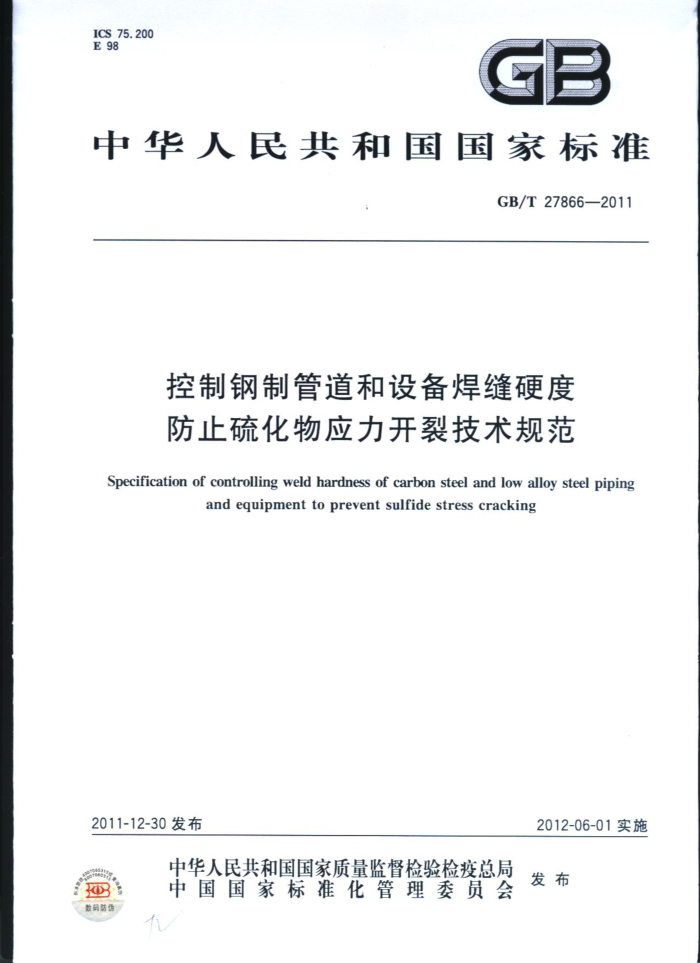
ICS 75.200 E 98
C
中华人民共和国国家标准
GB/T27866—2011
控制钢制管道和设备焊缝硬度防止硫化物应力开裂技术规范
Specification of controlling weld hardness of carbon steel and low alloy steel piping
and equipmentto prevent sulfide stress cracking
2012-06-01实施
2011-12-30发布
中华人民共和国国家质量监督检验检疫总局
中国国家标准化管理委员会 发布
303 数码防伪
GB/T27866—2011
前和言
本标准按照GB/T1.1-2009给出的规则起草。 本标准的附录A为资料性附录。 本标准由中国石油天然气集团公司提出。 本标准由全国石油天然气标准化技术委员会(SAC/TC355)归口。 本标准起草单位:中国石油集团工程设计有限责任公司西南分公司、中国石油天然气股份有限公司
西南油气田分公司。
本标准起草人:姜放、宋德琦、曹晓燕、施岱艳、汤晓勇、李、赵华莱、杜毅、陈凤、傅贺平、郭佳春、 张津、杨帆、康洪波、杨劲松、刘刚、王沁、王秦晋。
GB/T27866—2011
控制钢制管道和设备焊缝硬度防止硫化物应力开裂技术规范
范围
1
本标准规定了防止钢制管道和设备焊缝在湿含硫化氢酸性油气环境中发生硫化物应力开裂(SSC)的硬度控制要求。
本标准适用于SY/T0599规定的可用于酸性环境SSC1区、2区和3区的抗SSC低碳钢、低合金钢管道和设备的焊缝。
本标准适用的设备包括压力容器、工艺管道、热交换器、常压储罐、阀体、泵和压缩机壳体等。
2 规范性引用文件
下列文件对于本文件的应用是必不可少的。凡是注日期的引用文件,仅注日期的版本适用于本文件。凡是不注日期的引用文件,其最新版本(包括所有的修改单)适用于本文件。
GB150钢制压力容器 GB/T231.1金属布氏硬度试验第1部分:试验方法 GB/T2654 焊接接头硬度试验方法 GB/T4340.1 金属维氏硬度试验第1部分:试验方法 GB/T5117 碳钢焊条 GB/T5118 低合金钢焊条 GB/T5293 埋弧焊用碳钢焊丝和焊剂 GB/T8110 气体保护电弧焊用碳钢、低合金钢焊丝 GB/T10045 碳钢药芯焊丝 GB/T12470 埋弧焊用低合金钢焊丝和焊剂 GB/T14957 熔化焊用钢丝 GB/T17394 金属里氏硬度试验方法 GB/T17493 低合金钢药芯焊丝 SY/T0599 天然气地面设施抗硫化物应力开裂和抗应力腐蚀开裂的金属材料要求 JB/T6046 碳钢、低合金钢焊接构件焊后热处理方法
3术语和定义
下列术语和定义适用于本文件。
3.1
焊缝weld 熔敷金属、熔合线和热影响区三部分的总称。
3.2
焊接件weldment 焊缝熔敷金属、焊缝热影响区,以及与其相邻的存在焊接残余应力的母材金属区的总称。
GB/T27866—2011
3.3
产品焊缝productweld 采用评定合格了的焊接工艺,以本标准中规定的低碳钢和低合金钢为母材金属,焊接产生的管道和
设备焊缝。 3.4
酸性环境 sourservice 暴露于含有H,S并能够引起金属材料的硫化物应力开裂(SSC)机理开裂的油气环境。
3.5
硫化物应力开裂(SSC) sulfide stress cracki 在含有水和硫化氢环境的腐蚀和拉应力[残留的和(或)外加的联合作用下,产生的一种金属开裂。
3.6
