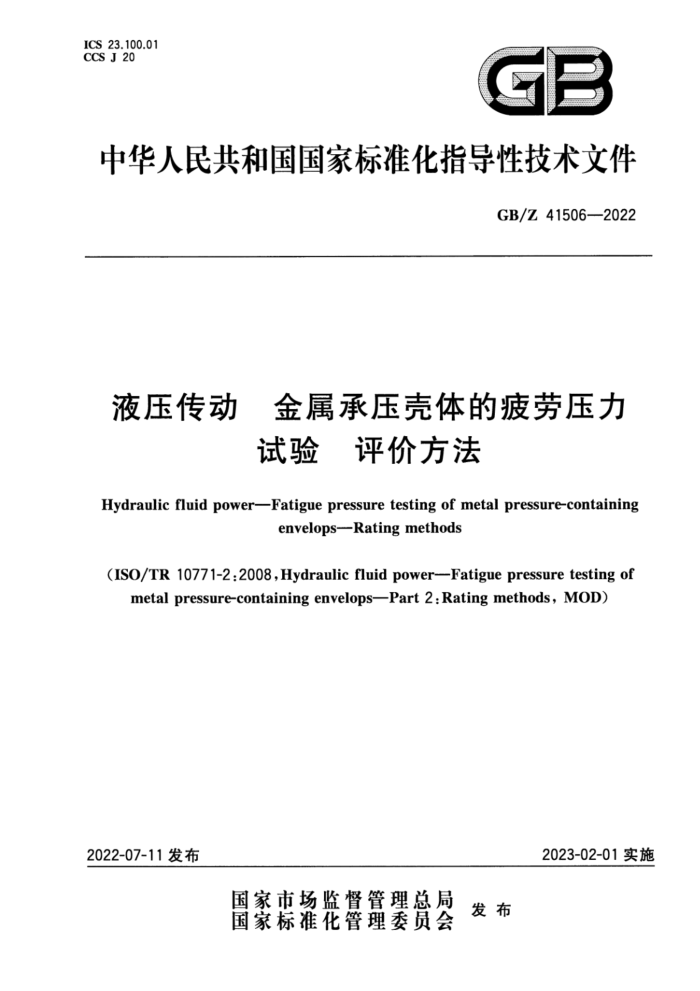
ICS 23.100.01 CCS J 20
GB
中华人民共和国国家标准化指导性技术文件
GB/Z41506—2022
液压传动 金属承压壳体的疲劳压力
试验评价方法
Hydraulic fluid power-Fatigue pressure testing of metal pressure-containing
envelops--Rating methods
(ISO/TR10771-2:2008,Hydraulicfluidp0wer--Fatiguepressuretestingof
metal pressure-containing envelops-—Part 2:Rating methods, MOD)
2023-02-01实施
2022-07-11发布
国家市场监督管理总局
国家标准化管理委员会 发布
GB/Z41506—2022
目 次
前言引言
Il
范围 2 规范性引用文件 3 术语和定义 4 材料相关系数的选择 5 确定循环试验压力 6 进行疲劳试验 1
1
2
2
相似性评价 8 评价声明 9 标注说明(引用本文件) 附录A(资料性) 材料系数附录B(规范性) 变异系数(Kv)的计算附录C(资料性) 加速系数附录D(资料性) 疲劳压力评价方法的基础理论附录E(资料性) 试验验证示例参考文献
Y
11
13
17 32 35
GB/Z41506—2022
前言
本文件按照GB/T1.1一2020《标准化工作导则第1部分:标准化文件的结构和起草规则》的规定
起草。
本文件修改采用ISO/TR10771-2:2008《液压传动金属承压壳体的疲劳压力试验 第2部分:评价方法》,文件类型由ISO的技术报告变更为我国的国家标准化指导性技术文件。
本文件与ISO/TR10771-2:2008的技术性差异及其原因如下:
用规范性引用的GB/T17446替换了ISO5598(见第3章),以适应我国的技术条件、提高可操作性;用规范性引用的GB/T19934.1替换了ISO10771-1:2002(见第3章、6.2、6.3),以适应我国的技术条件、提高可操作性;增加了“加速系数”的表述(见5.7),以适应我国的技术条件。
本文件做了下列编辑性改动:
将标准名称改为《液压传动金属承压壳体的疲劳压力试验评价方法》;增加了附录E(资料性)“试验验证示例”
请注意本文件的某些内容可能涉及专利。本文件的发布机构不承担识别专利的责任。 本文件由中国机械工业联合会提出。 本文件由全国液压气动标准化技术委员会(SAC/TC3)归口。 本文件起草单位:武汉科技大学、千里马机械供应链股份有限公司、油威力液压科技股份有限公司
济南液压泵有限责任公司、北京华德液压工业集团有限责任公司、北京机械工业自动化研究所有限公司。
本文件主要起草人:钱新博、陈新元、赵、许军、林广、刘传锋、周宇、曹巧会。
1
GB/Z41506—2022
引言
在液压传动系统中,动力是通过回路中受压流体来传递和控制的。由于疲劳失效模式与液压元件的安全功能和工作寿命密切相关,所以对于液压元件的制造商和用户,掌握液压元件的可靠性数据就显得非常重要。本文件提供了一种验证液压元件承压壳体的疲劳压力评价的方法。
在工作期间,系统内的元件可能承受来自以下方面的载荷:
内部压力;外力;
一惯性和重力的影响;一冲击和振动;
温度变化或温度梯度。 这些载荷的性质可以由单一的静态力作用到持续变化振幅、重复加载及振动。了解元件能否承受
这些载荷是很重要的,但本文件仅涉及由内部压力引起的载荷问题。
针对制造商采用的各种压力评价方法,本文件提供了一种通用的验证方法,用于提高元件压力评价的可信度。该验证方法是基于金属疲劳的统计分析及统计验证理论。为提高该验证方法的准确性,有必要结合每类元件及其典型试验样本的设计结构原理。无论样本数大小,本验证方法均可降低液压元件疲劳失效的风险。
依据本文件验证元件的额定疲劳压力,首先应初步设定元件的额定疲劳压力、选择试验样本及确定
试验压力;再依据GB/T19934.1进行疲劳压力试验。如果样本试验成功,则表明该类液压元件的疲劳压力评价通过了验证。
