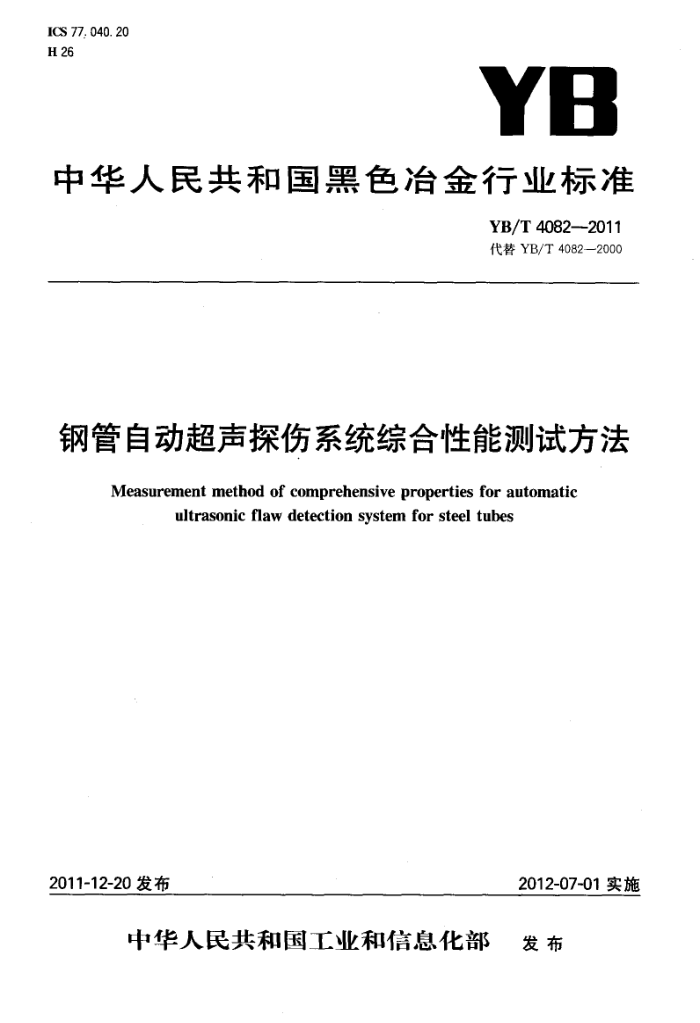
ICS 77, 040. 20 H 26
YB
中华人民共和国黑色冶金行业标准
YB/T 4082--2011 代替YB/T4082—2000
钢管自动超声探伤系统综合性能测试方法
Measurement method of comprehensive properties for automatic
ultrasonic flaw detection system for steel tubes
2012-07-01实施
2011-12-20 发布
中华人民共和国工业和信息化部 发布
YB/T 4082~-2011
目 次
前言 1 范围· 规范性引用文件 3术语和定义 4 测试条件·. 5对比试样.
2
测试项目及方法
6
2
测试报告· 附录A(资料性附录)超声检测技术特点及相关新技术
2
YB/T 4082-2011
前 言
本标准按照GB/T1.1一2009给出的规则起草。 本标准代替YB/T4082—2000,与YB/T4082—2000相比,主要技术变化如下:
增加仪器性能应满足JB/T10061的要求(见4.1);将超声探伤仪必须经有关部门检定合格修改为应经校准(见4.1);修改了槽伤有效长度的要求(见5.4,2000版的4.4);增加了测试报告规定(见7);增加了“超声检测技术特点及相关新技术”(见附录A)。
本标准由中国钢铁工业协会提出。 本标准由全国钢标准化技术委员会(SAC/TC183)归口。 本标准起草单位:钢铁研究总院、爱德森(厦门)电子有限公司、冶金工业信息标准研究院。 本标准主要起草人:范弘、张建卫、林俊明、张克、沈海红、贾慧明、马国华、董莉。 本标准所代替的历次版本发布情况为: YB/T4082—1992YB/T4082-—2000。
YB/T40822011
钢管自动超声探伤系统综合性能测试方法
1范围
本标准规定了钢管自动超声探伤系统(一般包括超声波探伤仪、超声探头和传动装置)综合性能的测试条件、对比试样、测试项目、测试方法、应达到的最低性能指标及测试报告内容。
本标准适用于钢管自动超声探伤系统综合性能的测试,对于手动超声探伤、电磁超声自动探伤、相控阵超声自动探伤及钢棒超声自动探伤系统的综合性能测试可参照使用。
2规范性引用文件
下列文件对于本文件的应用是必不可少的。凡是注日期的引用文件,仅所注日期的版本适用于本文件。凡是不注日期的引用文件,其最新版本(包括所有的修改单)适用于本文件。
GB/T5777无缝钢管超声波探伤检验方法 GB/T12604.1无损检测术语超声检测 JB/T10061A型脉冲反射式超声波探伤仪通用技术条件 YB/T144超声探伤信号幅度误差测量方法 YB/T145钢管探伤对比试样人工缺陷尺寸测量方法
3术语和定义
GB/T12604.1界定的术语和定义适用于本文件。 4测试条件 4.1探伤仪应为脉冲反射式多通道或单通道超声波探伤仪,性能应符合JB/T10061的规定,其衰减器(增益)精度、垂直线性和动态范围等应经校准。 4.2超声探伤信号幅度误差应符合YB/T144的规定。 4.3测试时系统的检测速度应为正常使用的最高探伤速度。多通道探伤设备在每个通道单独测试时,周向扫查线速度不变,检测速度应不小于正常探伤速度与设备通道数之比。测试时应如实记录探伤频率、重复频率、抑制、探伤速度、探头规格等参数。
