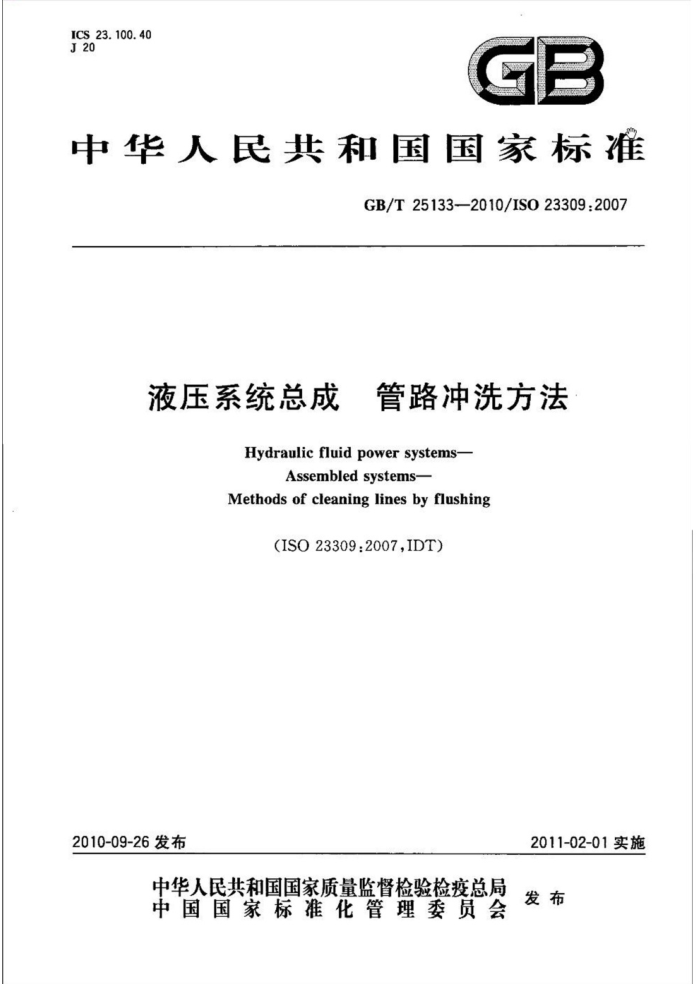
ICS_23. 100. 40 J20
GP
中华人民共和国国家标准
GB/T25133-—2010/ISO23309:2007
液压系统总成 管路冲洗方法
Hydraulicfluid power systems-
Assembledsystems-
Methods of cleaning lines by flushing
(ISO23309:2007,IDT)
2011-02-01实施
2010-09-26发布
中华人民共和国国家质量监督检验检疫总局中国国家标准化管理委员会
发布
GB/T25133—2010/IS023309:2007
前言
本标准等同采用IS023309:2007《液压传动系统 系统总成 管路冲洗方法》(英文版)。 本标准等同翻译ISO23309:2007。 为便于使用,本标准做了以下编辑性修改:
将“本国际标准”改为“本标准”;一用小数点符号“”代替作为小数点的退号“,”;一删除国际标准前言;以国家标准代替对应的国际标准。 本标准的附录A为资料性附录。 本标准由中国机械工业联合会提出。 本标准由全国液压气动标准化技术委员会(SAC/TC3)归口。 本标准起草单位:黎明液压有限公司、北京化工大学、中国船舶重工集团公司第七〇七研究所
(九江)、航空工业总公司过滤与分离机械产品质量监督检测中心。
本标准主要起草人:叶萍、李方俊、郑远、高院安、黄惠文、吕宏楠。
I
GB/T25133—2010/ISO23309:2007
引言
在液压传动系统中,功率是借助于封闭回路中的受压液体来传递和控制的。 液压系统的初始清洁度等级将影响系统的性能和使用寿命。如果不清除系统在制造和装配过程中
产生的颗粒污染物,颗粒污染物会在系统中循环并破坏系统元件。为了减小这种破坏的概率,液体和液压系统的内表面需要进行过滤和冲洗,达到指定的清洁度等级。
冲洗液压系统的管路是清除系统内部颗粒污染物的一种方法,但不是唯一的方法。
I
GB/T25133—2010/IS023309:2007
液压系统总成 管路冲洗方法
1范围
本标准规定了冲洗液压系统管路中固体颗粒污染物的方法。这些污染物可能是在新液压系统的制造过程中或是在对现有系统的维修与改造的过程中被带入。
本标准补充但不代替系统供应商和用户的要求,尤其当其要求比本标准的规定更为严格时。 本标准不适用于以下情形: a)液压管件的化学清洗和酸洗。 b)系统主要元件的清洗(见GB/Z19848一2005)。 系统总成的清洁度等级检验按照GB/Z20423进行。
2规范性引用文件
下列文件中的条款通过本标准的引用而成为本标准的条款。凡是注日期的引用文件,其随后所有的修改单(不包括勘误的内容)或修订版均不适用于本标准,然而,鼓励根据本标准达成协议的各方研究是否可使用这些文件的最新版本。凡是不注日期的引用文件,其最新版本适用于本标准。
GB/T17446流体传动系统及元件术语(GB/T17446一1998,idtISO5598:1985) GB/T17489 液压颗粒污染分析从工作系统管路中提取液样(GB/T17489一1998,idtISO4021:
1992)
GB/Z19848-2005 液压元件从制造到安装达到和控制清洁度的指南(ISO/TR10949:2002, IDT)
GB/Z20423液压系统总成清洁度检验(GB/Z20423—2006,ISO/TS16431:2002,IDT) 3术语和定义
GB/T17446确立的以及下列的术语和定义适用于本标准。
3. 1
冲洗flushing 清洗液压管道系统的过程,包括冲洗介质在液压系统管道中循环,以移出、传输并过滤在加工、装配
和维修过程中进入系统的颗粒污染物。 3.2
外冲洗outflushing 从管道盲端向开放的容器或桶中自由排放足够体积的冲洗介质,以去除其中的污染物的过程。
3. 3