II
GB/Z41506—2022
液压传动金属承压壳体的疲劳压力
试验评价方法
1范围
本文件给出了在持续稳定的、具有周期性的内部压力载荷下,液压元件金属承压壳体的疲劳压力评价方法。
本文件仅适用于用金属制造、在不产生蠕变和低温脆化的温度下工作、仅承受压力引起的应力、不存在由于腐蚀或其他化学作用引起的强度降低的液压元件承压壳体。承压壳体可包括垫片、密封件和其他非金属零件,但这些零件在试验中不作为被试液压元件承压壳体的组成部分(见GB/T19934.1)。
本文件不适用于ISO4413中规定的管路元件(即管接头、软管、硬管)。对于管路元件的疲劳试验方法见GB/T26143、ISO6803和ISO6605。
本文件给出了一种适用于液压元件金属承压壳体疲劳压力评价的通用方法。此外,EN14359对蓄能器的疲劳压力评价描述了具体方法和试验要求。
2规范性引用文件
下列文件中的内容通过文中的规范性引用而构成本文件必不可少的条款。其中,注日期的引用文件,仅该日期对应的版本适用于本文件;不注日期的引用文件,其最新版本(包括所有的修改单)适用于本文件。
GB/T17446流体传动系统及元件词汇(GB/T17446--2012,ISO5598:2008,IDT) GB/T19934.1液压传动金属承压壳体的疲劳压力试验第1部分:试验方法(GB/T19934.1-
2021,ISO10771-1:2015,IDT)
3术语和定义
GB/T17446、GB/T19934.1界定的以及下列术语和定义适用于本文件。
3.1
额定疲劳压力 ratedfatiguepressure PRF 在额定寿命周期内,随机选择的承压壳体以给定的概率通过验证不发生失效所能承受的最高压力。
3.2
保证水平 assurancelevel 随机选择样本的疲劳强度高于额定疲劳压力的概率。
3.3
验证水平 verification level 随机选择样本的疲劳强度不低于循环试验压力的概率。
3.4
离散系数 coefficient of variation k。
1
GB/Z41506—2022
在给定疲劳寿命条件下,材料的疲劳强度分布的标准差与均值之比。
3.5
变异系数 variabilityfactor Kv 循环试验压力与额定疲劳压力的比值。
3.6
组件element 元件的组成部分(如缸的拉杆、阀的端盖、泵壳体上的螺栓等)。
4材料相关系数的选择
4.1承压壳体中的每种材料所对应的离散系数(。)可从材料的疲劳试验获得,其试验方法宜符合国家或国际标准。 4.2特定材料的离散系数(k。)也可参考附录A。
5确定循环试验压力
5.1 选择额定疲劳压力评价的保证水平,名义值为90%。 5.2选择额定疲劳压力评价的验证水平,名义值为90%。 5.3 选择进行测试的元件样本数,确定被测元件中组件样本的数量。
注:由于试验压力会随样本数增加而降低,所以验证压力评价不受样本数影响。 5.4按表1确定元件中的每个组件的变异系数(Kv),其最大值作为该元件的变异系数。具体步骤和计算见附录B。 5.5初步设定承压壳体的额定疲劳压力。 5.6计算循环试验压力(Pcr):
Pcr=K×PRF
(1)
式中: Kv 变异系数; PRF—承压壳体的额定疲劳压力。
5.7加速系数:
在具备条件的情况下,可采用加速试验方法(附录C给出了循环试验压力的加速系数),以缩短试验循环次数。
表1验证水平为90%时的变异系数(K)
组件材料离散系数(k。)
组件样本数量 (n)* 0 0.02 0.04 0.06 0.08 0.10 0.12 0.14 0.16 0.18 0.20 0.22 0.26 0.28 0.30
保证水平
0.24
1.00 1.09 1.20 1.32 1.46 1.63 1.83 2.08 2.38 2.77 3.29 2 1.00 1.08 1.16 1.26 1.38 1.52 1.68 1.88 2.13 2.45 2.87
1
99.9% 3 1.00 1.07 1.15 1.23 1.34 1.46 1.61 1.78 2.01 2.29 2.66 3.18
