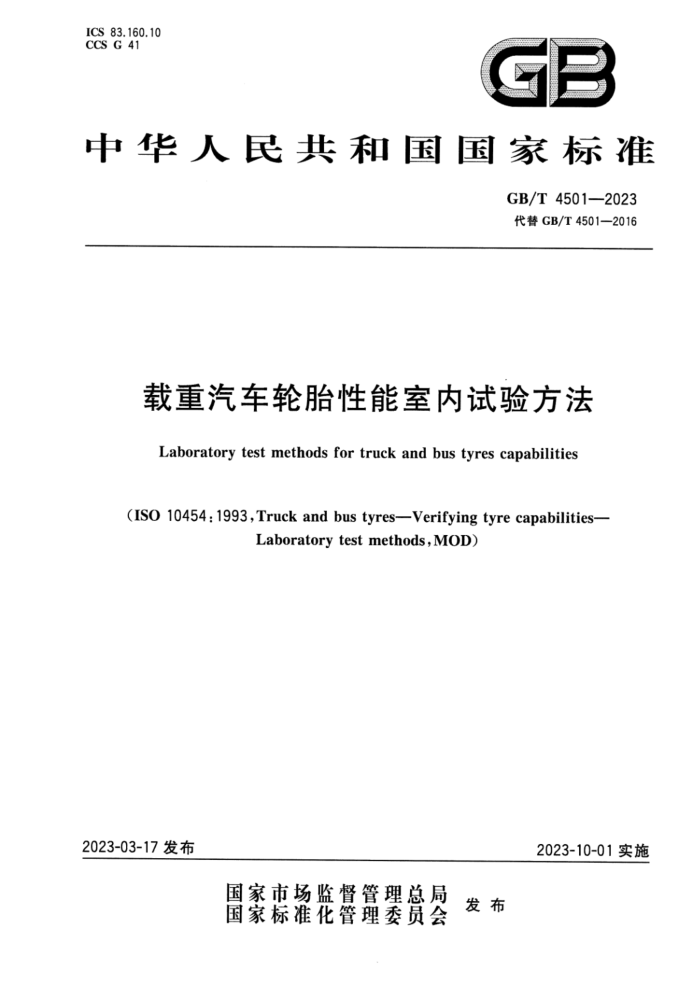
ICS 83.160.10 CCS G 41
GB
中华人民共和国国家标准
GB/T 4501—2023 代替GB/T4501—2016
载重汽车轮胎性能室内试验方法
Laboratory test methods for truck and bus tyres capabilities
(ISO 10454: 1993,Truck and bus tyres-—Verifying tyre capabilities-
Laboratory test methods,MOD)
2023-03-17发布
2023-10-01实施
国家市场监督管理总局
国家标准化管理委员会 发布
GB/T 4501—2023
前言
本文件按照GB/T1.1一2020《标准化工作导则第1部分:标准化文件的结构和起草规则》的规定起草。
本文件代替GB/T4501一2016《载重汽车轮胎性能室内试验方法》。与GB/T4501一2016相比,除结构调整和编辑性改动外,主要技术变化如下:
更改了适用范围(见第1章,2016年版的第1章);一删除了对气压表最大量程的规定(见2016年版的4.3); —一删除了对试验轮胎外观质量的规定(见2016年版的5.1.1.1、5.2.1.1、5.3.1.1); —更改了试验轮辋的规定(见5.1.1.1、5.2.1.1、5.3.1.1,2016年版的5.1.1.2、5.2.1.2、5.3.1.2);一更改了轻型载重汽车轮胎中速度级别Q级及其以上雪地胎耐久试验速度(见表3,2016年版
的表 3); 更改了耐久性能试验的判定规则(见6.1,2016年版的6.1);
一增加了微型、轻型载重汽车轮胎中轮辋名义直径≥15、层级18的最小破坏能值及无内胎载重
汽车轮胎中轮辋名义直径≤17.5、18层级的最小破坏能值(见表6); --增加了速度符号B和对应的速度(见附录C)。 本文件修改采用ISO10454:1993《卡车和客车轮胎检验轮胎性能室内试验方法》。 本文件与ISO10454:1993相比,在结构上有较多调整。两个文件之间的结构编号变化对照一览表
见附录A。
本文件与ISO10454:1993相比,存在较多技术性差异,在所涉及的条款的外侧页边空白位置用垂直单线(I)进行了标示,这些技术差异及其原因一览表见附录B。
本文件做了下列编辑性改动:
为与现有标准协调,将标准名称改为《载重汽车轮胎性能室内试验方法》;
-
—增加了资料性引用的GB/T2977;一增加了附录A(资料性)本文件与ISO10454:1993结构编号对照一览表; --增加了附录B(资料性)本文件与ISO10454:1993技术性差异及其原因;
删除了ISO10454:1993的附录A(资料性)非标准标记的轮胎试验条件;删除了ISO10454:1993的附录B(资料性)参考文献。
请注意本文件的某些内容可能涉及专利。本文件的发布机构不承担识别专利的责任。 本文件由中国石油和化学工业联合会提出。 本文件由全国轮胎轮辋标准化技术委员会(SAC/TC19)归口。 本文件起草单位:风神轮胎股份有限公司、山东玲珑轮胎股份有限公司、双钱轮胎集团有限公司、中
