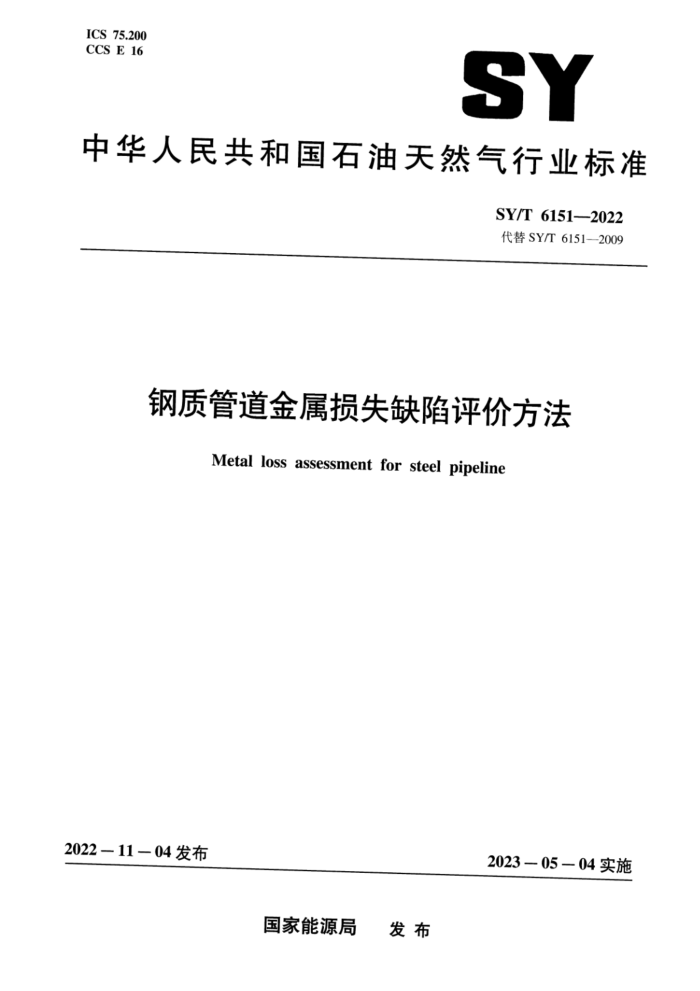
ICS 75.200 CCS E 16
SY
中华人民共和国石油天然气行业标准
SY/T 6151—2022 代替SY/T6151—2009
钢质管道金属损失缺陷评价方法
Metal loss assessment for steel pipeline
2022-11-04发布
2023-05-04实施
国家能源局 发布
SY/T6151—2022
目 次
前言 1
II
范围 2 规范性引用文件 3 术语和定义
一般要求 5 金属损失测量 5.1测量方法 5.2 金属损失深度测量 5.3 金属损失轴向长度测量 5.4 金属损失环向宽度测量 6金属损失规则化与合并 6.1 规则化处理 6.2合并处理按金属损失相对深度评定
4
7
按最大安全操作压力评定 8.1 确定响应准则 8.2 确定流变应力 8.3 按轴向缺陷评价 8.4 按环向缺陷评价 8.5 确定剩余强度 8.6 腐蚀增长预测附录A(规范性) 金属损失评价流程图附录B(资料性) 金属损失的响应准则参考文献
8
1
o
10
SY/T6151—2022
前言
本文件按照GB/T1.1-2020《标准化工作导则第1部分:标准化文件的结构和起草规则》的规定起草。
本文件代替SY/T6151—2009《钢质管道管体腐蚀损伤评价方法》,与SY/T6151-—2009相比,除结构调整和编辑性改动外,主要技术变化如下:
a)将文件名称更改为《钢质管道金属损失缺陷评价方法》; b)更改了标准的适用范围(见第1章,2009年版的第1章); c)更改了“规范性引用文件”(见第2章,2009年版的第2章); d)增加了“术语和定义”(见第3章); e)增加了“一般要求”,涵盖了原标准中“评价人员要求”和“评价前原始资料的准备”(见第
4章,2009年版的第3章和第4章); f)更改了“金属损失测量”(见第5章,2009年版的第5章); g)删除了“管体腐蚀损伤评定类别划分”(见2009年版的第6章); h)增加了“金属损失规则化与合并”(见6章); i)更改了“按金属损失相对深度评定”(见第7章,2009年版的第7章); j)更改了“按最大安全操作压力评定”(见第8章,2009年版的第8章); k)删除了“最大安全工作压力的断裂力学计算方法”(见2009年版的附录A); 1)删除了“评价流程图”(见2009年版的附录B); m)增加了“金属损失评价流程图”(见附录A)和“金属损失的响应准则”(见附录B)。 本文件由石油工业标准化技术委员会油气储运专业标准化技术委员会提出并归口。 本文件起草单位:国家石油天然气管网集团有限公司科学技术研究总院分公司、国家管网集团北
方管道有限责任公司、国家石油天然气管网集团有限公司生产部、中国石油天然气管道科学研究院有限公司、广东大鹏液化天然气有限公司、陕西延长石油(集团)有限责任公司管道运输公司。
本文件主要起草人:王富祥、杨辉、陈健、冯庆善、王维斌、毕武喜、雷铮强、玄文博、燕冰川、张海亮、贾光明、王婷、范玉然、李强、刘涛、张华兵。
本文件及其所代替文件的历次版本发布情况为 :
-1995年首次发布为SY/T6151-1995,2009年第一次修订;一本次为第二次修订。
II
SY/T6151—2022
钢质管道金属损失缺陷评价方法
1范围
本文件规定了在役钢质油气管道腐蚀、划痕、制造缺陷等金属损失缺陷的评价技术要求。 本文件适用于在役钢质油气管道金属损失缺陷的评价,适用的范围包括:
a)内、外腐蚀导致的金属损失; b)打磨后形成的轮廊光滑的金属损失; c)制管焊缝或环焊缝上的非选择性腐蚀; d)钝形划痕或制造缺陷; e)弯管、弯头上的金属损失。 本文件不适用于: a)未经打磨形成光滑轮廓的类裂纹缺陷; b)制管焊缝或环焊缝上的沟槽腐蚀、选择性腐蚀或优先腐蚀;
