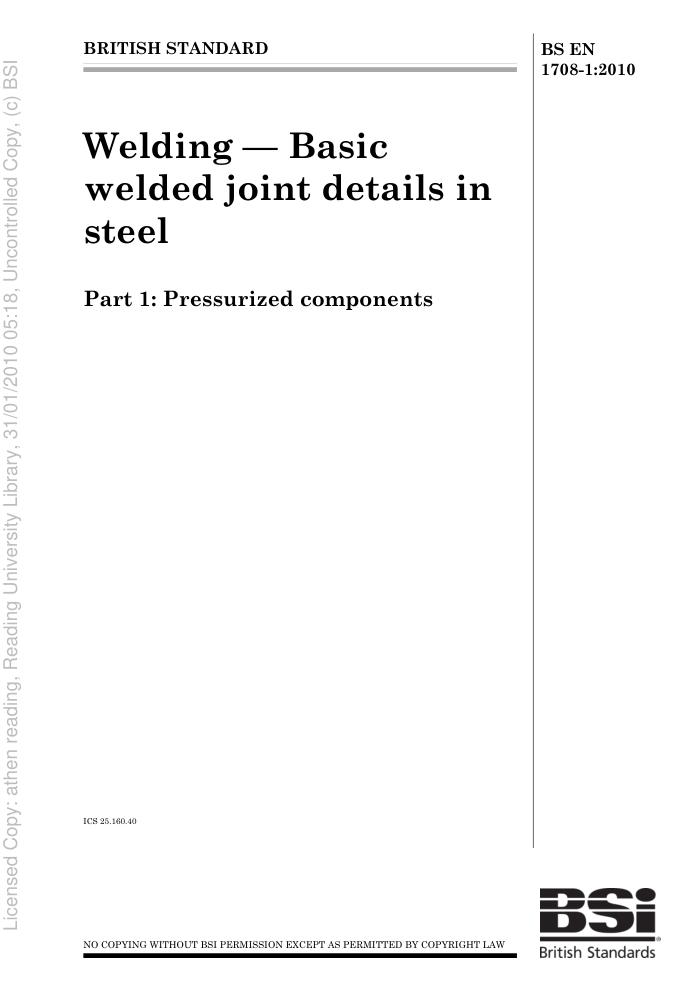
BS EN 1708-1:2010
BRITISH STANDARD
SA
)ese
Welding Basic welded joint details in steel
Part l: Pressurized components
eeeense
ICS 25.160.40
BSi
NO COPYING WITHOUT BSI PERMISSION EXCEPT AS PERMITTED BY COPYRIGHT LAW
British Standards
BSEN1708-1:2010
S
B
National foreword
?
nooon 8101
This British Standard is the UK implementation of EN 1708-1:2010. It supersedes BS EN 1708-1:1999 which is withdrawn. The UK participation in its preparation was entrusted to Technical Committee WEE/-/1, Briefing committeefor welding. A list of organizations represented on this committee can be obtained on request to its secretary. This publication does not purport to include all the necessary provisions of a contract. Users are responsible for its correct application. Compliance with a British Standard cannot confer immunity from legalobligations.
/ L0/L8
pea e e: asaa
This British Standard was published under the authority of the Standards Policy and Strategy
Amendments/corrigenda issued since publication
Date
Comments
Committee on 31 January 2010 BSI 2010
ISBN 978 0 580 55503 9
BSEN1708-1:2010
EN 1708-1
EUROPEANSTANDARD NORMEEUROPEENNE EUROPAISCHE NORM
S
B
?
eon "Ado
January2010
Supersedes EN 1708-1:1999
ICS 25.160.40
English Version
Welding-Basic welded joint details insteel -Part 1:Pressurized
components
“81:50 1 /L0/L8 “ pea ee
Soudage - Descriptif de base des assemblages soudes en
Schweisen - Verbindungselemente beim Schweisen von
Stahl - Teil 1: Druckbeanspruchte Bauteile
acier - Partie 1: Composants soumis a la pression
This European Standard was approved by CEN on 28 November 2009. CEN members are bound to comply with the CEN/CENELEC Internal Regulations which stipulate the conditions for giving this Europe an Standard the status of a national standard without any alteration. Up-to-date lists and bibliographical references concerning s uch national standards may be obtained on application to the CEN Management Centre or to any CEN member. This European Standard exists in three official versions (English, French, German). A version in any other language made by tra nslation under the responsibility of a CEN member into its own language and notified to the CEN Management Centre has the same status as the official versions. CEN members are the national standards bodies of Austria, Belgium, Bulgaria, Croatia, Cyprus, Czech Republic, Denmark, Estonia, Finland, France, Germany, Greece, Hungary, Iceland, Ireland, Italy, Latvia, Lithuania, Luxembourg, Malta, Netherlands, Norway, Poland, Portugal, Romania, Slovakia, Slovenia, Spain, Sweden, Switzerland and United Kingdom.