策橡胶集团股份有限公司、赛轮集团股份有限公司、北京橡胶工业研究设计院有限公司、浦林成山(山东)轮胎有限公司、四川轮胎橡胶(集团)股份有限公司、三角轮胎股份有限公司、双星集团有限责任公司、贵州轮胎股份有限公司、厦门正新橡胶工业有限公司、山东金宇轮胎有限公司、安徽佳通乘用子午线轮胎有限公司、青岛森麒麟轮胎股份有限公司、山东兴鸿源轮胎有限公司、山东昌丰轮胎有限公司、合肥万力轮胎有限公司、江苏通用科技股份有限公司、通力轮胎有限公司、韩泰轮胎有限公司、普利司通(中国)投资有限公司、住友橡胶(中国)有限公司、大连固特异轮胎有限公司、米其林(中国)投资有限公司、 大陆马牌轮胎(中国)有限公司、优科豪马橡胶有限公司、上汽通用五菱汽车股份有限公司、南京依维柯汽车有限公司、焦作市质量技术监督检验测试中心、黑龙江红河谷汽车测试股份有限公司、天津久荣车
-I
GB/T 4501—2023
轮技术有限公司、汕头市浩大轮胎测试装备有限公司、青岛高测科技股份有限公司、浙江保康轮毂制造有限公司。
本文件主要起草人:任绍文、李昭、陈少梅、许连玉、宋江红、侯晓倩、牟守勇、徐丽红、姜锡洲、 谢成艺、戴春丽、邢正涛、蒋中凯、陈建明、杨万龙、陈志友、秦靖博、李仁国、项晓明、付波涛、丁振洪、 高明、刘清杰、朱诚、章斌、尹庆叶、陆奕、马忠、王镇潇、徐铁、朱晓、张宏伟、赵鑫宏、顾正、陈迅、唐顺锋、 王克先、郑蕊、李淑环、李苗苗、龙盛忠、杨忠、王红闪。
本文件所代替文件的历次版本发布情况为:
GB/T4501,1984年首次发布,1998年第一次修订; -2008年第二次修订时,并人了GB/T6327—1996《载重汽车轮胎强度试验方法》 (GB/T63271996的历次版本发布情况为:1986年首次发布,1996年第次修订)、 GB/T7035一1993《轻型载重汽车轮胎高速性能试验方法转鼓法》(GB/T7035一1993的历次版本发布情况为:1986年首次发布,1993年第一次修订); -2016年第三次修订;
一本次为第四次修订。
GB/T4501—2023
载重汽车轮胎性能室内试验方法
1范围
本文件描述了载重汽车轮胎性能检验的实验室试验方法,包括试验仪器设备与精度、试验条件、试验步骤、判定规则和试验报告。在提出的试验方法中,仅有某些试验方法的应用依据被测轮胎的类型决定。
本文件包括:
耐久性能试验:通过在规定负荷和速度下的行驶时间,评价轮胎的耐疲劳性能;一高速性能试验:按照轮胎速度符号,评价轮胎高速行驶性能;
强度性能试验:通过检测轮胎胎冠部位的破坏能,评价轮胎结构性能。 本文件所列试验方法不宜用于轮胎产品的性能或质量水平的分级。 本文件适用于新的载重汽车充气轮胎和翻新载重汽车充气轮胎,其他轮胎经相关方协商同意,可参
照本文件进行试验。
2规范性引用文件
下列文件中的内容通过文中的规范性引用而构成本文件必不可少的条款。其中,注日期的引用文件,仅该日期对应的版本适用于本文件;不注日期的引用文件,其最新版本(包括所有的更改单)适用于本文件。
