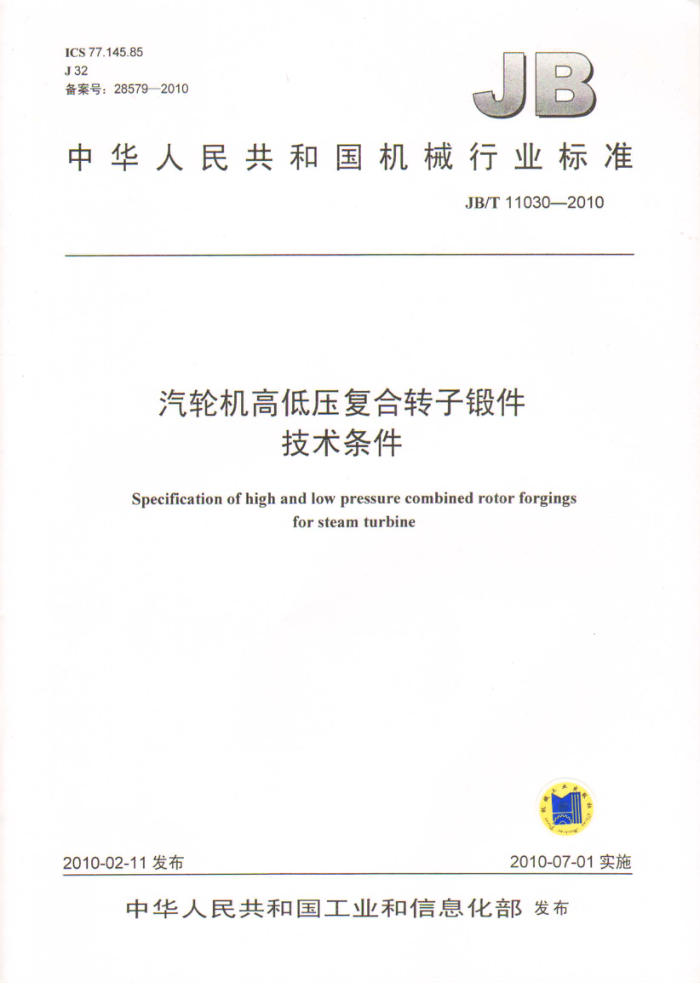
ICS77.145.85 J 32 备案号:28579—2010
中华人民共和国机械行业标准
JB/T11030—2010
汽轮机高低压复合转子锻件
技术条件
Specification of high and low pressure combined rotor forgings
forsteamturbine
2010-07-01实施
2010-02-11发布
中华人民共和国工业和信息化部发布
JB/T110302010
目 次
前言 1 范围 2 规范性引用文件 3 订货要求 4 制造工艺 4.1 冶炼和铸锭 4.2 锻造. 4.3 热处理 4.4 机械加工 4.5 焊接 5 技术要求, 5.1 化学成分, 5.2 力学性能 5.3 硬度... 5.4 无损检测 5.5 金相组织, 5.6 残余应力 5.7 热稳定性. 5.8 尺寸和表面粗糙度
口
检验规则和试验方法 6.1 化学成分分析 6.2 力学性能检验, 6.3 硬度检验 6.4 无损检测 6.5 金相检验. 6.6 残余应力检验 6.7 热稳定性试验. 6.8 复试. 6.9 重新热处理 7验收及质量证明书 7.1.验收 7.2质量证明书 8标志和包装表1化学成分表2成品化学成分的允许偏差表3气体含量表4力学性能表5高温持久强度
6
JB/T11030—2010
前言
本标准由中国机械工业联合会提出。 本标准由机械工业大型铸锻件标准化技术委员会归口。 本标准起草单位:中国第二重型机械集团公司、哈尔滨汽轮机厂有限责任公司。 本标准主要起草人:崔晋娥、白燕。 本标准为首次发布。
1
JB/T110302010
汽轮机高低压复合转子锻件技术条件
1 范围
本标准规定了汽轮机无中心孔高低压复合转子用真空处理的合金钢锻件的订货要求、制造工艺、技术要求,检验规则和试验方法,验收及质量证明书等。
本标准适用于汽轮机在高压侧高温和低压侧高应力下工作的无中心孔高低压复合转子锻件的订货、 制造与检验。 2 规范性引用文件
下列文件中的条款通过本标准的引用而成为本标准的条款。凡是注日期的引用文件,其随后所有的修改单(不包括勘误的内容)或修订版均不适用于本标准,然而,鼓励根据本标准达成协议的各方研究是否可使用这些文件的最新版本。凡是不注日期的引用文件,其最新版本适用于本标准。
GB/T223(所有部分)钢铁及合金化学分析方法 GB/T228 金属材料室温拉伸试验方法(GB/T228-2002,eqvISO6892:1998) GB/T229 金属材料-夏比摆锤冲击试验方法(GB/T229-2007,ISO148-1:2006,MOD) GB/T231.1 金属材料布氏硬度试验第1部分:试验方法(GB/T231.1-2009,ISO6506-1:
2005,MOD
GB/T2039 金属拉伸蠕变及持久试验方法(GB/T2039—1997,eqvISO204:1997) GB/T6394 金属平均晶粒度测定法(GB/T63942002,ASTME112:1996,MOD) GB/T10561-2005钢中非金属夹杂物含量的测定标准评级图显微检验法(ISO4967:1998,IDT) JB/T8468 锻钢件磁粉检验方法 JB/T8707—1998300MW以上汽轮机无中心孔转子锻件技术条件 JB/T8888 环芯法测量汽轮机、汽轮发电机转子锻件残余应力的试验方法 JB/T9021 汽轮机主轴和转子锻件的热稳定性试验方法 ASTMA370钢制品的力学性能试验方法和定义 ASTME292 金属拉伸持久试验方法
