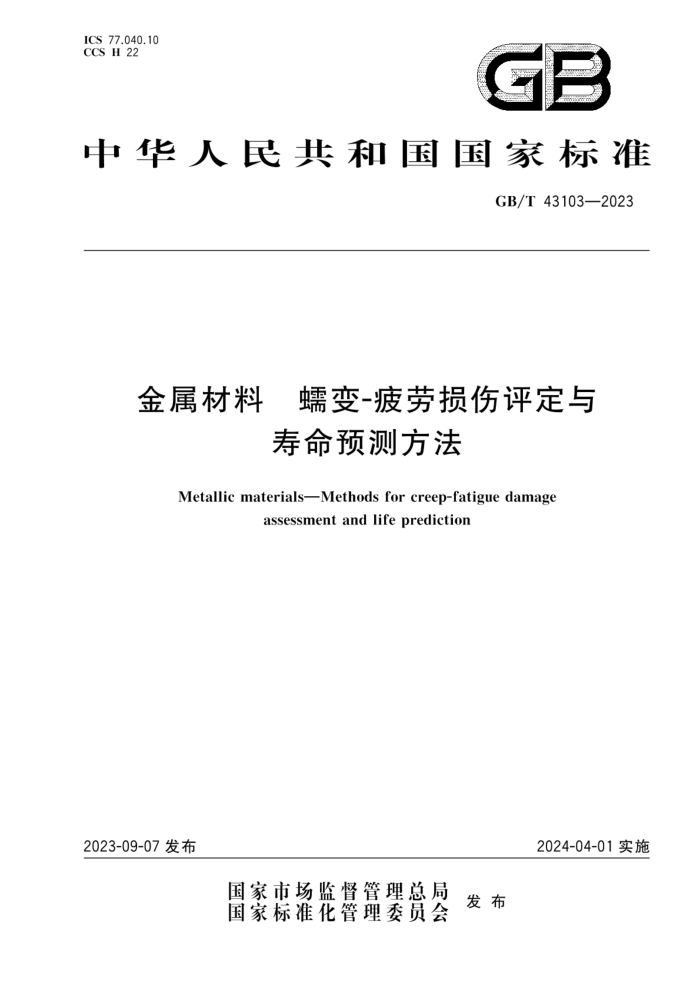
ICS77.040.10 CCS H 22
GB
中华人民共和国国家标准
GB/T43103—2023
金属材料 蠕变-疲劳损伤评定与
寿命预测方法
Metallic materials-Methods for creep-fatigue damage
assessment andlifeprediction
2024-04-01实施
2023-09-07发布
国家市场监督管理总局 发布国家标准化管理委员会
GB/T43103—2023
目 次
前言引言范围
1 2 3 4 5 原理 6
规范性引用文件术语和定义符号和说明
基础试验 6.1 试验要求 6.2 材料性能数据蜻变-疲劳损伤评定图基本步骤 7.1 蠕变-疲劳损伤散点 7.2 损伤准则临界线 7.3 蠕变-疲劳损伤评定图高温结构蠕变-疲劳损伤评定和寿命预测程序 8.1 基本应力分析 8.2 稳态应力-应变分析 8.3 数据处理 8.4 高温结构蠕变-疲劳损伤评定 8.5 高温结构变-疲劳寿命预测附录A(资料性) 应变能密度耗散变-疲劳寿命预测模型参数拟合方法附录B(资料性) 蠕变损伤公式推导附录C(资料性) 非弹性分析· 附录D(资料性) 高温结构蠕变-疲劳损伤评定和寿命预测程序应用案例参考文献
7
8
11
14
16 18 20 23
GB/T 43103—2023
前言
本文件按照GB/T1.1一2020《标准化工作导则 厂第1部分:标准化文件的结构和起草规则》的规定
起草。
请注意本文件的某些内容可能涉及专利。本文件的发布机构不承担识别专利的责任。 本文件由中国钢铁工业协会提出。 本文件由全国钢标准化技术委员会(SAC/TC183)归口。 本文件起草单位:华东理工大学、中国联合重型燃气轮机技术有限公司、中机试验装备股份有限公
司、冶金工业信息标准研究院、中国石油大学(华东)、天津大学、厦门市特种设备检验检测院、深圳万测试验设备有限公司、中国航发湖南动力机械研究所、中国航发商用航空发动机有限责任公司、南京工业大学、苏州热工研究院有限公司、中广核研究院有限公司、中国核动力研究设计院、中船重工(重庆)西南装备研究院有限公司。
本文件主要起草人:张显程、王润梓、束国刚、涂善东、轩福贞、董莉、蒋文春、陈刚、马伟、侯慧宁、 李维、张成成、谈建平、伏喜斌、黄星、王小威、李凯尚、聂文睿、马双伟、徐火力、夏威喜、曾飞、朱贺、李一磊、 巩建鸣、唐敏锦、张玉财、川阳、王煜伟、刘天佐、陈钢、胡洪伟、高云霄、邹志坚。
I
GB/T 43103—2023
引言
在航空、能源和电力等领域中,高温装备的工作环境日趋复杂,其中关键热端限寿部件除了承受稳态运行的恒定载荷之外,通常还承受装置起停和温度波动等引起的交变载荷作用,其服役过程伴随着严重的端变-疲劳载荷的交互作用。研究表明,蠕变-疲劳交互作用下的金属材料寿命远低于单一疲劳或者端变机制下的材料寿命。传统基于单一机制的损伤评定和寿命预测方法无法准确预估螨变-疲劳载荷下材料的失效循环周次和部件的使用寿命。因此,建立蜻变-疲劳损伤评定和寿命预测方法是确定蜻变-疲劳载荷下高温装备使用寿命的关键,对保障高温装备的寿命可靠性具有重要意义。
GB/T43103—2023
金属材料蠕变-疲劳损伤评定与
寿命预测方法
1范围