目测清洁度visiblecleanliness 无需放大就能直接目测识别的表面清洁度。
3. 4
清洁工作区cleanworkarea 工作时不产生碎屑或颗粒的工作区域。 注:焊接、琴铲、切削、磨削或燃烧等活动会产生碎屑或颗粒,因此不允许在清洁工作区进行。
1
GB/T25133—2010/IS023309:2007
4清洁度等级
冲洗的主要目的是为达到用户或供应商要求的系统或元件清洁度等级。对于未规定清洁度等级的情况,可参见附录A的选择指南。 5液压系统中管路的冲洗 5.1影响因素
为使液压系统管路达到满意的清洁度等级,需要考虑以下影响因素: a) 选择按GB/Z19848—2005清洗过的元件; b) 配接管路的初始清洁度; c) 采用合适的冲洗程序; d) 选择过滤比合适的过滤器,保证能在允许的时间周期内达到需要的清洁度等级; e) 建立紊流状态,以移出并传输颗粒到过滤器。
5.2系统设计 5.2.1液压系统的设计人员在设计阶段就应考虑系统的冲洗问题。应避免设计不能冲洗的言端。如果颗粒污染物有从盲端移动到系统其他部分的风险,则此盲端应能够进行外冲洗。 5.2.2因冲洗需要而连接的管路不允许作并联连接,只允许在保证紊流的条件下作串联连接。液压系统中的管路也应避免并联流道,除非用仪器检测证明每个平行的流道中都具有足够的流量。 5.2.3限流元件和易被高流速或颗粒污染物损坏的元件应能从回路或旁路中拆除。拆除元件后还应保证各管路能相互连接,以便冲洗。 5.2.4系统中的关键位置应设有符合GB/T17489的取样阀。 5.3元件清洁度等级
安装于系统中的元件和组件的清洁度等级应至少与规定的系统清洁度等级相同或更高。元件供应商应提供元件清洁度等级的资料。 5.4防腐剂
如果元件含有与系统工作介质不相容的防腐剂,可使用与系统密封件和工作介质相容的去污剂清洗元件。去污剂不允许影响元件的密封。
1
6管路处理
1
6.1制造时管路的准备
用作液压管路的管件应按照制造商与用户间达成的协议去除毛刺。有氧化层和铁锈的管件应按照制造商和用户间达成的协议进行处理。 6.2表面处理
管路安装前,为了维持其清洁度,应使用适当的防护液进行处理。在存储过程中需要采取防措施。 6.3管路与接头的存储
清洁和表面处理过的管件和管接头应立即使用干净的盖子封堵端头,并存放在清洁、干燥的地方。 7液压管路的安装 7.1在液压管路的安装过程中,应避免对管路进行熔焊、钎焊或加热,以防止产生氧化层。如果不可避免,则管路应重新清洗和保护(见GB/Z19848一2005中的5.3)。 7.2宜使用法兰或标准的接头。在安装过程中,管路和元件所有的保护元件(如盖)应尽可能在最后阶段移去。 2
GB/T25133—2010/ISO23309:2007
8冲洗要求
8.1总则 8.1.1要求冲洗的管路应建立专项文件来识别,并记录它们达到的清洁度等级。 8.1.2冲洗方法宜与实际条件相适应。但是,为保证获得满意的效果,应满足下列主要准则:
a)冲洗设备的油箱应至少清洁到与系统指定的清洁度相适应的水平(见第4章); b) 注人系统的冲洗介质应通过合适的过滤器过滤(见5.1d)。在加注冲洗介质的过程中,不应将
空气带入系统中,如果必要,系统应加满冲洗介质至溢流状态;冲洗设备的泵应尽可能近地靠近管路的吸油口,以使流量损失最小;
c) d)流量和温度测量装置应尽可能地靠近管路的回油口; e)过滤器应靠近管路的回油口;吸油口也可以使用过滤器。
8.2清除内表面颗粒 8.2.1为了有效地清除液压管路的颗粒污染物,要求冲洗介质的流动状态为紊流。介质的紊流流动能保证使管路系统中的颗粒污染物脱落并通过过滤器滤除。应使用雷诺数(Re)大于4000的流动介质冲洗系统。
注:如果使用雷诺数小于4000的流体进行冲洗,管路中可能有层流段。 8.2.2使用公式(1)和(2)可计算Re和要求的流量(qv):
Re_21220×qv
....(1)
uXd
v=dXRex
........(2)
........
