/T12604.1和GB/T20737界定的术语和定义适用于本文件。
4人员要求
按本标准实施检测的人员,应按GB/T9445或合同各方同意的体系进行资格鉴定与认证,并由雇主或其代理对其进行职位专业培训和操作授权。
对从事聚乙烯管道焊缝超声检测的人员进行职位专业培训的内容应包括: a)了解聚乙烯管道的制造工艺和焊接工艺; b)经过聚乙烯管道焊缝超声检测的专业技术培训和实践。
5检测系统
5.1超声检测系统性能
应按JB/T9214对超声检测系统性能进行测试,并符合下列要求:
水平线性偏差不大于1%;垂直线性偏差不大于5%:一动态范围不小于30dB:一当来自于附录A所述的PE-2型试块上Φ2mm×60mm横孔的回波幅度为80%时,仪器与探头组合灵敏度余量不小于30dB。
1
JB/T10662—2013
5.2探头
宜使用双晶聚焦直探头。双晶聚焦直探头的品片尺寸为6mm×8mm~8mm×10mm,频率范围为
4MHz~8MHz,声束汇聚区宜为聚乙烯管道焊缝厚度的1/2。
应根据聚乙烯管道焊缝厚度和表面形状的不同,选用适宜的品片尺寸、频率和焦距,以及外形适合的探头。 5.3耦合剂
采用接触技术检测聚乙烯管道焊缝时,宜选用化学浆糊(羧甲基纤维素水溶液)作耦合剂。
6 检测准备
6.1表面清理
聚乙烯管道对接焊缝两侧,沿圆周360°方向,宽度80mm范围内应清理干净,套接管焊缝整个外套管的焊接区域表面360°方向全部清理干净。超声检测现场应有水源和电源装置。 6.2表面粗糙度
被检的聚乙烯管道焊缝表面应光洁,凡是由于施工过程造成的毛糙表面应打磨光洁,使表面粗糙度 Ra≤12.5 μm。
7检测灵敏度
采用附录A所述的PE-2型试块上,将Φ2mm×60mm横孔的回波幅度调至80%屏高,以此作为起始灵敏度,对聚乙烯管道焊缝进行超声检测。
8检测
8.1检测时机
聚乙烯管道对接焊缝、套接焊缝的超声检测,应在热熔合焊接工作全部完成,并经过5h后进行。 8.2对接焊缝的超声检测 8.2.1从焊缝两侧入射检测
选择对接焊缝两侧与管道面结合处的任一点为探头入射点的位置,如图3所示。 探头最初放置时,与管道面大约成50°。检测时,在不改变入射点位置的前提下,左右摆动探头
摆动幅度各不超过20°,使声束从此点位置入射和扫查焊缝。
探头分别沿对接焊缝两侧与管道面结合处作360°周向移动扫查焊缝,并在每一入射点位置按上述要求左右摆动探头。 8.2.2从焊缝顶部入射检测
选择对焊缝顶部凹槽处的任一点为探头入射点,如图4所示。 探头最初放置时,与管道横截面大约成垂直。检测时,在不改变入射点位置的前提下,左右摆动探
头,摆动幅度各不超过20°,使声束从此点位置入射和扫查焊缝。
2
JB/T10662—2013
探头分别沿对接焊缝顶部凹槽处作360°周向移动扫查焊缝,并在每一入射点位置按上述要求左右摆动探头。
70
图3从对接焊缝两侧入射检测(单壁剖面图)
图4从焊接顶部入射检测(单壁剖面图)
8.3套接焊缝的超声检测 8.3.1有矩形槽表面的套接焊缝的检测
当套接焊缝管表面有矩形槽时,探头应分别在焊缝区域内的矩形槽顶部和底部做轴向扫查,同时沿矩形槽顶部和底部做360°周向扫查(见图5,探头A和探头B分别位于矩形槽的顶部和底部)。
图5矩形槽表面的套接焊缝的检测