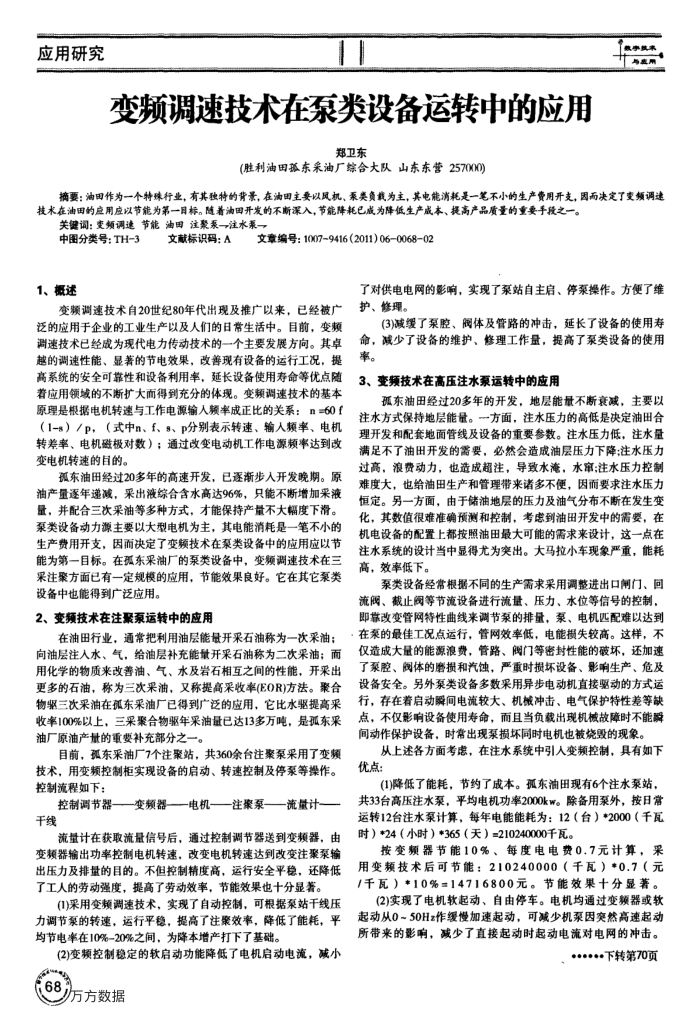
应用研究
变频调速技术在泵类设备运转中的应用
郑卫东
(胜利油田孤东采油厂综合大队山东东营257000)
做事教术与良用
摘要:油田作为一个特殊行业,有其独特的背景,在油田主要以风机、泵类负载为主,其电能消耗是一笔不小的生产费用开支,因而决定了变频调速技术在油田的应用应以节能为第一目标。随着油回开发的不断深入,节能降耗已成为降低生产成本、提高产品质量的重要手段之一。
关键调:变频调速节能油田注聚系一注水系一
文章编号:1007~9416(2011)06006802
中图分类号:TH-3 1、概述
文献标识码:A
了对供电电网的影响,实现了泵站自主启、停泵操作。方便了维
变频调速技术自20世纪80年代出现及推广以来,已经被广泛的应用于企业的工业生产以及人们的日常生活中。目前,变频调速技术已经成为现代电力传动技术的一个主要发展方向。其卓越的调速性能、显著的节电效果,改善现有设备的运行工况,提高系统的安全可靠性和设备利用率,延长设备使用寿命等优点随着应用领域的不断扩大而得到充分的体现。变频调速技术的基本原理是根据电机转速与工作电源输人频率成正比的关系:n=60f(1-s)/P,(式中n、f、、p分别表示转速、输人率、电机转差率、电机磁极对数);通过改变电动机工作电源频率达到改变电机转速的目的。
孤东油田经过20多年的高速开发,已逐渐步入开发晚期。原油产量逐年递减,采出减综合含水高达96%,只能不断增加采液量,并配合三次采油等多种方式,才能保持产量不大幅度下滑。泵类设备动力源主要以大型电机为主,其电能消耗是一笔不小的生产费用开支,因而决定了变频技术在泵类设备中的应用应以节能为第一目标。在孤东采油厂的泵类设备中,变频调速技术在三采注聚方面已有一定规模的应用,节能效果良好。它在其它泵类设备中也能得到广泛应用。
2、变频技术在注聚泵运转中的应用
在油田行业,通常把利用油层能量开采石油称为一次采油;向油层注人水、气,给油层补充能量开采石油称为二次采油;而用化学的物质来改善油、气、水及岩石相互之间的性能,开采出更多的石油,称为三次采油,又称提高采收率(E0R)方法。聚合物驱三次采油在孤东采油厂已得到广泛的应用,它比水驱提高采收率100%以上,三采聚合物驱年采油量已达13多万吨,是孤东采油厂原油产量的重要补充部分之一。
目前,孤东采油厂7个注聚站,共360余台注聚泵采用了变频技术,用变频控制柜实现设备的启动、转速控制及停泵等操作。控制流程如下:
控制调节器——变频器—电机——注案泵——流量计— 干线