GB/T6326轮胎术语及其定义(GB/T6326—2014,ISO4223-1:2002NEQ)
3术语和定义
GB/T6326界定的以及下列术语和定义适用于本文件。
3.1
试验速度 testspeed 钢制试验转鼓旋转时鼓面沿周向线速度。
4试验仪器设备及其精度要求
4.1 高速耐久试验机 4.1.1试验机转鼓直径应为1700mm士17mm。 4.1.2 试验机转鼓的试验鼓面应为平滑的钢质面,其宽度应不小于试验轮胎的断面总宽度。 4.1.3 试验加载装置的加载能力应能满足试验方法要求,其精度为满量程的士1.5%。 4.1.4 试验机转鼓及试验设备的速度能力应满足试验方法的要求,其速度精度为+km/h。 4.1.5 试验机转鼓的径向跳动不应大于0.25mm。 4.1.6 6环境温度测量装置应设置在距离试验轮胎150mm~1000mm的范围内。 4.2强度试验机 4.2.1 试验机上应配备一个足够长的钢质圆柱形压头,压头端部为半球形。载重汽车公制系列轮胎按
1
GB/T4501-2023
|照表1的规定采用不同的压头直径;载重汽车英制系列轮胎按照表2的规定采用不同的压头直径。
表1载重汽车公制系列轮胎强度试验用压头直径
单位为毫米
单胎负荷指数
压头直径土0.5
≤121 122~134 ≥135
19 32 38
表2载重汽车英制系列轮胎强度试验用压头直径
单位为毫米压头直径土0.5
轮胎类型
19 19 32 38 32 38
微型、轻型载重汽车轮胎
轮辋名义直径≤17.5
无内胎
12PR及以下 14PR及以上
轮辋名义直径>17.5
载重汽车轮胎
12PR及以下 14PR及以上
有内胎
轮辋名义直径≥16,且单胎最大负荷能力≥1500kg的轻型载重汽车轮胎,压头直径为32mm。
4.2.2 压头装置应能逐渐递增地施加负荷,力和位移指示器精度为满量程的土1%。 4.2.3 设备速度精度为满量程的士3%。 4.3 充气压力表
精度为士10kPa。
5 试验方法
5.1 耐久性能试验 5.1.1 试验条件 5.1.1.1 试验轮辋宜符合GB/T2977或相关行业技术文件中有关测量轮辋的规定。将试验轮胎安装在试验轮辋上,充以胎侧标识的负荷能力相应气压(当规定单胎和双胎两种使用条件时,以单胎负荷能力所对应的气压为准)。
注:相关行业技术文件仅适用于不在GB/T2977范围内的载重汽车轮胎规格。 5.1.1.2 轮胎轮辋组合体在38℃士3℃温度下,停放至少3h。 5.1.1.3 试验转鼓以匀加速启动到初始试验速度的时间应在5min以内。 5.1.1.4 各速度符号轮胎的耐久性试验条件应符合表3的规定。
2
GB/T4501—2023
表3 载重汽车轮胎耐久性试验条件
试验速度 km/h
轮胎负荷能力的百分比
% 持续时间 16 h (第二阶段)
轮胎速度符号
子午线轮胎
斜交轮胎
7 h (第一阶段)
24 h (第三阶段)
a)单胎负荷能力<1500kg
E G J K L M N P
35 40 50 55 65 80 90 100 120
35 40 50 55 55 65