应力定向氢致开裂(SOHIC)在大致垂直于主 应力(残余的或外加的)方向生成的互相交错排列的小双纹,与 已存在的HIC(往
往是细小的)相连接导致的“梯状”开裂。 3.7
软区裂纹(SZC) 属SSC类型的开裂当低屈服强度钢中 存在局部“软区” ,可能发生此类开裂。
4总则
4.1用抗硫化物应力开裂的低碳钢和低合金钢材料制成的管道和设备,均可能因其焊缝的强度过高、 局部残余应力过大以及存在局 高部过硬区等原因,造成产品焊缝硫化物应力开裂 为了控制产品焊缝硬度,特制定本标 4.2本标准是针对母材为抗SSC的低碳钢和低合金钢管道和设
止硫化物应力开双(SSC)的硬度
控制最低要求。 4.3本标准的焊缝是指新制造的焊缝及对其修复的焊缝。 4.4本标准的焊接方法包括手工电弧焊(SMAW)、熔化极气体保护电弧焊(GMAW)、药芯焊丝电弧焊(FCAW)、钨极气体保护电弧焊(GTAW)和埋弧焊(SAW) 4.5本标准对防止硫化氢引起的其他类型环境开裂没有作规定,如在低碳钢、低合金钢管道和设备的焊缝热影响区附近观察到的应力定向氢致开裂(SOHIC)和软区裂纹(SZC)。 4.6应合理选择母材、焊接材料、焊接工艺和(或)采用焊后热处理。 4.7应根据相关规范避免或限制焊接缺陷,特别是根部区的未焊透、未熔合、气孔、夹杂、裂纹和咬边等。 4.8钢制管道和设备焊缝除应符合本标准外,还应符合国家有关标准的规定
5控制原则
5.1影响低碳钢、低合金钢管道和设备焊缝在酸性环境中发生硫化物应力开裂的主要因素有:
a)环境腐蚀性的苛刻程度; b) 焊缝的显微组织和硬度; 2
GB/T27866—2011
c)母材金属和焊缝熔敷金属的化学成分; d)总拉伸应力值(作用应力和残余应力)。
5.2用于苛刻环境条件(如pH值低的酸性环境)的碳钢或低合金钢或强度较高的材料,即使硬度符合要求,还宜采用焊后热处理。 5.3焊缝熔敷金属的硬度控制 5.3.1应合理选择焊接材料和焊接工艺,以控制焊缝熔敷金属的化学成分和硬度。 5.3.2在焊接本标准规定的金属材料时,选用的焊接材料应符合下列要求:
a)焊条应符合GB/T5117和GB/T5118的规定; b) 焊剂应符合GB/T5293和GB/T12470的规定; e
焊丝应符合GB/T5293、GB/T8110、GB/T10045、GB/T12470、GB/T14957和GB/T17493 的规定;
d)焊接材料的匹配性应遵循焊缝与母材金属等强度、其他的力学性能基本相同的原则。 5.3.3如果在制造过程中变更了焊接材料的牌号、型号,包括牌号、型号相同,但制造厂不同的焊接材料,则应重新进行焊接工艺评定,包括硬度和化学成分的检验。 5.3.4焊接材料采用含锰焊丝的SAW不宜采用活性焊剂。 5.3.5焊丝、焊条等焊接材料的含镍量应不高于1%。 5.3.6必要时可按5.5规定进行焊后热处理。 5.3.7焊缝熔敷金属硬度检测和允许的硬度值:
a)宜用便携式布氏硬度计,按GB/T231.1规定测定产品焊缝熔敷金属的硬度,并符合6.1和
6.2的规定; b) 应采用维氏硬度检测在管道和设备施焊前的焊接工艺评定中的焊缝熔敷金属硬度,硬度试样
的制取和试验应符合GB/T2654和GB/T4340.1的规定以及6.3.2和6.3.3的规定。
5.4焊缝热影响区的硬度控制 5.4.1可综合采用下列方法获得可接受的热影响区硬度,特别是双面焊和封焊的焊缝最后焊道热影响区的硬度。
a)控制管道和设备母材金属的化学成分。一般做法是控制碳当量(CEV)、残余元素总含量和添
加的微量合金元素。 CEV通常按下式确定:
CEV=w(C) + Iw(Mn) + [w(Cr) +w(Mo) + w(V)J+[w(Cu) + w(Ni)] 式中: w(C)