cen
eed asaa
EUROPEAN COMMITTEE FOR STANDARDIZATION COMITE EUROPEEN DE NORMALISATION EUROPAISCHES KOMITEE FUR NORMUNG
Management Centre: Avenue Marnix 17, B-1000 Brussels
@2010CEN All rights of exploitation in any form and by any means reserved
Ref.No.EN 1708-1:2010: E
worldwide for CEN national Members.
BS EN 1708-1:2010 EN1708-1:2010 (E)
S
B
()
do pai
Contents
Page
Foreword 1
.3
OJ 00 2
Scope Normativereferences Reguirements
a
1
O
3 3.1 Selection of detail... 3.2 Joint preparation (geometry and size). 3.2.1 General. 3.2.2 Jointpreparationgeometry 3.2.3 Weld sizes 3.3 Presentation 3.4 Removalofinternalsharpedgesinbranchbores 3.5 Preparation ofholes in shell forset-throughbranches 3.6 Weids for smooth transition 3.7 Obliqueandtangential branches
8
C
O 3
Tables Table1Butt joints of different thickness Table2—Brancheswithoutcompensationrings Table3Brancheswithcompensationrings Table4—Socketsand couplings. Table5—Flanges Table6—Jacketedvessels Table7Tubeto tubeplate connection...
eig
4
23
...25
....27
upee ea
.31
..42 .46
R Table8Flate endor tubeplatetoshell connections
Table9Internaldiaphragmsandseparators Table1oSupportsandnon-pressureparts.. Table11—Special shell tohead end connections Table 12—Weld ring seal Table13—Pipe details Table14—Blockflanges
53
..54 ..61 .. 62
een
...64 .70
2
BS EN 1708-1:2010 EN1708-1:2010 (E)
sa ()
neoo “81:0010/101
Foreword
This document (EN 1708-1:2010) has been prepared by Technical Committee CEN/TC 121"Welding", the secretariat of which is held by DIN. This European Standard shall be given the status of a national standard, either by publication of an identical text or by endorsement, at the latest by July 2010, and conflicting national standards shall be withdrawn at the latest by July2010. Attention is drawn to the possibility that some of the elements of this document may be the subject of patent rights. CEN [and/or CENELEC] shall not be held responsible for identifying any or all such patent rights. This document supersedes EN1708-1:1999 EN1708,Welding—Basicweld jointdetails insteel, consistsof thefollowingparts
Part 1:Pressurized components Part2:Noninternalpressurizedcomponents
According to the CEN/CENELEC Internal Regulations, the national standards organizations of the following countries are bound to implement this European Standard: Austria, Belgium, Bulgaria, Croatia, Cyprus, Czech Republic,Denmark,Estonia,Finland,France,Germany,Greece,Hungary,Iceland,Ireland,Italy,Latvia Lithuania,Luxembourg,Malta, Netherlands,Norway,Poland,Portugal, Romania, Slovakia,Slovenia,Spain, Sweden, Switzerland and the United Kingdom
e
eeeooasaa
3
BS EN 1708-1:2010 EN1708-1:2010 (E)
sa O
7 Scope The purpose of this European Standard is to exemplify commonly accepted welded connections in pressure systems. It does not promote the standardization of connections that may be regarded as mandatory or restrict development in any way. Stress analysis rules should be considered if necessary This standard contains examples of connections welded by:
do pa
n 1 Kea bupea ean ee : :Adoo asa
Manual metal-arc welding with covered electrode (111); Submerged arc welding (12); Gas shielded metal arc welding (13); Tungsten inert gas arc welding; TIG-welding (14); Plasmaarc welding (15)
8
L:SO LO/
processes (process numbers according to EN IsO 4063)in steel pressure systems.Other processes by agreement.
1 This standard covers welded joint details in steel, but can be applied to other metallic materials. In such cases
the shape and dimensions of the weld should be checked. The estimation of the suitability of welded connections for special service conditions, for example corrosion and fatigue are not specially considered.