流量计在获取流量信号后,通过控制调节器送到变频器,由变频器输出功率控制电机转速,改变电机转速达到改变注聚泵输出压力及排量的目的。不但控制精度高,运行安全平稳,还降低了工人的劳动强度,提高了劳动效率,节能效果也十分显著。
(1)采用变频调速技术,实现了自动控制,可根据泵站干线压力调节泵的转速,运行平稳,提高了注聚效率,降低了能耗,平均节电率在10%-20%之间,为降本增产打下了基础。
(2)变频控制稳定的软启动功能降低了电机启动电流,减小 68
防方数据
护、修理。
(3)减缓了泵腔、阀体及管路的冲击,延长了设备的使用寿命,减少了设备的维护、修理工作量,提高了泵类设备的使用率。
3、变频技术在高压注水泵运转中的应用
孤东油田经过20多年的开发,地层能量不断衰减,主要以注水方式保持地层能量。一方面,注水压力的高低是决定油田合理开发和配套地面管线及设备的重要参数。注水压力低,注水量满足不了油田开发的需要,必然会造成油层压力下降;注水压力过高,浪费动力,也造成超注,导致水滤,水审:注水压力控制难度大,也给油田生产和管理带来诸多不便,因而要求注水压力恒定。另一方面,由于储油地层的压力及油气分布不断在发生变化,其数值很难准确预测和控制,考虑到油田开发中的需要,在机电设备的配置上都按照油田最大可能的需求来设计,这一点在注水系统的设计当中显得尤为突出。大马拉小车现象严重,能耗高,效率低下。
泵类设备经常根据不同的生产需求采用调整进出口闸门、回流阀、截止阅等节流设备进行流量、压力、水位等信号的控制,即靠改变管网特性曲线来调节泵的排量,泵、电机匹配难以达到在泵的最佳工况点运行,管网效率低,电能损失较高。这样,不仅造成大量的能源浪费,管路、阀门等密封性能的破坏,还加速了泵腔、阅体的磨损和汽蚀,严重时损坏设备、影响生产、危及设备安全。另外泵类设备多数采用异步电动机直接驱动的方式运行,存在着启动瞬间电流较大、机械冲击、电气保护特性差等缺点,不仅影响设备使用寿命,而且当负载出现机械故障时不能瞬间动作保护设备,时常出现泵损坏同时电机也被烧毁的现象。
从上述各方面考虑,在注水系统中引人变频控制,具有如下优点:
(1)降低了能耗,节约了成本。孤东油田现有6个注水泵站,共33台高压注水泵,平均电机功率2000kw。除备用泵外,接日常运转12台注水泵计算,每年电能能耗为:12(台)*2000(千瓦时)*24(小时)*365(天)=210240000千瓦。
按变频器节能10%、每度电电费0.7元计算,采用变频技术后可节能:210240000(千瓦)*0.7(元/千瓦)*10%=14716800元。节能效果十分显著。
(2)实现了电机软起动、自由停车。电机均通过变频器或软起动从0~50H2作缓慢加速起动,可减少机泵因突然高速起动所带来的影响,减少了直接起动时起动电流对电网的冲击。
***·下转第70页