3订货要求 3.1供方应有完善的质量保证体系,原则上应具有生产过类似材料、相近尺寸的转子锻件的业绩。 3.2需方应在订货合同书或技术协议中注明采用的标准、材料牌号、锻件强度级别、供需双方明确的相应技术要求和检验项目及本标准要求以外的检验项目。 3.3需方应提供标明力学性能试验取样位置的锻件订货图样并标识锻件发电机端。 3.4需方要求参加现场检验的项目应在合同中注明。 4制造工艺 4.1炼和铸锭 4.1.1锻件用钢应采用电炉冶炼、钢包精炼、真空碳脱氧工艺。经需方同意,也可采用保证质量的其他冶炼方法。 4.1.2钢水应在浇注时进行真空处理,以去除有害气体,特别是氢。在真空处理过程中,真空系统的能力必须大到足以在开浇后2min内就能将初始增高的压强降至较低值,通常应低于133Pa。
JB/T110302010
4.2锻造 4.2.1钢锭上部和下部应有足够的切除量,以确保成品锻件无缩孔、疏松、严重的偏析及其他有害缺陷。 4.2.2采用的锻造方法必须尽可能使整个锻件得到均匀的组织结构,锻压机应有足够的能力,以使锻件的整个截面锻透。应尽可能保持锻件轴线与钢锭的中心线重合。除非订货合同中另有规定,钢质量较好端应为靠近发电机端。 4.2.3可采用粗或直接拔长的锻造方法,总锻比应大于3。 4.3热处理 4.3.1锻后热处理
锻件至少应进行一次正火处理,在正火温度下保持足够长的时间,以保证组织奥氏体化和均匀化;随后冷却到转变温度以下再进行回火, 回火后炉冷或空冷。 4.3.2性能热处理 4.3.2.1转子锻件粗加工后应在垂直状态下进行率火、回火加热,采用分区热处理方法进行性能热处理。 4.3.2.2转子锻件在火温度下均匀加热并充分保温后,对高压侧应进行鼓风喷雾冷却,低压侧应进行喷水淬火。 4.3.2.3转子锻件回火保温足够长的时间后在炉内冷至300C以下再出炉空冷。 4.3.3去除应力处理
在性能热处理及粗加工以后,锻件应在低于转子低压侧回火温度15℃~50℃C范围内去除应力。 锻件应在垂直状态下进行去除应力处理,去除应力处理时应均勾加热,有足够的保温时间,以确保
完全烧透。锻件冷却至400℃以上时的冷却速度应不大于15C/m, 然后炉冷至250℃,再出炉空冷。 4.4机械加工 4.4.1在性能热处理以前,锻件的全部表面应进行第一次租加工。 4.4.2在性能热处理后,超声检测前锻件应进行第二次粗加工。 4.4.3 在超声检测合格后,锻件应进行第三次粗加工。 4.4.4在各项性能检验和超声检测后,锻件应按需方订货图样规定尺寸和公差进行加工。 4.5焊接
在制造和包装过程中,转子锻件不得进行焊接。 5技术要求 5.1化学成分 5.1.1 供方应对每炉钢水进行熔炼分析,分析结果应符合表1规定。
表1化学成分(质量分数)
(%)
材料牌号
Cu Al As Sn Sba
Mn Si
C
T
MO
P
2.00 050 1.00~ 0.20~ V 二 M
0.21~ 0.50~ M V 0.29 1.00 0.10 0.010 0.010 2.50 1.00 1.30 0.30 0.15 0.010 0.020 0.015 0.0015 0.21~ 0.102 I V 台 2.00 1.102 1.00~ 0.20~ ≤ ≤ V M N 0.29 0.37 0.10 0.010 0.010 2.50 1.50 1.30 0.30 0.10 0.008 0.0100.0100.0015
M
25Cr2NiMo1V
1
25Cr2Ni1Mo1V
Sb含量为目标值。
5.1.2 供方应对每个锻件进行成品分析,分析结果应符合表1的规定,但允许有表2规定的偏差。 2
JB/T11030—2010
表2成品化学成分(质量分数)的允许偏差
(%)
材料牌号 C Mn Si 25C12NiMo1V
Mo
Sb
S
CI
Ni