Normativereferences The following referenced documents are indispensable for the application of this document. For dated references, only the edition cited applies. For undated references, the latest edition of the referenced document (including any amendments)applies. ENIso4063,Welding and allied processes - Nomenclature of processes and reference numbers (ISO4063:2009) ENIso5817,Welding -Fusion-welded joints in steel, nickel,titanium and their alloys (beam welding excluded)
2
R Corrigendum1:2006) Quality levels forimperfections(IsO 5817:2003,correctedversion:2005,including Technical
ENIsO 9692-1:2003,Welding and allied processes- Recommendations forjoint preparation-Part 1: Manual metal-arc welding, gas-shielded metal-arc welding, gas welding, TiG welding and beam welding of steels (/SO9692-1:2003) ENIso9692-2:1998,Weldingand alliedprocesses-Jointpreparation-Part2:Submerged arcweldingof steels (ISO 9692-2:1998)
3 Requirements
3.1 Selection of detail Connections are not considered to be equally suitable for all service conditions, nor is the order in which they are shown indicative of their relative characteristics. In selecting the appropriate detail to use from the several
4
BSEN1708-1:2010 EN1708-1:2010 (E)
S ()
alternatives shown for each type of connection, consideration shall be given to existing fabrication and service conditions that pertain.
noon “8:010/10
3.2Jointpreparation (geometryand size) 3.2.1 General The limitations quoted in weld profiles and sizes are based on commonly accepted practice, but they may be subjected to modifications if required by special welding techniques or design conditions, which should be included in the design documents and in the welding procedure specifications (WPS), 3.2.2Joint preparationgeometry Examples of recommended joint preparation geometry (e.g.bevel angles,root radius,presence of backing strips,root faces) are referred to ENISO 9692-1 when applicable and to ENISO 9692-2 relative to submerged arc welding process. Missing dimensions of preparations are in accordance with EN IsO 9692-1. In case where full penetration butt joints are indicated, it is intended that they shall be back chipped or gouged and back welded, or alternatively that the welding procedure shall be such as to ensure sound, effective root penetration For relevant difference of thickness (generally a difference of about 3 mm (see Table 1, no. 1.1.1 to 1.1.6) could be considered relevant; in any case the thickness of material shall be taken into account, as well as the shape of the joint) of parts to be butt welded, the thickest element shall be shaped with a slope of 1:5 up to 1:2. Smoother transition of wall thickness is applicable in severe service conditions. 3.2.3 Weld sizes The thickness of welds (in particular of fllet welds), which are not determined by their profile, are based on the assumptionthatthe connection neednotbestrongerthanthe connectedparts
e ea
3.3Presentation
neeon
Figure1-Transversal section
Figure 2-Longitudinal section
The drawings of the nozzle and branch connections (see Tables 2 and 3)show a transversal section of the connection (see Figure 1) and a longitudinal section of the connection (see Figure 2).
3.4Removalof internalsharpedgesinbranchbores It will be noted that the internal edges on the bores of branches are shown partially radiused (for example see Table 2,no.2.1.6)because a stress concentration occurs at thispoint.The roundingof theedges is recommended whenthe branch connection is subjectedto severe service conditions likefatigue,creep and stress corrosion.
s
5
BS EN 1708-1:2010 EN 1708-1:2010 (E)
sa
3.5 Preparationofholesinshellforset-throughbranches In case of set-in and set-through branches (according to Table 2, no. 2.2 and no. 2.3) holes in the shell may be cutandprofiled intwo ways asfollows
do
The depth of the grooves h and h2 may be constant around the hole as shown in Figure 3.
E
81:0001/10/10
2
Key h1, h2 depth of the grooves
Figure3Preparationof holes intheshell
The roots of the joint preparations may be in one plane, as for example when they are machine drilled, in which case the depths of the grooves will vary around the hole as shown in Figure 4
X
Figure 4—Preparation of holes in the shell
3.6Weldsforsmoothtransition In some cases it is convenient to foresee afilletweld providing smooth geometric transition fromthe surface of one welded part to the surface of the other one, e.g. from branch to shell. Its purpose is to soften the notch effect in the branch-shell edge and therefore the throat thickness is not presented on the figure concerned.
bpea ueen e doo s
R 3.7 Obliqueandtangential branches
The welded connections are contained in Tables 1 to 13. Regarding branches, the oblique and tangential ones arenotspeciallyconsidered astheirpreparationis similartothat reported onTables 2and3forradial branches.Onlysome significant cases are therefore considered (see Table2, no.2.2) NOTE1 The welds are only blackened in the following tables when the figures do not give information about the dimension of the values for the preparation. NOTE 2 It is not intended that the values of the dimension given in the tables should be measured precisely but rather the general philosophy should be applied.
6