65
85
100
70
90
105
75§
95b
115
Q及其以上 b)单胎负荷能力≥1500kg
/
E G J K L M N P 牵引型花纹轮胎按普通轮胎的85%试验速度进行试验。 单胎负荷能力≥1500kg,且最高速度为70km/h及其以下的轮胎,按30km/h试验速度进行试验。 单胎负荷能力≥1500kg,且最高速度为160km/h及其以上的子午线轮胎,按110km/h试验速度进行试验。 单胎负荷能力<1500kg,且最高速度为160km/h及其以上的雪地轮胎,按110km/h试验速度进行试验。 轮胎速度符号对应的速度按附录C的规定。 第一和第二试验阶段的时间分别为4h和6h。
35 45 50 55 65 70 80 90
35 35 40 50 50
65
85
100
-
5.1.2 试验步骤 5.1.2.1 将停放后的轮胎气压重新调整到5.1.1.1规定值 5.1.2.2 将按上述条件准备好的轮胎轮辋组合体安装在试验轴上,使之垂直转鼓外表面加压。 5.1.2.3 试验期间环境温度为38℃士3℃。 5.1.2.4 按表3规定的条件进行试验。整个试验过程应连续进行,不应调整轮胎气压,不应人为地冷却轮胎,各阶段相应的试验负荷保持不变。
3
GB/T4501—2023
5.1.2.5 5按规定程序完成试验后,让试验轮胎自然冷却15min~25min并应在此规定时间段内测量轮胎气压,待完全冷却后卸下轮胎进行外观检查。 5.2高速性能试验(微型、轻型载重汽车轮胎) 5.2.1试验条件 5.2.1.1试验轮辋宜符合GB/T2977或相关行业技术文件中有关测量轮辋的规定。将试验轮胎安装在试验轮辋上,充以轮胎胎侧标识的负荷能力相应气压(当规定单胎和双胎两种使用条件时,以单胎负荷能力所对应的气压为准)。
注:相关行业技术文件仅适用于不在GB/T2977范围内的载重汽车轮胎规格。 5.2.1.2充气后的试验轮胎和轮辋组合体在38℃士3℃的温度下停放至少3h。 5.2.1.3试验转鼓以匀加速启动到初始试验速度的时间应在10min以内。 5.2.1.4试验条件应符合表4的规定。表4中,除第1试验阶段外,其他各试验阶段速度改变到速度稳定,所需时间应在1min以内。 5.2.1.5在整个试验过程中,环境温度应保持在38℃士3℃的范围内。 5.2.2试验步骤 5.2.2.1将停放后的试验轮胎气压重新调整到5.2.1.1规定值。 5.2.2.2将按上述条件准备好的试验轮胎和轮辋组合体安装在试验机上,并使其垂直于试验转鼓外表面施加试验负荷,试验负荷应为单胎最大负荷的90%。 5.2.2.3按表4的规定进行试验。整个试验过程应连续进行,不应调整轮胎气压,不应人为地冷却轮胎,各阶段相应的试验负荷保持不变。 5.2.2.4按规定程序完成试验后,让试验轮胎自然冷却15min~25min并应在此规定时间段内测量轮胎气压,待完全冷却后卸下轮胎进行外观检查。
表4轮胎高速性能试验程序
试验速度 km/h
试验时间 min
试验阶段
10 10 10 30
0~初始试验速度
1 2 3 4