本文件规定了金属材料蜻变-疲劳损伤评定与寿命预测方法相关的原理和基础试验、蜻变-疲劳损
伤评定图基本步骤、高温结构蠕变-疲劳损伤评定和寿命预测程序。
本文件适用于大气环境下承受蠕变-疲劳载荷的无宏观缺陷金属材料以及存在裂纹萌生风险的高温结构临界区域。
规范性引用文件
2
下列文件中的内容通过文中的规范性引用而构成本文件必不可少的条款。其中,注日期的引用文
件,仅该日期对应的版本适用于本文件;不注期的引用文件,其最新版本(包括所有的修改单)适用于本文件。
GB/T 2039 金属材料 单轴拉伸螨变试验方法 GB/T 15248 金属材料轴向等幅低循环疲劳试验方法 GB/T 38822 金属材料 端变-疲劳试验方法
术语和定义
3
GB/T38822界定的以及下列术语和定义适用于本文件。
3.1
循环周次 numberofcycle 在加载过程中,试验控制变量应变随试验时间变化的不可重复拆分的最小波形单元。 注:见图1a)。
3.2
应力松弛 stressrelaxation 在一定温度下,加载应变保持期间应力响应随时间逐渐减小的现象。 注:见图1b)。
3.3
滞后回线 hysteresisloop 一个循环周次内应力-应变响应的关系曲线注:见图1c)。
3.4
半寿命循环周次 half-lifecycle 材料失效循环周次的一半。 注:对于大部分金属材料而言,半寿命循环周次是循环稳定的代表性周次
1
GB/T43103—2023
3.5
蠕变-疲劳损伤散点creep-fatiguedamagescatter 以计算的累积疲劳损伤为横坐标、计算的累积蠕变损伤为纵坐标的二维散点。 注:本文件通过应变能密度耗散模型计算累积疲劳和蜻变损伤。
3.6
线性损伤准则临界线 critical line of linear damagerule 以线性损伤累积方程构建,且对所有蠕变-疲劳损伤散点具有下包络性质的直线。
3.7
双线性损伤准则临界线critical lineofdouble-lineardamagerule 以双线性损伤累积方程构建,且对所有蠕变-疲劳损伤散点具有下包络性质的折线。
3.8
连续损伤准则临界线criticallineofcontinuousdamagerule 以连续损伤累积方程构建,且对所有蠕变-疲劳损伤散点具有下包络性质的曲线。
3.9
螺变-疲劳损伤评定图 creep-fatigue damage assessment diagram 分别以累积疲劳和蠕变损伤为横坐标和纵坐标轴绘制的二维图形。 注:其中包含一系列蜻变-疲劳损伤散点和损伤准则临界线。
3.10
蠕变-疲劳安全域 safetymargin ofcreep-fatigue 在蠕变-疲劳损伤评定图中,损伤准则临界线以内的区域。
3.11
稳态循环周次 steadycycle 高温结构在经历循环周期变化后,滞后回线趋于稳定或保持恒定所对应的循环周次。
号
4e
46
Lp
Feio
b)保载时间内的应力松弛
a)蠕变-疲劳循环周次
c)滞后回线
图1蠕变-疲劳应力-应变关系曲线
4符号和说明
本文件使用的符号和说明见表1。
2
GB/T43103—2023
表 1 符号和说明
符号 D. 蠕变损伤的累积值 Dr 疲劳损伤的累积值 D.,D 蠕变-疲劳双线性损伤准则临界线中累积疲劳和蠕变损伤的转折点 D.,D. 损伤准则临界线和损伤累积轨迹线的交点 d.