5对比试样
5.1测试用对比试样应根据产品种类及规格制作,其长度应满足探伤方法和探伤设备的要求,试样的弯曲度不大于1.5mm/m,人工缺陷形状通常为人工刻制的纵向槽,需要时可补充人工刻制的横向槽或斜向槽。 5.2测试所用对比试样应按系统所能检测钢管外径尺寸的上限与下限规格分别制作。 5.3槽口应在试样的中部外表面和试样两端的内、外表面各加工一个,如图1所示。当试样内径小于 25mm时可不加工内壁纵向槽;对于航空和其他重要用途的不锈钢管,当内径小于12mm时可不加工内壁纵向槽。 5.4对比试样槽口的形状、宽度、深度和长度尺寸及允许偏差应符合GB/T5777的规定。 5.5对比试样制作完毕,经计量合格后方能使用。对比试样的计量报告应记载试样的编号、钢种、规格表面状况、所有人工缺陷的具体尺寸以及试样两端槽口距钢管端部的尺寸(该尺寸为槽口在管端方向的
1
YB/T4082—2011
ZZZZZZ
Z
22777722777777227277777777777777
图1综合性能测试用对比试样示意图
端点距管端的尺寸,也是该系统管端不可探区的长度表征),人工缺陷的深度可用光学方法、机械或YB T145规定的复型等方法进行测量。必要时,在测试完成后应对内壁人工缺陷进行解剖计量。 6测试项目及方法 6.1测试应按探伤系统所能检测钢管外径的上限和下限规格进行动态测试,周向灵敏度差(周向灵敏度波动)、内外壁灵敏度差、信噪比和稳定性应逐个通道进行测试,每个通道的测试结果如不相同,取最劣值。 6.2周向灵敏度差(周向灵敏度波动)测试 6.2.1对于探头旋转、钢管直线前进的探伤系统,用图1所示的对比试样使中部的外壁人工缺陷重复通过探伤系统,先将试样任意设定0°位置,调节仪器各通道灵敏度,记下人工缺陷刚刚报警时增益或衰减器的dB值,旋转试样以同样方法测试并记录120°、240°位置人工缺陷刚刚报警时的dB值。其中两个差别最大的dB值相减,即为周向灵敏度差,此差值的绝对值不大于4dB。每个通道测试3次,3次结果如不相同,取最劣值。 6.2.2对于探头固定、钢管螺旋前进的探伤系统,以及探头沿钢管轴向前进、钢管原地旋转的探伤系统,测试周向灵敏度波动。用图1所示的对比试样使中部的外壁人工缺陷重复通过探伤系统,每通道记录3 次人工缺陷刚刚报警时的dB值,3次读数的最大差值即为周向灵敏度波动。此差值的绝对值不大于4dB。 6.3内外壁灵敏度差的测试
用图1所示的对比试样使两端的内、外壁人工缺陷重复通过探伤系统,调节仪器各通道的增益或衰减器,分别记下试样内、外壁缺陷刚刚报警时的dB值,两值之差即为内、外壁缺陷探伤灵敏度差(允许采用补偿技术),此差的绝对值不大于4dB,每个通道测试3次,3次结果如不相同,取最劣值。对于内、外壁缺陷采用同一报警闸门的系统,该项必须测试;对于内、外壁缺陷采用不同报警闸门的系统,仅作测试记录,不作最后判定依据。 6.4信噪比的测试
用图1所示的对比试样重复通过探伤系统,对于内、外壁缺陷采用不同报警闸门的系统,应将两个闸门连起来,调节仪器各通道的灵敏度,分别记下各通道对比试样上所有人工缺陷刚刚报警时的dB值,该值即为探伤规定灵敏度;分别提高各通道的灵敏度,记下各通道中噪声信号刚刚报警时的dB值,此值与探伤规定灵敏度之差即为该通道的信噪比,每个通道测试3次,3次结果如不相同,取最劣值,此值应不小于8dB。 6.5漏、误报率测试