P
As
Sn
4
C
王0.02 ±0.04+0.02+0.003+0.003±0.05 ±0.05±0.02±0.01 +0.02 2+0.002+0.005+0.002+0.0002
25C/2Ni1Mo1V 5.1.3 供方应对每个锻件进行气体含量分析,分析结果应符合表3的规定。
表3气体含量(体积分数)
(%)
H2 ≤1.5X10-4
N2 ≤100X10
0
≤35X104
5.2力学性能 5.2.1常温力学性能
锻件的常规力学性能应符合表4的规定。
表4 力学性能
锻件强度级别
项 目
取样位置
590 高压侧 590~690
700 低压侧
620 高压侧
735 低压侧 ≥735
Rpo.2 MPa Rm MPa A4 (%) Z (%) Akv J FATTSO C 上平台能
本体径向、轴端
700
620~720
本体径间、轴端本体径向、轴端
≥720
≥720
>800
≥820
≥15
≥16
≥16
≥16
≥45
本体径向、轴端
≥45
≥45
≥45
本体径向
≥25
M60
≥30
≥60
本体径向
≤80
≤75
≤20
本体径向
≥75
≥80
75
≥80
J
推荐用材料牌号
25C12NiMo1V
25CT2Ni1Mo1V
5.2.2 高温持久性能(高压侧叶轮体)
当需方有要求时,应在转子高压侧取光滑一缺口复合试样进行高温持久强度试验,结果应符合表5 的规定。
表5高温持久强度
温度 ℃ 510 540 565 595
应力 MPa 365 310 260 220
试验要求
断裂时间≥100h 伸长率≥15%
断口不得在V型缺口上
2
JB/T11030—2010
5.3硬度
在性能热处理以后应检查锻件硬度的均匀性,硬度的绝对值供参考。在同一圆周上各点间的硬度差不应超过30HBW。 5.4无损检测 5.4.1一般要求
锻件不应有裂纹、白点、缩孔、折叠、过度的偏析以及超过允许的夹杂和疏松 5.4.2磁粉检测
在转子锻件的外圆表面完成精加工以后,应对转子锻件本体轴承部位表面和两轴身外端面及过渡区进行磁粉检测。磁粉检测由需方进行,但供方应保证检测结果符合以下要求:
a)转子外圆表面上不允许有长度大于1.5mm的任何缺陷显示; b)同一母线上两个缺陷之间的距离小于其中较大缺陷长度五倍时,按一个连续缺陷处理; c)转子最终检查时,除了轴承部位之外,在其他部位发现有大于1.5mm的缺陷显示时,允许进行
局部打磨和抛光,抛光的深度不应超过1.6mm,并应与周围表面圆滑过渡。
5.4.3超声检测
锻件至少应进行两次超声检测,超声检测结果应符合以下要求。 5.4.3.1当量直径1.6mm以下的单个分散缺陷信号不计,但杂波高度应低于当量直径1.6mm的缺陷幅度的50%。
注:单个的分散缺陷是指相邻两缺陷之间的距离大于其中较大缺陷当量直径10倍的缺陷。 5.4.3.2当量直径为1.6mm~Φ3.5mm的所有缺陷均应记录其轴向、径向和周向位置并报告需方。在转子锻件的叶轮体表面150mm以内的区域不允许存在当量直径大于$1.6mm的单个缺陷,其余区域允许存在当量直径为g1.6mm~g3.5mm的缺陷总数不得超过20个,不允许存在当量直径大于3.5mm 的任何缺陷。 5.4.3.3在转子锻件的叶轮体表面150mm以内的范围内不允许有g1.2mm~g1.6mm密集缺陷,其余区域允许有当量直径g1.2mm~1.6mm的非金属夹杂密集区三个,应记录密集区尺寸及其轴向、径向和周向位置,并报告需方。 5.4.3.4由缺陷引起底波衰减损失达到3dB时,应当记录并报告给需方。 5.4.3.5不允许存在由缺陷引起的游动信号。 5.4.3.6供方应向需方提供用2MHz~2.5MHz和4MHz5MHz探头分别在转子最大直径处两端及中间三处测得的材料衰减数据。 5.4.3.7当锻件的超声检测结果超出上述规定时,应由供需双方进行复验和协商,但锻件是否可判合格应由需方决定。 5.5金相组织 5.5.1锻件的平均晶粒度为高压侧不应粗于2.0级,低压侧不应粗于3.0级。 5.5.2锻件的A、B、C、D四种类型夹杂物均不应超过3.0级。 5.6残余应力