21220
式中: qv—流量,单位为升每分钟(L/min); —运动黏度,单位为平方毫米每秒(mm/s) d一一管路的内径,单位为毫米(mm)。
8.2.3获得大于4000的Re可能比较困难。Re随着流量的增大或黏度的降低而增大。降低黏度是获得紊流的首选方法。降低黏度可通过提高冲洗介质温度或使用低黏度等级的系统工作介质。
如果提高冲洗介质温度,温度的增高应加以限制,以保证冲洗介质的性质不会变化或系统元件不会受到不利的影响。如果使用专用的冲洗介质,冲洗介质应能与系统计划使用的工作介质相容。首选方案是使用系统工作介质来冲洗或使用与系统工作介质相同的低黏度等级的介质。 8.2.4在寒冷的环境下,冲洗介质的热量可能会受到损失。在这种情况下,为了验证Re大于4000,应在估计的系统温度最低点检查冲洗介质的温度。当测量的介质的最低温度能保证Re大于4000(向制造商咨询相关冲洗介质的黏度和温度数据)时,才允许使用此介质进行冲洗。在非常寒冷的条件下,系统应能保温以保证冲洗介质温度高于使Re大于4000的最低值。 8.2.5在考患通过减小液压管路的直径来维持需要的Re数时应谨慎,因为这可能会对冲洗流量或低压元件产生影响。 8.2.6振动、超声波或改变流向将有助于更快的使管路系统中的颗粒污染物脱落。然而,这仅是对紊态流动的补充,而不能替代流体的紊态流动。 8.2.7应监测管道系统的压力,保证其不超过系统允许的最高工作压力。 8.3过滤器及颗粒的分离 8.3.1总体要求 8.3.1.1冲洗使用的过滤器决定了系统最终的清洁度等级和清洗时间。
3
GB/T25133—2010/ISO23309:2007
8.3.1.2应选用具有合适过滤比的过滤器。如果选用过滤比不合适的过滤器,将出现达不到指定的清洁度等级或需经过延长冲洗时间才能达到的情况。
注:过滤比按GB/T18853确定。 8.3.1.3过滤器应带有堵塞监控装置(如压差指示器)。必要时应更换滤芯,以保证压差在滤芯允许工作范围内。 8.3.2辅助冲洗过滤器 8.3.2.1在冲洗过程中可能需要附加辅助冲洗过滤器,以便:
a) 保护敏感元件,避免颗粒侵入(如用在吸油管处可保护泵免于油箱中污染物的危害),应考附
加压降的作用; b)直接过滤掉元件释放的颗粒(如使用回油过滤器可防止颗粒沉降于油箱中); c)减少冲洗时间。
8.3.2.2应尽可能使用大的冲洗过滤器。最小冲洗过滤器应满足在冲洗介质的实际黏度和最大流量下,通过清洁滤芯的最大压降不超过旁通阀或堵塞报警指示器设定值的5%。 8.4最短冲洗时间 8.4.1所需要的最短冲洗时间取决于液压系统的容量和复杂程度。在冲洗一小段时间后,即使冲洗介质取样表明已经达到指定的固体颗粒污染等级,也应继续进行紊流冲洗。
注意:继续冲洗增加了清除粘附在管壁上的颗粒的可能性。 8.4.2推荐的最短冲洗时间(t)可用公式(3)来计算:
t=20V
........(3)
..
qv
式中: dv——流量,单位为升每分钟(L/min); V—系统容积,单位为升(L)。
9最终清洁度的检验
最终清洁度等级应按照GB/Z20423验证,并应在冲洗操作完成前形成文件。 10标注说明(引用本标准)
当制造商选择遵照本标准时,建议在试验报告、产品样本和销售文件中使用以下说明: “液压系统总成中管路的清洗方法符合GB/T25133一2010《液压系统总成管路冲洗方法》”。
4
GB/T25133—2010/ISO23309:2007
附录A (资料性附录)
系统清洁度等级要求指南
A,1系统可能需要高清洁度的应用场合
当高可靠性为控制要素或系统包含下列元件时,系统需要高的清洁度: a) 比例阀或伺服阀; b) 小流量的流量控制阀和减压阀,特别是在承受高压降的条件下; c)工作状态接近性能极限的马达或泵。
A.2 2系统可能需要中等清洁度的应用场合
当元件在供应商和用户一致同意的非正常工况下运行,且总运行时间又相对受控时,系统应规定中等清洁度。 A.3 满足系统高、中等清洁度要求的介质中固体颗粒污染等级指南
表A.1给出了满足系统高、中等清洁度要求的介质中固体颗粒污染等级的指南。
表A.1满足运行液压系统高、中等清洁度要求的介质中固体颗粒污染等级指南
液体清洁度要求,按GB/T14039表达
系统压力 ≤16MPa(160bar) >16 MPa(160 bar)
中等 19/17/14 18/16/13
高 17/15/12 16/14/11
5