在对比试样上所有人工缺陷刚刚报警的基础上,可再提高2dB的增益,以正常使用的最高探伤速度连续测试对比试样25次,分别记下人工缺陷的漏、误报次数。对于多通道探伤系统,各通道在人工缺陷处均不报警,称为漏报,每漏报1个人工缺陷记1次;任一通道在无人工缺陷处报警称为误报,每次测试中,出现1次或1次以上的误报均记为1次。若在此之内出现的漏、误报次数较大,可将测试次数增加到 50次。系统的漏报率应不大于1.5%,误报率不大于3%。漏、误报率分别以公式(1)和公式(2)计算: 2
YB/T4082—2011
漏报人工缺陷个数
漏报率二
对比试样人工缺陷不数文测试次数×100% 误报次数×100%
(1)
误报率:
(2)
测试次数
6.6'管端不可探区的测试
在6.5的基础上测试管端不可探区。如果在连续3次测试中,对比试样两端的槽口均可靠报警,则两槽口距钢管端部的尺寸即记为管端不可探区。管端不可探区应不大于200mm。对于管端不可探区大于200mm的特殊情况应在测试报告中加以说明。 6.7稳定性测试 6.7.1整套系统连续工作2h后,按照6.2重新测试周向灵敏度差(周向灵敏度波动),所测得指标与2h 前相比波动不得大于2dB,且仍能满足6.2的要求。 6.7.2整套系统连续工作2h后,按照6.4重新测试探伤的规定灵敏度和信噪比,同一通道所测得的探伤规定灵敏度与2h前相比波动不得大于2dB,且信噪比仍能满足6.4的要求。 6.7.3稳定性测试只测试上限规格。 7测试报告
测试报告至少应包括以下内容: a)周向灵敏度差(周向灵敏度波动)、内外壁灵敏度差、探伤规定灵敏度、信噪比、漏报率、误报率、
管端不可探区、稳定性;
b)探伤设备及仪器的制造厂名、型号、编号: c)对比试样的材质、规格、状态、编号及人工缺陷尺寸; d) 测试时的探伤频率、重复频率、抑制、探伤速度、探头规格等参数; e) 测试者姓名、测试日期; f) 测试地点、环境条件等; g) 特殊情况说明。
YB/T4082—2011
附录A (资料性附录)
超声检测技术特点及相关新技术
相对于其他无损检测方法,超声无损检测技术在管线材的质量检测中有着明显的特点和优势,是当前对于钢管进行宏观缺陷检测的一种普遍应用的有效方法之一。近年来,为克服现行常规超声无损检测技术的局限,且同时也可能在一定程度上弥补其他钢管无损检测技术的某些不足,随着检测和计算机技术的进步,电磁超声、相控阵超声和无损检测集成(如超声涡流一体化检测、超声漏磁体化检测)等新技术和装备得到了很大发展,并开始逐步应用于实际工业检测。这对于管线材使用条件日益苛刻、质量可靠性要求不断提高的今天,无疑是一些有益的技术进步。
中华人民共和国黑色冶金
行业标准
钢管自动超声探伤系统综合性能测试方法
YB/T4082—2011
*
冶金工业出版社出版发行北京北河沿大街嵩祝院北巷39号
邮政编码:100009
三河市双峰印刷装订有限公司印刷
各地新华书店经销
*
开本880×1230 1/16印张0.75字数16千字 2012年3月第一版 2012年3月第一次印刷
*
统一书号:155024·368 定价:25.00元