6
C的质量分数;
w(Mn) Mn的质量分数; w(Cr) Cr的质量分数; w(Mo) Mo的质量分数;
V的质量分数;
w(V) w(Cu) Cu的质量分数; w(Ni) -Ni的质量分数。
b)应采用预热、控制焊接线能量,降低焊缝的冷却速度等方式,防止热影响区高硬度显微组织的
形成,避免大部件上的小焊道焊缝热影响区的高硬度。 e) 应采用GB/T4340.1维氏硬度试验方法进行管道和设备施焊前的焊接工艺评定中的硬度检
测,以控制焊缝热影响区的显微组织硬度。
3
GB/T27866—2011
d)为软化热影响区显微组织,应在足够的高温下进行焊后热处理。 5.4.2应采用5.4.1b)的做法避免大部件上的小焊道焊缝热影响区的高硬度。 5.4.3应采用5.4.1b)的做法或其他技术,降低难以采用焊后热处理减小焊缝热影响区硬度的某些阀门、泵、压缩机壳体的焊缝热影响区硬度。 5.4.4可通过有意添加微量合金元素和附加预热及更高温度的焊后热处理,来获得可接受的低碳钢热影响区硬度。 5.4.5焊缝热影响区硬度检测和允许的硬度值应符合下列要求:
a)应用便携式布氏硬度计,按GB/T231.1规定检测产品焊缝热影响区的硬度,并符合6.1和
6.2的规定;
b)应采用维氏(HV)硬度检测方法检测在管道和设备施焊前的焊接工艺评定中的热影响区硬
度,硬度试样的制取和试验应符合GB/T2654和GB/T4340.1以及6.3.2和6.3.3的规定。
5.5焊后热处理的规定 5.5.1低碳钢和低合金钢消除焊接残余应力热处理的温度,应大于或等于620℃。但降低焊缝硬度的焊后热处理温度通常比消除残余应力热处理的温度高。工件的热处理保温时间至少!h。 5.5.2应按JB/T6046 6制定 焊后理工:包百格型 艺类型、热电偶数量和位置、详细的支撑方式、加热和冷却速度最大允许温差、保温时间和焊后热处理温度范围。 5.5.3焊后热处理后,应避免 免再进行产生高残余应力的加工,如矫直,否则应再次热处理 5.5.4对5. 4.4条中所述的有意添加微量合金 元素的低碳钢,当其Nb和V 的质量 分数超过0.03% 和残余元素总量大于0.5%(质量分数)时,应考虑降低热影响区硬度的焊后热处理对其韧性产生的影响。
6管道和设备焊缝硬度检测及验收
6.1产品焊缝硬度宜采用6.2的规定进行检验验品焊缝如角焊缝,或不能准确测定其硬度时,在有经验并严格按焊接工艺进行焊接条件下,才允许按6.3 的规定,用管道和设备施焊前的焊接工艺评定中的硬度检测结果作为验收该产品焊缝硬度的依据。 6.2用宏观硬度检测验收产品焊缝硬度 6.2.1.产品焊缝硬度宜使用便携式布氏硬度计,按GB/T231.1的规定进行检验。也可按照 GB/T17394规定采用里氏硬度计进行检验,并按照GB/T17394将测得的硬度值转换为HBW值。 6.2.2产品焊缝硬度最低测定次数应满足下列要求
用便携式布氏硬度计检测硬度的产
a)容器或储罐的纵向焊缝,每3m测定一次,每节筒体上的每条纵向焊缝至少测定一次; b) 容器或储罐的环向焊缝,每3m测定一次,每条环向焊缝至少测定一次; c) 开口接管上的焊缝,每条测定一次; d)除本条已要求测定硬度的焊缝外,其余的属GB150规定的A类和B类焊缝,每条至少测定
一次; e)无法用仪器测定硬度的开口接管的角焊缝,应采取必要的工艺措施或采用5.4.3和6.3的做
法,避免硬度超过极限值;管道和配管对接焊缝,应每条对接焊缝至少测定一次; g)硬度检测一次指对焊缝熔敷金属和热影响区至少各检测一处。
6.2.3产品焊缝硬度测定的位置应符合如下要求:
4.