4 1.00 1.06 1.13 1.22 1.31 1.42 1.56 1.72 1.93 2.19 2.54 3.02 5 1.00 1.06 1.13 1.20 1.29 1.40 1.53 1.68 1.87 2.12 2.44 2.89
2
GB/Z41506—2022
表1验证水平为90%时的变异系数(Kv)(续)
组件材料离散系数(k。)b
保证 组件样
水平 本数量
(n)* 0 0.02 0.04 0.06 0.08 0.10 0.12 0.14 0.16 0.18 0.20 0.22 0.24 0.26 0.28 0.30
1.00 1.08 1.16 1.25 1.35 1.47 1.60 1.75 1.92 2.12 2.35 2.63 2.96 2 1.00 1.06 1.12 1.20 1.28 1.37 1.47 1.58 1.72 1.87 2.05 2.26 2.52 2.85 3 1.00 1.05 1.11
1
99%
1.17 1.24 1.32 1.40 1.50 1.62 1.75 1.90 2.09 2.31 2.59 2.94
4 1.00 1.05 1.10 1.15 1.21 1.28 1.36 1.45 1,55 1.67 1.81 1.98 2.18 2.43 2.74 3.16 5 1.00 1.04 1.09 1.14 1.20 1.26 1.33 1.41 1.51 1.62 1.75 1.90 2.08 2.31 2.60 2.98 1 1.00 1.05 1.11 1.17 1.23 1.29 1.36 1,44 1.52 1.60 1.69 1.79 1.89 2.00 2.12 2.25 2 1.00 1.04 1.07 1.11 1.16 1.20 1.25 1.30 1.35 1.41 1.47 1,54 1.61 1.69 1.77 1.86 3 1.00 1.03 1.06 1.09 1.12 1.16 1.19 1.23 1.28 1.32 1.37 1.42
90%
1.54 1.60 1.67
48
4 1.00 1.02 1.05 1.07 1.10 1.13 1.16 1.19 1.23 1.26 1.30 1.34 1.39 1.44 1.49 1.55
1.00 1.02 1.04 1.06 1.08 1.11 1.13 1.16 1.19 1.22 1.25 1.29 1.33 1.37 1.41 1.46
如果选择99%的验证水平,则测试组件样本数变为原来的两倍。 b可在k。值列表进行线性插值,或依据附录D的方程(D.14)计算Kv
6进行疲劳试验
6.1确定评价元件的试验循环周期数,范围是105~10″。 6.2由6.1确定的循环周期数和公式(1)求得的PcT,依据GB/T19934.1对元件样本进行疲劳压力试验。 6.3 3试验结束时,若5.3中选择的样本均未失效(失效准则按GB/T19934.1),则疲劳压力试验成功。
7相似性评价
若几何形状相似的元件之间的差异不会导致疲劳强度有显著差异,则可将被试元件已验证的额定疲劳压力(Prr)作为形状相似元件的额定疲劳压力。比如,相对于被试元件,具有较小口径或不同的轴向长度,但其他几何形状相同的元件。
8评价声明
若满足6.3的要求,则5.5提出的承压壳体的额定压力(PRF)得到了验证(附录E给出了试验验证的示例)。元件的PRF宜按如下方式表示:
Pr=PRr(MPa)/保证水平/验证水平/试验中的Kv值/试验周期数示例:额定疲劳压力为12.5MPa的承压壳体通过了2X10°循环次数的疲劳压力试验,其中,保证水平为99%,验证水平
为90%和Kv为1.36,即可表示为:
Prp=12.5MPa/99%/90%/1.36/2×105
3
GB/Z41506—2022
标注说明(引用本文件)
9
当选择遵守本文件时,宜在试验报告、产品目录和产品销售文件中采用以下说明:“额定疲劳压力评价方法符合GB/Z415062022《液压传动 金属承压壳体的疲劳压力试验 评价方法》”。