c)弯管和弯头以外的其他管件的金属损失; d)具有脆性断裂启裂特性材料的金属损失。 规范性引用文件
2
下列文件中的内容通过文中的规范性引用而构成本文件必不可少的条款。其中,注日期的引用文件,仅该日期对应的版本适用于本文件;不注日期的引用文件,其最新版本(包括所有的修改单)适
用于本文件。
SY/T 6477 含缺陷油气管道剩余强度评价方法 SY/T6597 油气管道内检测技术规范 SY/T 6996 钢质油气管道凹陷评价方法
3术语和定义
下列术语和定义适用于本文件。
3.1
金属损失 metalloss 任何发生金属减损的管道异常。 注:金属损失通常是由于腐蚀所致,但划痕、制造缺陷也能导致金属损失。 腐蚀 corrosion 由于与所处环境发生化学或电化学反应,造成某种材料(通常是金属)的劣化。 划痕gouge
3.2
3.3
1
SY/T6151—2022
金属机械切削造成的细长凹槽或凹腔。
3.4
制造缺陷millanomaly 管子在制管、敷设或运行维护过程中产生的除腐蚀、划痕外的其他金属损失。 注:广义的制造缺陷指在钢板制造或钢管、管件、法兰、阀门等元件生产过程中产生的缺陷,本文件中特指管
子在制管、敷设或运行维护过程中产生的除腐蚀、划痕外的其他金属损失。
3.5
规定的最小屈服强度specifiedminimumyieldstrength(SMYS)针对某种管材,在技术条件中所规定的屈服强度的最小值。
3.6
规定的最小抗拉强度 specifiedminimumtensilestrength(SMTS) 针对某种管材,在技术条件中所规定的抗拉强度的最小值。 响应 response 对含缺陷管道采取修复、降压或其他的风险减缓措施。 最大允许操作压力 maximumallowableoperatingpressure(MAOP) 管道系统遵循设计规范的规定,所能连续操作的最大压力,小于或等于设计压力。 安全系数safetyfactor(SF) 结构承载能力的安全允余比值,为大于或等于1的数值。 3.10
3.7
3.8
3.9
腐蚀速率边界值 corrosionratethreshold 根据可接受保守程度选取的管段腐蚀速率的阈值。 注:本文件取值为管段所有内腐蚀点或外腐蚀点腐蚀速率的平均值与标准差的和。
4一般要求
4.1金属损失缺陷评价应收集评价所需的相关资料,充分考虑各种载荷和可能的失效模式,根据本文件规定对评价对象进行评价,给出评价结论。 4.2缺陷评价所需的资料包括:
a)管道的材质、管径、壁厚数据; b)管材的强度、韧性等力学性能数据; c)输送介质、工作压力、温度情况、外部荷载; d)缺陷的类型、位置、尺寸与形貌; e)腐蚀环境及腐蚀防护情况 f)管道工况、运行历史、失效与维修历史和所处的环境资料 g)管道在线检测记录,包括壁厚测量结果和其他无损检测结果。
4.3评价人员应具备下列基本知识和能力:
a)管道工作原理与安全运行注意事项; b)管道缺陷及力学基本知识; c)无损检测基本知识,以及缺陷类型判定及尺寸测量能力。
4.4评价需要的管材力学性能参数宜选择待评价管道管材的规定最小值,也可选择该管材力学性能 2
SY/T6151—2022
实测值。 4.5评价结论应给出缺陷在指定工况下的剩余强度或可接受性。 4.6对于与时间相关的缺陷,应基于管道投用时间、检测时间、缺陷致因等信息,应用管道缺陷增长预测模型,预测缺陷增长趋势,根据不同类型缺陷的响应准则,给出缺陷的计划响应时间。 4.7应结合管道的历史失效事故、最近运行状况、缺陷失效后果严重程度等,给出缺陷修复前含缺陷管道的安全运行建议。 4.8应考虑检测与适用性评价结果的时效性,缺陷响应时间应从现场检测完成时开始算起。 4.9与凹陷相关的腐蚀与制造缺陷,当凹陷深度小于2%OD(OD为管道外径)时,可按照本文件金属损失的规定进行评价;当凹陷深度大于或等于2%OD时,可按照SY/T6996的规定进行评价。与凹陷相关的划痕,可按照SY/T6996或SY/T6477的规定进行评价。 4.10金属损失的评价流程按照附录A执行。