初始试验速度初始试验速度十10 初始试验速度十20
:初始试验速度=速度符号对应的速度一20(km/h)。
5.3 3强度性能试验 5.3.1试验条件 5.3.1.1 试验轮辋宜符合GB/T2977或其他相关行业技术文件中有关测量轮辋的规定。将试验轮胎安装在试验轮辋上,充入轮胎胎侧标识的负荷能力相应气压,如果轮胎的单双胎气压不相同,则应采用双胎气压进行试验。
注:相关行业技术文件仅适用于不在GB/T2977范围内的载重汽车轮胎规格。 5.3.1.2实验室温度应保持在18℃~36℃范围内。试验轮胎和轮辋组合体应在实验室温度下停放至少3h。
4
GB/T 4501—2023
5.3.2试验步骤 5.3.2.1将停放后的轮胎气压重新调整到5.3.1.1规定值。将试验轮胎和轮辋组合体安装在试验机上。 5.3.2.2沿轮胎胎面中心线取大致等间距分布的5个点进行试验。 5.3.2.3压头垂直于胎面,并压在靠近胎面圆周中心线的花纹块上,避免压人花纹沟中。 5.3.2.4压头以50mm/min士2.5mm/min的移动速度向轮胎胎冠逐渐递增地施加作用力(F),至轮胎胎冠被压穿或达到表5或表6规定的最小破坏能值时为止。在转人下一个试验点前校正气压。 5.3.2.5测量并记录压头在每个试验点停止移动瞬间的作用力(F)和压人深度(行程P)。 5.3.2.6凡因压头触及轮辋而轮胎尚未被刺穿,该试验点应视为通过试验,并应在试验报告中注明“触及轮辋未穿”。 5.3.2.7用公式(1)计算各点(5.3.2.6点除外)的破坏能。
_F×P
W= 2 000
..(1)
式中: W一—破坏能,单位为焦耳(J); F—作用力,单位为牛顿(N); P—行程,单位为毫米(mm)。
5.3.2.8采用自动计算破坏能装置时,当达到规定的最小破坏能后,应立即停止压头继续压人轮胎。 5.3.2.9试验过程中,如果无内胎轮胎无法保持充气压力,可装入内胎进行试验,但应在试验报告中注明。
6判定规则
6.1耐久性能试验、高速性能试验
按本文件规定的条件进行试验后,轮胎气压不应低于规定的初始气压;轮胎外观检查不应有(胎面、 胎侧、帘布层、气密层、带束层、胎圈)脱层、帘布层裂缝、帘线剥离、帘线断裂、崩花(轻型载重汽车雪地轮胎耐久性能试验引起的PTBC除外)、接头裂开、龟裂以及胎体异常变形,则为“通过试验”,否则为“未通过试验”。
注:衍生型胎面崩花(PTBC)是轮胎在转鼓测试中产生的现象,从轮胎胎面脱落橡胶块或者产生撕裂但不暴露轮胎
骨架材料(如胎体帘布层、带束层等),在实际道路运行中不会出现。它通常在软胎面配方或复杂的胎面花纹样式(例如许多细小沟槽)轮胎试验过程中出现。
6.2强度性能试验
载重汽车公制系列轮胎各试验点的破坏能值均不小于表5的规定值时,判定“通过试验”;若有一试验点的破坏能值小于表5的规定值时,则判定“未通过试验”。
载重汽车英制系列轮胎各试验点的破坏能值均不小于表6的规定值时,判定“通过试验”;若有一试验点的破坏能值小于表6的规定值时,则判定“未通过试验”。
如果压头触及轮辋,轮胎未压穿,且未达到最小破坏能值,则该试验点视为通过试验。
5