说明
单位
一
一个循环周次内螨变损伤值一个循环周次内疲劳损伤值个循环周次内蠕变和疲劳叠加的总损伤值弹性模量等效弹性模量多轴蠕变延性与单轴蠕变延性的比值试验的蜗变-疲劳寿命低周疲劳试验下的失效循环周次
d: d. E E MDF N. N ro N. 预测的蜻变-疲劳寿命 n
一
MPa MPa
一一
连续损伤准则临界线中幂指数的数值蠕变-疲劳试验温度个循环周次内拉伸峰值应变保持不变的时间致使金属材料蠕变失效所需要的时间弹性跟随因子,用以描述保载阶段弹性跟随效应程度的标量
T th tR Z E19E2+E3 微元体主平面上的正应变
℃ 5, s
mm/mm mm/mm mm/mm mm/mm mm/mm mm/mm mm/mm mm/mm mm/mm
致使金属材料蠕变失效所需要的应变 ·个循环周次内最大应变的代数值。拉伸为正,压缩为负一个循环周次内最小应变的代数值应变范围的一半一个循环周次内保载时间内产生不可回复的变应变范围个循环周次内塑性应变范围和变应变范围的代数和个循环周次内加卸载过程产生不可回复的塑性应变范围个循环周次内最大和最小应变的代数差材料在单拉或单压时,横向与轴向正应变的绝对值的比值蠕变应变能密度
er Emx E min Ae: Ae Ain Aep Ae: 1 w w. 蠕变应变能密度耗散率
MJ/m3 MJ/(m"· s) MJ/ma MJ /m MPa MPa
蠕变失效应变能密度免螨变损伤所对应的螨变失效应变能密度平台值微元体主平面上的正应力三个主应力的代数平均值
wf 'l.cit 01+02+03 CH
3
GB/T43103—2023
表1符号和说明(续)
符号 0m O max mi G: Ag Ao;
说明
单位 MPa MPa MPa MPa MPa MPa
个循环周次内峰谷值应力的代数平均值个循环周次内最大应力代数值。拉伸为正,压缩为负个循环周次内最小应力代数值个循环周次内保载时间结束后的应力一个循环周次内最大和最小应力的代数差保载开始和结束阶段应力水平的代数差
5原理
通过一系列材料的蠕变-疲劳基础试验,获取其在特定温度下的变-疲劳性能。根据应变能密度耗散模型,计算材料累积疲劳和蠕变损伤,绘制蠕变-疲劳损伤的散点分布图,确定损伤准则临界线及蠕变-疲劳损伤评定图。
通过直接测量或借助有限元分析方法获取高温结构临界区域的应力-应变响应,结合多轴损伤公式计算稳态循环周次下的疲劳和蠕变损伤,从而进行高温结构临界区域的蠕变-疲劳损伤评定与寿命预测。
6 基础试验
6.1 试验要求 6.1.1基础试验包括单轴低周疲劳、单轴拉伸蠕变以及单轴蠕变-疲劳3类试验。 6.1.2按照GB/T15248进行单轴低周疲劳试验,应实施不少于4组不同应变范围下的单轴低周疲劳试验,用以拟合疲劳损伤公式中的参数 6.1.3按照GB/T2039进行单轴拉伸螨变试验,应实施不少于5组不同恒定加载应力下的单轴拉伸端变试验,用以拟合端变损伤公式中的参数。 6.1.4按照GB/T38822进行单轴蠕变-疲劳试验,应实施不少于共12组不同保载时间和应变范围下的端变-疲劳试验,用以建立端变-疲劳损伤评定图 6.1.53类试验应在同一温度下进行,以获得该温度下金属材料的疲劳、蠕变及蠕变-疲劳力学性能。 其中,单轴低周疲劳与单轴蠕变-疲劳均为应变控制,且在加卸载过程中保持同一应变速率。 6.2# 材料性能数据 6.2.1 低周疲劳力学性能包括不同应变范围下的低周疲劳寿命、半寿命循环周次的塑性应变范围和峰值应力等。 6.2.2拉伸蠕变力学性能包括不同应力水平下的蠕变延性和蠕变断裂时间等。 6.2.3蠕变-疲劳力学性能包括蜻变-疲劳寿命以及半寿命循环周次的峰值应力、谷值应力、塑性应变范围、弹性模量以及不同应变保载水平内应力松弛数据等。
4