5金属损失测量 5.1测量方法 5.1.1对金属损失缺陷,可采用内检测技术进行测量,具体按照SY/T6597的规定执行。 5.1.2对金属损失缺陷,也可采用卡尺、直板尺、卷尺、超声测厚仪、激光扫描仪及其他测量仪器(如点蚀测量规)等无损检测方法。 5.2金属损失深度测量
应准确测量金属损失的深度;对连成片的金属损失,应测量最深部位的深度。 5.3金属损失轴向长度测量 5.3.1测量每个金属损失在管道轴线方向的最大投影长度。 5.3.2 测量按照6.2给出的细则合并为同一金属损失的总长度。 5.4金属损失环向宽度测量 5.4.1 测量每个金属损失在管道圆周方向的最大投影长度(弧线长)。 5.4.2 测量按照6.2给出的细则合并为同一金属损失的总投影长度(弧线长)。
6金属损失规则化与合并 6.1规则化处理 6.1.1# 按照图1所示规则对金属损失的轴向长度L、环向宽度2c及最大深度d进行规则化处理。 6.1.2考虑到缺陷基底处的加工硬化层的影响,宜将划痕的深度测量值增加0.5mm作为评价时的划痕深度。 6.2合并处理 6.2.1当相邻缺陷之间的轴向距离和环向距离均小于3倍管道壁厚(3t,1为公称壁厚)时,应将缺陷合并作为一个缺陷进行评价。评价使用的缺陷长度为合并后的轴向长度,宽度为合并后的环向宽度(弧线长),如图2所示。
3
SY/T 6151—2022
轴向长度L
最大深度。
图1金属损失长度的规则化处理
轴向长度L
图2金属损失长度的合并处理
6.2.2当划痕与腐蚀合并后,合并后的缺陷宜按照划痕进行评价,缺陷增长速率可按照合并前腐蚀缺陷的增长速率进行计算:当制造缺陷与腐蚀合并后,合并后的缺陷宜按照腐蚀进行评价,缺陷增长速率可按照合并前腐蚀缺陷的增长速率进行计算,当划痕与制造缺陷合并后,合并后的缺陷宜按照划痕进行评价。
7按金属损失相对深度评定
7.1金属损失相对深度按公式(1)计算:
a
(1)
×100%
A:
1
式中: A 一金属损失相对深度; d-实测的金属损失区域的最大深度,单位为毫米(mm);
管道公称壁厚,单位为毫米(mm)。
7.2对于腐蚀和制造缺陷,当A≥80%,应立即响应;对于划痕,A≥60%,应立即响应。 7.3如果A≤10%,可免于评价。 7.4 除7.2和7.3以外的情况,应按照第8章进行评定。 4
SY/T6151—2022
8: 按最大安全操作压力评定 8.1 确定响应准则
评价前应确定不同金属损失的响应准则,腐蚀、划痕与制造缺陷的响应准则参见附录B。 8.2 确定流变应力 8.2.1管材等级不大于L485(X70)时,流变应力St可按公式(2)计算,且不超过SMTS。
Snow=SMYS+69
(2)
式中: Sfow -流变应力,单位为兆帕(MPa); SMYS- 一规定的最小屈服强度,单位为兆帕(MPa)。
8.2.2管材等级不大于L555(X80)时,流变应力Srow可按公式(3)计算:
SMYS+SMTS
Show
(3)
2
式中: Sfow 流变应力,单位为兆帕(MPa); SMYS一一规定的最小屈服强度,单位为兆帕(MPa); SMTS——规定的最小抗拉强度,单位为兆帕(MPa)。
8.3 按轴向缺陷评价
含缺陷管道轴向爆破压力Pa按公式(4)计算:
d
1.
2t Pfa: =mS.
(4)
D
dr 1
M
式中: Pra 轴向爆破压力,单位为兆帕(MPa); D- 一管道外径,单位为毫米(mm);
管道壁厚,单位为毫米(mm): m- 管道形状因子; Show 流变应力,单位为兆帕(MPa);
缺陷形状因子,腐蚀评价时取0.85,划痕和制造缺陷评价时取1;缺陷深度,单位为毫米(mm);
n d M - 鼓胀因子。
管道形状因子,直管取1,弯管或弯头按公式(5)计算:
4R2D 4R-D
m:
(5)
式中: m 管道形状因子;
5