锻件应测定残余应力。高压侧、低压侧的残余应力值应分别不大于表4中屈服强度下限值的8%,如果残余应力超过该规定,则锻件应按4.3:3的规定进行补充去应力回火,并重新测定残余应力和硬度值。 5.7热稳定性
热稳定性试验结果应符合JB/T9021的规定,供方应对试验结果负责 5.8尺寸和表面粗糙度
加工后的锻件应符合订货图样规定的尺寸、公差和表面粗糙度要求。 6检验规则和试验方法
A
JB/T11030—2010
6.1化学成分分析 6:1.1化学成分分析应按GB/T223规定的方法或能保证分析质量的其他方法进行。 61.2每炉(每包)钢水可于浇注时取样测定钢水的化学成分,多炉合浇时还应报告权重平均分析结果。当无法进行熔炼分析时,允许用成品分析代替熔炼分析,但从锻件上取样进行分析的分析结果应符合成品分析要求。 6.1.3成品分析试样可取自锻件延长部分,或取自径向性能验收试样。 6.1.4气体分析用试样应在径向试棒上切取。 6.2力学性能检验 6.2.1拉伸性能试验应按GB/T228或ASTMA370规定的方法进行。 6.2.2冲击性能试验应按GB/T229规定的方法进行,冲击试样槽口方向应与转子的轴线平行。 6.2.3转子的轴端和径向试样应按需方订货图样和取样图规定的部位和数量切取。 6.2.4高温持久强度试验应按ASTME292和GB/T2039的规定进行。 6.3硬度检验
硬度试验应按GB/T231.1规定的方法进行。在每个锻件两轴颈及轴身部位高压侧和低压侧的外圆表面每隔90°各测一点(共16点)。 6.4无损检测 6.4.1磁粉检测应按JB/T8468进行。 6.4.2超声检测应按JB/T8707—1998中附录A的规定进行。若按JB/T8707-—1998中附录A的表A.1 中的A.1、A.2项采用纵波直束超声检测合格后,则在A.3中选择α=7°、α=14°在B.1中选择β= 45°探头进行检测,若上述检测合格后不再用其他探头进行检测;若检测结果出现疑义,再按附录A 的表A.1的要求,采用其他探头全面进行检测。 6.4.3供方至少应进行两次超声检测,第一次检测在调质之前,第二次检测在调质之后,两次检测结果均应提供给需方。 6.5金相检验 6.5.1晶粒度检验应按GB/T6394的规定进行。晶粒度检验的试样为取自轴身电机端的径向试样。 6.5.2夹杂物检验应按GB/T10561—2005附录A评级图I进行评定。夹杂物检验试样为取自轴身电机端的径向试样。 6.6残余应力检验 6.6.1应采用切环法或环芯电阻应变法测定锻件的残余应力。 6.6.2采用切环法测定残余应力时,在轴身一端切取25mm×25mm的圆环,用测量该圆环切割前后平均变形量的方法来计算残余应力,计算公式为:
CE8D
.(1)
式中: F一 残余应力,单位为MPa; E 材料的弹性模量,单位为MPa; 8一直径增量的代数值,单位为mm; D一切割前圆环的外径,单位为mm。
6.6.3采用环芯电阻应变法测定残余应力时,应在订货图样要求的部位按JB/T8888的规定进行。 6.7热稳定性试验
热稳定性试验应按JB/T9021规定的方法进行。 6.8复试 6.8.1如果力学性能检验中某一试验结果不合格,可在锻件上与原试样相邻部位取两个试样进行复试。 复试结果以及初试、复试三个试验结果的平均值均应满足规定要求。
5