GB/T27866—2011
硬度测定的部位应包括焊缝熔敷金属区和热影响区,每区测定一处,每处硬度值为三个压痕平
a)
均值;
b)只有在因条件限制无法测定与酸性环境相接触侧的焊缝硬度时,才允许采用另一侧的焊缝检
测硬度代替。
6.2.4焊缝熔敷金属和热影响区的硬度值应不大于200HBW,对有高硬度现场使用经验的管道和设备,允许的硬度最大值可为225HBW。 6.2.5任一焊缝硬度超过规定的极限时,必须在此焊缝超限的部位附近增测三处硬度。如果这三处硬度测定值的平均值超过规定值5个HBW或任一处硬度测定值超过规定值10个HBW时,则此焊缝应判为不合格。 6.2.6硬度不合格焊缝的修复方
:
a)铲除清理后,按规定重新焊接, b)在不低于620C温度下进行回火处理,使其焊缝硬度下降至能满足规定值要求。但应注意焊
缝熔敷金属和母材金属力学性能的变化,保持其性能符合有关规定。
6.2.7修复后的焊缝应按本标准6.1、6.2的规定重新检测焊缝的硬度。 6.3用焊接 艺评定中的硬度检测验收 6.3.1为确保在焊接工艺评定中硬度检测结果能代表随后施焊的管道和设备焊缝硬度,要求施焊管道和设备的焊接工艺规程应按焊接工艺评定合格(包括硬度检测)的整套焊接技术规定来编制,并应满足下列要求,
a) 应由参加焊接培训考核合格人员采用符合要求的 设备进行焊接 b) 管道和设备所用母材金属的标准、钢级、生产方法和炉批号应与焊接工艺评定所用母材金属
相同; c) 管道和设备所用母材金属的最大碳当量(CEV)不应超过焊接工艺评定所用母材金属的相应
值。化学成分应采用炉前分析结果 d) 对管道和设备所用母材金
V、Ti和B等)的最大量应不超
过焊接工艺评定所用母材金属的相应值。化学成分应采用炉前分析结果管道和设备焊接需要预热的规格、预热的方法和温度都应与焊接工艺评定相同;
e)
f)管道和设备所用焊接材料的标准、类型、牌号、炉批号、规格尺寸都应与焊接工艺评定所用的
相同;管道和设备焊接的接头形式、坡口形式、焊接层数、道数和焊接顺序以及焊缝余高和焊缝宽度均应与焊接工艺评定的相同;管道和设备焊接采用的焊接方法、层间温度、焊后热处理以及焊接工艺参数,包括不同焊道所
g)
h)
用的焊材规格、电流范围、电压范围、焊接速度等均应与焊接工艺评定相同。
6.3.2对接焊缝和角焊缝、补焊和部分熔透焊缝应按图1~图5分别给出的有代表性的部位进行硬度测定。每个部位在三个非常靠近的压痕上读取的硬度值的平均值作为其硬度,只要它们的平均值不超过本标准的允许值,那么其中一个硬度读取值高于允许值10HV以内,则该硬度读取值是可接受的。
允许的热影响区最大硬度值为248HV,熔敷金属最大硬度值应为248HV,熔敷金属平均硬度值不应超过210HV。
GB/T27866—2011
一焊缝热影响区(浸蚀后可见);一虚线为测量线。
4
R
图1典型双面焊对接焊缝硬度检测位置
A
一焊缝热影响区(浸蚀后可见); B一虚线为测量线。 注1:236,7,1011141517和19硬度压痕应完全在热影
基近熔散金属与热影响区之间的熔
合线。
注2:上部的测量线应位于适当位置使得2和6
与最后焊道的熔合线的变化轮廊
一致。
图2典型单面焊对接焊缝硬度检测位置